Read this article in French German Italian Portuguese Spanish
Smarter roads: The emerging technologies behind modern paving
16 July 2025
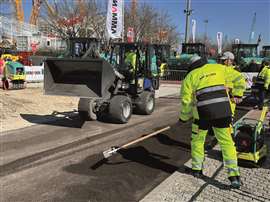
To the untrained eye, road construction may seem simple: here’s the path, the material, the machine – go make a road.
But building roads remains tough work, with success often measured in millimetres – in pavement evenness, density, or smoothness. New sustainability goals and evolving materials have introduced fresh challenges, and while machines have gotten smarter, the gains in efficiency often happen behind the scenes – incrementally, deliberately.
The question isn’t just, “What’s new about today’s roads?” but: “What’s new about how we build them?”
Automation meets asphalt
In March, at the 2025 World of Asphalt/AGG1 Expo (WOA) in St Louis, Missouri, US, it was clear that the most critical innovations are happening beyond the iron. The show highlighted an obvious trend: the future of roadworks depends on smarter systems, better data, and adaptive machines.
One stand-out machine launch at WOA this year was Hamm’s Smart Compact Pro, a real-time density control system using temperature sensors, accelerometers, and a new scanner to fine-tune compaction on the fly. Hamm is a brand name under the Wirtgen Group-John Deere family of machines.
“Once the sensor is calibrated, we can go to work,” says Dan Sant Anselmo, applications support manager. “If I want 95% density, the machine dynamically compacts until we hit that, then it shuts off vibration.”
Smart Compact Pro aims to eliminate traditional core sampling, offering results within 1% accuracy. Anselmo also noted that automated mapping and surface temperature monitoring help prevent overwork, preserving asphalt quality.
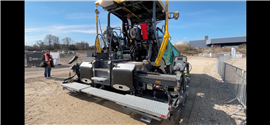
“The tighter you can make the job,” he tells International Construction, “the longer the road’s going to last. That’s better use of tax dollars.”
Wirtgen also showcased its 3D paving integration on the Vögele Dash series, built for cross-compatibility with Trimble, Topcon and Leica systems.
“If a system fails at 2am, you don’t want to swap a full control package,” says product manager Laikram Narsingh. “You just want to keep laying mix. That’s what this allows.”
Even as machines get smarter, many gains in roadbuilding come millimetre by millimetre.
“Every extra percent below target density shortens road life,” Anselmo said. “Every percent above adds risk of cracking.”
It means that high-tech improvements in the machine can see the unseen for contractors, reducing time spent, materials used and labour needed.
Data-driven construction
Automation is only one step; the foundation for full autonomy is data.
Trimble’s mobile mapping platform, the MX60, illustrates just how data is reshaping roadbuilding. Mounted on a vehicle, the system collects laser and photogrammetric data - capturing road depth, conditions, and composition in real time.
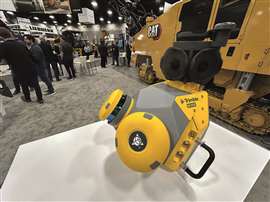
“We now have a digital twin of what the world looks like,” Kevin Garcia tells International Construction. He is the general manager of civil specialty solutions for the US-based surveying and construction tech firm. “Instead of relying on old paper files, we scan, layer and archive every job. That becomes the new baseline.”
The system supports multiple stakeholders – from DOTs and surveyors to contractors so once it’s timestamped and spatially located, it can be used for everything.
Trimble engineer Patrick Dimeco added that the system feeds into planning and billing. “We track progress, invoice off it, and learn what worked. That helps on the next bid,” he notes.
While it sounds simple, the reality is most roadworks firms’ volume of work and expanse across locales means manually tracking this information can be, at best, cumbersome.
Concrete is also seeing an infusion of automation and artificial intelligence (AI) alongside its production and uses. Mexico-based materials producer and provider Cemex is now deploying AI to optimise finish mill operations – an early-stage but promising use of machine learning in cement production.
“You train that AI to look for certain outputs, and you let it solve them,” Joel Gassalini tells International Construction. He serves as Cemex VP of sustainability, advocacy and customer experience. “We’re seeing 10% efficiency gains already on cement and concrete production.” He adds that the data gleaned today will grow exponentially as the AI systems better-learn the segment.
Similar methods are being trialled in kiln control and mix optimisation, where systems adjust real-time variables to maximise throughput or consistency, which should be music to the ears of road construction contractors who need to spend less time figuring out new mixes.
Gassalini notes that AI can also enhance planning and logistics. “From dispatch to delivery, we’re rethinking how we use trucks. Things like idle time, delivery timing and batching – all of that feeds into carbon and cost.”
Contractors, too, can benefit, as scanning a jobsite can catch grading issues early. Trimble’s Garcia calls this approach “construction archaeology” – holding information on the lifecycle of a road before it even needs repair.
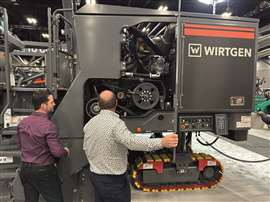
AI is also beginning to assist with early-stage planning, including permit routing, risk forecasting, and utility clash detection, extending data-driven workflows across the entire project lifecycle.
Dimeco sums up the advantages neatly, saying, “Better roads, fewer surprises. And every surprise you avoid is money you keep.”
Meanwhile, Q Point, a brand developed by hiQ solutions and Switzerland-based Ammann Group, aim to create an open, manufacturer-independent digital platform to connect every stage of roadbuilding – from material production to transport to paving and beyond.
“The idea is to support the entire process with a connected workflow,” Q Point CEO Thomas Leopoldseder says. “Planning, production, transport and paving are linked through one system.”
The Q Site application allows users to plan projects on a web browser, phone or tablet. If the weather changes, field crews can adjust the plan and update the asphalt plant in real time. This seamless communication helps avoid stoppages and wasted mix, Leopoldseder says.
“We even connect with third-party pavers and rollers using sensors and GPS,” adds Leopoldseder. “The goal is to visualise every step – from mix temperature to roller passes – to maintain quality and track environmental impact.”
Q Point is also working to incorporate recycling workflows and calculate CO₂ footprints across projects. “Clients can see the full ecological impact, including transport, machine operation and material mix,” says Leopoldseder.
Operator-first machines with built-in flexibility
Smart machines aren’t just about automation – they’re also becoming easier to run, maintain and adapt.
Komatsu’s new WA475-11 and WA485-11 wheel loaders feature the company’s Hydraulic Mechanical Transmission (KHMT), delivering up to 12% lower fuel use and 21% more power than previous models. A new yard loader configuration, shown at World of Asphalt, includes wide tires, a 7.2-cu-yd bucket and added counterweight.
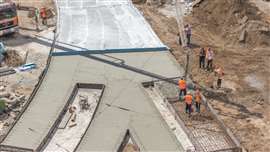
“We designed the engine from scratch,” says Kwanju Cho, Komatsu product manager. “The new cab includes joystick steering, better visibility, and even room for a large lunchbox. It’s built for long days.”
Dynapac’s CP28 pneumatic roller also got a full redesign. “It now standardises across markets and integrates temperature sensing,” Vijay Palanisamy, VP of product management, tells International Construction. “You can do more with less confusion.”
Bomag’s CR 820 T2 paver similarly focused on usability. “We kept the flow gates mechanical for feel, but added fine auger controls and better screens,” product specialist Zach Watson explains.
These small changes add up – making machines easier to learn, safer to run, and faster to master.
That mindset of adaptability is also driving interest in onsite batch plants and volumetric mixers, which Cemex sees as growing practical tools for urban or remote projects.
“The tech on these trucks has advanced significantly – they’re no longer just transport; they’re mobile production units,” says Cemex’s Gassalini.
Volumetric mixing reduces waste, especially on small or custom loads, while onsite batching allows electric mixers or autonomous tech better access to materials in controlled environments.
Sustainability gains traction, quietly and practically
On the power side, while electrification is still rare in roadworks, practical steps to electric roadworks is accelerating.
Volvo Construction Equipment previewed its DD15 Electric compactor and unveiled updates to soil compactors that lower emissions and reduce fatigue.
“We’re preparing for when electrification scales,” Dave Foster, VP of marketing and communications, tells International Construction, noting the company has not stopped improving fossil fuel engines, either. “In the meantime, we’re making diesel smarter.”
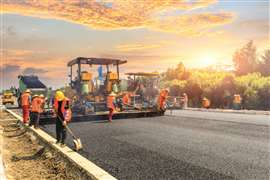
Benninghoven, part of Wirtgen Group, retrofitted a mixing plant in Vienna with a hot gas generator to allow 100% recycled asphalt production, reducing emissions by up to 20% at 60% reclaimed asphalt pavement (RAP).
“There’s no compromise on quality,” said Steven MacNelly, head of R&D for Benninghoven. “But you save fuel and CO₂.”
US-based Philippi-Hagenbuch has leaned into material upgrades to tailgates, water tanks, and sideboards to reduce waste, spillage and dust. The company also adopted SSAB Zero, a zero-emission steel, across its product line.
“These small tweaks add up,” says Philippi-Hagenbuch sales VP Josh Swank. “When scaled, they deliver real safety and sustainability benefits.”
At Cemex, sustainability is also reshaping how producers view profitability.
“It’s not just about regulation anymore,” says Gassalini. “If I can figure out how to lower carbon efficiently – or find a competitive advantage to do it – that gives me a leg up.”
He points to seemingly simple logistics shifts, like sending aggregate trucks at night instead of peak traffic, as low-cost ways to cut emissions and diesel use.
The company is exploring carbon capture through a pilot plant in Germany, but Gassalini acknowledges challenges. “You need a place to store it, maybe build pipelines – it changes the cost structure completely.”
In the meantime, incremental wins – from reducing truck idling to using more supplementary cementitious materials – offer road builders clearer gains on emission and material reduction, helping lessen the load before even turning on a paver.
Looking ahead
From autonomous compaction to site-wide digital twins, roadbuilding is quietly getting transformed by tech and practicality.
The machines still matter, and they always will, but it is increasingly what’s inside them, or what surrounds them in data, that defines future success.
For contractors under pressure from cost, regulation, and workforce gaps, these changes offer hope: fewer surprises, less rework, and more control.
The road ahead may still be paved in asphalt and concrete—but how tightly and precisely that road is built will define how long it lasts, how much it costs, and how far public dollars stretch.
And in that sense, fine-tuning the job is no longer optional. It’s the future of roadworks.
Turning down the heat: new life for old asphalt
Low-temperature asphalt mixes and recycled materials are gaining momentum as contractors look to reduce emissions without sacrificing performance.
Known as warm mix asphalt (WMA), these formulations are produced at temperatures 20–40°C lower than traditional hot mix, cutting fuel use and lowering odours and fumes on site.
Across the US, more than 50 million tons of reclaimed asphalt pavement (RAP) are reused annually, according to National Asphalt Pavement Association (NAPA) data; this makes asphalt the most recycled material in the country by volume.
In Europe, the European Asphalt Pavement Association (EAPA) reported an increase in RAP usage during 2018, indicating a growing trend in the region.
Globally, it’s estimated that over 750 million tons of RAP are generated annually.
Though WMA and high-RAP designs are already proven in many contexts, researchers and producers continue to refine mix performance and durability, especially for use in extreme climates or high-traffic routes.
STAY CONNECTED

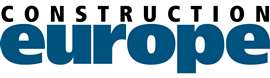
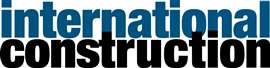
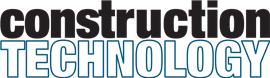
Receive the information you need when you need it through our world-leading magazines, newsletters and daily briefings.
CONNECT WITH THE TEAM
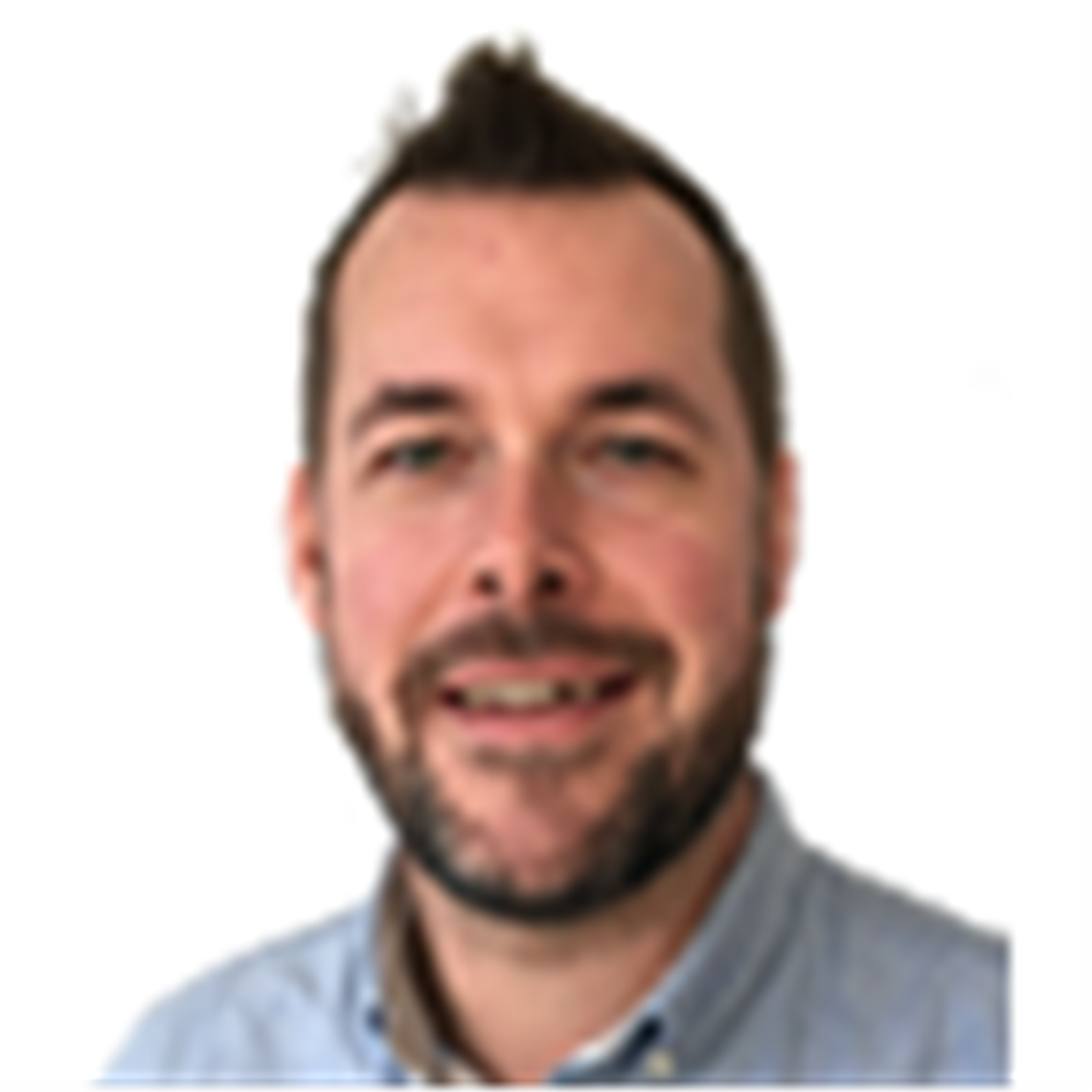
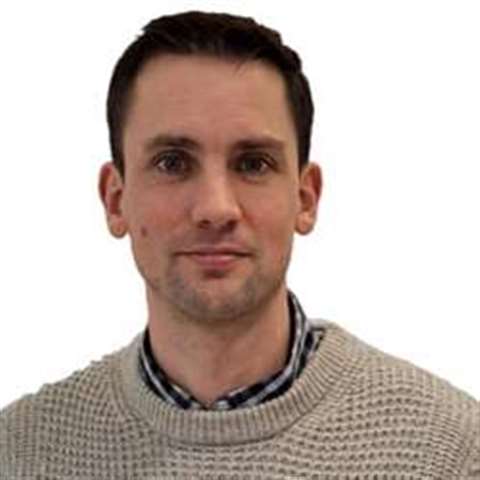
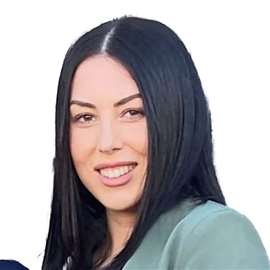
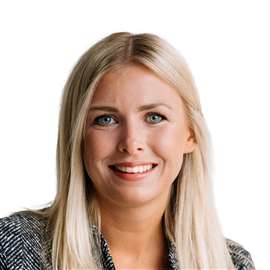