Read this article in French German Italian Portuguese Spanish
The future of hauling is articulated

Partner Content produced by KHL Content Studio
18 March 2024
Although the articulated dump truck (ADT) was first conceived in the 1950s, it wasn’t until the 1970s – when the first six-wheel-drive ADTs with bogie undercarriages appeared – that a new popular hauler was born.
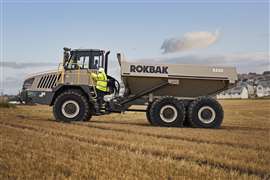
These machines were the first with wheels which could undulate over irregular terrain, without unsettling the dumper body.
Since then, ADTs have come a long way, with operators appreciating the reassurance of having six wheels firmly planted on the ground at all times.
Today’s articulated haulers are sure-footed, have a small turning radius and can maintain manoeuvrability in muddy, slippery and generally softer ground – some on gradients exceeding 30%.
Unsurprisingly, they continue to gain traction, literally, across quarrying, road construction, civil engineering and mining applications.
But the upsides of the modern ADT go way beyond manoeuvrability.
Product-focused development
Rokbak is a case in point. From its base in Motherwell, Scotland, the Volvo-owned company produces two articulated haulers, the RA30 and the RA40.
The company is a short-line product manufacturer, with its focus purely on these two machines – one with a payload of 28 tonnes, the other 38 tonnes.
With 37 years with the business, and 12 as product manager, Scott Pollock has seen a lot of changes, not least of which is the company’s rebrand from Terex Trucks to Rokbak in 2021, a move that sparked a dramatic change in both the machines and the company’s ethos.
While the new-look Rokbak hauler has received considerable praise for its sand-colouredbodywork and aggressive styling, Pollock says much of the customer feedback is focused on the reliability of a workhorse that can answer modern jobsite demands.
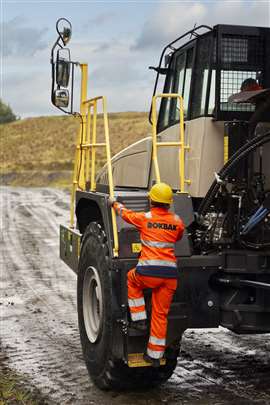
“At the end of the day,” he says, “the customer wants a hauler that works hard, with minimal downtime, that’s cost-effective, easy to operate and that’s productive.”
The difference articulation makes
Rokbak haulers are focused on performance, driven by a combination of heavy-duty axles, drivetrain gear reduction and differential locks.
As with the majority of ADTs, all three axles of Rokbak’s RA30 and RA40, remain in permanent all-wheel drive, giving enhanced traction, as well as reducing driveline wear and wheel spin.
Both machines feature transmission retarders, with the RA40 equipped with a variable retarder, which increases levels of control for operators, particularly reassuring when having to haul on very steep inclines.
The hauling power of the machines is impressive, with the RA30’s engine delivering 276kW and a maximum torque of 1880Nm at 1400rpm, and its big brother, the RA40 boasting engine power of 331kW and a maximum torque of 2255Nm at 1300rpm.
Rokbak’s regional sales manager for EMEA, Kenny Price, says, “Torque and rim pull are areas we focus on when it comes to the design of the trucks. They need to have that torque and pull when they’re fully loaded to move in an efficient manner.”
Scottish at heart
While Rokbak benefits from the financial backing of Volvo, as well as adopting many of its Swedish owner’s well-defined and proven working practices, it is an unequivocally Scottish company.
The haulers are designed and built in Motherwell, Scotland, with new innovations driven by the in-situ Rokbak R&D team. And, as is the case across the industry, technology is playing an increasing role in construction equipment.
“We’ve seen a real ramping up of functions and features in industrial equipment technology,” says Scott Pollock.
Future-proofing the next generation of ADTs is part of the strategy Rokbak has now developed.
Pollock says, “As we prepare for future motion and cleaner driving systems, you have to put in a foundation of technological infrastructure, for these systems to work effectively.”
The shape of things to come
Rokbak is working on operator equipment which Pollock says is “setting down the foundation for future innovation, so we do not run out of road.
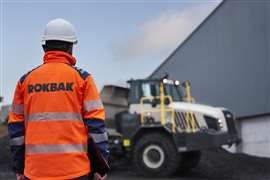
“Everything we release from now on needs to be future-proofed, so we can start building on the requirements of the customer – sustainability, future propulsions, green energy – which is all coming.”
At the same time, Pollock says, the need for new technologies must be balanced against the primary needs of customers, which have remained largely unchanged in recent years.
“Reliability and durability have to be a given for all buyers,” he says, “but if you’re working with a contractor in, say, a production facility – whether it’s a quarry, mine or waste disposal facility – they are very keen to understand how much this machine is going to cost per month, over and above just purchasing it.”
The philosophy of Rokbak, with its balance of future-proofing and old-fashioned ruggedness, has been condensed into four themes of innovation, sustainability, connected services and efficiencies.
These themes run through the company’s design and build practices, with each element merging with the others, ultimately creating a connected philosophy.
On Track for productivity gains
With this in mind, connected services is a logical theme to examine, and it is one that’s based primarily on Rokbak’s telematics system, Haul Track.
“Haul Track is our telematics system,” says Pollock, “but from that comes production, maintenance planning, protecting your asset, and further retail services.
“What started out as a GPS locator, 10 years ago, is now a wide and ranging system that incorporates productivity, maintenance planning, protection of the asset and further retail services.”
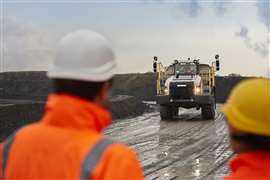
Knowing customers wanted a system that could aid their productivity, rather than simply notifying about fuel consumption, the location of the truck and, additionally, some machine faults, Rokbak released a new weigh-load feature, that communicates with the telematics system.
“Now the customer can sit remotely and have a real understanding of the productivity of the machine,” says Pollock. “You can put the data together, create production studies and get TCO [total cost of ownership] calculations done automatically.”
The system can also help reduce costly damage and minimise downtime. Pollock says, “With automated protection, if there is a fault code, a signal can be sent to the truck’s inhibitor, ensuring reduced gearing or reduced speed, to uphold operator safety and machine protection.
Behind the scenes
While operators will see clear differences in the next generation of RA30s and RA40s, many of the advances will be hidden – some are not part of the machine at all.
As Pollock says, “Some of the new innovations will require new tooling and new competencies to put the new trucks together.
“We’ve invested in two robot welders; that gives us a consistent penetration weld, as well as ensuring the throughput from the factory is leaner.
“We’ve also updated the CNC (Computer Numerical Control) machinery for all our machine parts – for more accuracy, consistency and quality of build.
“What we’re trying to do is make a cost-effective product and manufacturing efficiencies are a part of that.”
The road to net zero
The benefits of being lean and efficient in manufacturing cannot be overstated, but the balance between sustainable practices and the bottom line is key.
As much as the equipment manufacturing industry has shown a willingness to get on board with net zero goals, it also has a duty to fulfil customer requirements, one of which includes offering hardworking, hardwearing machines at an affordable price.
The hauler is a heavy yet extremely mobile machine and we are yet to see a model on the market powered by electricity or hydrogen.
The Rokbak machines have, however, made the switch to HVO (hydrogenated vegetable oil), which is one of the greenest fuels currently available.
Pollock says, depending on the grade, HVO can reduce carbon emissions by between 60 and 80%.
“That is a step towards our strategy of having a 30% reduction in CO2 emissions by 2030, and 0% by 2040.
“In our trucks, right now, you can add HVO – it can be mixed with diesel – with no adverse effect, no adjustments required and no additional filters.”
ADTs are a major investment for mining, quarrying and construction businesses – all of which are trying to navigate tightening environmental regulations and challenging economic markets.
As times remain tough for earthmoving industries, Rokbak’s holistic approach to the development of the next generation of machines – encompassing sustainable practices, new technology and efficient manufacturing processes – could be a smart blueprint for others to follow.
Rokbak assisted with the research on this article.
For more information on the RA30 and RA40 articulated dump trucks, visit the Rokbak website.
STAY CONNECTED

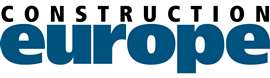
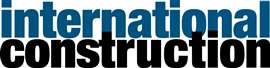
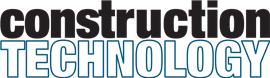
Receive the information you need when you need it through our world-leading magazines, newsletters and daily briefings.
CONNECT WITH THE TEAM
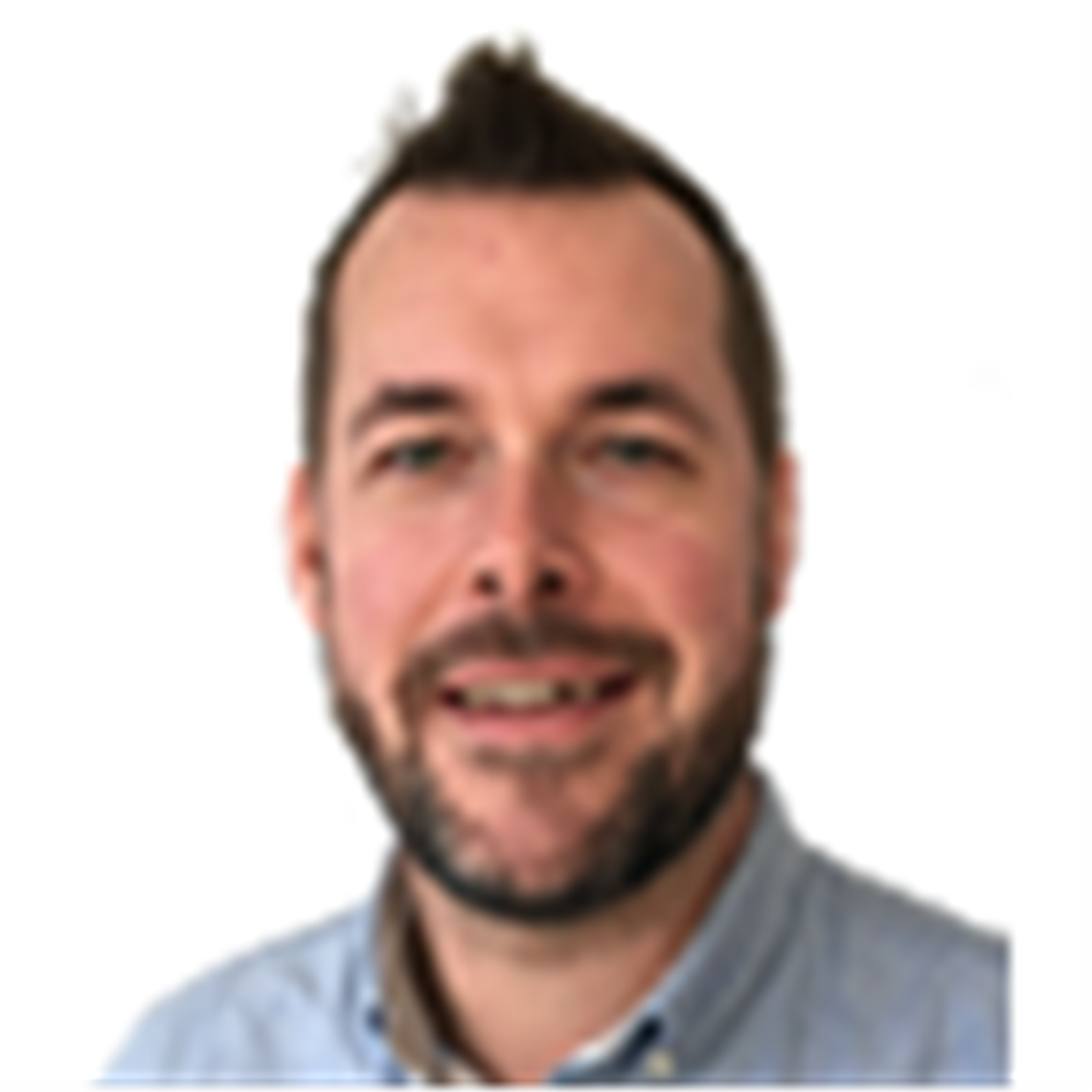
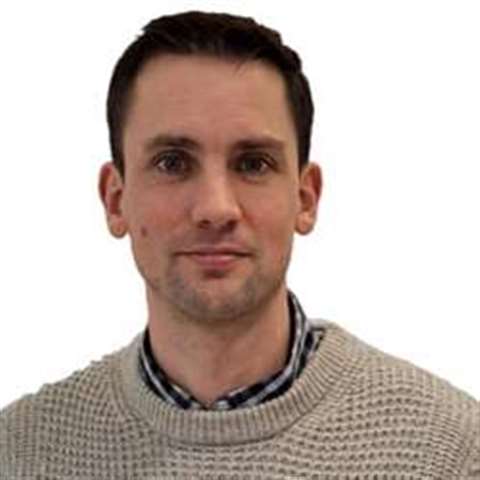
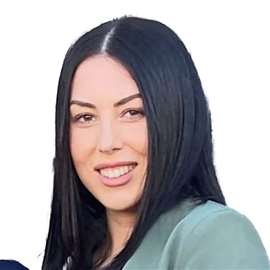
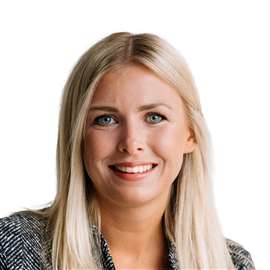