Read this article in French German Italian Portuguese Spanish
Climbing higher: What’s the latest in European high-rise construction?
02 July 2025
While much of the world continues to build taller, Europe is charting its own course by embracing smart construction methods and refined systems to meet growing demand for high-rise development.
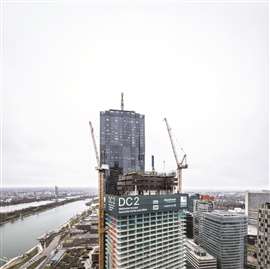
Historically, regions like China, the Middle East, and the US have dominated the skyline with massive towers, driven by rapid urbanisation and economic growth.
But, as the Council on Tall Buildings and Urban Habitat (CTBUH)’s survey of the tall building landscape for 2025 reveals, the global picture is more challenging these days. A record 260 projects over 200 metres tall are currently on hold worldwide, with 192 of these in China, where tightened financing and real estate market challenges have stalled development. Yet despite these setbacks, China remains a dominant force, having delivered six of the ten tallest buildings completed globally in 2024.
By comparison, Europe’s high-rise activity remains modest, with skyscrapers concentrated mainly in cities like London, Paris, and Frankfurt. However, this traditionally cautious approach to vertical construction is beginning to shift. Spurred by advances in falsework, formwork, and tower crane technologies, European contractors are now better equipped to tackle the complex logistical, safety, and efficiency challenges of building taller structures, even if the number of such projects remains comparatively small.
Improving speed and efficiency
This shift is reflected in the growing adoption of advanced climbing and formwork systems, which were highlighted at Bauma in Munich, Germany, in April. Jonas Hab, junior product application engineer at Peri, explained some of the advantages of the company’s Rail Climbing System (RCS).
He said the ability to link up to 64 platforms was a key factor in improving speed and efficiency across a wide range of projects.
“For example, in Frankfurt, on the Tower Four high-rise project, we only needed one hour to complete a climbing cycle. That’s incredibly fast — normally in Europe, it would take around half a day. Here, we only needed eight workers and one hour, and that was it. This really improves the workflow for our customers.”
Peri’s RCS is designed to enable the safe and efficient movement of climbing formwork – and recent updates have made it even more versatile. With the introduction of new solutions like RCS MAX Shaft, Peri says that it can now be used economically on smaller projects too, allowing formwork to be moved in small to medium-sized shafts without the need for a crane or special components.
Hab added that the same system is now being used at the DC Tower 2 in Vienna, where the project is already three months ahead of schedule due to the speed of the climbing system. “Now, the slabs have actually become the bottleneck because they can’t keep up with how fast we’re climbing,” he said.
On the DC Tower’s exterior shaft, the team is also using Peri’s RCS Next system, which allows everything to climb hydraulically. “We have the driving rail and our pumps installed, so at each level we simply climb up hydraulically. After that, the hydraulic system disassembles, and all the other processes take place.”
Europe’s high-rise scene
Vienna might not be the first city that comes to mind when it comes to skyscrapers — places like London and Frankfurt have long dominated Europe’s high-rise scene. But Austria’s capital could be about to show them how it’s done.
The DC Tower 1, designed by French architect Dominique Perrault, stands at 250 metres, making it Austria’s tallest building. Now, its companion, DC Tower 2, is under construction nearby, further transforming Vienna’s skyline.
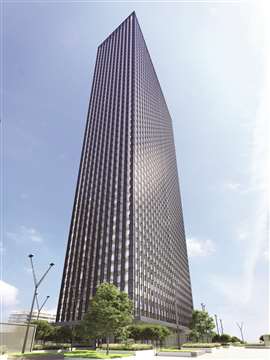
At 53 storeys and with five basement levels, the tower is being constructed on what is likely the deepest private-sector excavation in Vienna to date. Built by Austrian contractor Porr, the site presented exceptional challenges due to its dense urban surroundings: flanked by DC Towers 1 and 3, hemmed in by major road networks, the U1 underground line, and just metres from the Wien Kanal (Vienna canal).
The 22.7-metre-deep construction pit required an extensive range of specialist techniques, including diaphragm walls, jet grouting, dewatering, and low-pressure injections. Despite the complexity, Porr completed the specialised civil engineering works on schedule between March 2022 and May 2023, with the entire project expected to finish in 2026.
Similarly complex and ambitious towers are taking shape elsewhere in Europe. In Karlskrona, Sweden, the NKT Tower 3 has been completed at a height of 200 metres, making it the second-tallest tower in Scandinavia.
Built by Skanska, the structure will form part of what is expected to become the world’s largest high-voltage submarine cable manufacturing facility. The cables produced at the site will support renewable energy projects, including wind farms and solar parks.
Two Liebherr tower cranes, a 542 HC-L 12/24 Litronic and a 258 HC-L 10/18 Fibre, were used throughout the construction. Supplied from Liebherr’s rental fleet, the cranes supported the rapid build programme, which took place over a 90-day period. The cranes reached final working heights of 213 metres and 210 metres, respectively.
Liebherr’s Tower Crane Solutions (TCS) team also provided engineering support, including tie-in geometry calculations, structural loading data, and the design of tower bracing. Climbing steps and other operational aspects were pre-planned to suit the project’s schedule and structural demands.
Construction was carried out using a four-shift system, allowing for 24-hour activity. On average, the structure rose by approximately 2.6 metres per day. The completed tower has a footprint of 23 by 23 metres and a total volume of 112,445 cubic metres – roughly equivalent to 45 Olympic-sized swimming pools.
The project was delivered through coordinated work between Liebherr’s TCC and TCS teams, Skanska’s tower crane management, and Ekström Lyftkonsult AB, a local specialist consultancy.
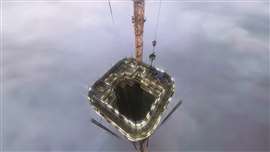
Streamlined solutions
As high-rise construction becomes faster, taller, and more complex, the pressure is growing for contractors and suppliers to deliver smart, streamlined solutions. Digital platforms, automation, and real-time data are no longer optional extras – they’re necessary tools for managing the scale and speed of modern building sites.
At Bauma, Doka demonstrated how it is addressing these challenges head-on with its new digital customer platform.
“In many ways, how we interact with our customers is still a bit old school – a lot of phone calls, a lot of emails, a lot of paperwork being shuffled back and forth,” Robert Hauser, CEO at Doka, explains. “We knew we needed to take this to the next level.”
That next level is Doka 360, a fully integrated platform where customers can manage every aspect of their projects digitally, from planning and ordering to tracking deliveries and managing materials on site.
Users, such as infrastructure site managers, log in to a personalised dashboard where they can view all active projects, track deliveries in real time, monitor material stock, and even handle returns.
“Everything you need for your projects is right there with one login — no jumping between different applications,” Hauser adds.
Doka 360 also integrates applications like DokaXact, which uses sensors embedded in formwork to measure concrete pressure and curing status. Alerts are pushed directly to the user’s dashboard, allowing real-time monitoring and faster decision-making on site.
Material management is similarly streamlined. “When materials are dispatched, en route, or delivered, the customer can see everything here,” Magdalena Auer, digital strategy and transformation manager at Umdasch Group says. In future updates, Doka plans to let users adapt the delivery of ordered items even after dispatch, giving customers even more control over the logistics flow.
The project wasn’t a quick turnaround. “It was a slow but massive effort,” Hauser explains. A task force from different departments came together to build the platform with Bauma in mind as the deadline.
“When you look into other industries, for example, take Amazon, it’s state of the art,” Hauser says. “And we asked ourselves, why not create the same thing?”
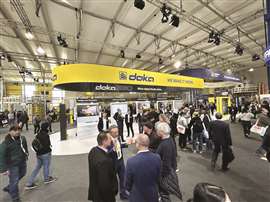
And while retail platforms deal mainly with simple purchases, Doka’s platform handles complex processes like rental agreements, project-specific planning, and technical engineering – all within one system.
Designed with user-friendliness at its core, Doka have UX experts in house with backgrounds in consumer digital products. “We really tried to make it as user-centric as possible,” Auer says.
A dedicated early access phase with selected partner companies in Germany and the US will begin in July 2025. The initial rollout in these markets is planned for 2026, with further countries to follow.
As contractors and manufacturers adapt to the complex logistical and engineering challenges of vertical construction, Europe is carving out a distinct high-rise identity – one defined not only by scale, but by innovation, precision, and efficiency.
STAY CONNECTED

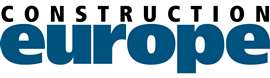
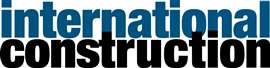
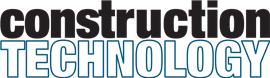
Receive the information you need when you need it through our world-leading magazines, newsletters and daily briefings.
CONNECT WITH THE TEAM
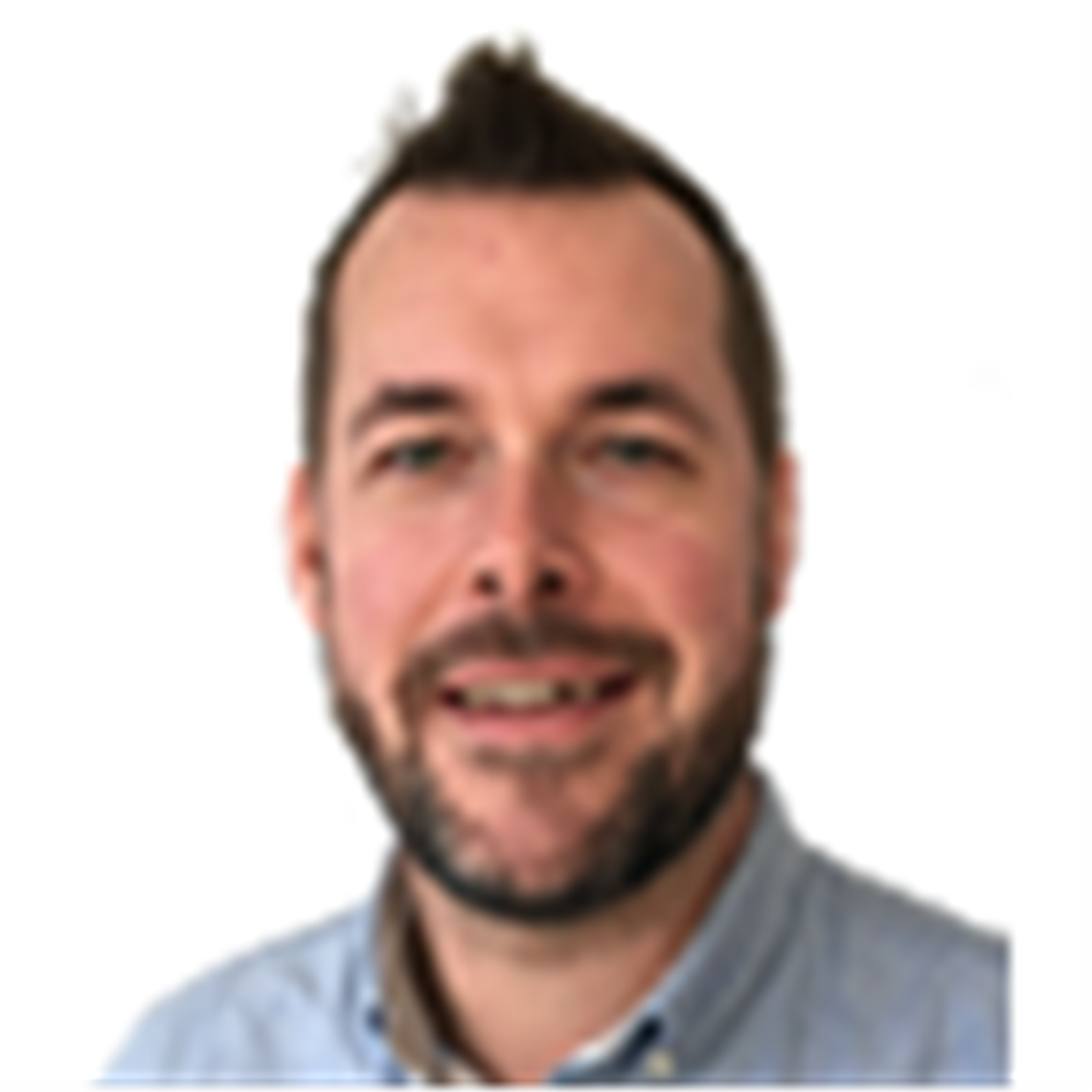
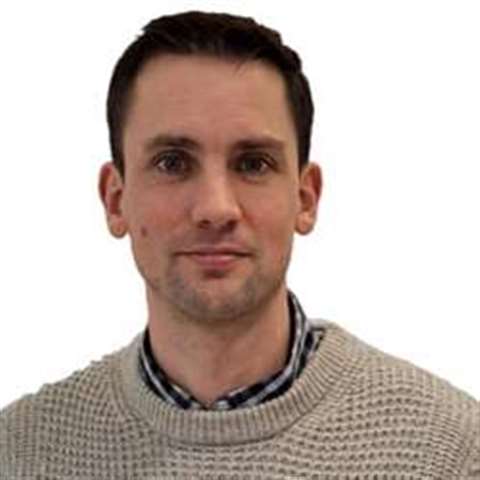
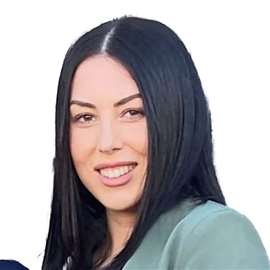
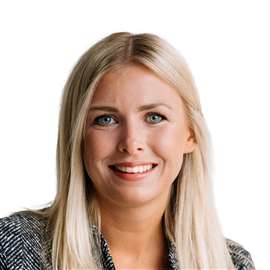