Read this article in French German Italian Portuguese Spanish
What makes construction projects in the UK so unusually expensive?
16 April 2024
London is currently the most expensive city in the world in which to build, pipping Geneva in Switzerland to take the top spot in the 2024 Arcadis International Construction Costs (ICC) report. Neil Gerrard finds out why.
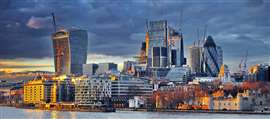
London perennially rides high in the ranking of costly places to build.
But what is perhaps more surprising than the UK capital’s presence at the top of the chart is the sheer number of other UK cities that sit high up in the latest index, published yesterday.
Bristol in south west England only has a population of just under 450,000 people yet still managed 10th on the list. Manchester and Birmingham are 12th and 14th respectively.
In fact, UK cities account for seven of the top 20 places (see list below). Northern Ireland’s capital Belfast isn’t far behind at 28th.
Arcadis’s ranking suggests that the UK is a peculiarly expensive place to build. Why?
Different drivers, cumulative effects
Talking to Construction Briefing, Simon Rawlinson, head of research and strategic insight at Arcadis, says, “There are some cumulative effects of different drivers that have resulted in this but it is a long-term trend. I think some of the reasons are cultural. At least from the point of view of our contractor-delivered buildings, as opposed to volume housebuilding, we tend to go down quite a craft-based, customised way of working. Architects like to design things in a fairly bespoke way and contractors tend to quite like to respond to that.
The 10 most expensive cities in which to build
1) London
2) Geneva
3) Zurich
4) Munich
5) New York City
6) San Francisco
7) Philadelphia
8) Copenhagen
9) Hong Kong
10) Bristol
“In other markets, and France is probably a good example, contractors have a bit more control over the solutions they put forward. They are more motivated to standardise around the solutions they develop. Similarly, there’s far more control in the hands of US contractors over the kind of product they deliver as well. The UK has a cultural willingness to design and deliver one-off solutions, even in the context of quite standardised products.”
And Rawlinson was quick to point out that the high cost of construction in the UK was not isolated to buildings but also applies to infrastructure projects.
Another significant factor is, in his view, the UK’s contracting model. “The UK has a contracting model that passes inflation – as well as deflation – through quickly. But we have multiple layers of subcontracting – much more than France, for example. That means you have multiple layers of management cost and profit risk allowances on top of the actual resource cost of labour, plant and materials. When you get the sort of moments that we had after Covid where labour is in quite short supply, that becomes quite an explosive inflationary trend.”
The third reason Rawlinson puts forward for the UK’s high construction cost is one that comes down to timing – it has recently introduced new sustainability regulations within the Future Buildings Standard and the Future Homes Standard, along with safety-related changes to design and construction methods following the Grenfell Tower disaster.
“We have seen lots of changes influencing the way that buildings are designed in the UK over the last year or so. I haven’t seen that level of regulatory uncertainty elsewhere and it’s not picked up in inflation,” he says.
Finally, he sees a trend in the UK with a growing number of clients specifying high-quality projects that carry increased costs with them. “Clients are investing in very high quality buildings with features like rooftop terraces and other amenities, better quality interiors. There’s a race for quality that I think is more extreme than in many other places. Having net zero features is a significant element to it. That is driving clients to spend more on the base build specification in terms of the air conditioning systems and sensor networks. There are more standards like WiredScore and WELL standards and the UK real estate market is standard sensitive – people will invest in these standards because they know they will get a response form the market.”
Cost drivers for larger projects
As far as larger projects and developments in particular are concerned, Noble Francis, economics director at the UK’s Construction Products Association (CPA), sees four significant reasons why the UK is such an expensive place to build.
Where do UK and Ireland cities rank?
London (1/100)
Bristol (10/100)
Manchester (12/100)
Birmingham (14/100)
Edinburgh (15/100)
Cardiff (16/100)
Glasgow (18/100)
Dublin (19/100)
Belfast (28/100)
“Firstly, getting projects through the planning system takes a lot of time and resources. The larger the project, the longer the time and the number of delays throughout an exhaustive planning process. To use the most extreme example, the planning application for the 14-mile Lower Thames Crossing is 359,000 pages and £800 million has already been spent on the project, despite it not even starting until 2026 at the earliest,” Francis tells Construction Briefing.
He also points out that larger projects and developments also involve high mitigation costs. Tunnelling to minimise complaints from local residents can add millions of pounds to projects like the UK’s troubled high-speed rail project, HS2. Commitments to additional local infrastructure as part of larger housing developments through legally binding arrangements with local authorities called Section 106 Agreements can also pile on costs, he points out.
Then there is the volatility of demand in the construction sector in the UK, which leads to greater costs over the medium term. “Construction in the UK is very volatile, as we have seen from the recent sharp downturn in housebuilding. But it equally applies to new commercial tower developments and to infrastructure. The government finished the Sizewell B nuclear power station in 1995. But then there was no new nuclear power station construction until Hinkley Point C in 2016. There isn’t a consistent pipeline of long-term projects in the UK,” says Francis.
“As a result, the business models from major housebuilders and main contractors in the UK need to focus on dealing with the volatility in activity by subcontracting out the cost, activity and risk rather than making large upfront investments in skills, capacity and modern methods of construction for a long-term rate of return,” he adds, going back to Rawlinson’s point about significant layers of subcontracting in the UK construction sector.
Among other contributors to a hefty bill for UK projects that Francis cites are continual pauses on projects, consultancy reviews and changes in spec.
A sign of market health?
Many of those contributors could hardly be seen as a positive. But a city’s downward slide on Arcadis’s ranking of the most expensive places to build doesn’t necessarily amount to good news either.
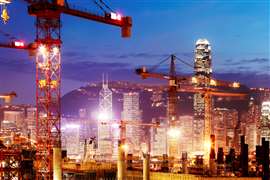
Hong Kong has traditionally occupied the top few places in Arcadis’s list but this year has dropped to ninth.
That’s not because the industry there has uncovered some secret formula for building more cost effectively. Instead, Rawlinson says, it’s a sign that the construction sector is struggling.
“Hong Kong is a city that has been moving down the index. That is a reflection of quite a tough market there over the last few years. Often when cities move down, it is a sign of a negative rather than a positive. In Hong Kong, the private sector has slowed, and it is a ferociously competitive market. That would probably be quite a difficult place to be a contractor.
But Rawlinson also acknowledges that a city riding high in the rankings is problematic in the public sector in particular. “You want to be able to deliver as much social and economic infrastructure as you can. That is one of the reasons why the UK government has been investing in various aspects of offside manufacturing process improvement,” he says.
Another faller in the rankings is Amsterdam in the Netherlands, where concerns about nitrogen pollution has led to a significant reduction in the number of construction permits being issued.
Munich, on the other hand, has risen rapidly to sixth place amid high inflation in Germany.
However, there is one other factor governing a city’s position in the tables and that is currency fluctuations.
“It is one variable that you mustn’t forget. It didn’t move very much in the period until we froze the currency, which was in February while we were compiling the report,” Rawlinson says. “But the US dollar has started to strengthen a bit recently and it was very strong in 2023, so you get these movements that are often related to things that have got nothing to do with the construction sector.”
How is the 2024 Arcadis Internation Construction Costs Index compiled?
Arcadis’s International Construction Costs Index covers 100 of the world’s large cities across six continents. It examines costs across twenty different building types, including residential, commercial, and public sector developments. It is based on a survey of construction costs, a review of market conditions and the professional judgement of Arcadis’ global team of experts. The calculations are based in USD and indexed against the price range for each building type relative to Amsterdam.
|
STAY CONNECTED

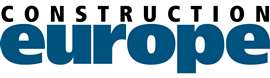
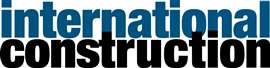
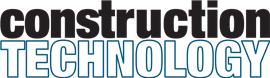
Receive the information you need when you need it through our world-leading magazines, newsletters and daily briefings.
CONNECT WITH THE TEAM
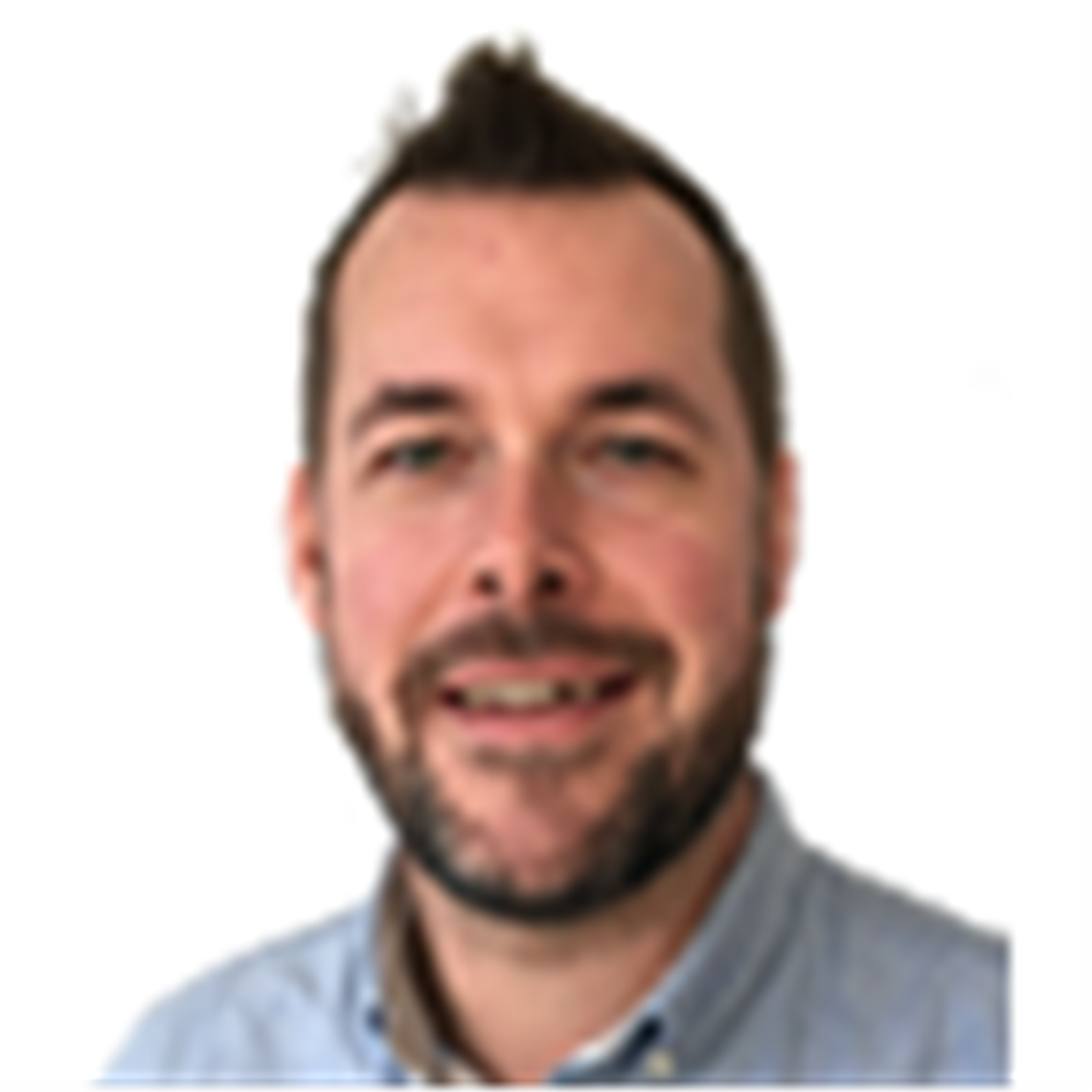
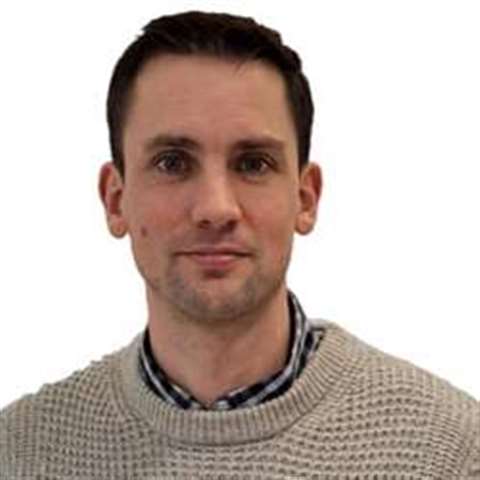
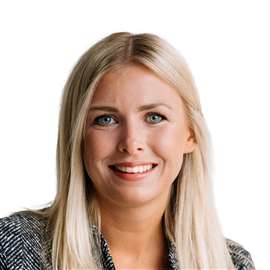