Read this article in French German Italian Portuguese Spanish
Three unusual new technologies for bridge inspections and maintenance
15 July 2025
The scale of the challenge to inspect, maintain, rehabilitate, and occasionally rebuild bridges is vast and growing.
In the US, nearly half of all bridges are at least 50 years old and 7.5% are considered structurally deficient, according to consultant WSP.
In Europe, around 10% of the region’s two million bridges are estimated to be in potentially dangerous condition, according to Christian Tridon, founder of the Eurobridge Conference.
And in Japan, 30% of bridges have already reached their design life of 50 years, while in 15 years from now, about 80% of them could be obsolete, according to one estimate.
Recent high-profile bridge collapses, notably the 2018 Morandi bridge collapse in Italy that killed 43 people, and last year’s collapse of the Carola Bridge in Dresden, Germany, highlight the need for faster and more efficient inspection and maintenance.
And new technologies are being developed for the construction industry to meet the challenge by making the inspection process faster and more efficient, as well as providing inspection capabilities in hard-to-reach areas of structures.
In today’s Construction Briefing, we highlight three unusual innovations from all over the world that have been developed for the purpose:
1) The unusual suction-cup drone that can inspect inaccessible structures
Drones for surveying and mapping, progress monitoring, and even inspection and quality assurance, have become a relatively common sight in construction over the past few years.
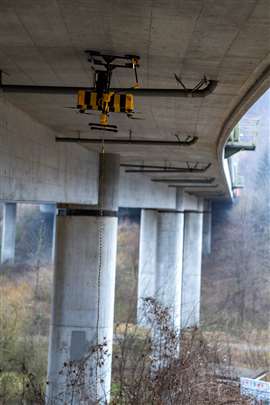
But imagine a drone that doesn’t just fly over or past built structures, but can attach itself to perform more detailed inspections, and even core sampling and drilling.
That is what a team of technology and engineering specialists at ETH Zürich university in Switzerland have done, creating a new company called Aithon Robotics.
Aithon Robotics has developed a new type of drone that uses high-airflow suction pumps and is able to latch onto difficult-to-reach areas of structures.
Core sampling or drilling work is one of three main types of task that the drone can perform. It can also undertake area scans using ground-penetrating radar that allows it to detect and mark rebar within structures, as well as placing objects like sensors.
“What we are looking at is a more efficient, safer, and cheaper access solution to infrastructure assets such as bridges,” said Friederike Biffar, a pioneer fellow at the company, who is responsible for software and controls.
“We can use it to fly to built assets and once we are there, we can attach to the structure via high-airflow suction pumps.”
The start-up claims that the drone can attach reliably to man-made surfaces and has been tested and deployed on concrete with varying degrees of deterioration, including cracks, dirt, and wet surfaces.
“Once we attach, we can turn off the rotors and we are super stable at the wall. And then we rotate the UAV body towards the work surface to do those three different types of work,” Biffar said.
The drone is operated by a human pilot via remote control and is tethered, which means that its flight time is not limited to the life of a battery.
The company hopes that the robot will prove useful and more cost-effective for structural health monitoring, as well as for small maintenance tasks.
“We have a lot of bridges built in the 1960s and 1970s [in Europe] and they are now reaching the end of their lifecycle. So now it is maybe an assessment of which bridge gets dealt with first and being able to decide that. I hope in the future, we don’t wait 40 years until the bridge collapses,” Biffar said.
As a project at ETH Zürich, Aithon Robotics, led by CEO Roman Dautzenberg, is currently involved in pilot projects, as it attempts to find traction, and ultimately paying customers, for its innovation.
2) AI inspection technology
Asia Pacific-based consulting engineer Beca is refining the use of artificial intelligence (AI) in bridge inspections. In 2023, it trialled AI-enabled drones on the 100-year-old Purewa Bridge in Auckland, New Zealand, which carries more than 20,000 vehicles a day.
Beca’s transport and infrastructure team used drones equipped with Niricson technology to capture 15,000 high-resolution images and acoustic soundings from multiple angles. AI software then analysed the data, identifying and quantifying defects such as cracks, spalls and honeycombing, including very small faults.
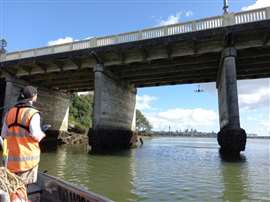
Following the trial, Beca applied the approach to the 528m-long Waipuna Bridge in Auckland in 2024. Kevin Williams, associate – bridge structures, mobility & precincts at Beca, explained how the 51-year-old, 528m-long bridge consists of precast concrete balanced cantilever segmental box girders in spans two to eight, and twin pre-stressed double-T girders for the end spans. Spans four and six have halving joints with horizontal bearings and vertical ties.
A Skydio 2+ autonomous drone captured a full photogrammetric model, allowing AI mapping of cracks in critical areas. The processed data helped Beca programme further investigations on the complex structure.
Beca has since moved on to the 114-year-old Grafton Bridge in Auckland, which can only be inspected at night because it spans over four sections of the SH1/SH16 motorway.
That requires a drone that can operate in darkness and has seen Beca upgrade to Skydio X10 drone with enhanced capabilities and an enhanced camera. Beca claims to be the first company in New Zealand to own such a drone.
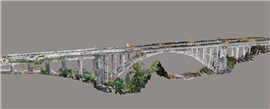
Williams explained that this time, Beca wanted to produce a full reality mesh/photogrammetric model of the bridge. “From this we would use a digital providers smart platform to perform the inspection condition reporting of all significant defects and use this to perform maintenance planning and workflow using trend and condition monitoring in a workspace environment model for this significant heritage bridge asset,” he said.
The firm says the AI-based approach is safer, faster, more accurate and less disruptive than traditional methods, allowing full digital condition assessments and 3D modelling to be delivered in shorter timeframes.
3) Lasers to remove rust from structural steel
Japanese company Toyokoh has established a business called CoolLaser that uses powerful beams of light to strip rust from structural steel.
The company, founded in 2008, has developed a handheld device with a maximum power output of 5.4kW, making it powerful enough to remove rust from steel in outdoor environments.
The entire system has been designed to fit into a standard car and while it has multiple potential applications within the construction industry, one of the main areas of focus for CoolLaser is the bridge field, including roads and railways (the others are communications and transmission towers, maritime, and other applications including industrial plants).
The company’s chief executive Kasuaki Toyosawa explained to investors last month (May 2025) that more than 30% of bridges in Japan have already reached their design life of 50 years, while in 15 years from now, about 80% of them will be obsolete.
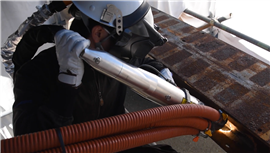
“If we continue to repair these damaged facilities after the fact, the national budget will no longer be available and the cost will be enormous. Therefore, the industry is shifting to preventive maintenance, repairing these parts before they break, and strengthening them,” he said.
He explained that the main cause of bridge failure is corrosion caused by rust, which is currently removed through shot blasting or sand blasting, which involves spraying sand and iron powder at high speed.
The company’s CoolLaser technology has adapted lasers for welding and laser cutting along with high-speed rotation to increase the laser’s output. Toyosawa claimed that it has several advantages over shot blasting, given that it is quieter, does not produce dust, and is able to remove rust more finely than conventional methods, including in areas with complex geometry.
He asserted that general contractors and major construction companies in Japan are already renting the equipment through equipment providers, while power companies are also starting to use the technology.
“The greatest advantage of using lasers is in the form of zero secondary industrial waste and no waste in total,” he said. “Secondly, salt is mixed in with the rust and this salt cannot be removed using existing technology. If you paint over it without removing it completely, the paint will deteriorate.”
He added that the technology is also safer for operators, with a dust collection device at the tip of the device’s nozzle that removes harmful substances like lead and PCBs that may be mixed into the coating.
Manual inspection methods still required
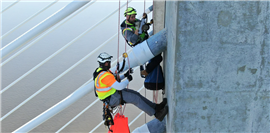
Depending on the regulations and mandates governing bridge inspections in a given market, there could still be limits to how much new technology can be used.
In the US, for example, where all bridges have to be inspected at least once every two years under the National Bridge Inspection Standards (NBIS), federal requirements govern the inspection processes.
And as Matt Sullivan, who leads a bridge inspection team at consultancy WSP in the US, some inspections require a hands-on approach to ensure things are being properly examined and measured.
That means that powered access and ropes are still required. “We use the drones as much as we can,” says Sullivan. “[But] a drone simply can’t replicate that physical, firsthand approach. That said, drones have proven to be a good addition to our toolkit.”
STAY CONNECTED

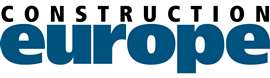
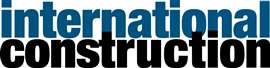
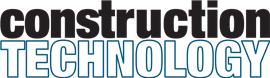
Receive the information you need when you need it through our world-leading magazines, newsletters and daily briefings.
CONNECT WITH THE TEAM
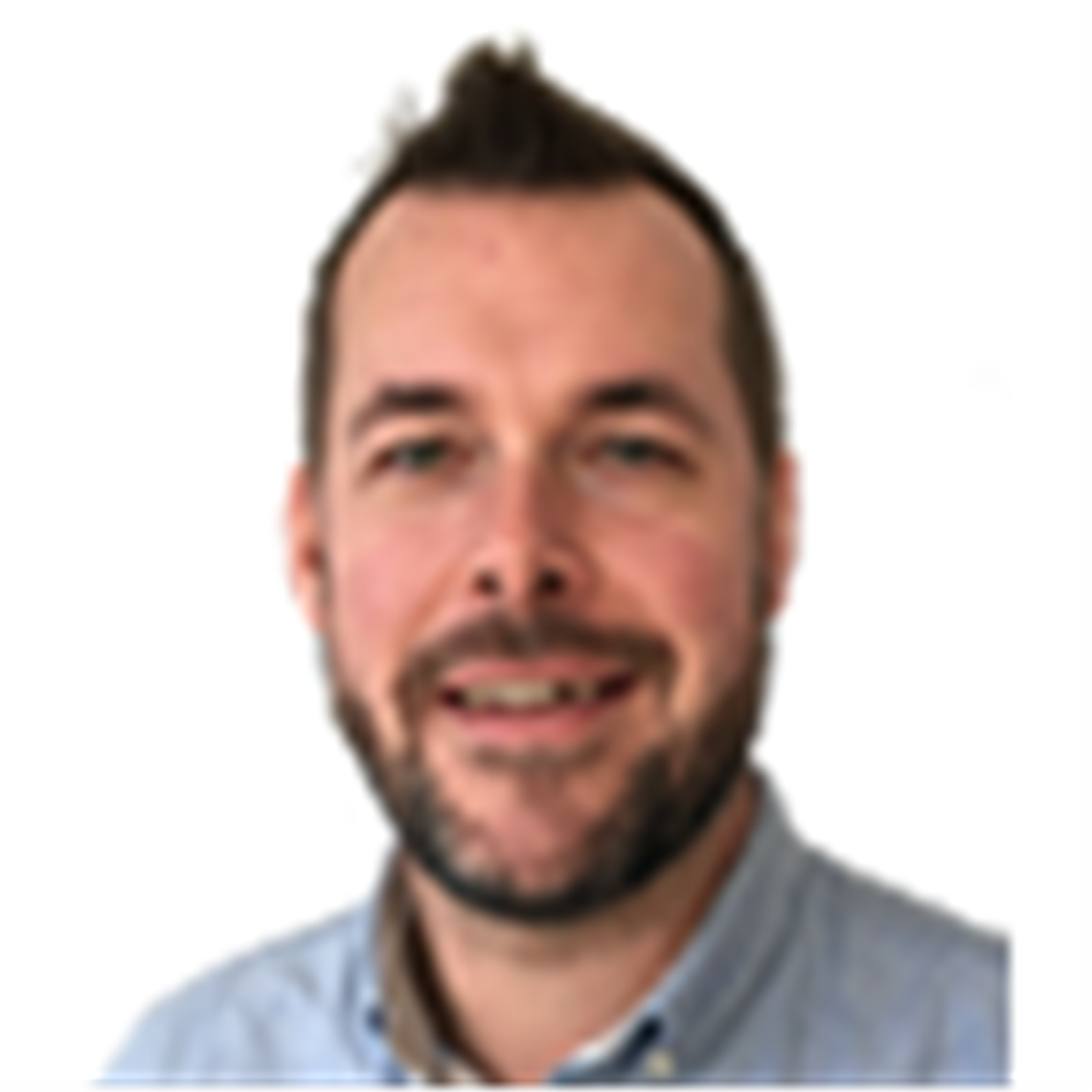
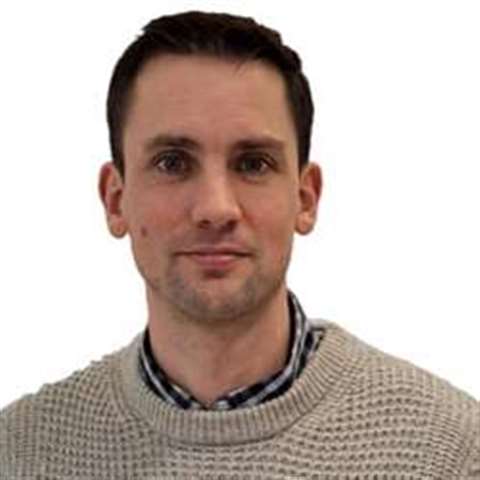
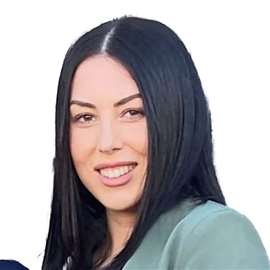
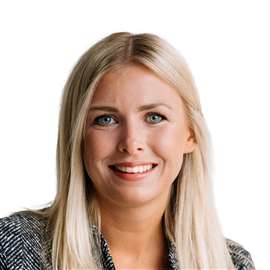