Read this article in French German Italian Portuguese Spanish
5 different ways to control construction labour costs
03 May 2024
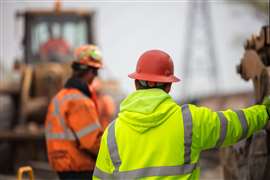
Brian Kassalen, partner and construction leader at Baker Tilly suggests five ways construction companies can control costs.
If there’s a “wild card” in construction costs, it’s labour.
It’s much easier to estimate fixed costs like permits, insurance and taxes, and the variable costs of materials like concrete, steel and wood.
Labour, which often accounts for 20-40% of the final costs, adds complexity to construction estimates and can make or break a final profit. Savvy builders and developers can shift the odds in favour of their profitability if they consider five different ways to help control construction costs:
1) Hire good project managers
Good project managers have strong communication skills – both interpersonal and written – and keep tabs on their workforce. If they are active and engaged in construction projects, they know if their workers meet deadlines, reach targets, and adhere to labour budgets. In turn, they can keep senior management accurately updated on a project. A word of advice – if you have a first-class project manager with a solid reputation for excellence, treat them well and show your appreciation or another company may hire them.
2) Invest in technology
The latest artificial intelligence (AI) and construction software can help streamline labour needs. These technologies allow a live look at estimates, labour and materials. By looking at the real-time balance, construction managers can quickly identify if they’ve gone through 60% of the labour budget with only 30% of the project done. Technology can also help reduce the need to be onsite with virtual construction tools and automating inventories, thereby increasing productivity.
Robots are starting to offer the potential to help address labour issues for a variety of construction tasks, including surveying and even bricklaying. This looks set to grow in the future. From an affordability perspective, construction robots appeal most to large developers with substantial projects. Smaller and midsize builders and developers may shy away from technology investment due to cost, but to their detriment, they will quickly find themselves behind in an industry that is addressing labour shortages with automation and digital solutions.
3) Conduct a robust scheduling analysis
Successful project managers regularly look closely at scheduling to ensure they have the right mix of labour and skills. They ask themselves, “Do I have the right mix of people and experience? Are we overstaffed or understaffed in any areas? Are we using everyone to their best abilities?” Fortunately, technology is, once again, our friend.
Dozens of software packages are available to help manage labour costs. Their features vary based on price and sophistication. For example, some software applications feature the ability to create Gantt charts to help visualize and understand construction schedules and tasks. Most packages offer resource management features and compatibility with other tools and systems used in construction workflow. Others have communication tools to collaborate with owners, general contractors, subcontractors, and engineers. Many software packages also have a sister app that allows project managers and field personnel to access and update schedules from their phones while on the job site.
4) Perform regular project audits
Regular audits ensure a system of checks and balances on the construction site and labour costs aren’t spiraling out of control. Audits keep project managers honest and accountable by comparing budgeted labour costs to the actual costs. The construction companies can do internal audits or can engage a third party to perform the review. Audits help determine what’s happening on the job site and whether the project is on track. Again, technology is our friend when auditing and monitoring job performance and ensuring critical timelines are met.
5) Invest in your employees
Employee retention is sometimes overlooked in the labour cost model. Development and training are vital in retaining construction employees. Workers who feel valued and are learning and growing are more likely to stay with the company. Many companies – and unions in the United States – offer employees professional development through apprenticeships. Continual job training allows employees to work more efficiently and effectively by exposing them to the latest tools and techniques.
Globally, we have seen a continual decrease in skilled labourers like electricians and carpenters, as many senior workers retire from the construction trades. Retaining these older workers can also help address labor shortages as companies look at ways to retain them. Experienced workers are a valuable resource, even as part-time or seasonal workers.
Retention and motivation of construction workers can also be affected by earned incentives. An earned incentive rewards people for actual results based on predefined and precise tasks, accomplishments, and milestones. Most often, we see these as bonuses offered if a job gets done more quickly than planned, saving the company money while passing some of the cost savings to employees. Safety rewards are also sometimes used. Accidents and related safety investigations can also slow down a project, so many companies offer additional incentives to employees if there are no accidents or safety violations on the worksite.
An optimistic outlook for controlling labour costs
On the bright side, construction companies can access many strategies and tools to help control labour costs. Companies that use these resources can better manage labour issues, even during a global shortage of skilled workers. More importantly, an in-depth analysis of labor costs also forces construction companies to think “future forward” and operate more predictably, taking the wild card out of labour.
Brian Kassalen is partner and construction leader at Baker Tilly.
|
STAY CONNECTED

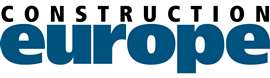
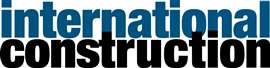
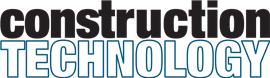
Receive the information you need when you need it through our world-leading magazines, newsletters and daily briefings.
CONNECT WITH THE TEAM
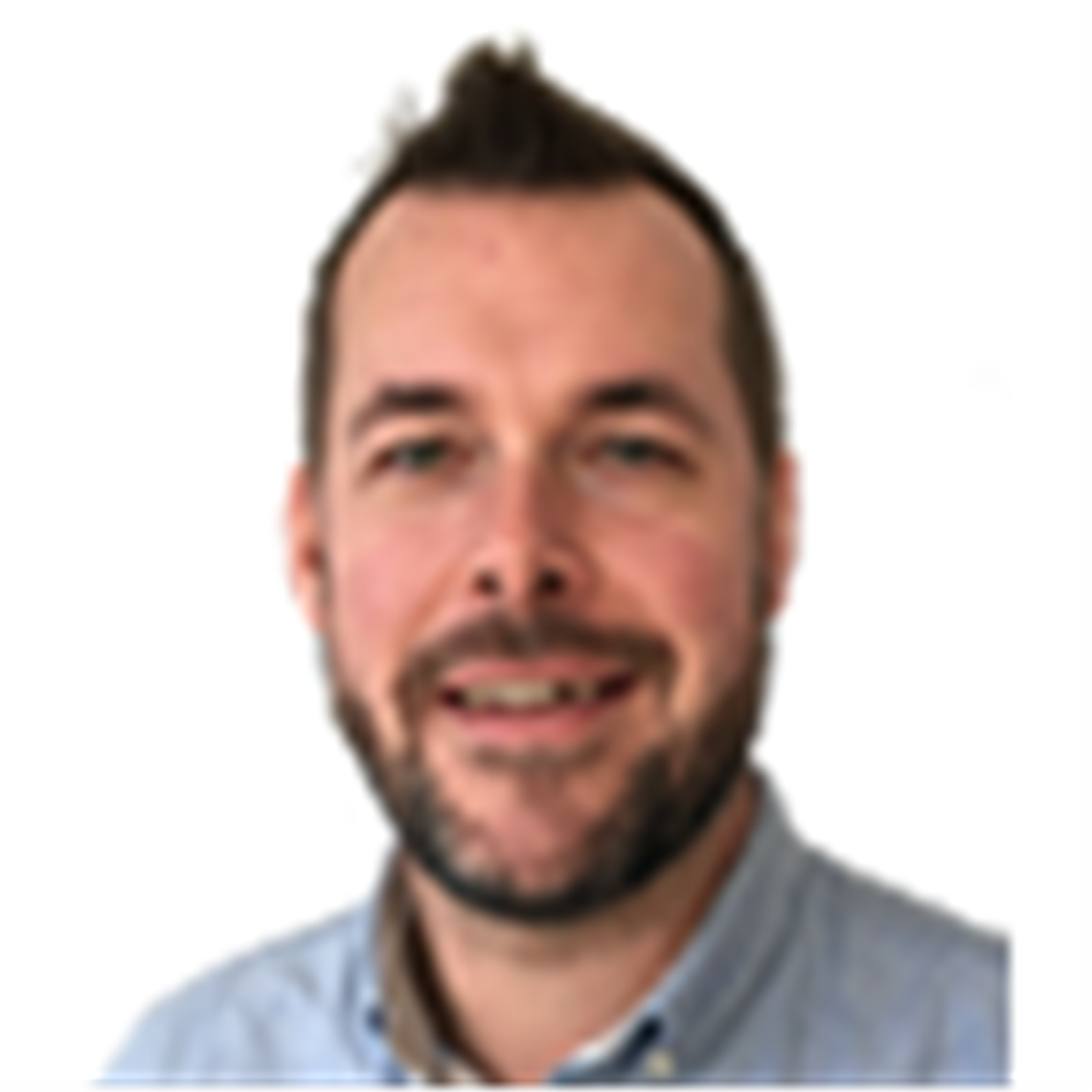
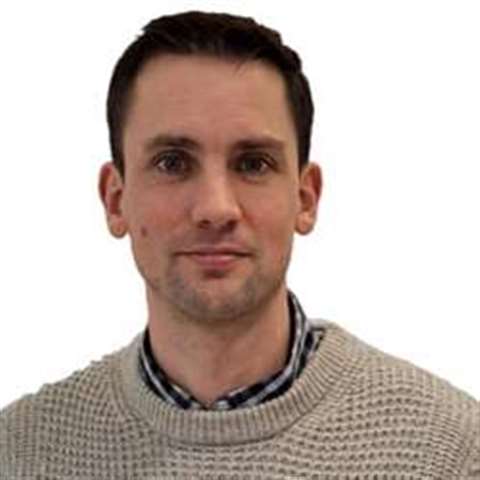
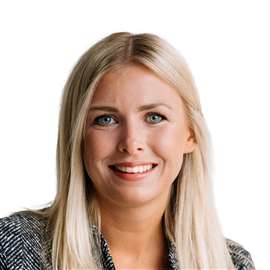