How can jobsite health and safety be improved?
26 April 2022
Safety risks and dangers are well known to the construction industry. Catrin Jones examines what more can be done and whether technology can play a key role in improving safety
As construction safety continues to evolve, improved safety equipment and wearable technology are helping to drive the industry forward. Despite the improvements that have undoubtably been made – although these do vary from country to country – a renewed commitment to safety and training is still vital for the industry’s future, especially due to the level of preventable injuries and deaths each year.
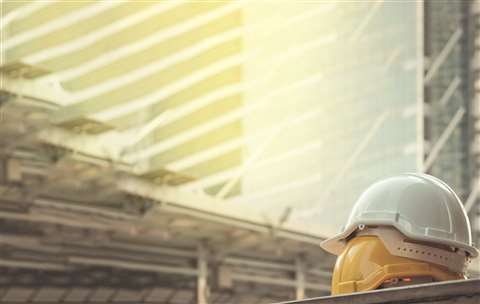
Construction has been revealed as the fourth most dangerous sector, according to research from health and safety consultants Arinite, with a global average fatality rate of 10.24. In 2019, the US saw 5,333 deaths from construction accidents alone, the highest fatality rate of any industry. In the same year more than a fifth of all fatal accidents at work in the EU took place within the construction sector.
Perhaps surprisingly, Arinite’s research found that the country with the highest rate recorded was in Europe, in the Republic of Moldova at 44.7. Recognising that more needs to be done to reduce their fatality rate, Moldova will adopt the International Labour Organization’s convention – Occupational Health Services Convention, 1985 (No. 161) – in May 2022. This will address both the country’s poor oversight of occupational safety and health, as well as its failure to implement safe practices.
Robert Winsloe, managing director at Arinite, says, “It is the responsibility of all business owners, no matter what industry you work in or the size of the company, to comply with their country’s health and safety legislation.
“Working at height, moving objects as well as slips, trips and falls are all common health and safety risks. Failing to implement the required measures could put your employees’ lives at risk. Even a low-risk job can become dangerous if you do not meet basic health and safety requirements,” added Winsloe.
The cost of ill health and injury in construction
According to a new study of data from the Health and Safety Executive (HSE) by the construction site storage company SiteStak, the estimated cost of ill health and injury in UK construction is between £963 million (US$1.2 million) and £1.4 million (US$1.9 million) per year.
Despite the cost of injury, it was reported that there has been a 7.85% year-on-year decrease in 2019/20 in non-fatal injuries to employees and self-employed people in construction in the UK. Huge strides have been made in safety on construction sites over the last decade, with non-fatal injuries in UK construction dropping by 45%.
Peter James, managing director of SiteStak, says, “While the number of construction-related injuries is on a slow overall decline, our study reveals that ill health in the industry is still leading to a large human and financial cost. Fatal and non-fatal injuries in construction remain stubbornly high and it is sad to see that males and older workers seem to be disproportionately affected.
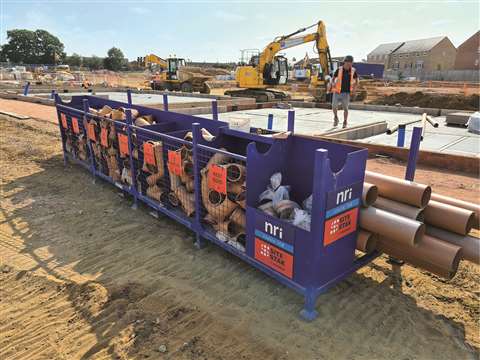
“Given our findings, we would like to see more measures to ward against injury where feasible. This should include better management of construction sites and could also mean stronger adherence to health and safety procedures, greater use of safety apparel, more regular breaks, and more thorough risk assessments.”
SiteStak says that its materials management system has been specifically designed to improve the organisation of building sites. The system aims to prevent trips and falls by reducing excess materials lying on-site and the need for human movement across sites.
Protecting construction workers from weather
While the obvious slips, trips and falls need to be mitigated, some countries around the world also need to consider protecting employees from the weather.
Working outdoors year-round requires companies to protect workers from inclement or overly warm weather. Public Citizen, a non-profit consumer advocacy organization in the US, reported that 130 million workers, including those in construction, lack protection from heat injury and illness.
The Biden administration announced at the end of last year that they would create a standard to protect workers from heat as climate change continues to be a growing threat to public health. The Occupational Safety and Health Administration (OSHA) is implementing an enforcement initiative on heat-related hazards and have developed a National Emphasis Program on heat inspections.
Elsewhere, a vast number of migrant workers moved to Qatar to help build the numerous infrastructure projects that were necessary for the FIFA World Cup. However, harsh work conditions have posed a huge risk and caused an unquantifiable number of deaths.
Amnesty International stated in their Reality Check 2021: A Year to the World Cup report that available evidence shows that Qatar’s extreme climate could play a role in a substantial number of deaths, particularly in light of the absence of adequate mitigating measures.
As the 2022 World Cup approaches, it has been made clear that enhanced protections from heat stress-related health hazards have not been instated.
The Business and Human Rights Resource Centre has been tracking work-related abuses in Qatar since 2016. Their research found that construction workers were the most frequently affected in recorded cases, with the construction sector notably having represented two in five cases across Qatar.
Technology in health and safety
Technological advancement in health and safety management appears to be growing and could be a key solution when it comes to minimising illness and injury on-site.
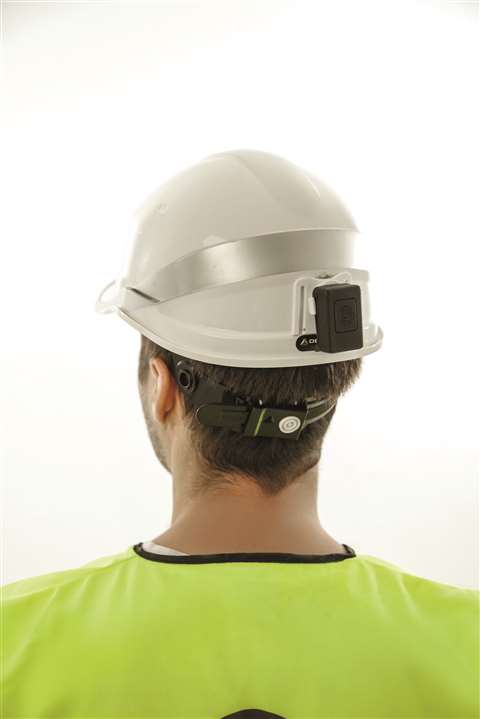
Soter Analytics, an occupational health and ergonomics technology company, has produced a wearable device that is driven by an AI training programme that coaches workers to self-correct their movements in real-time – preventing back and shoulder ergonomic injuries by up to 55%, says the multi-national company.
The International Labour Organisation estimates that 30% of construction workers in some countries suffer from back pain or other musculoskeletal disorders.
Heather Chapman, chief ergonomist at Soter Analytics, says, “Construction presents many safety challenges and, in terms of ergonomics, the tasks can be ever-changing. A person can be faced with a new set of ergonomic risk factors on any given day.
“The wearables are a scalable way to coach workers into better body mechanics regardless of the task. The real-time biofeedback from the device assists with internal learning changing motor neural pathways to permanently adopt improved postures,” Chapman adds.
Using science to improve safety
Tended, a deep-tech startup company that develops solutions to transform occupational safety, has also turned to behavioural science in order to develop its new platform.
Tended’s CEO and founder, Leo Scott Smith, said, “By using behavioural science techniques, our new Safety Culture solution enables companies to uncover and understand the underlying influences of unsafe actions and provides the resources to help them make safety culture improvements that drive safe behaviours.
“Ultimately, promoting a safer workplace and positive employee experience.”
Using the platform, organisations will be able to unlock insights into their safety culture, enabling them to identify areas for improvement, make sustainable changes and create a safer employee experience.
The solution works by gathering anonymous employee feedback using science-backed surveys to provide insights into the true perceptions and influences behind unsafe behaviours.
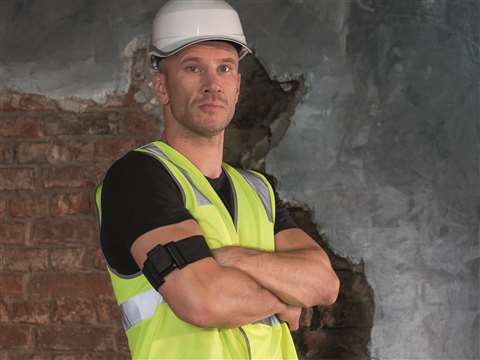
This data is then measured against a 30-point maturity matrix to provide clear insights into the perceptions and influences behind unsafe behaviours, in turn providing targeted safety recommendations and improvements.
Data management platforms are likely to grow in popularity over time as companies readdress their health and safety measures. Technological advancements give the industry plenty of choice – wearable technology offers an alternative solution to prevent physical injury and behavioural science-backed solutions dive into why incidents occur. The industry has never had more tools at its disposal to enable it to be safer for those that work in it.
STAY CONNECTED

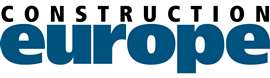
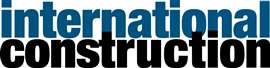
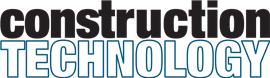
Receive the information you need when you need it through our world-leading magazines, newsletters and daily briefings.
CONNECT WITH THE TEAM
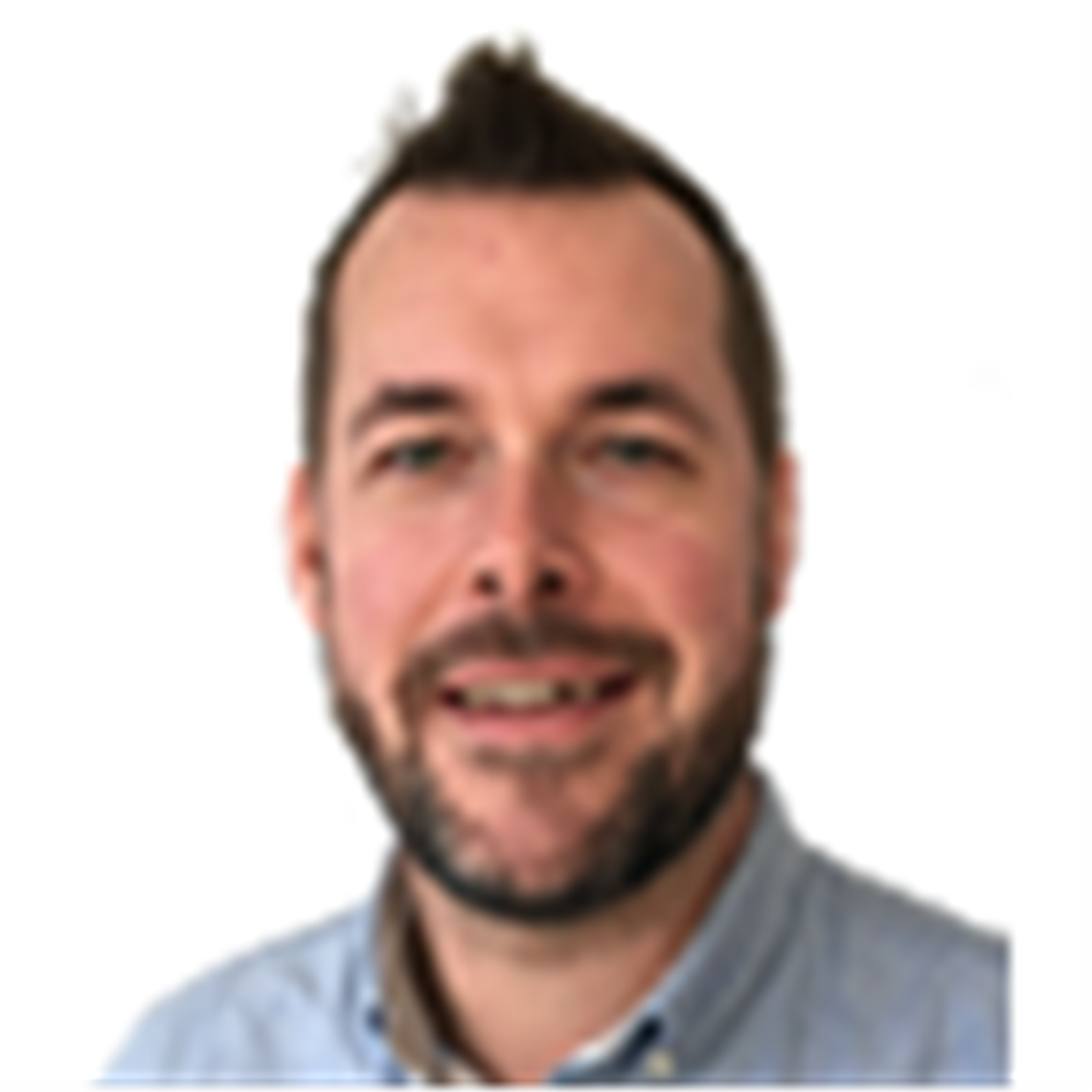
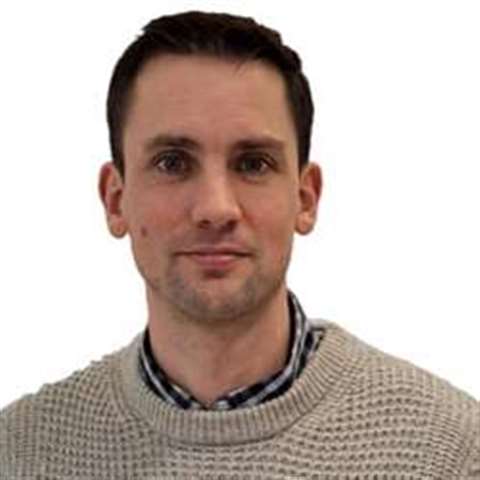
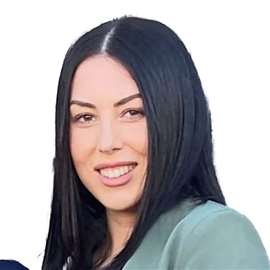
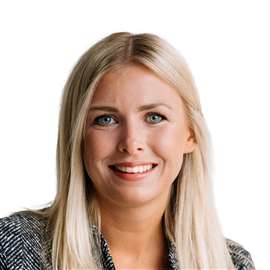