Read this article in French German Italian Portuguese Spanish
In ‘world first’ for size, ABB converts diesel truck to electric
12 June 2024
ABB, a multinational corporation and OEM that provides electrification and automation solutions for the construction and manufacturing industries, said it completed a retrofit of a haul truck from Türkiye-based Nuh Cement from diesel to fully-electric propulsion. The company believes it’s a ‘world-first’ for a truck this size and class.
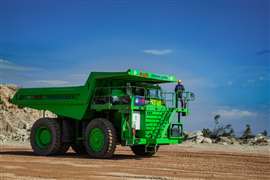
The vehicle was a Euclid R85B haul truck, which ABB said was transitioned into an zero-emission electric machine, with collaboration from employees at Nuh Cement.
The R85B stands taller than 16 ft (4.9m), is approximately 34-ft (10m) long, and nearly 18-ft (5.5m) wide. It weighs around 132,000 lbs (60 tonnes) empty, with a maximum loaded weight up to 315,300 lbs (143 tonnes).
“[It’s the] first time in the world that a vehicle of this size and class type has been fully electrified,” confirmed ABB.
ABB aided the project with system engineering and contributed a BORDLINE CC200 drivetrain platform, a traction-battery, and an air-cooled traction motor.
The company said it also provided “vehicle control electronics, a battery thermal management system, and a DC Fast charger.”
Flip to electric benefits Nuh Cement’s mineworks
ABB noted switching the truck from diesel to electric will cause immediate reductions in fuel costs and CO2 emissions.
“The retrofitting of this one truck will save approximately 100,000 litres (26,417 gallons) of diesel fuel and prevent 245 tons (222 tonnes) of CO2 emissions annually; equivalent to 58 gasoline-powered passenger vehicles driven for one year,” said ABB.
Group CEO of Nuh Cement, Gökhan Bozkurt, said, “This retrofitting conversion… leads the way towards a more sustainable future for the mining and cement industries and will significantly reduce our costs and impact on the environment.”
But cost-savings, sustainability, and reduced climate-impact weren’t the only benefits, as ABB noted the unique conditions and accessibility of Nuh’s cement mine also revealed advantages resulting from the electric switch.
“The cement mine, which is located in Kocaeli-Körfez, east of the Marmara region surrounding Istanbul, Türkiye, is positioned in such a way that the trucks travel downhill, fully loaded, on an average ramp gradient of between 18-20%,” explained ABB. “Regenerative braking enables the truck to recharge its battery as it descends, and once unloaded, ascend to the top of the mine using only previously regenerated electric power.”
Furthermore, the refurbished machine was nearing the natural end of its projected 30-year lifespan, and ABB said it anticipates the electrified version of the Euclid to operate for “many more years.”
“Rather than scrap and replace the original mining vehicle, which would involve disposing of several tons of material and purchasing a new vehicle at the cost of several million dollars, the project propelled greater returns on the initial investment made by Nuh Cement some 30 years ago,” said ABB.
STAY CONNECTED

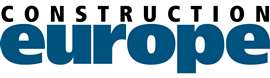
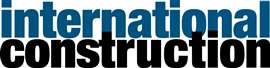
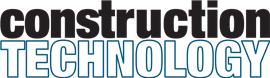
Receive the information you need when you need it through our world-leading magazines, newsletters and daily briefings.
CONNECT WITH THE TEAM
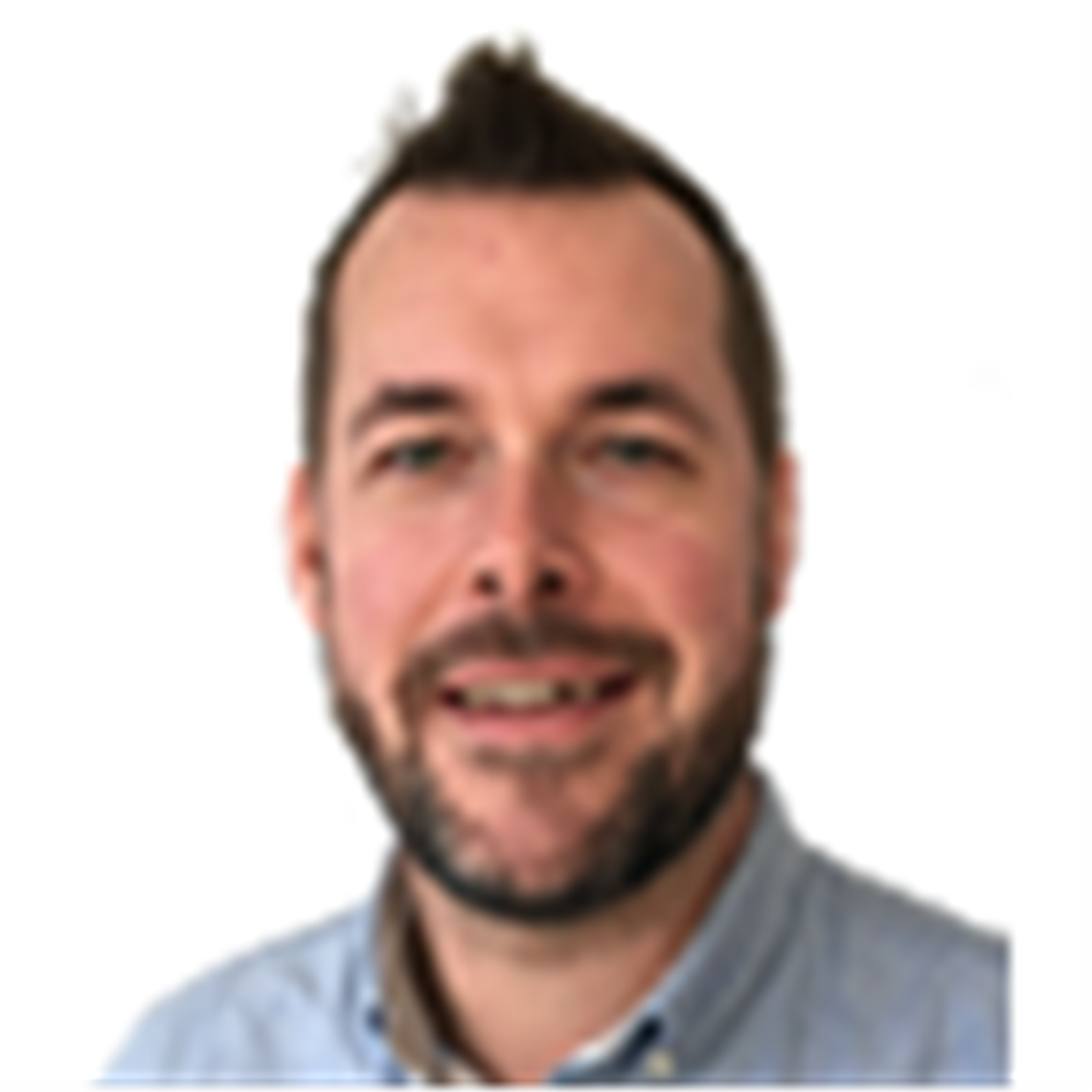
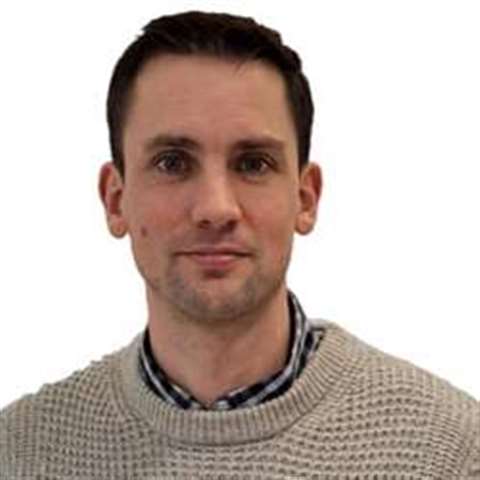
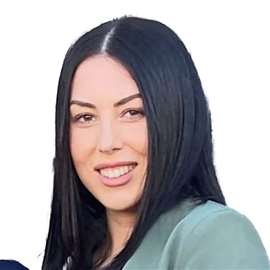
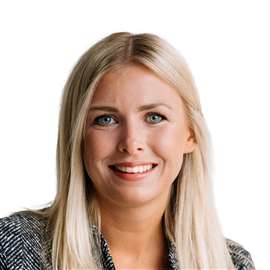