Read this article in French German Italian Portuguese Spanish
What US Army engineers found when they repaired corroded steel with fibre polymers
30 September 2024

Steel corrosion in infrastructure is a multi-trillion-dollar problem.
In fact, the National Association of Corrosion Engineers in the US estimated the total global annual cost of corrosion to be US$2.5 trillion - and that was back in 2013. The cost now is likely to be significantly higher.
But the same association estimated that the cost of steel corrosion could be reduced by 35% if proper controls are introduced.
That’s where a new study by the US Army Engineer Research and Development Centre (ERDC) comes in.
The study picks up on previous work to explore the potential of applying carbon fibre (CFRP) and basalt fibre (BFRP) reinforced polymers to repair corroded steel cross sections.
It conducted a series of full-scale experimental tests on steel beams to see how CFRP and BFRP affected their structural characteristics, including their ductility (a metal’s amenability to being drawn or stretched without breaking).
The stakes
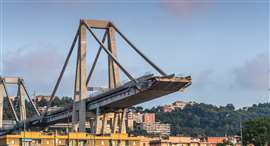
The stakes are high when it comes to the corrosion of steel in infrastructure – and it’s a particular problem for structures that are in or near water, whether that is bridges, flood control structures, pipelines to buildings, and other underwater marine structures.
Aside from the cost of inspecting and repairing structural components (which in some cases can include dewatering them), there is the potential service disruption.
And failure to keep on top of the silent threat of the corrosion can lead to structure deterioration, still costlier repairs and, as the report highlights, even failure of the structure.
It pointed to the high-profile example of the Morandi Bridge collapse in Genoa, Italy, which resulted in the deaths of 43 people. The 51-year-old, three-span viaduct was part of the A10 motorway leading to Savona and was designed as a continuous beam, supported by three diagonal cable-stayed systems. Italian engineering experts believe that the gradual corrosion of the steel cables played a pivotal role in the bridge’s collapse, diminishing its structural integrity by 20%.
Repairs to steel corrosion
The ERDC study noted that there are several existing approaches to repairing and retrofitting corroded steel in structures. They can be as simple as removing corrosion and repainting the steel.
But when it comes to more severe corrosion, each method of retrofitting brings its own disadvantages. That is the case whether it involves replacing corroded steel elements with new cross sections (which can cause service disruption), or attaching extra steel plates (which increases the dead load of the structure and potentially disrupts service).
More recently, applying CFRP to wrap corroded steel cross sections has become more popular but it requires an insulation material such as glass fibres to prevent galvanic corrosion between the carbon fibre and steel.
And while FRP materials have been investigated by several studies in recent years, which have suggested they can increase the load carrying capacity and yield capacity of beams as compared to unrepaired ones, the ERDC suggested that more experimental tests were needed to assess the full structural behaviour of repaired beams and the impact of the debonding of fibre polymer wraps on beam performance.
The tests
The study set out to ascertain the effectiveness of fibre-reinforced polymers to repair corroded steel beams that are subjected to bending and shear stress.
To do so, researchers installed seven different steel W x 24 beams with a span length of three metres in a test frame that was then put under four-point bending and loading conditions using a 489KN actuator.
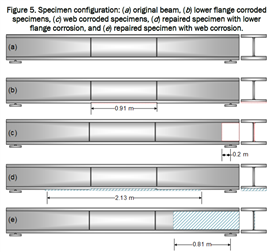
The first of the beams was a control specimen where there was no corrosion or repair (see a. in the above diagram). The next was a beam where the lower flange mechanical section had been reduced by 20%, effectively by having a section of the steel cut out, to simulate the effects of corrosion (b).
The third beam was similar in that it had a 20% reduction at its web (c).
Then there were two beams where the sections at the tension flange and web respectively had been reduced by 20% and then repaired with CFRP patches featuring unidirectional carbon fibres (see d. and e.). And the final two beams had had their tension flange and web reduced by 20% respectively and were then repaired by BFRP patches with quad-directional fibres (see d. and e.).
All the patches were installed onto a surface roughened by an angle grinder, using an epoxy called Tyfo S, mixed with silica fume.
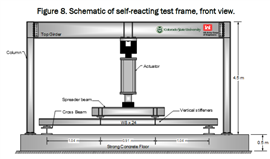
The results
The ERDC researchers found that their attempts to simulate corrosion by cutting out parts of the beams at the bottom flange and web elements reduced the strength and ductility of the steel.
Adding CFRP patches to the ‘corroded’ beams helped to increase their ultimate capacity by 7%, both when the repair was added to the bottom flange and the web element. But it had a negative impact on ductility and the patches started to de-bond early, the study found.
The results were better for BFRP patches. There was a 10% improvement in ultimate strength for the beam where a patch was applied to the bottom flange and de-bonding was minimal. The BFRP patch on the web element of the beam increased ultimate capacity by 5%, ductility improved, and there was no de-bonding.
In its conclusion, the study said, “The BFRP outperformed the CFRP patches in enhancing the structural behaviour of the tested beams, and its debonding, if it exists, is expected to occur after the beams reach their ultimate capacity. BFRP caused a minimal change in the strain distribution in the repaired beams, which is critical to maintaining the same structural conditions and performance of the undamaged structural members.”
Recommendations
Given the debonding of the CFRP patches, the researchers recommended further studied that examined different types of adhesives for fibre-reinforced polymers (because the debonding failures happened in the adhesive surface without any fractures in the patches).
They also noted that the quad-directional BFRP patches showed “promising performance” in areas subjected to higher shear forces and recommended testing bi-directional CFRP patches.
Future investigations could also study the performance of corroded cross sections that are completely wrapped in FRP patches, which is an approach often applied in the repair of navigation steel structures, the researchers said.
And another recommendation was to investigate the durability of applied repair approaches to understand the lifespan of FRP materials as a long-term approach for steel hydraulic structures.
To access the full report, click here.
STAY CONNECTED

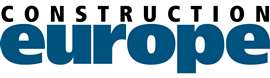
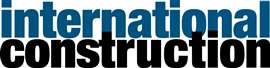
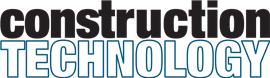
Receive the information you need when you need it through our world-leading magazines, newsletters and daily briefings.
CONNECT WITH THE TEAM
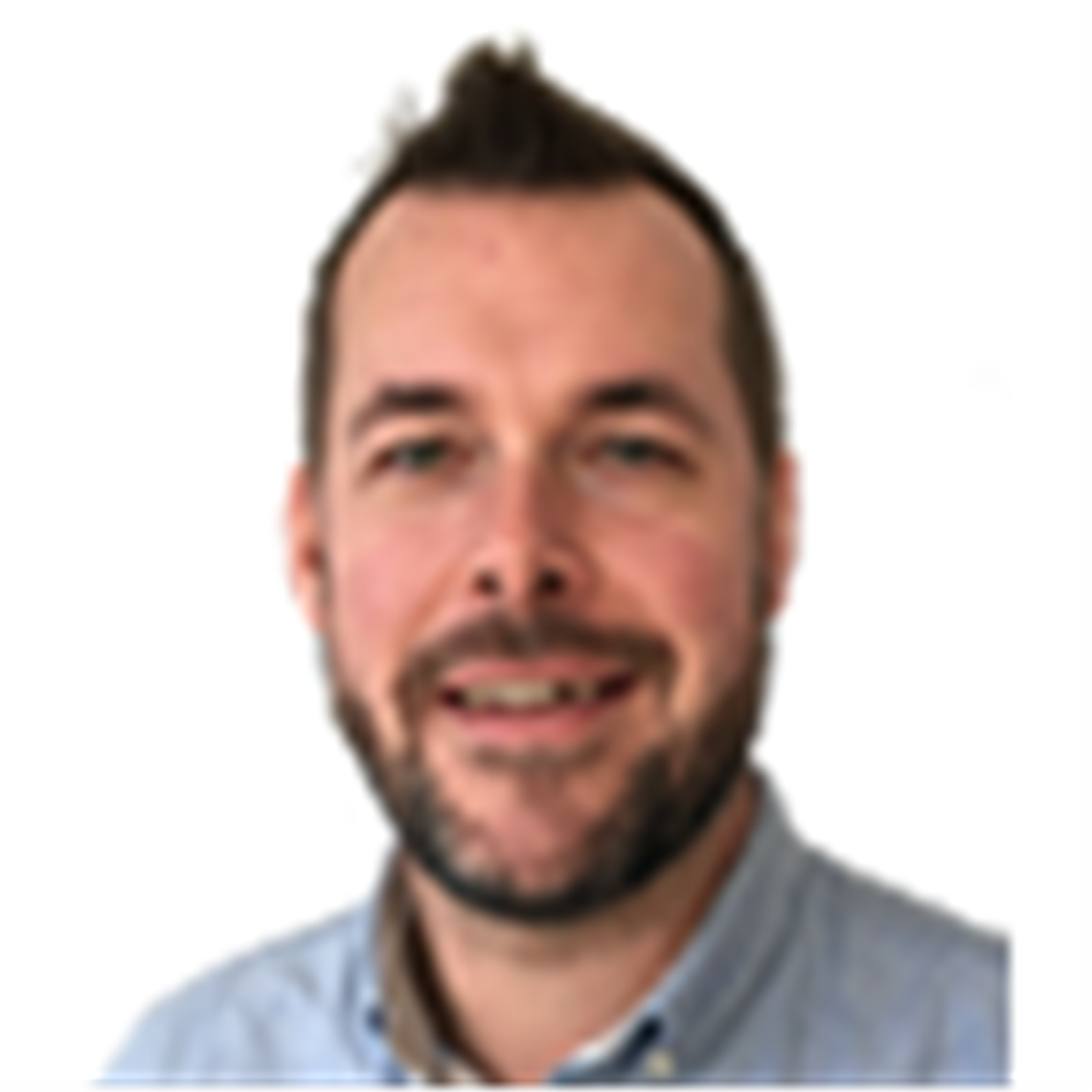
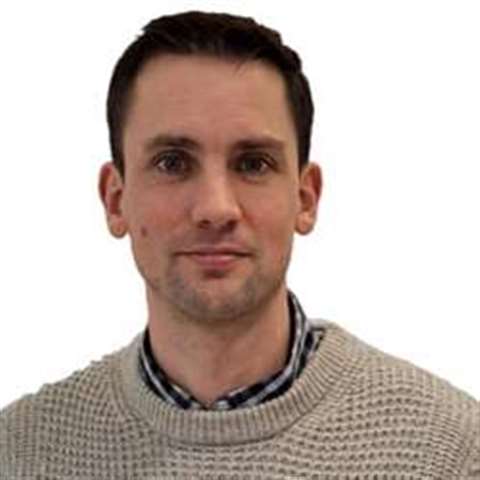
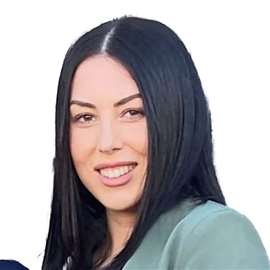
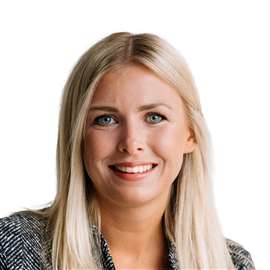