Read this article in French German Italian Portuguese Spanish
Concrete block: The company planning to capture carbon using ready mix
17 October 2024
Could concrete ever be used as a vehicle to capture and store carbon dioxide from the Earth’s atmosphere? That’s the idea proposed by Professor Sid Pourfalah, founder and chief executive of green tech start-up Concrete4Change. Lucy Barnard asks him how the world’s most polluting building materials, responsible 8% of global carbon emissions, could be turned into a carbon sink.
From his laboratory on a business park in the city of Nottingham, Professor Sid Pourfalah is just a short 15-minute drive from the spot where, until recently, the UK’s last remaining coal-fired power station churned out clouds of white steam from its eight distinctive cooling towers.
Visible for miles around, the power station at Ratcliffe-on-Soar, built in 1967, finally ceased operations on 30 September 2024, making the UK the world’s first major economy to phase out coal from national electricity generation.
But while the closure of Ratcliffe has been hailed as a victory for cleaner power in general, it spells problems for the country’s construction industry which had been relying on the fly ash it produced as a waste product to reduce the carbon footprint of the concrete it uses (see box).
“Concrete is the second most used substance on earth after water and the most widely used building material on earth,” says Pourfalah, the founder and chief executive of Concrete4Change, a green tech start-up aiming to decarbonize concrete. “Globally right now as a civilization we are consuming around three tonnes of concrete per person a year.”
“Globally, concrete is responsible for around 8% of carbon emissions each year,” he adds. “Most of that comes from the cement inside the concrete because it is inherent in the material. So, people have been taking waste from a different industry and replace some of the cement to try to reduce overall emissions.”
With no coal-fired power stations now operating in the UK, firms producing the prefabricated concrete blocks used in construction are having to take the unlikely - and carbon intensive – step of importing their fly ash all the way from China.
For contractors and builders under growing pressure to reduce their carbon emissions, a significant proportion of which come from the building materials they use, this matters. Using concrete which uses a significant proportion of fly ash can be classified as ‘low carbon’ and therefore reduces the tonnes carbon dioxide equivalent contractors need to tot up to calculate their scope 3 emissions.
Many major UK and European construction firms have already announced that they are using low-carbon concrete mixes in their projects. These include Swedish giant Skanska, UK-based contractor Laing O’Rourke, Austria-based Strabag and French giant Vinci.
What is low-carbon concrete?
Fly ash is all the grime left at the bottom of combustion chamber of a coal-fired power station. Throughout much of the industrial age it was one of the main components of smoke belching out of factories and causing black spots on washing hanging out to dry. But over the last 70 years, increasingly strict air quality regulations have required plant owners to filter their emissions and collect the ash and store it.
Since Roman times, builders have been adding ash and other things to the mix, either to make it stronger, easier to pour, or since the 1990s, to reduce costs and carbon emissions.
Today fly ash from coal-fired power stations is the most commonly used concrete additive (technically known as a supplementary cementitious material or SCM). It is typically less expensive than cement and, depending on what it is used for and where it is used, can replace up to 60% of the Portland cement in a mix (although 15% - 25% is most common).
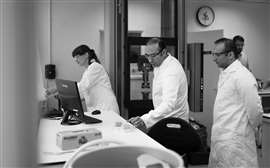
Researchers from the Universities of Lahore and Guayaquil found that by replacing 10%, 20% or 30% of traditional lime cement with fly ash lowered global warming potential by 9%, 19% and 29% respectively and increased the strength of the concrete.
But with other countries set to follow the UK’s lead and switch electricity generation to cleaner sources, the amount of fly ash available for concrete production is set to dwindle in many regions, making it harder to get hold of and more expensive.
The move is prompting a frantic search for suitable alternatives for fly ash to add into concrete mixes as manufacturers introduce other similar products such as blast furnace slag or silica fume from steel mills, chalk or shale.
It is also prompting a sudden flurry of new start-ups aiming to make the whole concrete-making process more sustainable.
“Unless we do something now, the cement industry, the concrete industry will never reach net zero by 2050,” says Pourfalah. “Even now it is a little late, but it is better than nothing.”
For Pourfalah, the big idea is to chemically engineer concrete which can be made to capture and store carbon dioxide – turning one of the world’s biggest carbon producers effectively into a carbon sink.
Although the actual process of making cement would still release carbon dioxide, the idea would be to capture that before it escapes into the atmosphere and use it as an additive to make concrete stronger.
“What most people don’t know about concrete is that it is actually one of the safest sinks for carbon dioxide in the world,” says Pourfalah. “Concrete by itself has the capacity potential to absorb 30% of its own weight in CO2. However, this won’t happen naturally. If you leave a concrete wall for 4,000 years, it is still not fully carbonated because of the barriers in nature. You need a specific temperature. You need a specific humidity. Exposure to the air cannot penetrate more than 40-50 millimeters inside.”
Pourfalah’s lab, dotted with centrifuges, gas cannisters and all manner of gauges and dials, scientists in white coats, goggles and green plastic gloves are busy carrying out tests and noting down findings.
Why does concrete naturally absorb carbon?
At the heart of his thinking is the basic chemistry that the calcium hydroxide in hydrated cement naturally absorbs CO2. If done properly, Pourfalah says, the carbon dioxide can be mineralised inside the concrete, making it stronger and permanently locking it away from the earth’s atmosphere.
“Our original questions were, is it possible to enable the concrete to absorb this CO2 uniformly?” he says. “And is it possible to reduce the carbonization time from say a thousand years to less than a hundred hours?”
Although other start-ups are attempting to come up with a similar solution by using CO2 gases from carbon capture and storage projects as an additive to mix directly with concrete, Pourfalah says he sees limitations with this approach and instead is working on manufacturing an additional substance which he calls a ‘carrier’ to store the CO2 before adding it into the mix. The carrier can then be used either alongside traditional SCMs or instead of them as a partial replacement for Portland cement.
“Concrete is a really hostile environment, usually pH 12 or 13. Even using the most advanced technology, what people are doing is taking CO2 in either its liquid or gas form and then mixing it up with concrete,” he says. “If you introduce too much CO2 in one go it drastically reduces the strength of the concrete. And obviously it doesn’t need a lot of chemistry knowledge to understand that in a few minutes the CO2 will either react or go back into the atmosphere and then we are wasting all those CO2 molecules. So, we lock the CO2 into a carrier and then introduce that to the concrete.”
Pourfalah says that the Concrfete4Change carrier would only comprise around 1% of the concrete mix, meaning that the concrete it produces looks and behaves in the same way as traditional mixes.
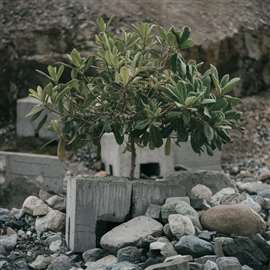
“When you think about concrete you think about a boring grey block that is like that for always. But when you start looking at it you find out that concrete is going through many different phases,” says Pourfalah.
“As the concrete goes from early hydration through 28 days of curing time there is a series of ions dissolving inside the water. They can work as a seed to form different crystals, and these crystals then change over time, so the environment is very dynamic. After a year, a lot of these crystals start dissolving and developing new crystals, so nothing is constant. And the results you get if you are releasing the CO2 inside the concrete after five hours is absolutely different from ten hours or 24 hours. The question is which one is better and that’s really hard to understand because nobody has looked at these processes in this amount of detail so it’s a mix of trial and error and gaining knowledge from across the board and building some new equipment to make a system that can show scientifically what happens when we release CO2 at different times.”
In January Concrete4Change completed a seed investment round of £2.5 million (US$3.3 million). The company’s investors currently include German pre-cast concrete manufacturer Goldbeck and Bangkok-based Siam Cement Group. The company says it needs another £20-£30 million (US$26-US$39 million) to set up a manufacturing line which it says should be up and running by the end of 2026.
And Concrete4Change is not the only company looking to find a way to net zero concrete. Over the past couple of years, a growing number of firms have been putting forward ideas for creating carbon zero concrete ranging from recycling cement paste from existing buildings to attempting to use algae and sea creatures to grow calcium carbonate to form cement.
“There has definitely been a culture change in the industry,” says Pourfalah. “A few years ago this really wasn’t seen as important. Now I can see that change is happening.
As well as a number of companies which inject CO2 into ready mix cement such as Novia Scotia-based CarbonCure which has been operating for the last decade, an increasing number of start-ups plan to capture carbon emissions and either bury them or use them as additives for concrete.
Carbon capture and storage
In Brevik, Norway, German building materials company Heidelberg Materials is currently constructing the cement industry’s first carbon capture and storage project in which carbon emissions from the manufacturing process will be captured at source, stored as a liquid and pumped 2.5 kilometers beneath the Norwegian seabed.
“Of course, all of these different technologies are complementary. We are not the only solution. We are part of a big eco system which can help the concrete and cement industry get to net zero,” says Pourfalah. “But I am not a big fan of schemes where CO2 is buried underground. It’s not a path to net zero because storing it like that creates unnecessary emissions and also we are creating a manmade volcano. If any leakage happens it has a very drastic effect and it must be monitored and maintained for perhaps a thousand years. Our product can take flue gas , improves the strength of the concrete and stores it away so it won’t come out even if it is crushed.”
Concrete facts:
Although people often use the terms ‘cement’ and ‘concrete’ interchangeably, they are in fact very different, with cement forming a vital ingredient of concrete (rather like flour in cake). Portland cement, made from limestone, is the glue that makes concrete strong. To make traditional concrete, builders mix about 10% of cement powder with around 15% water to make a paste which is then mixed with 75% sand and gravel.
However, making Portland cement is one of the most carbon intensive processes on earth. Limestone is heated in huge kilns to temperatures of up to 1,450 degrees Celsius – hotter than most lava – turning it from calcium carbonate into calcium oxide or lime. At the same time releasing carbon dioxide into the atmosphere. Making one kilogram of cement send out roughly one kilogram of CO2 into the atmosphere.
According to the World Economic Forum, the cement making industry alone is responsible for producing 1.6 billion metric tons of carbon dioxide. In fact, if the industry was a country, it would be ranked as the world’s third or fourth largest emitter of climate warming gasses.
One way to reduce concrete’s massive carbon footprint is to reduce its reliance on Portland cement. Concrete companies already use millions of tonnes of supplementary cementing material (SCM) to reduce concrete’s carbon footprint and to cost-effectively strengthen the material. Most SCMs are made from fly ash from coal-fired power stations or slag from steel blast furnaces. As coal plants and steel blast furnaces close, these materials are becoming harder to get hold of and more expensive.
STAY CONNECTED

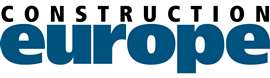
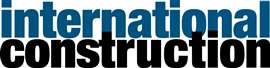
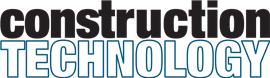
Receive the information you need when you need it through our world-leading magazines, newsletters and daily briefings.
CONNECT WITH THE TEAM
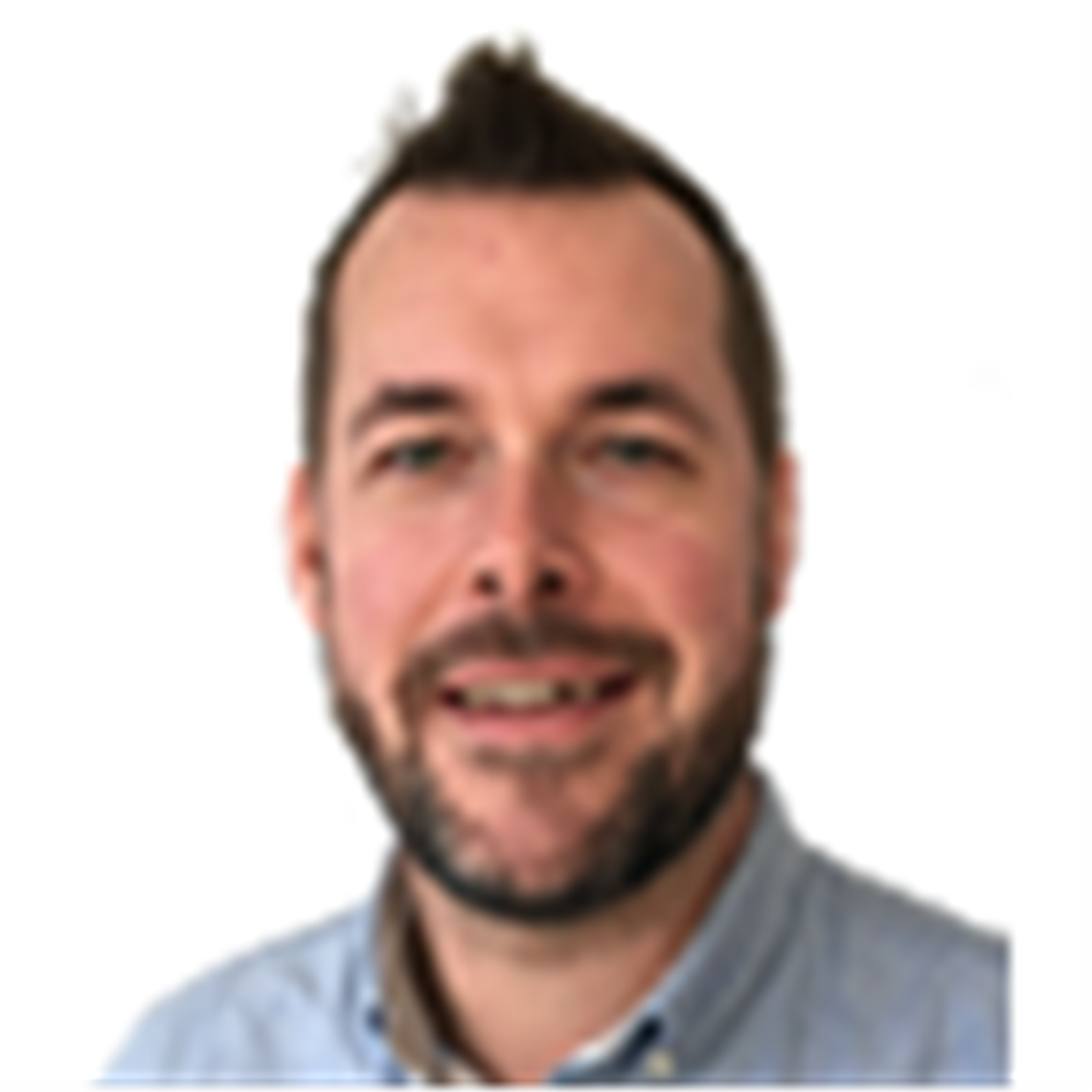
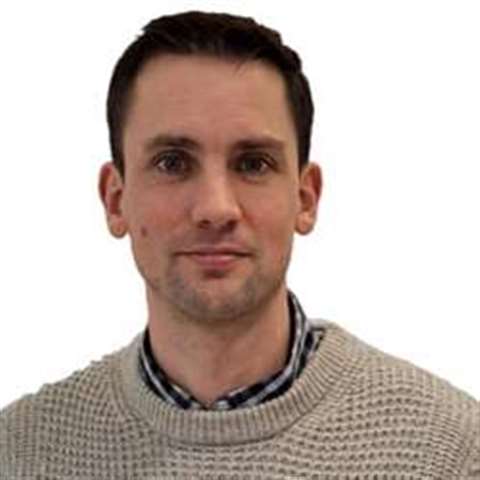
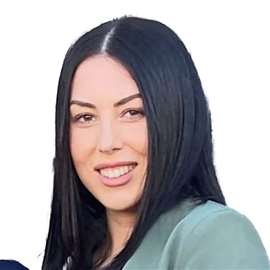
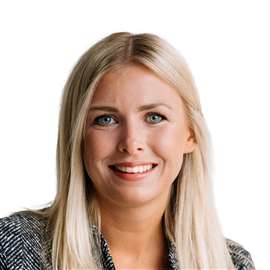