Why contractors fear ‘Buy America’ policy could push up US construction prices
27 June 2023
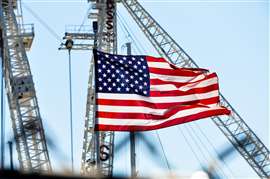
A body representing contractors in the United States (US) has warned that incoming regulations on the provenance of construction products and materials could lead to further price rises in the sector.
Provisions in the Build America, Buy America Act (BABAA) enacted as part of the Infrastructure Investment and Jobs Act in 2021, focus on maximizing the government’s use of services, products and materials from the US.
BABAA requires all iron, steel, manufactured products and construction materials permanently installed on federally assisted infrastructure projects to be produced in the US.
Heads of federal agencies can make exceptions to the rules by posting a proposed waiver online for 15 days to allow the public to review and submit comments.
The law is currently in effect but from a functional and legal standpoint, the regulations have yet to be finalized.
Major federal agencies like the US Department of Transportation (US DOT) are still deciding on the way the rules will work.
A spokesperson for the Associated General Contractors of America (AGC) told International Construction, “As we understand it, most states are still accepting bids that have a note at the bottom that says contractors cannot guarantee these projects comply with anticipated Buy America rules.”
Contractors’ concerns
But contractors fear that when the rules do finally come into effect, they could push prices up, at a time when they are only just starting to recover after a period of inflation and supply chain turmoil.
Association officials said that new Buy America requirements will “severely limit” the supply of materials contractors can use and increase the costs of those products when the guidance goes into effect.
They noted that the new requirements are “so strict” that many products currently made in the US will not comply because some of the materials used to make those products come from overseas.
“There is a real possibility that they will require 100% of products to be manufactured and sourced in the US,” an AGC spokesperson warned.
That could mean, for example, that every screw used on a construction project will not only have to have been molded in the US but the metal for it will also have to have been produced domestically.
The spokesperson said: “A good example is of a contractor building a rest stop in Florida that includes a generator. The generator is made in the US but several of the small parts on the generator are not made in the US – so that would not qualify.”
They claimed there were also signs that US DOT will require all aggregates and cement in concrete to come from US, which would restrict the supply of concrete, with a significant quantity of it coming from other countries like Mexico.
International Construction contacted US DOT for comment and it directed us to a FAQ section on its website about BABAA.
“Federal officials are attempting to wish away a diversified global supply chain for construction materials by regulatory fiat,” said Stephen E. Sandherr, the association’s chief executive officer.
“All of us want more domestic manufacturing, but the reality is that it will take years – if ever – before the products those factories make will be entirely sourced within the U.S., as the administration is seeking to mandate.”
STAY CONNECTED

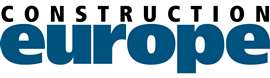
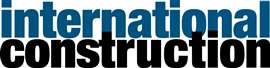
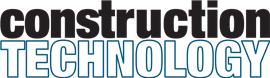
Receive the information you need when you need it through our world-leading magazines, newsletters and daily briefings.
CONNECT WITH THE TEAM
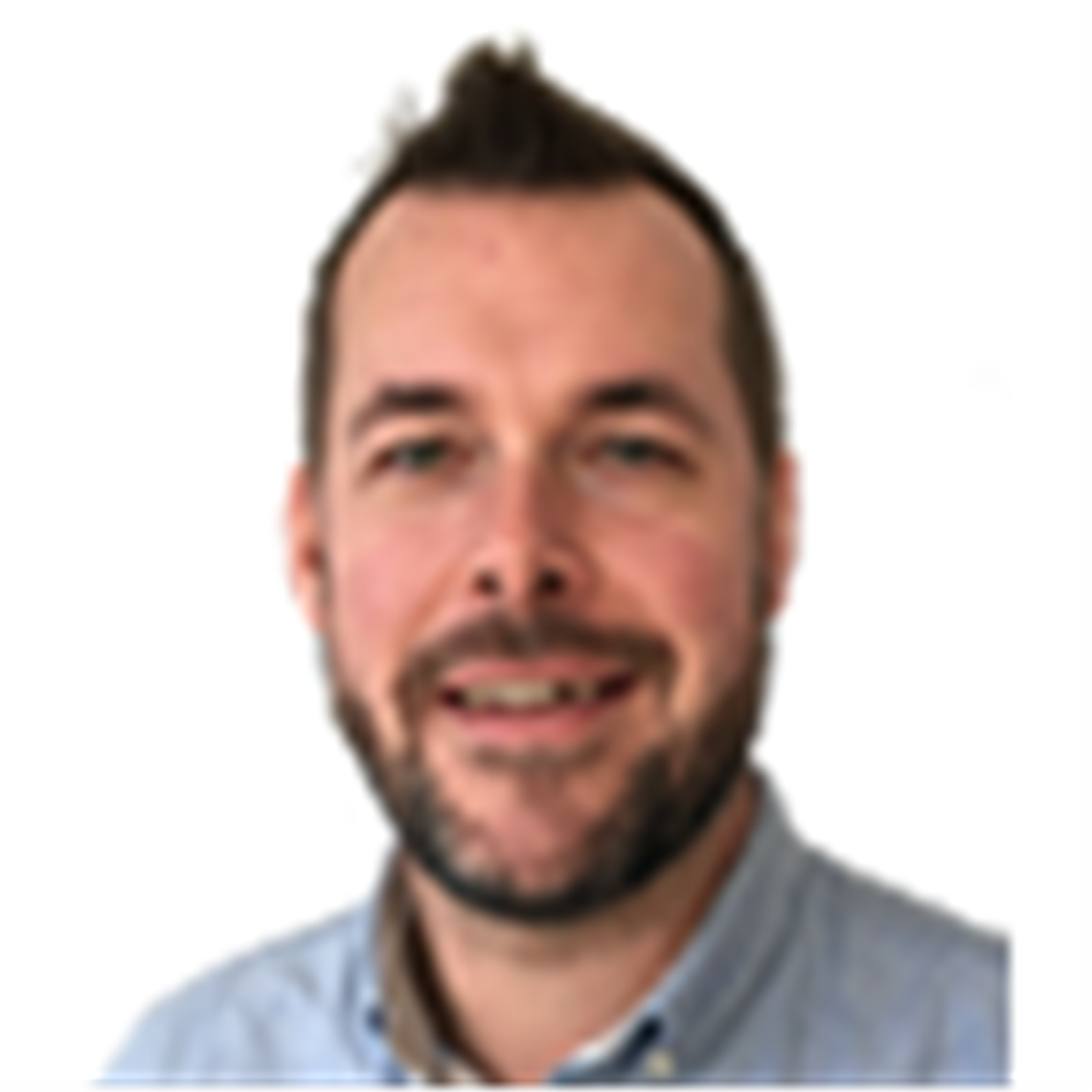
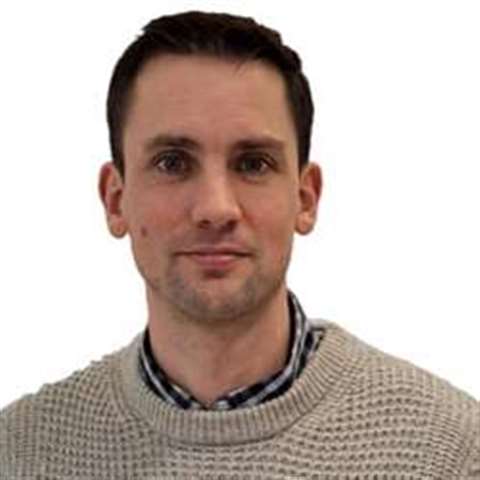
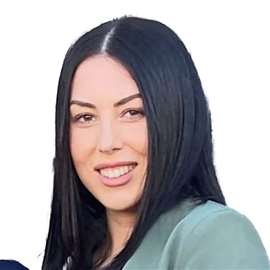
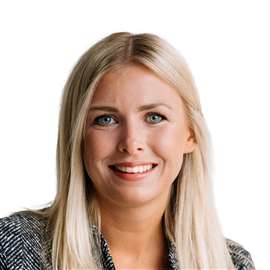