Read this article in French German Italian Portuguese Spanish
Why construction in the Netherlands has gone to pot
13 February 2024
Known around the world for its marijuana-selling coffee shops, the Netherlands is looking to cannabis as a low carbon building material. Lucy Barnard reports.
Located on a nature reserve between the Veluwe hills and the Ljssel valley, the Dutch municipality of Voorst lies just over an hour’s drive away from Amsterdam.
While the capital’s 164 licensed coffee shops attract more than 1.5 million visitors each year, keen to take advantage of the Dutch government’s tolerant soft drugs policies, in Voorst cannabis is changing the urban landscape in an entirely different way – as a building material.
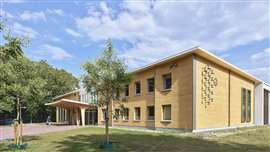
Voorst townhall in the Dutch village of Twello, which was nominated for the Royal Institute of Dutch Architects (BNA) Best Building of the Year Award 2023, is the biggest building in the country to be built using ‘hempcrete,’ a building material that mixes cannabis or hemp fibres with a lime-based binder and water.
Industrial hemp – a type of cultivated cannabis less likely to get you high than its marijuana cousin - has been used in construction since medieval times, typically in houses or farm buildings, mostly due to its good insulating properties and light weight. On top of that it is long lasting, does not shrink and is pest, water and fire resistant.
Although hempcrete is lighter and less dense than traditional concrete, making it harder to use to support the structure of a building, advocates say hemp’s many environmental benefits make it a sustainable alternative to concrete for many applications.
Over the past decade, the material has started increasing in popularity due to the fact that the fast-growing plant has carbon capturing properties and has already been used on projects around the world including affordable housing in Texas, a sports hall near Paris and even a 12-storey tower in Cape Town.
How sustainable is hemp for construction?
Joost Roefs, board member of De Twee Snoeken, the Dutch architectural firm which Voorst Municipality appointed in 2020 to revamp and retrofit the 1980s-built Voorst Municipality city hall, says that the use of hempcrete fitted with the Municipality’s aim to create a building that would be “the epitome of sustainability” to replace its 1980s-built original which had become no longer fit for purpose.
Initially, the team had wanted to use another traditional building technique, rammed earth, where layers of damp earth are poured into framework and then compressed to around half their original volume, creating a freestanding structure. However, rammed earth’s poor insulation value meant that additional insulation material would have been needed.
Roef’s next choice was to use hempcrete – a material which could be produced relatively locally and continues to absorb carbon over its lifespan.
“We initiated the use of hempcrete as a façade material. We introduced the Municipality of Voorst to the material and explained why it was a suitable building,” Roefs tells Construction Briefing.
As hempcrete had never been used on a similar scale in the Netherlands before, the architect came up with an alternative traditional brick façade building too. After extensive research including two visits to reference projects, various thermal and fire tests, and work with bio-based construction contractor EcoBouwSalland to come up with a execution and work sequence, Roefs presented his findings to the Municipality.
To Roef’s delight, the Municipality agreed, greenlighting the decision to create a total of 1,180 square meters of hemp lime facades and using Keim silicate paint to protect it.
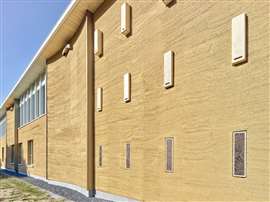
The project required a total of 13 hectares of hemp, which was grown in the Dutch province of Groningen.
According to the European Commission, one hectare of hemp sequesters up to 15 tonnes of CO2 from the atmosphere and only takes five months to grow, making it better than typical commercial forestry at sequestering carbon. Roefs estimates that this means that the hemp in the building alone accounts for 195 tonnes of CO2 which have been captured and stored.
Moreover, the lime mortar used in the construction also acts as an overall carbon sink, Roefs says. Like cement, lime gives off carbon dioxide during its manufacture. However, unlike cement, lime mortar then goes on to reabsorb CO2 during its production process and while it is in use. The lime used in the Voorst town hall façade was quarried in nearby Belgium and transported by barge along the Maas River, again keeping the carbon footprint low.
“This lime is so pure that it has a food-grade label,” Roefs says. “During its carbonization process, which takes decades, the lime absorbs as much CO2 as it emitted during the physico-chemical reaction in the production process. The lime is burned at the lowest possible temperature. It was transported in bulk via the Maas River by barge and it matured on its way to the building site.”
After the chopped hemp wood and lime had arrived at the construction site, the hemp and lime were mixed with water and poured into a formwork and pounded around the pillars of a wooden skeleton.
Casting hempcrete on site
Roefs says the team decided early on to cast the hempcrete on site rather than using factory-made pre-cast blocks because it meant they could create larger complete sections.
“By realizing the hempcrete façade on site, we were able to preserve the beautiful, marbled structure of the hempcrete,” he says. “Because as we did not manufacture them in a factory, we could create high sections instead of separate, smaller façade elements.
“The appearance and structure of the hempcrete façade we hoped to realize, have come into their own very well. Thanks to the marbled structure, it gets a very natural look and looks beautiful in the landscape,” he adds. “The concave wall panels show very nicely that the shape possibilities of hempcrete are enormous. It has become clear that building with hempcrete gives total freedom of form.”
During the construction, a total of 14 craftsmen worked on the façade at the same time, using a 46-foot-wide temporary platform to fill the formwork with hempcrete.
The drawbacks of hempcrete in construction
Nonetheless, working with a relatively untried material came with complications, Roefs admits. The hempcrete mix created by the team took longer to dry than expected, resulting in a series of cracks which had to be painstakingly repaired.
“The unforeseen occurrence of cracks was a part of the innovation and learning process,” Roefs admits. “We ensured that these cracks have been fully repaired. We also investigated the cause, allowing us to anticipate the same thing happening in future projects.”
Another issue faced by construction firms looking to incorporate hemp into buildings is the difficulties associated with getting hold of the material.
Even though industrial hemp plants grow and thrive in many climates, the fact that the plant belongs to the same species as cannabis has meant that growing it as a crop has been banned or heavily regulated in many countries.
Both marijuana and hemp were effectively made illegal in the USA in 1937 and banned outright in 1970 until a law change in 2019. In the UK, all hemp growing was banned in 1971 until the rules were relaxed for industrial hemp in 1993.
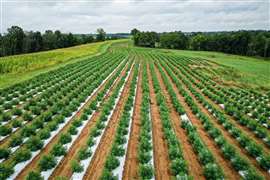
Currently different national governments have differing rules over which particular hemp plants they allow to be grown, mostly based on the level of tetrahydrocannabinol (THC) chemicals contained in each strain.
In the European Union, only strains of hemp with THC levels of 0.3% are allowed to receive EU subsidies while member states may set their own rules regarding which crops can be legally grown.
These supply chain difficulties mean that the use of hemp can push up construction costs compared with traditional builds.
Roefs says that the Voorst town hall construction cost a total of €10.3 million, with construction costs kept low mostly due to the fact that the municipality preserved the concrete structure of the building.
“The hempcrete was not inherently more expensive than a linear alternative such as a brick façade,” he says. “We were able to complete the entire project on schedule and within budget.”
A more pressing issue for Roefs was that because hempcrete had not been used to such a scale before in the country, getting the necessary technical certifications required proved challenging. Roefs says that the team had to conduct some of these itself including fire safety tests with the Dutch certification authority KIWA.
“The reason that more builders are not using hempcrete at the moment is mainly due to unfamiliarity with this material,” Roefs says. “At the moment only a few parties can work and build with hempcrete in this manner.”
Moving into the mainstream
Nonetheless, Roefs says that he believes that as pressure continues to mount on construction teams to move to more sustainable alternatives, hempcrete will continue to move into the mainstream.
“In terms of ecology, we look optimistically towards the future,” he says. “The biobased material hempcrete serves as a soil conditioner after the building’s lifespan and even offers possibilities for farmers to reorganize their businesses through hemp cultivation. In this way, it contributes to the societal debate about the future of agriculture.”
“We strongly believe in this material and see a promising future for it.”
Brought To You By
|
STAY CONNECTED

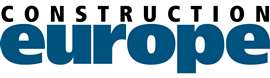
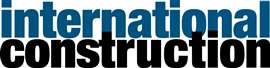
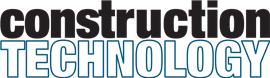
Receive the information you need when you need it through our world-leading magazines, newsletters and daily briefings.
CONNECT WITH THE TEAM
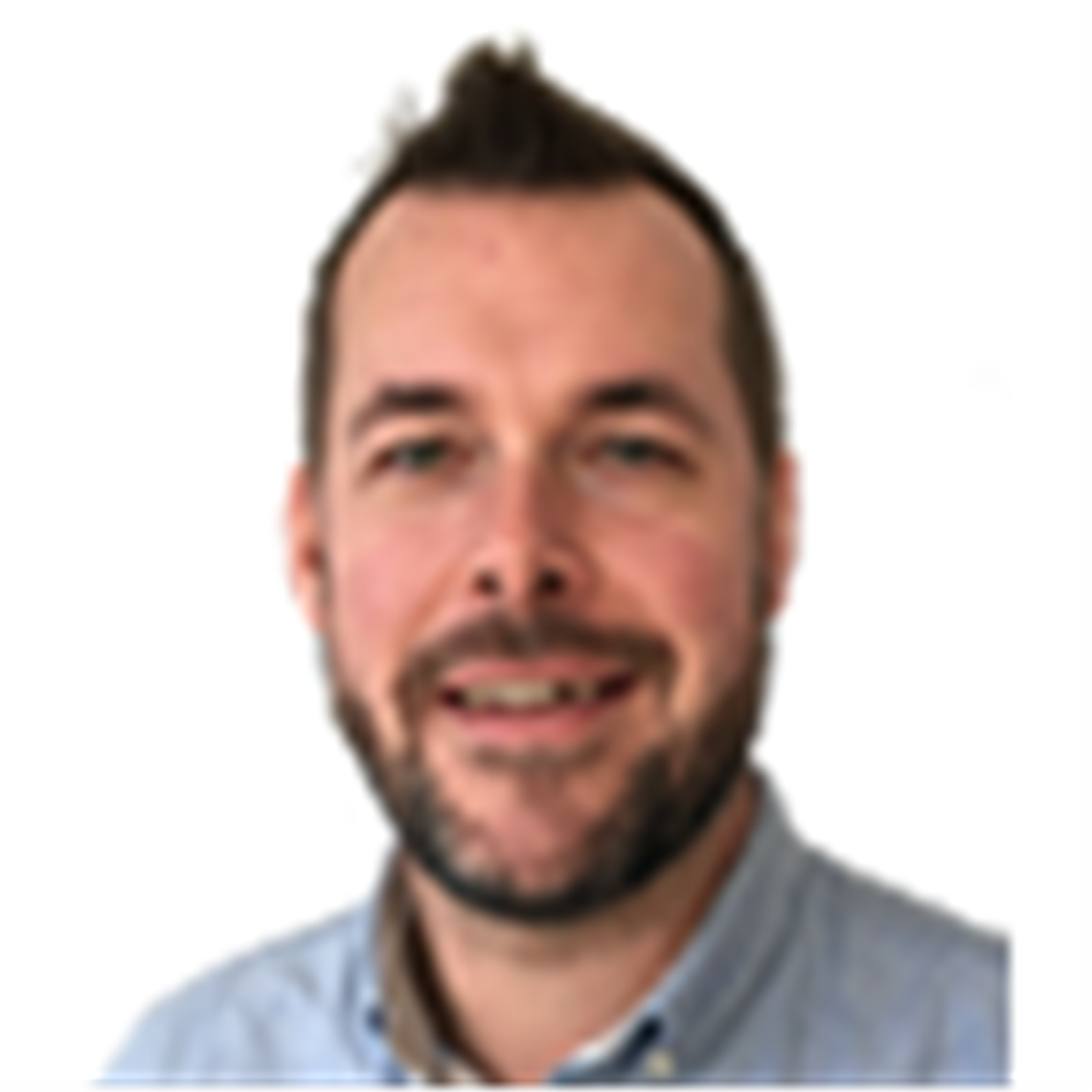
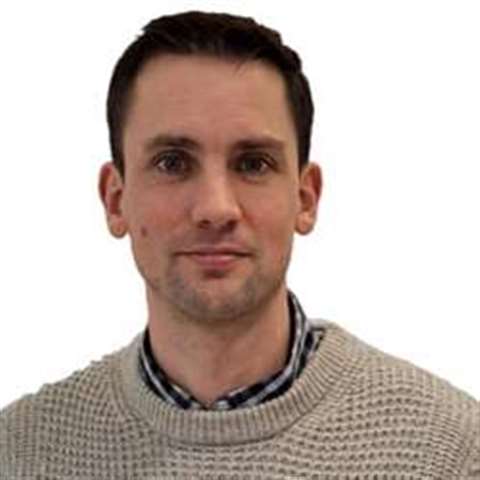
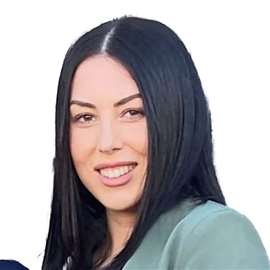
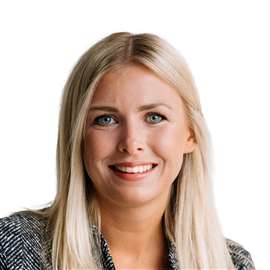