Read this article in French German Italian Portuguese Spanish
Liebherr pushes autonomy and hydrogen from concept to reality
25 July 2025
While autonomous construction machines are no longer the stuff of science fiction, they’re not quite an everyday reality either – something that could be about to change. Liebherr is preparing to launch a commercial version of its autonomous wheeled loader kit by the end of this year, marking a major step from pilot testing to real-world deployment.
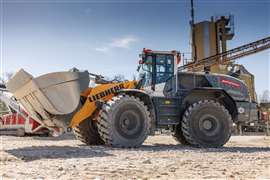
“It is already in a serial production status and now we need to sell it. This is the next status. It’ll be available commercially around the end of the year,” Jürgen Appel, head of technology coordination, Liebherr-International AG, tells Construction Briefing.
“There is a mobility kit with additional sensors and computers. Customers might not order big amounts, maybe just one in order to see how it works. You take a machine that is already on the market and you would equip it with the technology.”
The (sometimes scary) speed of AI
Appel speaks pitch-perfect English and, as befitting a man with his job title, chooses his words precisely. He says that the pace of learning of the artificial intelligence (AI) in the wheeled loader surprised him. When the wheeled loader was initially used it only half filled its bucket – something that changed rapidly.
“It was trained over the weekend and then on Monday morning the wheel loader was as good as our best people. This was, for me, a big surprise. I said, ‘okay, now it’s the time for artificial intelligence, it is here,’” he says with a laugh, still marvelling at its sheer pace of improvement.
While there is no one in the cab, human involvement remains: the autonomous loader’s daily tasks are set up via computer each morning, and its progress can be tracked periodically by the same interface.
The wheel loader was chosen because of its repetitive actions – something that can lead to mistakes and boredom for human operators but provides ideal training material for AI systems.
Appel says that the technology that Liebherr is using for the wheel loader is “the base that will be suitable for all kinds of machines,” hinting at a future with other automated Liebherr equipment.
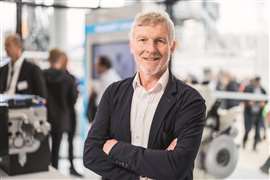
From autonomy to power
While electric machines are now operating on jobsites globally, their adoption still trails diesel significantly. Hydrogen-powered equipment, meanwhile, is in a similar position to autonomous machines – mostly confined to controlled trials.
And, just as before, it could be that it is Liebherr and a wheel loader that proves to be the disruptor, albeit on a longer time frame, with Appel revealing that their hydrogen wheel loader could be commercially available by 2029, although there is no definitive date yet.
When asked about the potential of hydrogen and Liebherr’s approach he pauses to think before answering slowly at first, then picking up speed, “It is a good question because what is our approach to this? There are billions, trillions of dollars being invested in the hydrogen economy. It seems clear that hydrogen will be one of the big energy carriers in the future.”
The company is researching both fuel-cell and hydrogen combustion engine solutions. Of the two, combustion is more straightforward, given Liebherr’s long-standing engine expertise.
Regarding hydrogen combustion engines Appel says, “We are in the phase that we are making our engines. I would say that they are good and almost ready for serial production. We are not there yet though.
“Now we are in the test phase in the field and gaining a lot of information; what is good and what is not good. This will lead to what we could potentially see on the next Bauma, not the prototype, but the first serial machine of a hydrogen powered wheel loader.”
Hydrogen fuel tanks are significantly larger than diesel tanks, requiring longer machines, but Appel says the bigger challenge lies elsewhere: infrastructure and safe fuel delivery.
“You have to have in mind that you don’t only need to take care of the machine, but also for the complete availability and the infrastructure around the machine,” he confirms.
“Our customers are asking us, how can I fill the tank when it’s outside somewhere on a site? We said, okay, we are taking care of the technology development of mobile refuelling of these machines. So we are involved there with partners to ensure there is some kind of infrastructure to make it easier for our customers.”
Despite the challenges involved in hydrogen he clearly sees great potential, although he is keen to stress that he is not a fortune teller with a crystal ball – the logically minded Appel is about as far removed from a mystic as one could imagine.
“If these kind of machines with this kind of energy will be there and customers are asking for it then we are prepared. For this, of course, it’s a bit of a bet on the future. I do not have the glass ball, nobody has.”
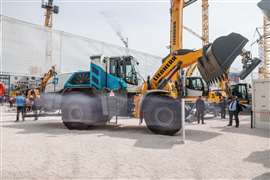
Construction’s engineering challenges
One aspect of technology developing quickly is battery electric, with Appel saying that they are now able to power machines larger than he would have thought possible in the past.
Part of this is down to the partnership Liebherr has with Fortescue – it was announced last year that the companies will develop zero emission mining solutions, which will result in the supply of 475 new Liebherr machines to Fortescue’s operations Australia.
Valued at up to US$2.8 billion, the deal is the largest equipment agreement in Liebherr’s 75-year history.
“Batteries are heavy and extremely expensive and so we thought for smaller machines it would be a suitable approach and we couldn’t imagine that it will also fit for larger machines. But the Fortescue development drives us towards thinking beyond hurdles…. you can do nearly every machine battery electric. The question is: is it always the best solution?”
As he alludes to, the price of batteries has been a barrier to their adoption, but he says that the price will continue to decrease in the future as the performance increases, leading to a situation where the proposition may look markedly different in the future.
As well as hydrogen and electric there are other power options. Appel mentions ammonia engines and ethanol engines as having potential for the future, leading him to say, somewhat ruefully, that, “from an engineering standpoint, the world was much easier ten years ago. The concept of a new engine was you take a diesel and make it a bit better. Now you have in mind that you have to reduce the emissions. You have different kinds of technologies; you need to make it as good as the diesel machine for reliability. That’s why it takes a certain amount of time to have this technology available as good as before.”
Autonomous machines and battery-powered behemoths are engineering challenges being tackled now with commercial outcomes in sight, while hydrogen combustion engines are under active development but will require a longer timeline before serial production is realistic. The world may have been simpler for engineers a decade ago, but given how passionately Appel talks about these developments, you get the sense that he wouldn’t have it any other way.
STAY CONNECTED

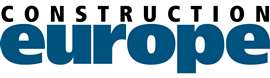
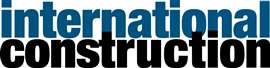
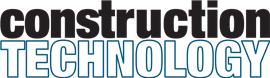
Receive the information you need when you need it through our world-leading magazines, newsletters and daily briefings.
CONNECT WITH THE TEAM
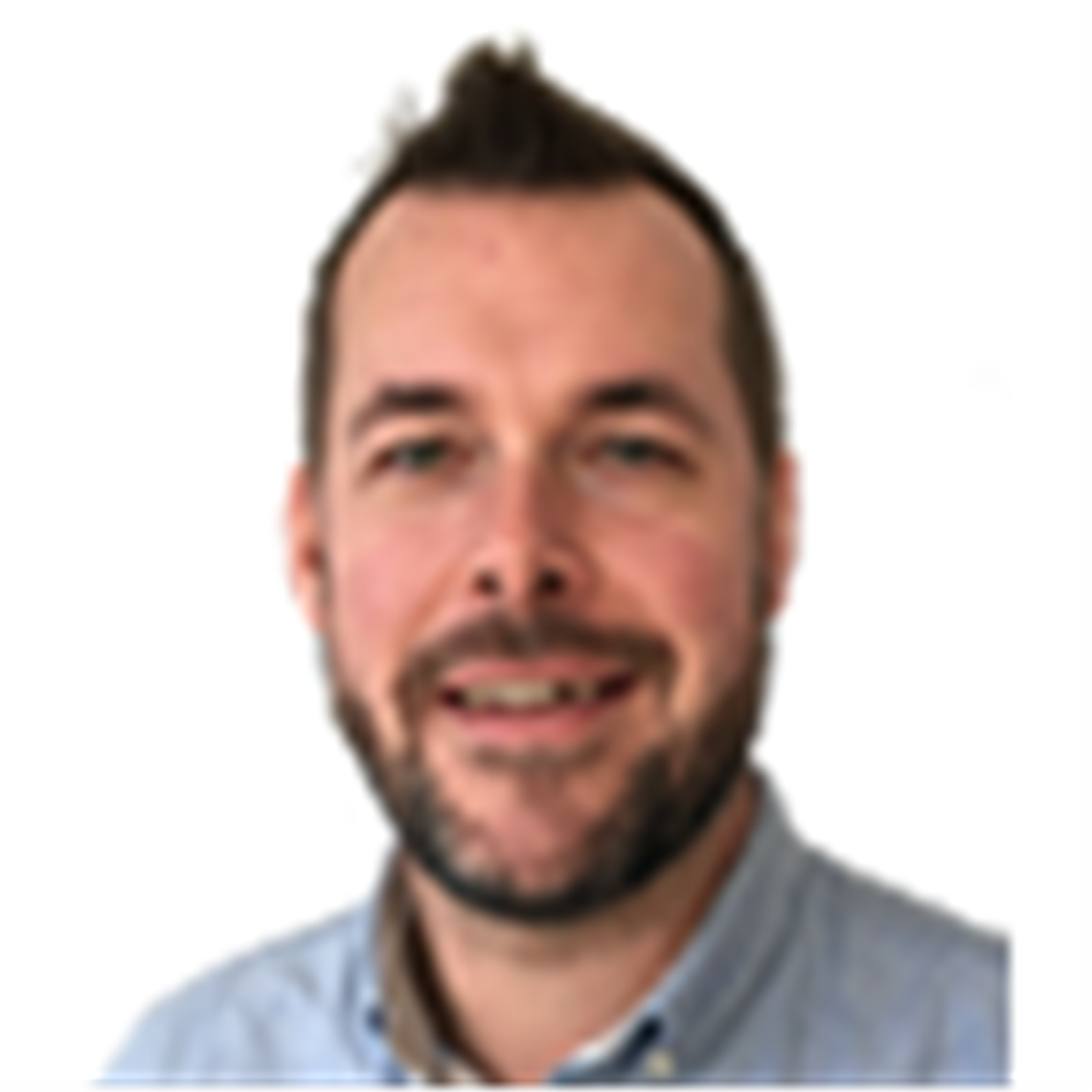
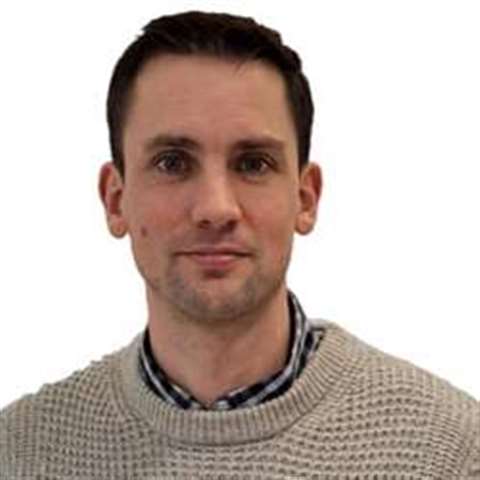
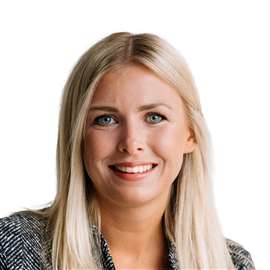