Automatisch von KI übersetzt, Original lesen
Betonblock: Das Unternehmen plant die Bindung von Kohlenstoff mithilfe von Fertigbeton
17 Oktober 2024
Könnte Beton jemals als Vehikel verwendet werden, um Kohlendioxid aus der Erdatmosphäre zu binden und zu speichern? Diese Idee schlägt Professor Sid Pourfalah vor, Gründer und Geschäftsführer des Greentech-Start-ups Concrete4Change. Lucy Barnard fragt ihn, wie man das umweltschädlichste Baumaterial der Welt, das für 8 % der globalen Kohlendioxidemissionen verantwortlich ist, in eine Kohlenstoffsenke verwandeln könnte.
Von seinem Labor in einem Gewerbegebiet in der Stadt Nottingham ist es für Professor Sid Pourfalah nur eine kurze 15-minütige Autofahrt zu der Stelle, wo bis vor kurzem das letzte verbliebene Kohlekraftwerk Großbritanniens aus seinen acht markanten Kühltürmen weiße Dampfwolken ausstieß.
Das kilometerweit sichtbare Kraftwerk in Ratcliffe-on-Soar wurde im Jahr 1967 erbaut und am 30. September 2024 endgültig eingestellt. Damit ist Großbritannien die erste große Volkswirtschaft weltweit, die aus der Kohlestromerzeugung aussteigt.
Doch während die Schließung von Ratcliffe allgemein als Sieg für eine sauberere Energieerzeugung gefeiert wird, bringt sie für die Bauwirtschaft des Landes Probleme mit sich. Denn bislang war sie auf die als Abfallprodukt anfallende Flugasche angewiesen, um den CO2-Fußabdruck des von ihr verwendeten Betons zu reduzieren (siehe Kasten).
„Beton ist nach Wasser der am zweithäufigsten verwendete Stoff auf der Erde und das am häufigsten verwendete Baumaterial der Welt“, sagt Pourfalah, Gründer und Geschäftsführer von Concrete4Change, einem Greentech-Start-up, das sich zum Ziel gesetzt hat, Beton zu dekarbonisieren. „Weltweit verbrauchen wir als Zivilisation derzeit rund drei Tonnen Beton pro Person und Jahr.“
„Weltweit ist Beton jedes Jahr für rund 8 % der CO2-Emissionen verantwortlich“, fügt er hinzu. „Der Großteil davon stammt aus dem Zement im Beton, da dieser inhärent im Material ist. Daher haben die Menschen versucht, einen Teil des Zements durch Abfälle aus einer anderen Industrie zu ersetzen, um die Gesamtemissionen zu reduzieren.“
Da derzeit in Großbritannien kein einziges Kohlekraftwerk in Betrieb ist, müssen die Hersteller vorgefertigter Betonblöcke für die Bauindustrie den unwahrscheinlichen – und CO2-intensiven – Schritt wagen und ihre Flugasche aus China importieren.
Für Bauunternehmer und Bauherren, die zunehmend unter Druck stehen, ihre Kohlenstoffemissionen zu reduzieren, von denen ein erheblicher Anteil aus den von ihnen verwendeten Baumaterialien stammt, ist dies von Bedeutung. Die Verwendung von Beton, der einen erheblichen Anteil Flugasche enthält, kann als „kohlenstoffarm“ eingestuft werden und reduziert daher die Tonnen Kohlendioxidäquivalent, die Bauunternehmer zur Berechnung ihrer Scope-3-Emissionen zusammenrechnen müssen.
Viele große britische und europäische Bauunternehmen haben bereits angekündigt, dass sie bei ihren Projekten kohlenstoffarme Betonmischungen verwenden. Dazu gehören der schwedische Bauriese Skanska, der britische Bauunternehmer Laing O'Rourke, die österreichische Strabag und der französische Bauriese Vinci.
Was ist kohlenstoffarmer Beton?
Flugasche ist der ganze Schmutz, der am Boden der Brennkammer eines Kohlekraftwerks zurückbleibt. Während des größten Teils des Industriezeitalters war sie eine der Hauptkomponenten des Rauchs, der aus den Fabriken aufstieg und schwarze Flecken auf zum Trocknen aufgehängter Wäsche verursachte. Doch in den letzten 70 Jahren haben immer strengere Luftqualitätsvorschriften die Kraftwerksbesitzer dazu verpflichtet, ihre Emissionen zu filtern und die Asche aufzufangen und zu lagern.
Schon seit der Römerzeit fügen Bauleute der Mischung Asche und andere Stoffe hinzu, entweder um sie stabiler zu machen oder sie leichter gießen zu können, oder – seit den 1990er-Jahren – um Kosten und CO2-Emissionen zu senken.
Heute ist Flugasche aus Kohlekraftwerken der am häufigsten verwendete Betonzusatzstoff (technisch bekannt als ergänzendes zementartiges Material oder SCM). Es ist in der Regel billiger als Zement und kann, je nach Verwendungszweck und Einsatzort, bis zu 60 % des Portlandzements in einer Mischung ersetzen (am häufigsten sind jedoch 15 % - 25 %).
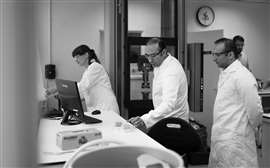
Forscher der Universitäten Lahore und Guayaquil fanden heraus, dass sich das Treibhausgaspotenzial um 9 %, 19 % bzw. 29 % senken ließ, wenn herkömmlicher Kalkzement durch Flugasche zu 10 %, 20 % bzw. 30 % ersetzt wurde. Gleichzeitig konnte die Festigkeit des Betons erhöht werden.
Doch da andere Länder dem Beispiel Großbritanniens folgen und bei der Stromerzeugung auf sauberere Quellen umsteigen, wird die für die Betonproduktion verfügbare Flugaschemenge in vielen Regionen abnehmen, was ihre Beschaffung erschwert und sie teurer macht.
Dieser Schritt löst eine fieberhafte Suche nach geeigneten Alternativen für Flugasche als Zusatz zu Betonmischungen aus, da die Hersteller andere ähnliche Produkte wie Hochofenschlacke oder Silica-Rauch aus Stahlwerken, Kreide oder Schiefer einführen.
Darüber hinaus führt dies zu einer plötzlichen Flut neuer Start-ups, die den gesamten Betonherstellungsprozess nachhaltiger gestalten wollen.
„Wenn wir jetzt nichts unternehmen, wird die Zement- und Betonindustrie bis 2050 nie die Netto-Null-Emissionen erreichen“, sagt Pourfalah. „Auch jetzt ist es zwar ein bisschen spät, aber es ist besser als nichts.“
Die große Idee besteht für Pourfalah darin, Beton chemisch so herzustellen, dass er Kohlendioxid abfangen und speichern kann – und so einen der weltweit größten Kohlenstoffproduzenten effektiv in eine Kohlenstoffsenke zu verwandeln.
Obwohl beim eigentlichen Herstellungsprozess von Zement immer noch Kohlendioxid freigesetzt wird, besteht die Idee darin, dieses aufzufangen, bevor es in die Atmosphäre entweicht, und es als Zusatzstoff zu verwenden, um Beton fester zu machen.
„Was die meisten Menschen nicht über Beton wissen, ist, dass er tatsächlich eine der sichersten Kohlendioxidsenken der Welt ist“, sagt Pourfalah. „Beton allein hat das Potenzial, 30 % seines Eigengewichts an CO2 zu absorbieren. Dies geschieht jedoch nicht auf natürliche Weise. Wenn Sie eine Betonwand 4.000 Jahre lang stehen lassen, ist sie aufgrund der natürlichen Barrieren immer noch nicht vollständig karbonisiert. Sie brauchen eine bestimmte Temperatur. Sie brauchen eine bestimmte Luftfeuchtigkeit. Die Luft kann nicht tiefer als 40 bis 50 Millimeter in das Innere eindringen.“
In Pourfalahs Labor, das mit Zentrifugen, Gasflaschen und Messgeräten und Zifferblättern aller Art übersät ist, sind Wissenschaftler in weißen Kitteln, Schutzbrillen und grünen Plastikhandschuhen damit beschäftigt, Tests durchzuführen und die Ergebnisse zu notieren.
Warum absorbiert Beton auf natürliche Weise Kohlenstoff?
Im Mittelpunkt seiner Überlegungen steht die chemische Grundidee, dass das Calciumhydroxid in hydratisiertem Zement auf natürliche Weise CO2 absorbiert. Bei richtiger Umsetzung, sagt Pourfalah, kann das Kohlendioxid im Beton mineralisiert werden, wodurch dieser stärker wird und dauerhaft von der Erdatmosphäre ferngehalten wird.
„Unsere ursprünglichen Fragen waren: Ist es möglich, den Beton so zu befähigen, dieses CO2 gleichmäßig aufzunehmen?“, sagt er. „Und ist es möglich, die Karbonisierungszeit von, sagen wir, tausend Jahren auf weniger als hundert Stunden zu reduzieren?“
Obwohl andere Start-ups versuchen, eine ähnliche Lösung zu finden, indem sie CO2-Gase aus Projekten zur Kohlenstoffabscheidung und -speicherung als Zusatzstoff verwenden, der direkt mit Beton vermischt wird, sieht Pourfalah bei diesem Ansatz Grenzen und arbeitet stattdessen an der Herstellung einer zusätzlichen Substanz, die er als „Träger“ bezeichnet, um das CO2 zu speichern, bevor es der Mischung hinzugefügt wird. Der Träger kann dann entweder neben herkömmlichen SCMs oder anstelle dieser als teilweiser Ersatz für Portlandzement verwendet werden.
„Beton ist eine sehr feindliche Umgebung, normalerweise liegt der pH-Wert bei 12 oder 13. Selbst mit der modernsten Technologie mischen die Leute CO2 in flüssiger oder gasförmiger Form mit Beton“, sagt er. „Wenn man zu viel CO2 auf einmal einführt, verringert sich die Festigkeit des Betons drastisch. Und man braucht natürlich keine großen chemischen Kenntnisse, um zu verstehen, dass das CO2 in wenigen Minuten entweder reagiert oder in die Atmosphäre zurückkehrt und wir dann all diese CO2-Moleküle verschwenden. Also binden wir das CO2 in einem Träger und führen es dann dem Beton zu.“
Pourfalah sagt, dass der Träger von Concrfete4Change nur etwa 1 % der Betonmischung ausmachen würde, was bedeutet, dass der damit produzierte Beton genauso aussieht und sich genauso verhält wie herkömmliche Mischungen.
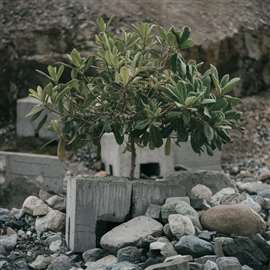
„Wenn man an Beton denkt, denkt man an einen langweiligen grauen Block, der immer so bleibt. Aber wenn man sich den Beton genauer ansieht, stellt man fest, dass er viele verschiedene Phasen durchläuft“, sagt Pourfalah.
„Während der Beton von der ersten Hydratation bis zur 28-tägigen Aushärtungszeit durchläuft, lösen sich eine Reihe von Ionen im Wasser auf. Sie können als Keime zur Bildung verschiedener Kristalle dienen, und diese Kristalle verändern sich dann im Laufe der Zeit, sodass die Umgebung sehr dynamisch ist. Nach einem Jahr beginnen sich viele dieser Kristalle aufzulösen und neue Kristalle zu entwickeln, es gibt also keine Konstante. Und die Ergebnisse, die man erhält, wenn man das CO2 nach fünf Stunden im Beton freisetzt, sind völlig anders als nach zehn oder 24 Stunden. Die Frage ist, was besser ist, und das ist wirklich schwer zu verstehen, da sich niemand diese Prozesse so detailliert angesehen hat. Es ist also eine Mischung aus Versuch und Irrtum und dem Sammeln von Erkenntnissen aus allen Bereichen sowie dem Bau neuer Geräte, um ein System zu schaffen, das wissenschaftlich zeigen kann, was passiert, wenn wir CO2 zu verschiedenen Zeiten freisetzen.“
Im Januar schloss Concrete4Change eine Seed-Investitionsrunde über 2,5 Millionen Pfund (3,3 Millionen US-Dollar) ab. Zu den Investoren des Unternehmens gehören derzeit der deutsche Betonfertigteilhersteller Goldbeck und die in Bangkok ansässige Siam Cement Group. Das Unternehmen benötigt nach eigenen Angaben weitere 20 bis 30 Millionen Pfund (26 bis 39 Millionen US-Dollar), um eine Produktionslinie aufzubauen, die bis Ende 2026 betriebsbereit sein soll.
Und Concrete4Change ist nicht das einzige Unternehmen, das nach einem Weg sucht, CO2-neutralen Beton herzustellen. In den letzten Jahren haben immer mehr Firmen Ideen zur Herstellung von CO2-neutralem Beton vorgelegt, die vom Recycling von Zementleim aus bestehenden Gebäuden bis hin zu Versuchen reichen, mithilfe von Algen und Meereslebewesen Kalziumkarbonat zur Herstellung von Zement zu züchten.
„Es hat definitiv einen Kulturwandel in der Branche gegeben“, sagt Pourfalah. „Vor ein paar Jahren wurde das wirklich nicht als wichtig angesehen. Jetzt sehe ich, dass sich etwas ändert.“
Zahlreiche Unternehmen wie CarbonCure aus Novia Scotia mischen Transportbeton mit CO2. Seit zehn Jahren ist das Unternehmen in Betrieb. Auch die Zahl der Start-ups, die CO2-Emissionen auffangen und entweder vergraben oder als Betonzusatzstoffe verwenden wollen, nimmt zu.
Kohlenstoffabscheidung und -speicherung
Im norwegischen Brevik errichtet der deutsche Baustoffkonzern Heidelberg Materials derzeit das erste Projekt zur Kohlenstoffabscheidung und -speicherung der Zementindustrie. Dabei werden die Kohlenstoffemissionen aus dem Herstellungsprozess an der Quelle aufgefangen, in flüssiger Form gespeichert und 2,5 Kilometer unter den norwegischen Meeresboden gepumpt.
„Natürlich ergänzen sich all diese verschiedenen Technologien. Wir sind nicht die einzige Lösung. Wir sind Teil eines großen Ökosystems, das der Beton- und Zementindustrie helfen kann, Netto-Null zu erreichen“, sagt Pourfalah. „Aber ich bin kein großer Fan von Systemen, bei denen CO2 unter der Erde vergraben wird. Das ist kein Weg zu Netto-Null, denn eine solche Speicherung erzeugt unnötige Emissionen und wir erschaffen außerdem einen künstlichen Vulkan. Wenn es zu einem Leck kommt, hat das sehr drastische Auswirkungen und muss möglicherweise tausend Jahre lang überwacht und gewartet werden. Unser Produkt kann Rauchgas aufnehmen, verbessert die Festigkeit des Betons und speichert es so, dass es nicht austritt, selbst wenn es zerkleinert wird.“
Konkrete Fakten:
Obwohl die Begriffe „Zement“ und „Beton“ oft synonym verwendet werden, handelt es sich tatsächlich um zwei sehr unterschiedliche Begriffe. Zement ist ein wesentlicher Bestandteil von Beton (ähnlich wie Mehl in Kuchen). Portlandzement aus Kalkstein ist der Klebstoff, der Beton seine Festigkeit verleiht. Um herkömmlichen Beton herzustellen, mischen Bauarbeiter etwa 10 % Zementpulver mit etwa 15 % Wasser zu einer Paste, die dann mit 75 % Sand und Kies vermischt wird.
Die Herstellung von Portlandzement ist jedoch einer der kohlenstoffintensivsten Prozesse der Welt. Kalkstein wird in riesigen Öfen auf Temperaturen von bis zu 1.450 Grad Celsius erhitzt – heißer als die meiste Lava – und verwandelt ihn von Kalziumkarbonat in Kalziumoxid oder Kalk. Gleichzeitig wird Kohlendioxid in die Atmosphäre freigesetzt. Bei der Herstellung von einem Kilogramm Zement wird etwa ein Kilogramm CO2 in die Atmosphäre freigesetzt.
Dem Weltwirtschaftsforum zufolge ist allein die Zementindustrie für die Produktion von 1,6 Milliarden Tonnen Kohlendioxid verantwortlich. Wäre die Branche ein Land, wäre sie tatsächlich der dritt- oder viertgrößte Emittent von klimaerwärmenden Gasen weltweit.
Eine Möglichkeit, den enormen CO2-Fußabdruck von Beton zu reduzieren, besteht darin, die Abhängigkeit von Portlandzement zu verringern. Betonunternehmen verwenden bereits Millionen Tonnen Zusatzzementmaterial (SCM), um den CO2-Fußabdruck von Beton zu reduzieren und das Material kostengünstig zu verstärken. Die meisten SCM werden aus Flugasche aus Kohlekraftwerken oder Schlacke aus Stahlhochöfen hergestellt. Mit der Schließung von Kohlekraftwerken und Stahlhochöfen werden diese Materialien immer schwieriger zu beschaffen und teurer.
Bleiben Sie verbunden

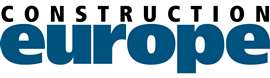
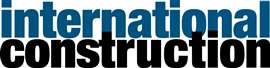
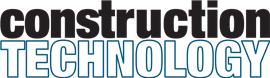
Erhalten Sie die Informationen, die Sie brauchen, genau dann, wenn Sie sie benötigen – durch unsere weltweit führenden Magazine, Newsletter und täglichen Briefings.
Mit dem Team verbinden
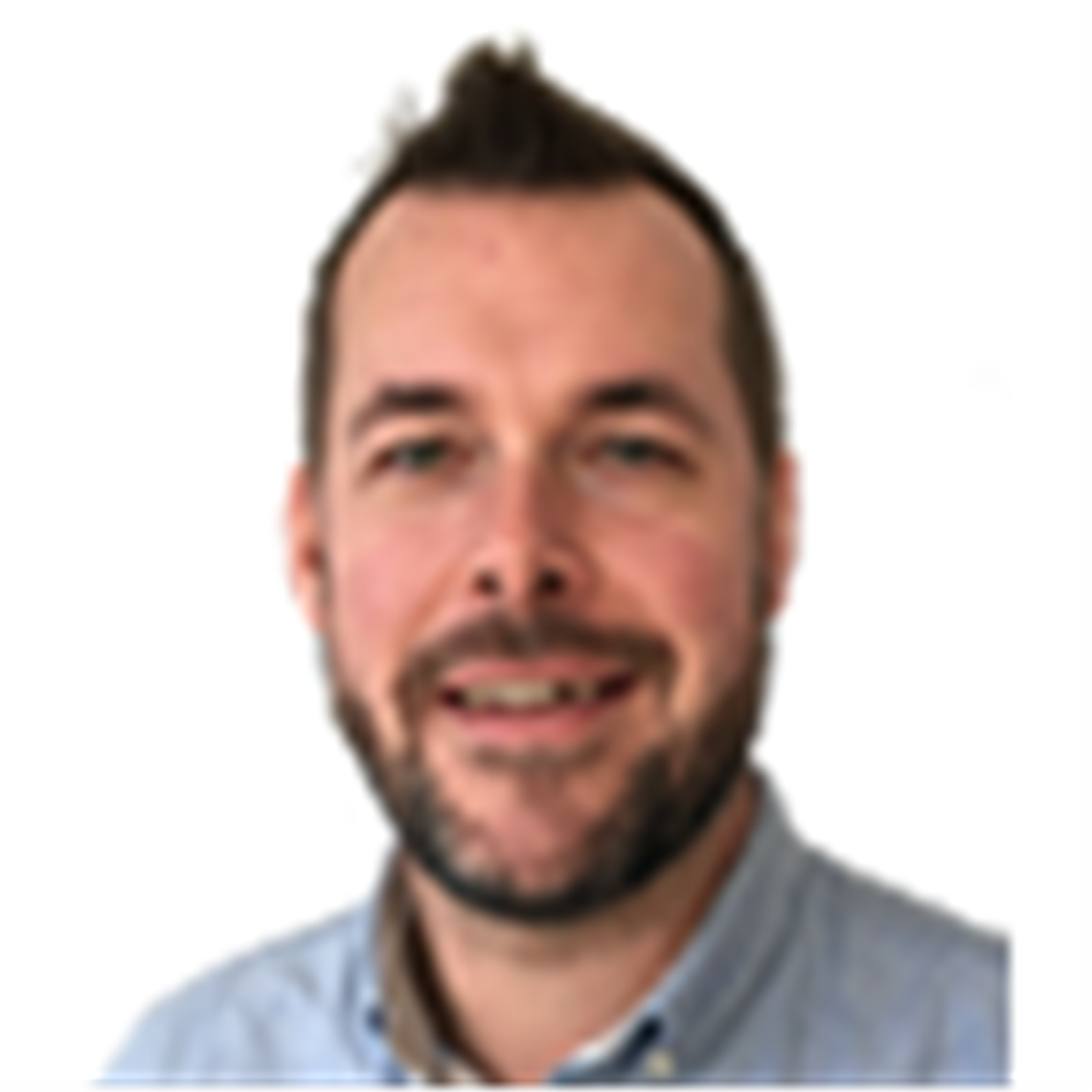
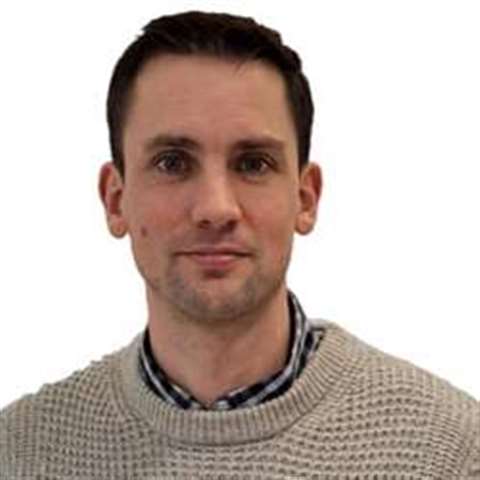
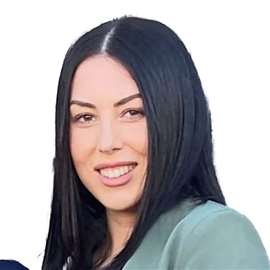
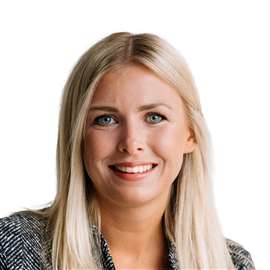