US construction: How new laws and investment needs impact the sector
29 September 2023
Construction in the US has performed strongly in recent years, with government support and growing sectors such as infrastructure and sustainability-related spending providing impetus, reports Andy Brown.
The US was one of the best performing markets last year, with construction equipment sales at a record-high and, while it is anticipated that sales will drop in 2023, it will still be one of the best ever years for sales in the US. It is also worth noting that, although equipment volumes might drop, construction in the region is pivoting towards infrastructure, which will drive sales of heavier (higher value) equipment. This means that, while the overall number of machines sold might drop, revenues in the segment will rise.
Government acts
The sector has benefited hugely from government acts, such as the Infrastructure Investment and Jobs Act (IIJA), Inflation Reduction Act (IRA), and CHIPS Act. According to the US Department of the Treasury’s Office of Economic Policy, since the end of 2021 real manufacturing construction spending has doubled. The Biden Administration is pursuing an economic approach based on “modern supply side economics” which seeks to expand the productive capacity of the economy by investing in things like infrastructure, high-tech manufacturing, and workers.
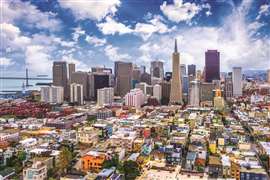
The report from the Treasury noted that, “While it can be difficult to compare such granular data across countries, the surge appears to be uniquely American – not mirrored in other advanced economies.”
Demand is certainly high, but a factor that has consistently hampered the industry is a lack of workers, something that was once more reiterated in an analysis of government statistics from the Associated General Contractors of America (AGC).
Construction employment increased in 226 of 358 metro areas between July 2022 and July 2023, according to analysis by the AGC of new government employment data.
Association officials said demand for many types of construction remained strong in most parts of the country, but firms still have hundreds of thousands of unfilled construction positions.
“Demand for construction projects remains strong nationwide and most metros have continued to add construction jobs in the past year,” said Ken Simonson, the association’s chief economist.
“But there were 378,000 unfilled job openings in construction at the end of July, which suggests that even more markets would have posted year-over-year employment increases if there were enough qualified workers to fill the openings.”
Dallas-Plano-Irving, Texas, added the most construction jobs (12%), followed by New York City (9%). Construction jobs declined over the year in 80 metro areas and were unchanged in 52 areas. The largest job loss occurred in Miami-Miami Beach-Kendall, Florida (-8%), followed by Nassau County-Suffolk County, New York (-3%).
Investment needed in infrastructure
Despite increased government investment, upgrading the US’s ageing infrastructure requires even greater funding.
One in three bridges in the US need to be repaired or replaced, according to American Road & Transportation Builders Association’s (ARTBA) analysis of the recently released US Department of Transportation 2023 National Bridge Inventory (NBI) database.
The total number of bridges that need major repair work or should be replaced is more than 222,000, which is approximately 36% of all bridges in the US.
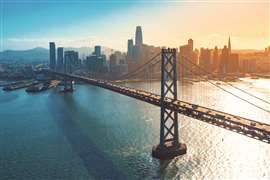
Of the bridges needing repair, nearly 42,400 are rated in poor condition and classified as “structurally deficient.” Motorists cross these structures 167 million times a day.
The number of bridges in poor condition declined by 560 compared to 2022. At the current pace, it would take nearly 75 years to repair them all.
ARTBA chief economist, Alison Premo Black, who conducted the analysis, estimates it would cost more than US$319 billion to make all needed repairs.
States currently have access to US$10.6 billion from the 2021 federal Infrastructure Investment and Jobs Act’s (IIJA) bridge formula funds that could help make needed repairs, with another US$15.9 billion to be available in the next three years.
As the end of FY (full year) 2023 approaches on September 30, states have committed US$3.2 billion (around 30%) of available bridge formula funds to 2,060 different bridge projects, with US$7.4 billion still coming.
Over the last five years, the share of bridges in ‘fair’ condition has continued to grow as the share of structures classified in ‘poor’ or ‘good’ condition declined. In 2023, nearly half of all bridges in the US (48.9%) were in fair condition.
Bridges are classified in good, fair, or poor condition based on their inspection ratings and definitions from US Department of Transportation.
Reducing emissions
Meanwhile, the construction industry continues to find itself at the forefront of efforts to cut carbon emissions.
The state of California in the US has changed its building code to limit the amount of embodied carbon emissions allowed in commercial and school buildings.
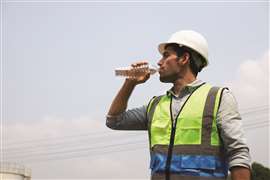
The California Building Standards Commission (CBSC) voted the changes to two building codes into effect, making it the first State in the US to implement required embodied carbon reduction in some buildings.
The new code will “limit embodied carbon emissions in the construction, remodel, or adaptive reuse of commercial buildings larger than 100,000 square feet (9,230 square metre) and school projects over 50,000 square feet (4,650 square metre),” according to The American Institute of Architects (AIA) California, which worked closely with policy-makers on the changes.
The new changes will come into effect July 1, 2024. The change is an amendment to the 2022 California Green Building Standards Code (CALGreen), California’s first statewide green building code, which was first developed to supplement the general code in 2007.
Embodied carbon encapsulates the carbon emissions generated from the entire lifespan of a building, including manufacturing, construction, maintenance and eventual demolition.
“This action is a real catalyst for change that will push the industry forward in rapidly addressing the growing climate emergency,” said William Leddy, AIA California Vice President of Climate Action.
In the state of California – the world’s fifth largest economy – construction activity is credited with about 40% of the state’s greenhouse gas pollution. By reducing embodied carbon, California aims to mitigate its contribution to climate change and promote sustainable building practices.
The compliance options include reusing at least 45% of an existing structure, using materials that meet specific emission limits, and using a performance-based approach that involves analysing the entire lifecycle of a building.
“The most sustainable buildings are the ones that are already built. Prioritising the reuse of existing buildings not only accelerates the reduction of embodied carbon emissions from new construction, it ‘incentivises’ the industry to address California’s severe housing crisis more quickly and efficiently, creating more sustainable and resilient communities,” added Leddy.
With temperatures rising globally, working conditions may become more extreme for construction workers in the future. The industry will therefore be looking on with interest at the news that a judge in Texas, US, ruled a new law that would effectively ban water breaks for construction workers by eroding cities’ power to enact local rules as unconstitutional.
Controversial planned law
The state law, signed by Governor Greg Abbott earlier this summer, aims to stop cities and counties from putting their own local ordinances in place. It would affect mandatory water breaks that have been implemented in certain cities like Austin and Dallas.
The planned law, which was due to come into force on 1 September, has proved controversial during a summer of record-breaking heat. The City of Houston filed a suit against the state in relation to the law earlier this summer.
State District Judge Maya Guerra Gamble ruled that the law unconstitutional at the end of August. The law, which its supporters say will cut down on the variation of rules across the state, is still expected to go into effect.
But the new ruling gives cities ammunition to counter any lawsuit against their local ordinances challenged under the new state law. The state of Texas has appealed the ruling.
The US economy is predicted to see real Gross Domestic Product (GDP) growth for 2023 from 1.8%-2.2%, and for 2024 from 1.2%-1.4%. Longer term predictions are more positive, with Oxford Economics estimating that the construction sector will see a period of more sustainable growth, with the company forecasting that US construction work done will grow by almost 30% over the next 15 years to reach over US$1.8 trillion by 2037 – up by almost US$400 billion. Even if this prediction is on the optimistic side of the scale, construction in the US is certainly looking in robust health.
What is Build America, Buy America?
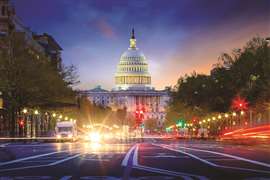
The Build America, Buy America Act was part of the US$1.2 trillion 2021 Infrastructure Investment and Jobs Act. It stated that all Federal projects using money from the Act had to ensure that a proportion of the materials used in the projects were bought from America.
The Act covers five construction materials categories: non-ferrous metals, plastics and polymer-based products, glass, lumber and drywall. Some waivers to the rules are being considered, according to the US Department of Transportation.
Any item incorporated into a project will fall under one of four categories for compliance. These are iron, steel, construction materials, and manufactured products. Specific domestic manufacturing processes are delineated for all eight categories of construction materials that are included.
To qualify, the manufactured products must be US manufactured and the cost of domestic-made components must exceed 55% of the cost of all components. Per a rule issued by the Biden administration in March 2022, the percentage will increase to 60% in October, 65% in 2024 and 75% in 2029.
The cost of components for manufactured products is defined as acquisition cost and transportation costs for components purchased by the manufacturer, and all costs associated with the manufacture of any components created by the manufacturer.
STAY CONNECTED

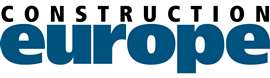
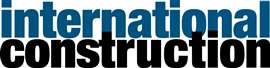
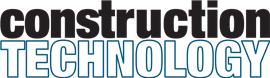
Receive the information you need when you need it through our world-leading magazines, newsletters and daily briefings.
CONNECT WITH THE TEAM
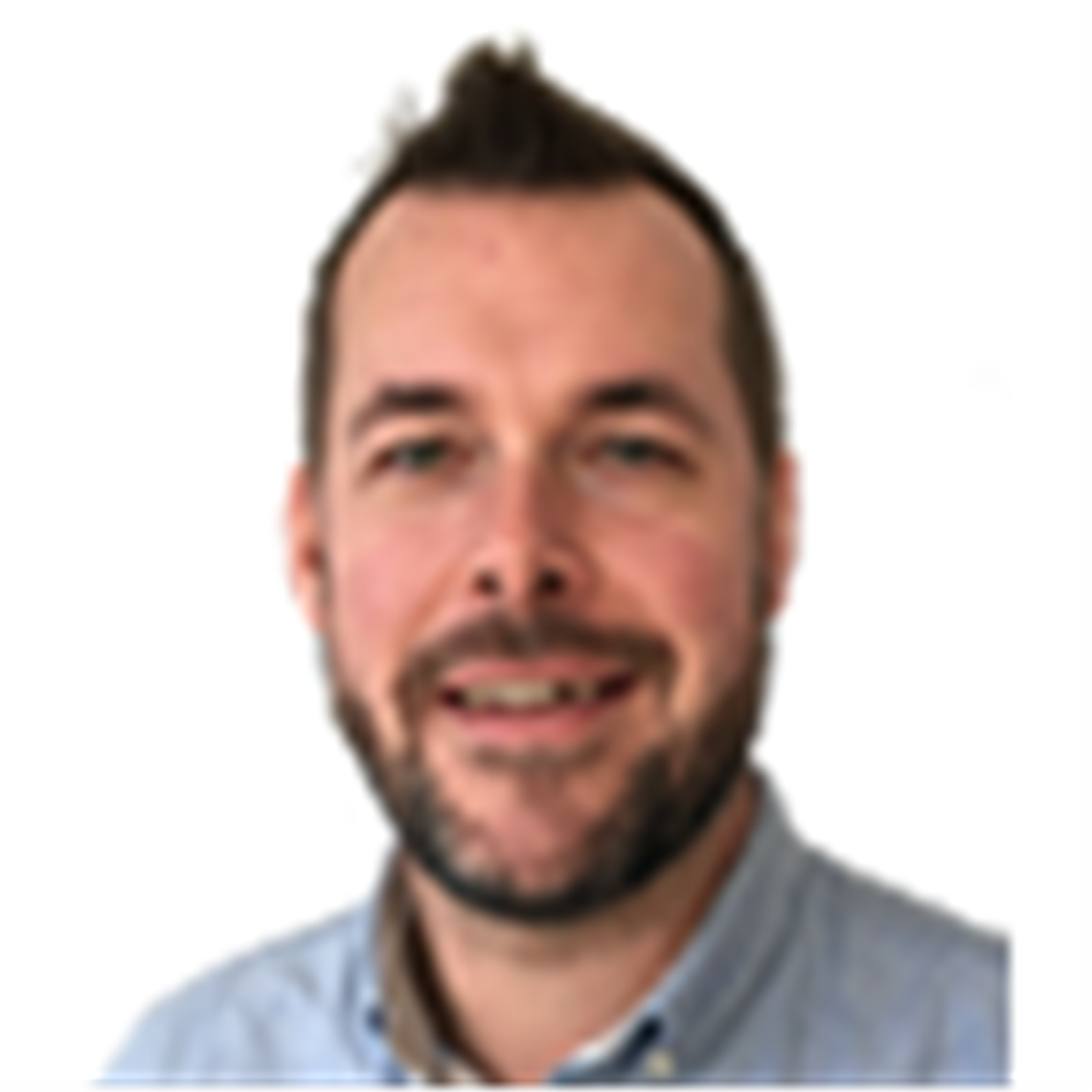
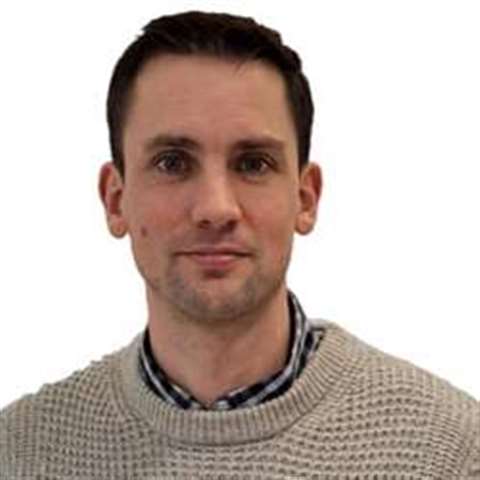
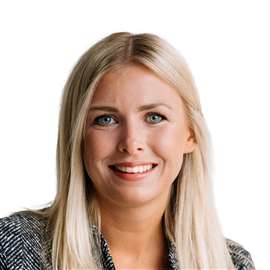