Project overview: Galataport
12 April 2021
Salvatore Miranda, a senior engineer with the Italian contractor Trevi, gives an insight into the fascinating port project in the heart of Istanbul

In 2016, the Italian construction company Trevi was awarded the contract to undertake major renovation and expansion work at the historic Galtaport cruise ship terminal in Istanbul, Turkey.
Having not undertaken any construction work in Turkey for some years, Trevi could not have chosen a more complex and challenging task than this €1.5 billion project.
Not only did the package include the construction of the world’s first underground cruise ship terminal, but it also called for the delicate underpinning of a number of historic buildings at the port.
This year, with the project successfully completed, Trevi has described the extraordinary complexity of the port rebuild.
In an in-depth virtual presentation, senior geotechnical engineer on the project, Salvatore Miranda, described some of the challenges the company faced throughout the three-year project.
To begin with, he explained that Galataport covers some 1.2km of coastline and covers an area of approximately 100,000m2. It is divided into two distinct jobsites: the Salipazari quay and the Karaköy quay.
On studying the original plans for the work, he said, Trevi engineers immediately noted some challenging issues, including a potential seismic hazard, the risks to the historic buildings of significant groundwork and the issues of having numerous contractors on site simultaneously. Furthermore, the entire project would be taking place in the heart of a city containing 20 million people – and the port would continue to operate throughout the project.
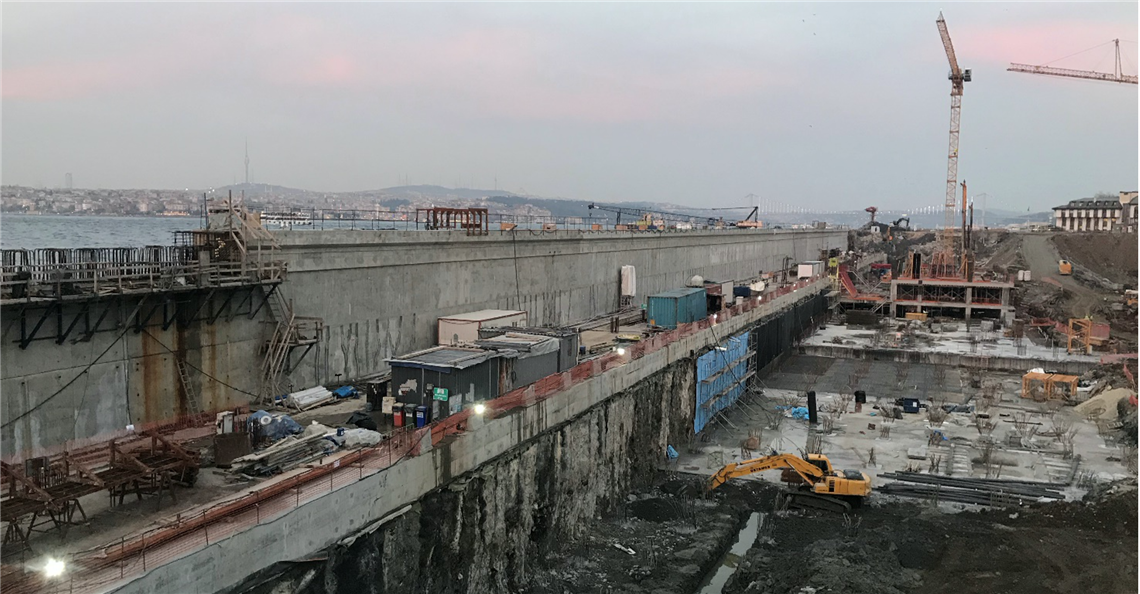
It became clear that cutting-edge technology would be required, as well as complex logistical analysis.
Salipazari quay
In Salipazari quay, the underground terminal was to be constructed. Trevi first had to excavate to approximately 13m below sea level. In doing so, 65,000m2 of soil had to be excavated to 15m below ground level.
A 1.2m-thick diaphragm wall was constructed to allow for the excavation, before tension piles could be bored to a depth of 15m. Trevi utilised the equipment of its sister ground engineering equipment company Soilmec across the project, recruiting a mechanical grab and hyrdomill for the diaphragm wall build.
The process demanded significant deep soil mixing, with a thickness of 1500mm and a total volume of 250,000m3 of treated soil.
The soil improvement against liquefaction required 100,000m2 of stone columns and a pile foundation of 1,000mm-diameter bored piles, as well as a dewatering system across the entire site.
The quay wall is a combination of steel combi-wall and a reinforced concrete diaphragm wall, with soil improvement by deep soil mixing between the two.
Originally, the quay was constructed on the sea-side as a deck on piles.
Descending from the deck, the ground constituted uncontrolled fill, followed by loose silty sand, then medium stiff clay and finally greywacke limestone.
Once the original quay had been demolished, Trevi backfilled the soil, then used its own patented Turbojet technology for the deep soil mixing.
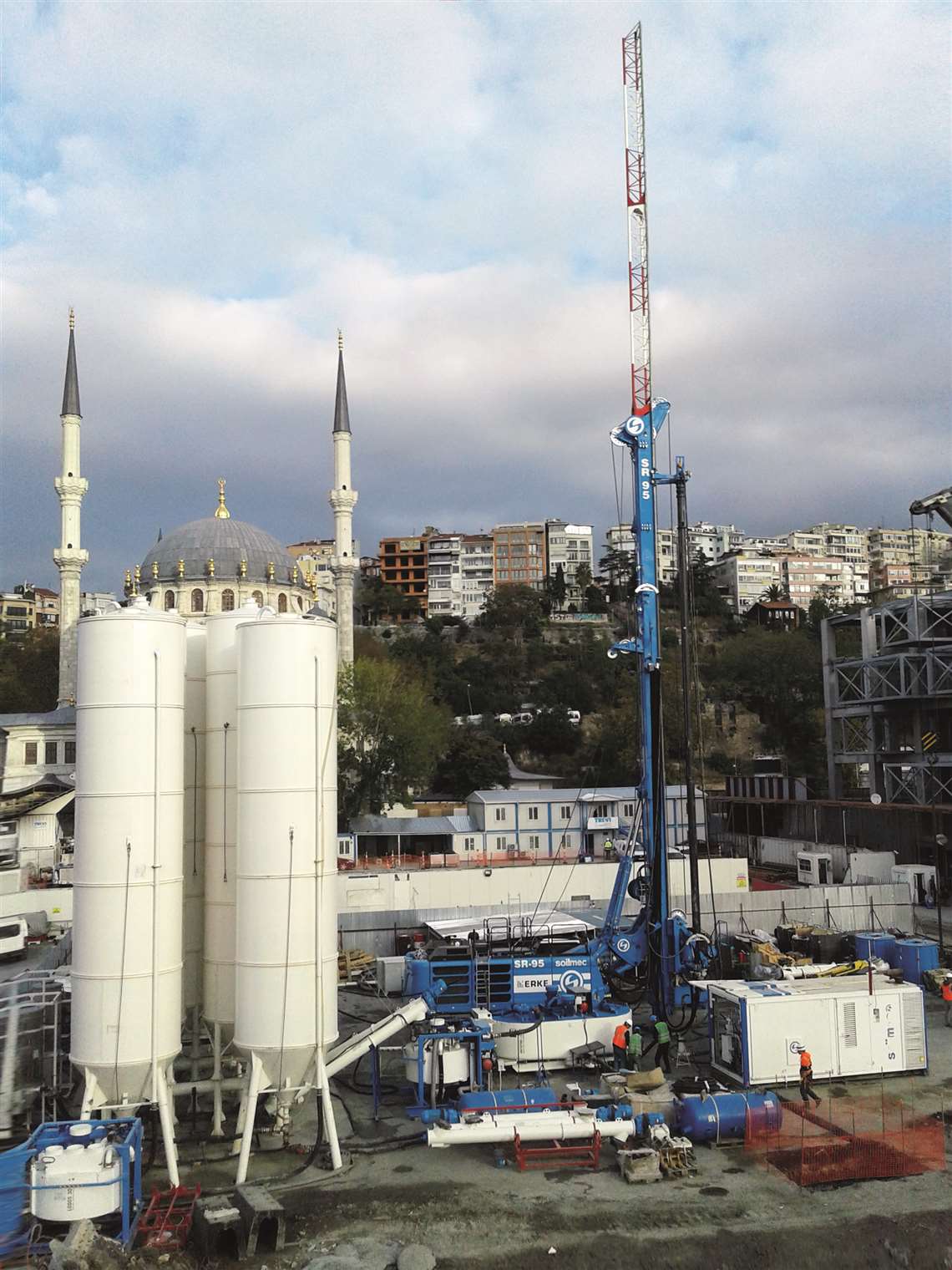
The method involves the disaggregation and mixing of the soil by the mechanical action of the blades and the kinetic energy generated by high-speed jets of cement grout.
Only after the completion of the soil improvement, could the diaphragm wall be installed. This was undertaken by the new Soilmec Hydromill SC-135 Tiger rig, which was used by Trevi on a project for the first time.
Once the work on the soil behind the combi-wall (the quay wall) was completed, a gangway could be constructed to connect it to the diaphragm wall behind.
After this, the excavation could be safely carried out to enable the construction of the underground terminal building.
Karaköy quay
At Karaköy, where historic buildings were to be preserved, Trevi had to construct 13m diaphragm walls around two such buildings, where basements were to be constructed.
Subsequently, the foundations of the buildings were improved using jet grouting from the inside and also through the use of underpinning micropiles to a depth of 13m.
Where the new basement excavations were to be undertaken, a 2m-thick jet grouting bottom plug was installed, to prevent water incursion. Furthermore, elliptical jet grouting was undertaken to mitigate the risk of liquefaction.
As well as further installation of permanent micropiles and bored tension piles at Karaköy, Trevi was also tasked with dewatering and long-term monitoring of the site.
In fact, Trevi established a monitoring network, not just on the main buildings, but on a number of neighbouring buildings. In the main buildings, the technologies introduced included inclinometers and pressure cells installed in walls to assess wall displacement, settlement plates to assess ground settlement, and 3D prisms, magnetic settlement columns, tiltmeters and liquid levelling systems, to assess building movement.
Sustainability through technology
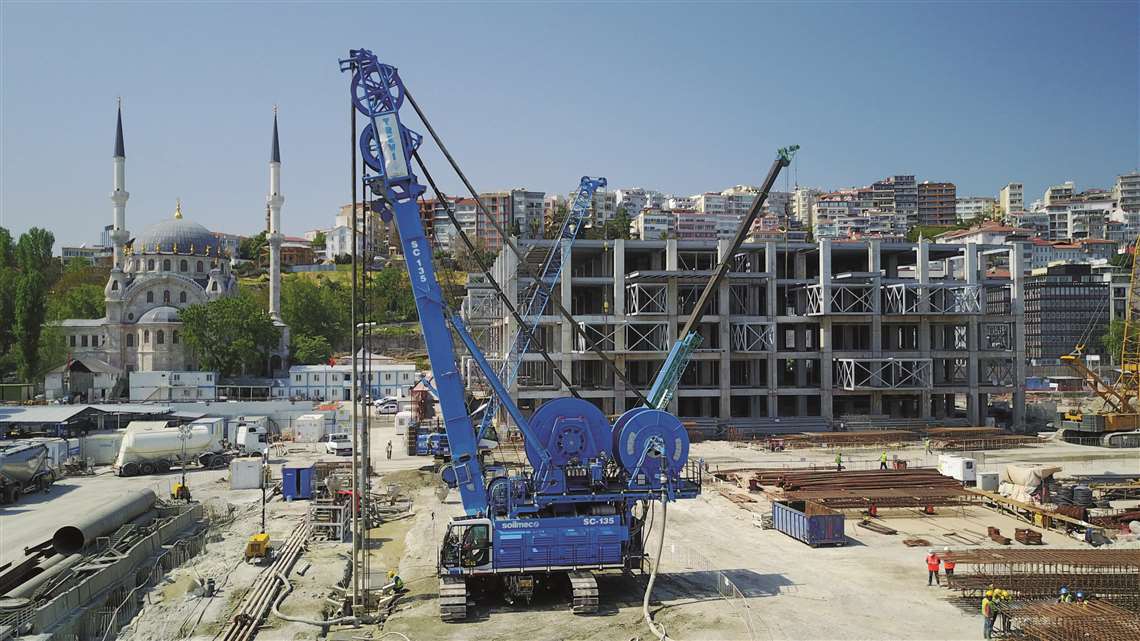
In total, Trevi worked on the complex and challenging project for three years.
The result, however, was more than satisfactory, with the Salipazari element picking up an American Green Building Certificate LEED Gold Target award, and the Karaköy buildings collecting a British Green Building Certificate BREEAM Excellent Target award.
Salvatore Miranda says both the design and construction phases played their part in securing recognition for the sustainability of the project.
“It starts from the design phase,” he says, “taking all the precautions and actions in order to improve the energy and water efficiency of the site and to reduce the carbon emissions.” Grey water recovery was also implemented, as well as a reduction of the heat island effect through the installation of green roofs.
Miranda adds that the sustainability of the construction phase was equally important, “from protecting the sediment on site, to the use of local and recycled materials, as well as choosing materials and chemicals that are not harmful to human health.”
Finally, Miranda describes the monitoring of the environment and the social impact of the port construction work “such as noise, PM10 [concentrations of particulate matter], settled dust and the continuous measurement of seawater quality.”
The construction of Galataport’s innovative underground cruise ship terminal makes it one of the most fascinating projects of recent years.
The detailed description of the challenges faced and the technology utilised to carry out the crucial geotechnical work only adds to its great interest.
You can register here for free, to view the complete webinar.
STAY CONNECTED

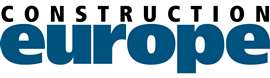
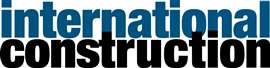
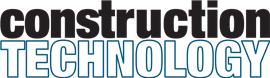
Receive the information you need when you need it through our world-leading magazines, newsletters and daily briefings.
CONNECT WITH THE TEAM
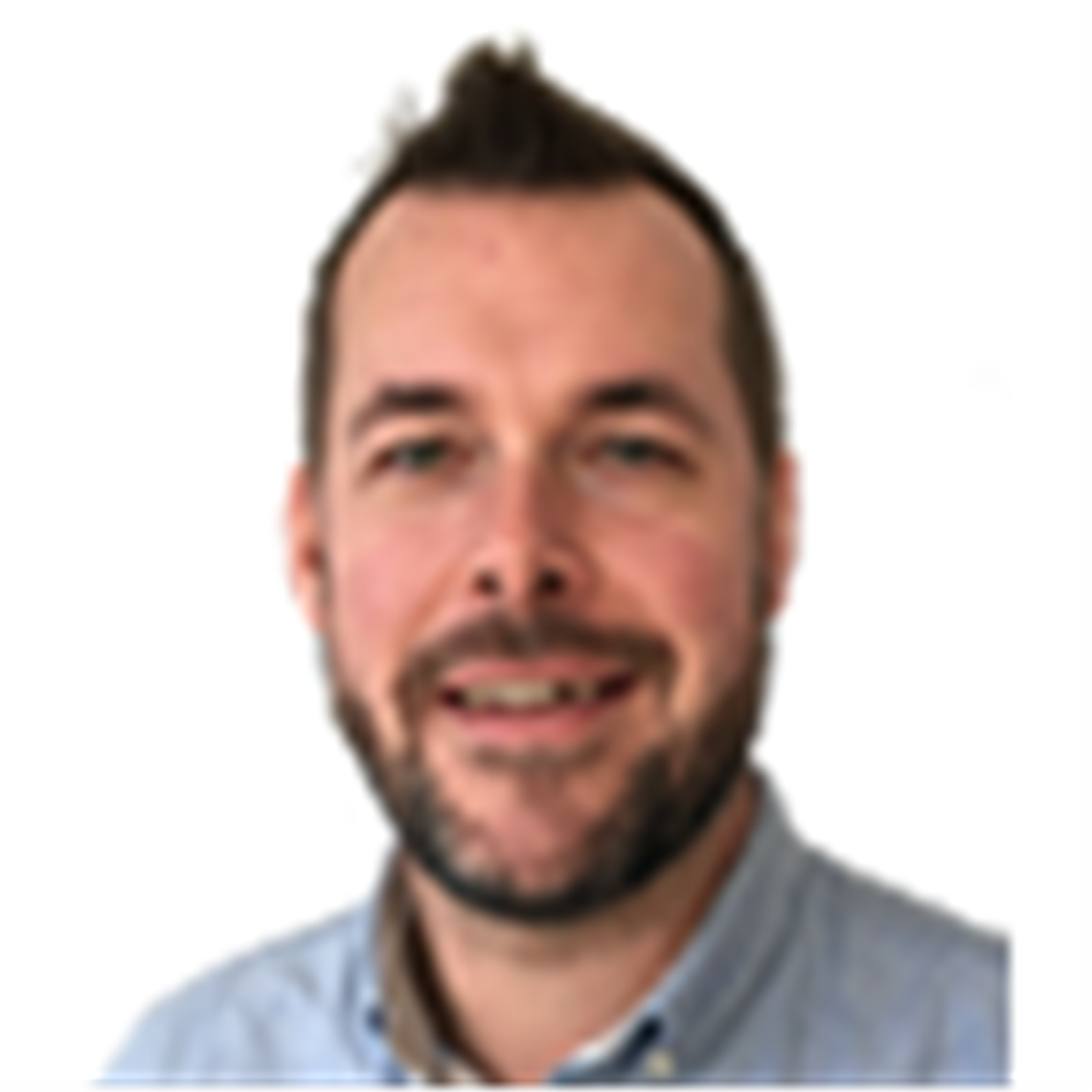
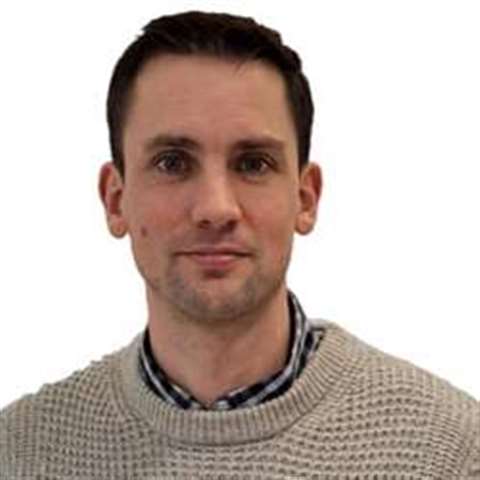
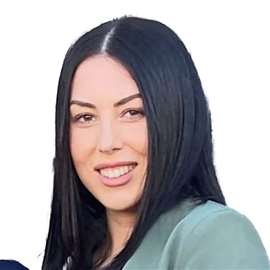
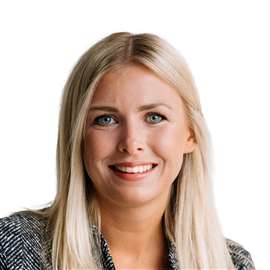