Read this article in French German Italian Portuguese Spanish
Laing O’Rourke Centre director: ‘What has really changed in construction? Not enough.’
10 July 2024
Construction’s much-heralded transformation into a highly productive, technologically advanced, low-carbon industry is taking longer to arrive than many would have liked.
But University of Cambridge Professor Campbell Middleton, director of the Laing O’Rourke Centre for Construction Engineering and Technology, and his colleagues are working to speed up the process.
The renowned UK university and the Laing O’Rourke Centre, which it runs in partnership with UK-based multinational contractor Laing O’Rourke, have just published a new review. Entitled Transforming Construction, it sets out a vision for what the construction sector should look like in the future and how it can get there.
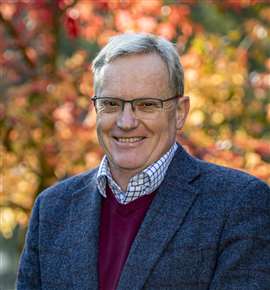
As Professor Middleton explains, the Laing O’Rourke Centre is working to educate and upskill current and future construction leaders through its Construction Engineering Masters (CEM) programme, undertake applied research in conjunction with companies in the sector, and generate an evidence base and thought leadership to support new policies, processes and methods in the construction sector.
Up until now though, the going in the industry as whole has been slow, he says. “We are not moving anywhere near quickly enough [to transform construction].
“We have had report after report on the industry saying there’s a need for change and about what we need to change. You can go right back to the 1940s for some of them.
“And they are excellent reports. But how many of them have led to really substantive change? What has really changed in the industry? Not enough. We could do far more.”
Bringing people together
The widely recognised fragmentation of the construction industry, which operates on a contractual model, does not help to foster clear and productive engagement between the industry, academia, and policy makers, he asserts.
“We’ve done a survey trying to identify key bodies representing the construction industry. I think we’ve got up to over 300 [in the UK alone] and that makes it very difficult to get a consistent message through to government and policymakers.
“What can we do in all that? I see our role is to use the profile of the university to bring people together and try to get people to work together and get some consistency in their approach.”
The Laing O’Rourke Centre’s research strategy outlines three key outcomes for a transformed construction industry: net zero carbon, enhanced productivity, and social value. The five enablers that it lists to reach those outcomes are: digital engineering; manufacturing (modern methods of construction and offsite manufacturing); whole life performance; procurement; and skills.
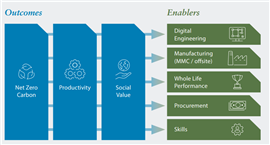
‘Data is the new gold’
For Professor Middleton though, it all begins with having consistent data. “If you can’t measure it and understand what is happening then you are not going to change it. So for me, the starting point for change all comes back to data. Data is the new gold.”
As such, a lot of the Laing O’Rourke Centre’s work is based around measuring performance, ranging from productivity, costs, programme, quality and other metrics during construction, to performance of built assets once in service. And he cites the example of working with the Cambridge Centre for Smart Infrastructure & Construction to place sensors on structures to measure loading, deformation and other factors. “There, for the first time, you begin to measure the margins of capacity left in them, which is quite an eye-opener.
“And then we are working with industry to take that information back to help the industry and to policymakers and government to recognise the opportunity for change. Perhaps the best example there is the work we have been doing with the Private Sector Construction Productivity Taskforce, which has representatives from some of the big clients and property developers but also many tier one contractors at a senior level.
“What we are doing is going in with them and firstly helping to define a consistent set of metrics that will measure performance. And then on the back of that we have developed a new methodology to collect, interpret and present the data in a meaningful way that project managers and those further up the tree can really understand.”
Meanwhile, the Centre is also working to rethink the classic method of construction management, starting with the ubiquitous Gantt chart, and instead implementing new approaches to presenting data that are based on the Lean community that has evolved out of the automotive industry.
“We’re finding that just by presenting data in a different way, it provides a whole new level of insight that the people we’ve been showing this work to have found extremely both eye-opening and informative. We are currently working on some large-scale major projects as demonstrators where we’re putting this into practice. And the key is to find a consistent method of metrics that can be adopted by all,” he explains.
How quantifying offsite manufacture benefits led to new approach
One area of the Centre’s research that has surprised Professor Middleton came out of its efforts to quantify the benefits of offsite manufacture, which he regards as a central plank of the industry’s approach to transforming itself.
“I am convinced that it is the future and the challenge is how we make it happen,” he says.
The Centre had an opportunity to work with the Construction Industry Research and Information Association (CIRIA) to look at the issue in depth by studying school construction in an area of the UK where there is a lot of offsite work underway alongside conventional builds.
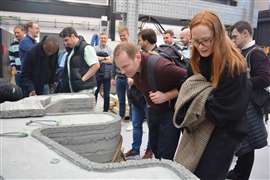
“We were very fortunate to work with a number of school contractors that were delivering these programmes. It was a case of building trust but effectively they shared their data with us,” he explains.
“These were top-tier companies delivering a range of schools and what we found was there was an inconsistency in how they approached measuring performance. It wasn’t just between companies, it was actually even within some companies from project to project. There was a lack of consistency in how you define cost, programme, quality. It wasn’t a case that some were right or some were wrong – it was a case that you couldn’t compare progress.”
The schools study resulted in a new methodology, published in 2020 by CIRIA called Methodology for quantifying the benefits of offsite construction (C792F).
“But what we realised is that what we had actually produced was a methodology for measuring construction performance across the whole industry. And several years down the line, that has formed the basis of what has evolved into a framework for performance measurement for construction,” he says.
“Consistency is crucial. And so now we need as many different organisations within the industry as possible to collect this data using the same sort of framework so that it can be properly measured. But we need buy-in and we need to work with industry. It’s no good academics coming in and saying ‘you need to measure X, Y and Z’. Often it is not practical or economic to collect. And then, is it actually used?
“So we’ve spent a lot of time sitting down on site talking to everyone from the foreman to the project manager about what we need to understand the performance and how feasible it is to get that data. The danger otherwise, which you often see, is you end up being drowned in a data swamp. We need less data at first but collected in a consistent way to demonstrate its value, and then build up for that.”
The Construction Data Trust
Working alongside the Construction Productivity Taskforce, the Centre is also involved in the Construction Data Trust. In conjunction with companies like Microsoft, developer British Land, and major contractors like Mace, Skanska and Sir Robert McAlpine, it aims to build a structured collection of data for the industry that can be used to establish benchmarks to understand what is achievable in the industry.
“It’s a very exciting initiative and what has been surprising is the huge variability we are finding in the performance of, for example, building a multi-storey commercial development in London,” he says.
“They are very similar projects but with a massive range of performance. Sometimes it [the variability] is even within projects. Working with our construction partners, our goal is to help them get insight into why this variability is there and what we can do to address it and improve productivity.
“I believe this could be an opportunity to change the industry far more quickly and dramatically and the timing is perfect because we are in a technological revolution with machine learning, artificial intelligence and data collection.”
‘Nike philosophy’ to construction
To effect meaningful change in construction, Professor Middleton advocates adopting what he calls a ‘Nike philosophy’: Just do it.
“My mantra is that underpinning everything is how we procure construction. And by procurement, I don’t just mean what contract you use but the wider context of how we approach planning of construction projects: how we procure them, how the design is incorporated, how we get contractors involved.
“What we’re trying to do now is find those exemplars around the world of where things have really worked. We want to go and measure them, show those outcomes, and bring them to policymakers to give them the encouragement to just do it.”
STAY CONNECTED

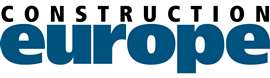
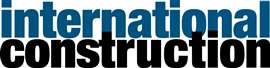
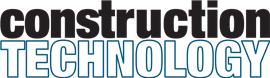
Receive the information you need when you need it through our world-leading magazines, newsletters and daily briefings.
CONNECT WITH THE TEAM
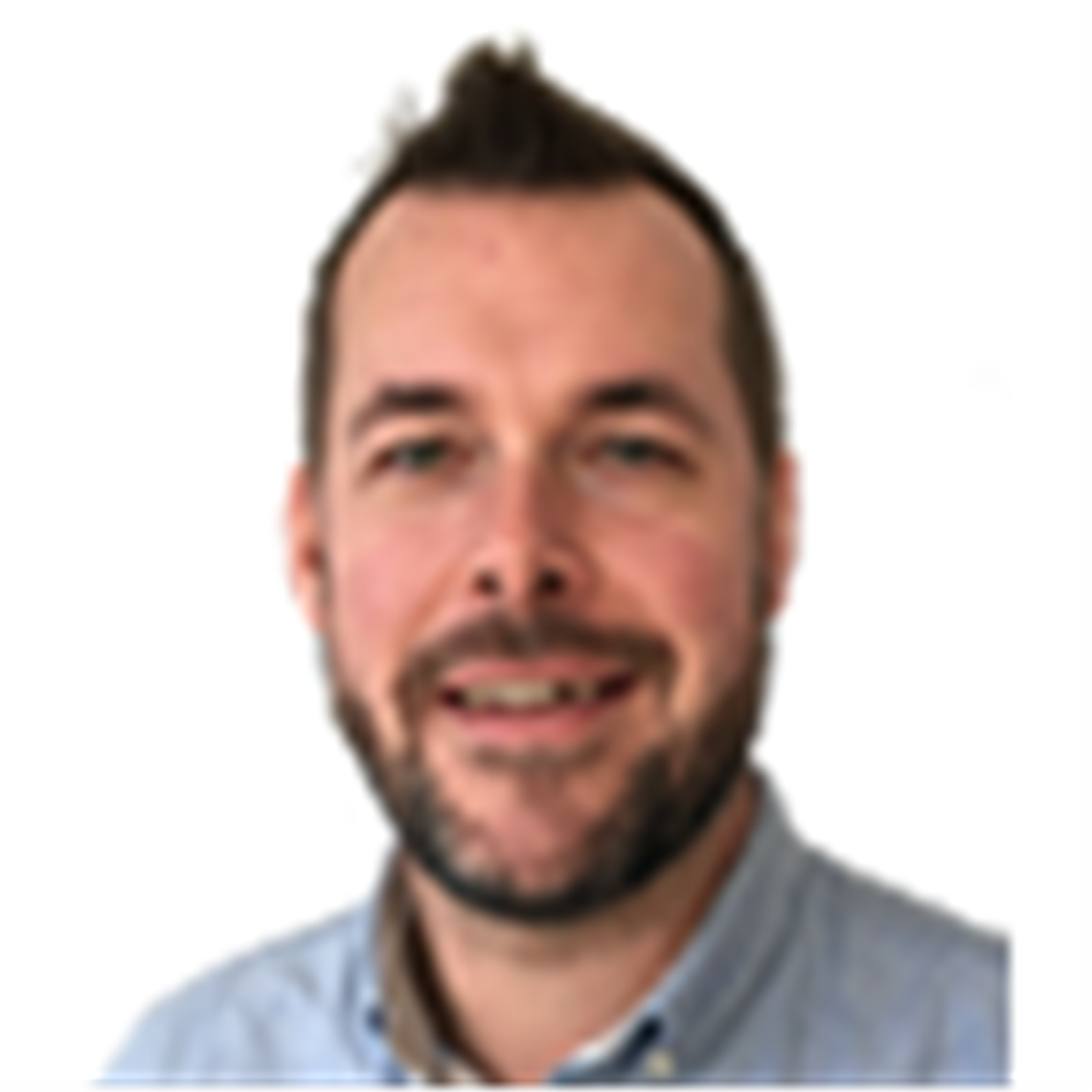
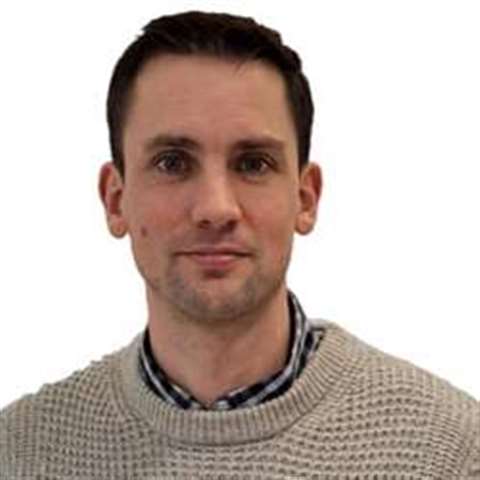
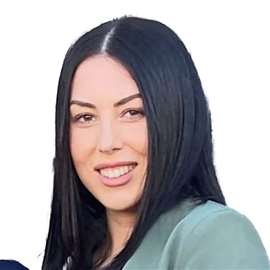
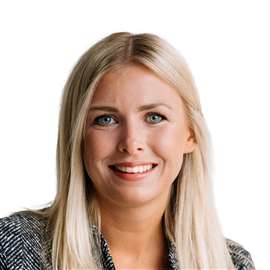