Read this article in French German Italian Portuguese Spanish
How is the high-rise industry advancing sustainability and tech?
08 January 2025
The high-rise industry is raising expectations in sustainability and tech advancements, Mitchell Keller reports.
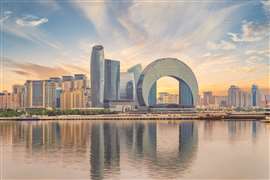
The world is getting taller. While an exact number won’t be known until later this year, it’s estimated about one dozen skyscrapers (at least 100m or higher) were delivered worldwide in 2024.
And 2025 looks set to continue this trend, with more cities planning and developing even more looming towers for city centres and urban expansion projects.
Contractors and engineers are turning to contemporary solutions in the lifting, foundation, and high-rise sectors, and suppliers have been delivering ‘first-time’ projects like never before. Whether increasing tower crane fleet sizes, finding innovative ideas for laying foundations or exploring alternative power, there’s a lot to see from atop the high-rise construction sector.
An eight-crane approach
Increasingly, megaprojects and major builds are leaning toward ‘the more the merrier’ approach to lifting. Instead of using just one or two heavy-lifting tower cranes on a given project, today’s bigger builds are filling the sky with ten or more machines at a time, when applicable.
In Milan, Italy, eight Potain cranes (a Manitowoc brand) are lifting to life the CityWave building, which is actually two buildings connected by a 140m-long, curved, wave-like roof. The exterior materials used include dowel-laminated timber for the roof, photovoltaic panels, and laminated glass, making precision in lifting vital.
“The building’s defining feature will be its unique roof, which will stand at 53m in height once complete and will be covered with photovoltaic panels to create Milan’s largest solar power installation,” says Manitowoc.
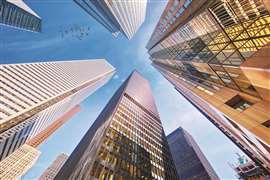
The east end of the building will reach around 50m in height, and the west end will reach 21 storeys and 105m. It will hold 63,000m2 of office and retail space. The site is within Milan’s CityLife mixed-use district near the city’s old centre. The entire CityLife development is expected to cost US$2.2 billion and finish next year. Already constructed at CityLife are recognisable high-rises like Allianz Tower (Il Dritto) and Generali Tower (Lo Storto).
An Italy-based joint venture of CMB and Colombo Costruzioni are leading the scheme for CityWave.
“The two companies are long-time users of Potain tower cranes and worked with Manitowoc’s Lift Solutions team to select a perfect mix of eight cranes for the building’s unique shape,” says Manitowoc.
The contractors are using a mixed fleet of Potains, including a new MDT 319 topless and an MDT 21. The two new units were joined by six other Potain cranes in the combined fleet.
Manitowoc says two MDT 219 cranes are anchored to the buildings as they climb. They are working with full jib lengths of 60m, and one of the units will eventually reach a working height of more than 120m. The second will reach a final working height of more than 80m, as will the MDT 319, which is working with a 50m jib.
The cranes feature Manitowoc’s Crane Control System, which includes an interface with graphic displays, jog dial, data input, and ergonomic controls, which Manitowoc says aids navigation, precision and efficiency.
Enzo Macis, jobsite director at CMB, says, “When we looked at crane planning, we weren’t focused as much on lifting capacity as we were on reliability and productivity.
“It became a question of selecting the right models that would work together as the project changed shape while construction advanced.”
The cranes will remain on site until the end of construction, helping dismantle equipment before CityWave opens prior to the 2026 Winter Olympic Games.
Foundational projects
The foundation segments – including formwork, falsework and shoring – have had plenty to boast about, too, with innovative strategies and materials setting a solid base for higher heights.
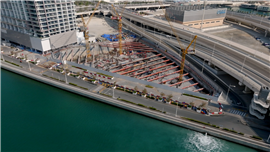
Or, perhaps new depths, as was the case with Altrad RMD Kwikform (Altrad), a UK-based provider of formwork, falsework/shoring, heavy-duty support, ground shoring and safety and access systems. Altrad says it supplied shoring solutions on “one of the largest excavations in the company’s history” in Abu Dhabi, United Arab Emirates (UAE).
The scheme is for a new city centre mixed-used development in the UAE’s capital city, which will integrate commercial and residential spaces. At the core of the project is a large basement excavation (measuring about 14m deep and 70m wide with an approximate volume of 111,000m3) in a dense urban setting surrounded by waterfront.
Altrad says it “was tasked with delivering a system that could handle the extensive loads and provide robust support throughout the excavation process.
“The proximity to the water required careful planning to prevent contamination as well as mitigating risks associated with flooding and erosion.”
Altrad says it used 387 tonnes of its S460 high-grade steel Tubeshor material. The props had a maximum span of 67m and prop spacing of 7.5m, which was supported by a single plunge column along the length.
“The Tubeshor system’s strength and modular design made it the ideal solution for the project’s complex requirements,” says Altrad, adding the solution also “enabled a value-engineered strutting design, which brought significant benefits to the project… with the maximum load acting on the prop of 3,295kN.”
Altrad says the strategy led to a 30% reduction in the amount of steel needed, which lowered costs and maximised the available excavation space. Bolted connections also improved the ease of use and reduced installation and dismantling time, the firm says.
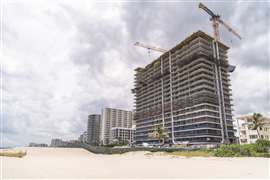
Flexibility was also touted, with Altrad saying it was able to deliver fewer plunge columns than originally designed, leading to a more streamlined process. “The ability to easily adjust and reconfigure the props on-site meant that the system could be tailored to meet the specific needs of the excavation as it progressed,” Altrad says.
“The original customer design had featured 28 plunge columns, but the team were able to reduce this to ten.”
In Florida, US, Austria-based Doka is providing shoring, reshoring, and formwork solutions for an upcoming 21-storey oceanfront residential high rise in Pompano Beach.
Named Casamar, the building is under development by Related Group with Coastal Construction serving as general contractor and Coast to Coast Forms as concrete contractor. Related Group received a nearly $160 million loan to begin construction in 2023.
“The structure utilises state-of-the-art formwork systems, including Doka’s Frami Xlife for the core, Eurex 30 Props for reshoring, and Truss Tables for shoring, ensuring strength, flexibility, and efficiency throughout the construction process,” says Doka.
The firm says its Frami Xlife lightweight formwork system’s quick install and dismantling capabilities are helping optimise the project schedule, allowing delivery trucks direct access to the site by eliminating the need for extensive laydown spaces.
“The innovative use of truss tables, starting as low as the third floor, significantly reduced crane picks, improving site efficiency and helping the project stay on schedule. The integration of Doka’s durable plywood further supported the successful execution of the formwork plan,” adds Doka.
The luxury tower topped off at nearly 70m in height in July and the project delivery is slated for early 2025.
STAY CONNECTED

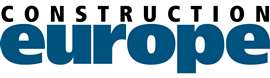
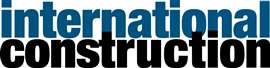
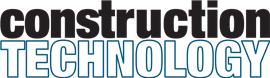
Receive the information you need when you need it through our world-leading magazines, newsletters and daily briefings.
CONNECT WITH THE TEAM
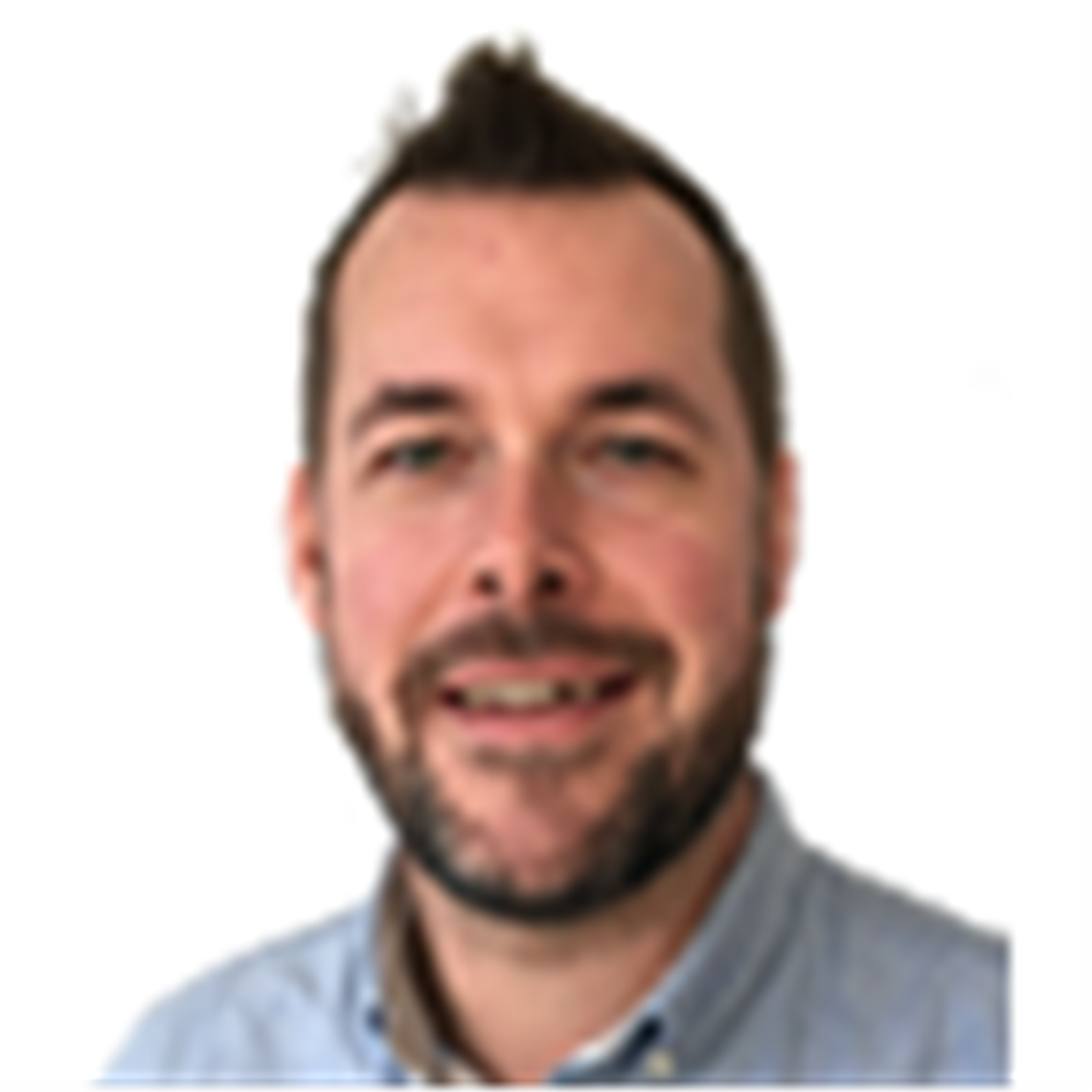
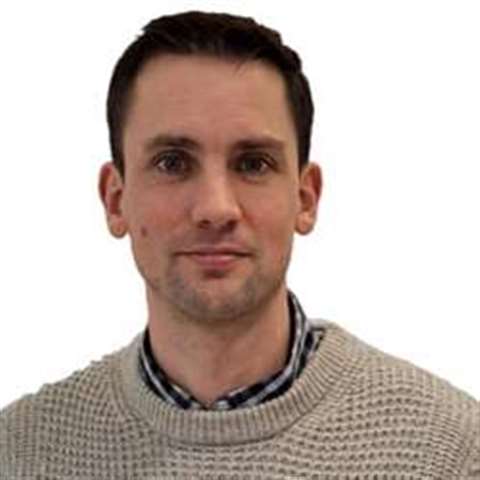
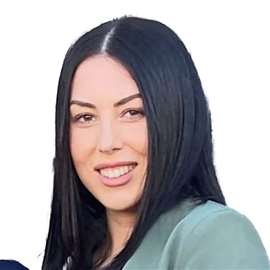
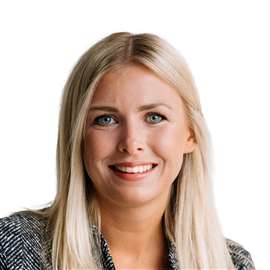