SBM shows latest ‘customer inspired’ operational concrete plant
14 June 2023
At a customer event in Magdeburg, Germany, SBM showed concrete specialists its latest semi-mobile concrete mixing plant, the Dynamix 2500.
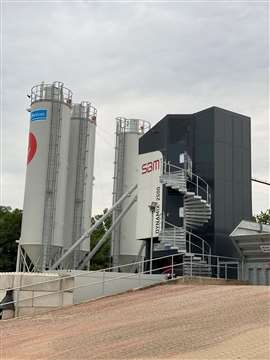
First launched at the recent Bauma exhibition in Munich, SBM says the plant is the result of calls from customers for a reliable technology that can deliver high concrete yields from a much smaller footprint than the average stationary plant.
The relatively dimensions of the Dynamix 2500 are particularly favourable for customers who need to get production underway quickly, avoiding many of the delays that can come with obtaining permissions to erect permanent stationary plants.
Rapid installation
In the case of the Magdeburg plant – the first to be installed for a customer – installation took a little under four weeks, although the company believes a two-week installation should be possible.
The unit itself, which has a 2.5m3 twin-shaft mixer, delivering approximately 115m3 of ready-mixed concrete per hour, is erected in one piece and arrives pre-wired.
The 3.5m mixer platform is completely pre-assembled on a base frame, which is suitable for low-bed trailers and cranes.
Located directly next to the mixing tower are four 69m3 mobile binder silos.
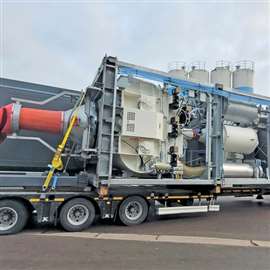
The plant also uses a four-chamber mobile aggregate store, with a maximum capacity of 128m3. From here, aggregates are metered via a weigh belt and fed into the mixer via a vertical tipping bucket lift.
Design focus
The Dynamix 2500 is available in three different versions: winter, summer and standard.
In the winter version, the mixing tower – as well as the tipping bucket lift and hopper transfer, is enclosed by lightweight panels, newly designed from UV-resistant sandwiched plastic.
SBM says the winter version can continue to produce concrete in all weather conditions.
The company adds that a focus on the ergonomic layout of the new plant resulted in a compact arrangement of the feeders of the weighbridge and easy and safe access to both mixing tower platforms, via an external spiral staircase.
Gerhard Mittendorfer, international sales manager for SBM, said the plant requirements of customers are changing, along with the increased use of recycled materials.
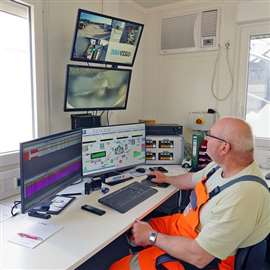
Regarding the mobile aggregate story, he said, “We regularly have four bins, but what we are learning at the moment, especially with recycled concrete, is that four types of aggregates is sometimes not enough any longer.
The direction of the market is for five or six different bins and we now have a solution for that as well.”
Expert views
The showcasing of the Dynamix 2500 plant at the Happy Beton site, coincided with a symposium on sustainability challenges and opportunities for concrete manufacturers.
Issues raised during the event, by experts in laboratory testing of concrete included the fact that the amount of recycled material available for the construction of buildings is sometimes in short supply.
Experts from Bautec also said maintaining consistency and quality of concrete might mean smaller percentages of recycled aggregates used on a greater percentage of projects, could be preferable to using large amounts on a small number of ‘showcase’ projects.
STAY CONNECTED

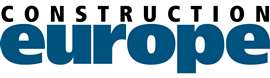
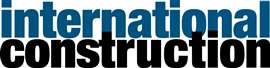
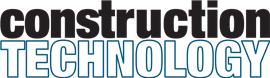
Receive the information you need when you need it through our world-leading magazines, newsletters and daily briefings.
CONNECT WITH THE TEAM
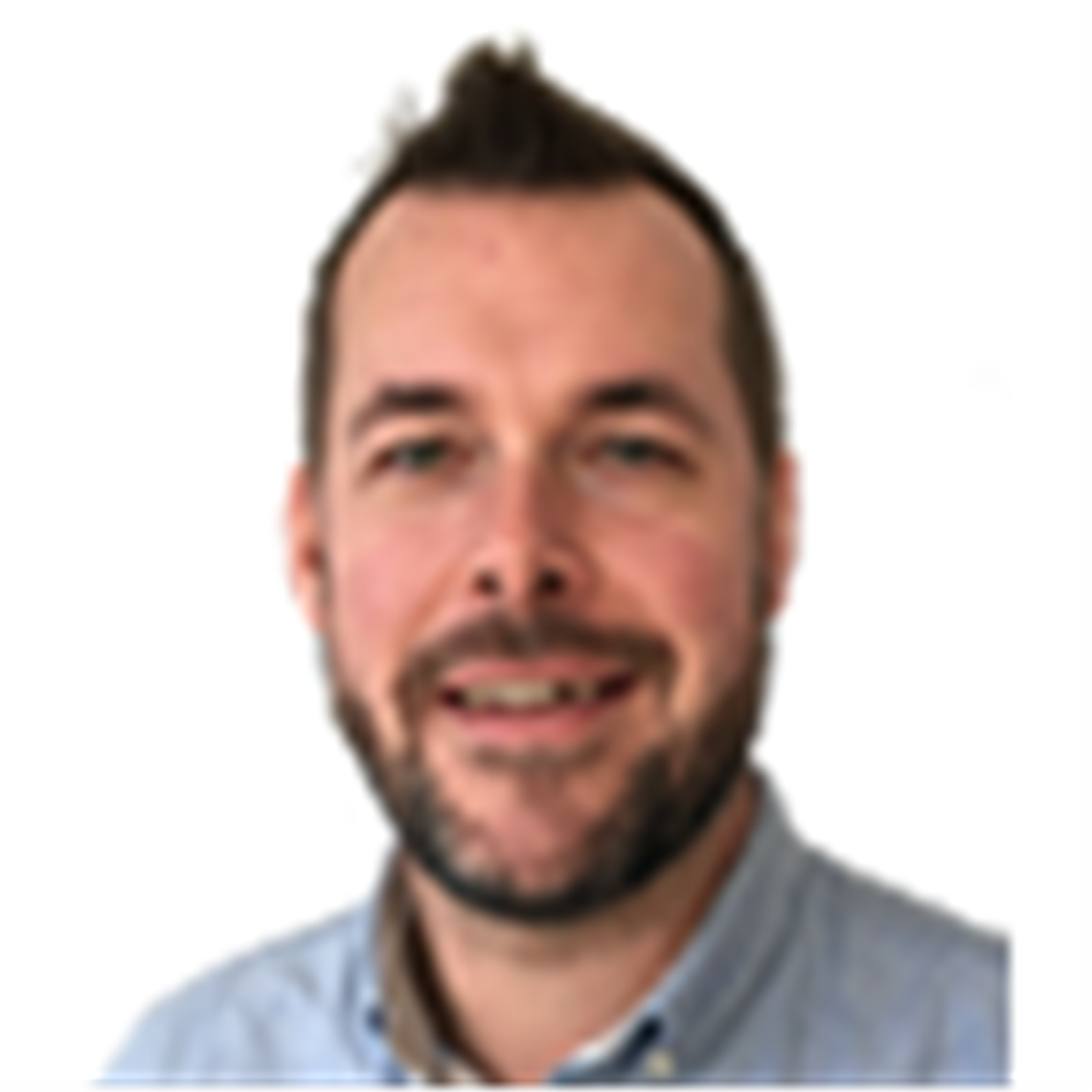
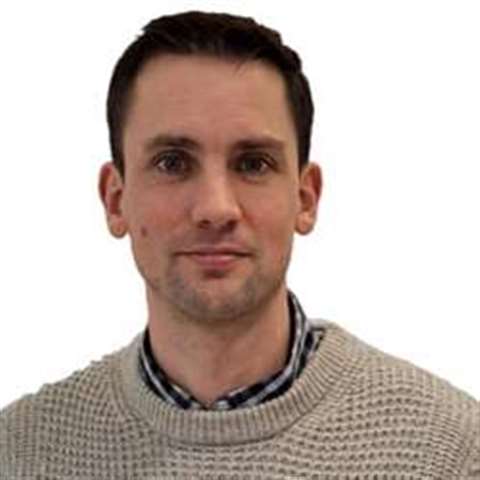
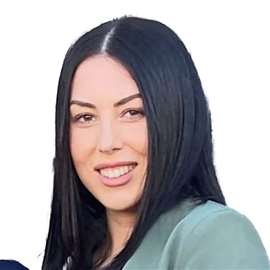
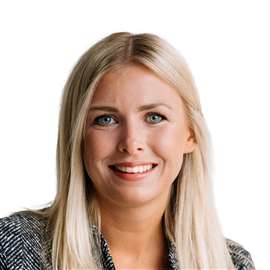