Read this article in French German Italian Portuguese Spanish
Could Züblin’s modular process using timber be a sustainability gamechanger?
02 September 2024
German-based Züblin, a building construction and civil engineering subsidiary of Austrian firm Strabag, said it’s developing a modular build method using cross-laminated timber (CLT) with support from the German Federal Ministry of Food and Agriculture. Could it be key to a sustainable built future?
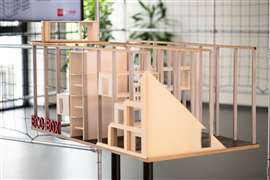
Called the ‘Eco-Box’, Züblin’s timber modular construction system is under development in collaboration with the University of Applied Sciences in Stuttgart, Germany.
In July, the company announced funding from the German government worth €718,000 (US$784,042) to help continue research and development.
The process applies a conventional modular approach while using traditional CLT. Züblin told Construction Briefing, “The Timber construction system will be developed with the aim of combining a modular design with a decoupled, primary load-bearing system and was submitted to the ‘Renewable raw materials’ funding program for further research.”
The company said the programme, through the Ministry of Food and Agriculture’s Agency for Renewable Resources, will run for 36 months in total, which includes the construction of a demonstration unit using Eco-Box methods and materials.
“The demonstrator will be used to research and implement information on prefabrication and logistics, BIM, building physics investigations and sustainable building service technologies in a total of five work packages,” said Züblin.
Ultimately, the developing method is meant to deliver a new product while analysing sustainability gains, said the firm.
“[Eco-Box] should allow for architectural diversity and variability, taking into account the location factors as well as the building’s internal structure.
“In addition, sustainability aspects are taken into account in the use of materials and in the construction process,” said Züblin.
What’s sets Züblin’s Eco-Box apart from other modular methods?
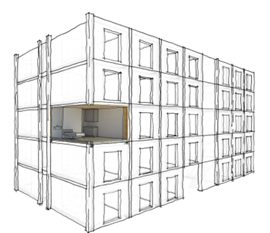
“Our Timber construction system differs from other methods in that the prefabricated modules are not stacked on top of each other; as is usual in modular construction,” Züblin explained to Construction Briefing.
“The innovation of the Eco-Box based on the modular principle consists in the separation of the modular system into a primary and a secondary supporting structure.”
In other words, the CLT modular units are placed and fixed to a primary supporting structure as opposed to the units, themselves, serving as primary supports.
“This construction method means that special uses [like] double storeys, loggias, etc. can be realised easily and cost-effectively,” Züblin said.
The company added, “The primary supporting structure forms a frame of reinforced concrete, [along with] the secondary supporting structure (the so-called ‘Eco-Boxes’).
“These are not stacked on top of each other but pushed into a stiffened shelving system like drawers. The boxes can be used individually for small apartments or combined for larger residential or office units.”
The boxes, themselves, aren’t entirely made from timber, either. Reinforced concrete floors accompany the CLT wall and ceiling elements.
Is Züblin’s Eco-Box process more sustainable?
The Eco-Box is still firmly in the prototype phase, however, Züblin said that it has seen early positive returns on sustainability goals, particularly the reduced time and materials needed to produce an Eco-Box project.
For now, and as the process progresses, the development team is working out holistic solutions for high-level problems.
“We see the development of optimal, recyclable design solutions in combination with a recyclable overall process, from production and construction to operation and dismantling, as the greatest challenges,” said Züblin, adding “issues relating to noise and moisture protection and the use of sustainable building technology systems are the top priority.”
The company also revealed that demand, too, is a current hinderance, “due to the almost complete standstill of the residential construction market.”
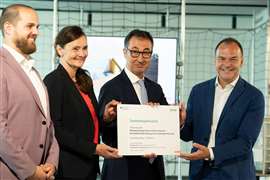
But if builders can get back to building, the company believes Eco-Box can help deliver Germany’s nationwide sustainability goals (it aims to make the country’s building stock carbon-neutral by 2050).
“When using wood, a very high degree of prefabrication can be achieved with great manufacturing accuracy. In addition, the transport weights are still easy to handle,” said Züblin. “Furthermore, once the research work has been completed, the system should be recyclable, [and] the materials should be almost completely recyclable by type.”
So Eco-Box may not yet be the modular method to disrupt the German built environment, but Züblin’s early research suggests the process could be beneficial, particular to regions short on residential home builds and the materials needed to produce cement and concrete.
Züblin board member Markus Landgraf added, “Due to the great influence of the construction industry on global energy and resource consumption, it is essential to align our actions with the sustainability strategy when planning, building, renovating and operating buildings.”
STAY CONNECTED

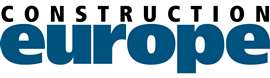
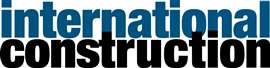
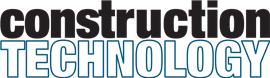
Receive the information you need when you need it through our world-leading magazines, newsletters and daily briefings.
CONNECT WITH THE TEAM
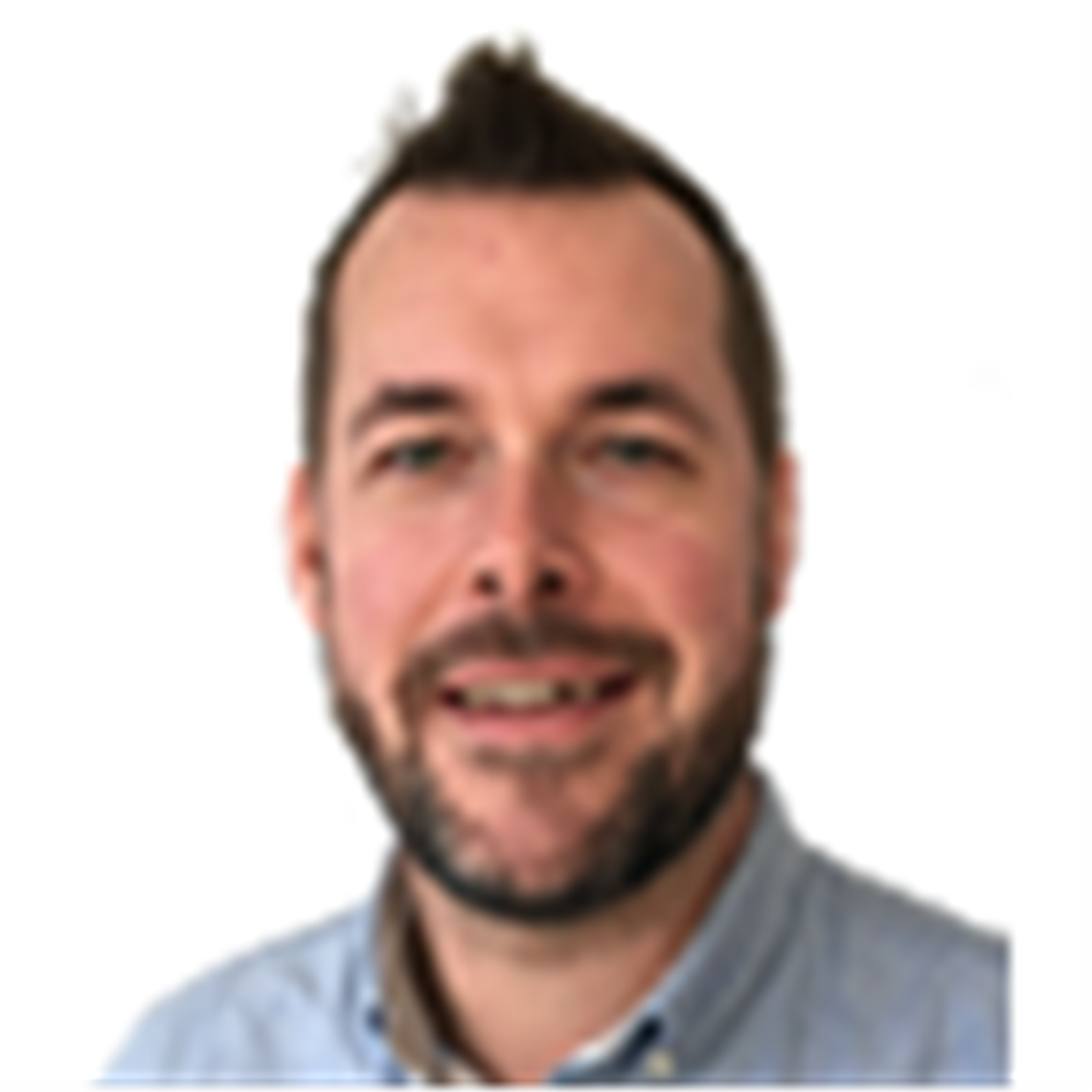
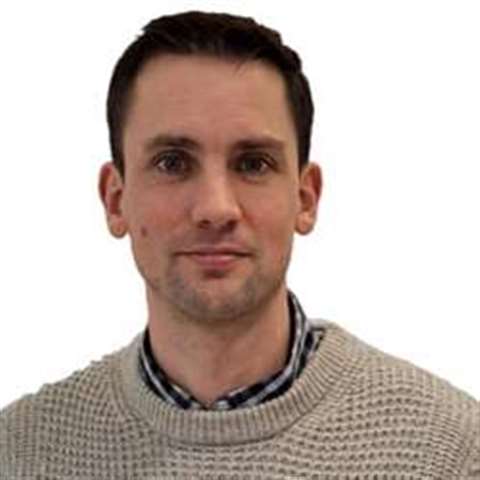
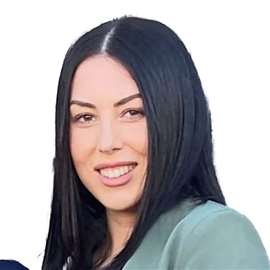
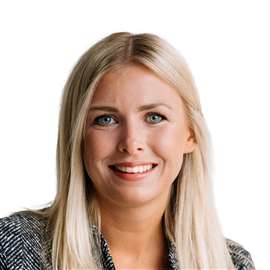