What concrete innovations are shaping the future?
12 March 2024
The most used manmade substance on the planet has evolved over millenniums, but the next decade of innovations will be key for the industry to meet its ambitious sustainability goals, Mitchell Keller reports.
“When people ask what I do… my go-to line is, ‘Have you seen The Flintstones?’” says Joel Galassini, executive VP of the commercial cement division for Cemex, a Mexico-based building materials company.
The Flintstones is a US cartoon from the 1960s set in a romanticised Stone Age.
His jokey response suggests the sector in which he works is old fashioned.
“I describe myself by a Stone Age cartoon, but we have so many people that are the Jetsons,” he adds.
The Jetsons were the main characters of another American animated comedy (simply called The Jetsons) from the ‘60s, which followed a family in an idealised setting of the future.
An evolving sector
Just over Galassini’s shoulder, while he tells this anecdote, is the South Lot of the Las Vegas Convention Center; packed to the edges with sophisticated construction equipment, technology, and state-of-the-art science on display for World of Concrete 2024.
It has taken time, the Cemex VP said, but he believes the concrete industry is making leaps and bounds into the future.
“We’re using AI in a lot of our operations, we’re running drones, and we’re looking at autonomous vehicles and all these things… I describe it as the Flintstones but, really, we got a lot of ‘Jetsonian’ things going on,” he said.
Low carbon solutions
Whether driven by in-company missions, governmental regulation or contract stipulation, the concrete industry has needed to make enormous strides, quickly, in creating more products from recycled materials with lower CO2 footprints.
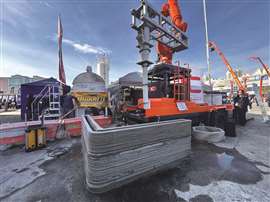
To meet consumer demand and comply with environmental stipulations, many companies reconfigured their cement-making process. Cement is a key ingredient in concrete but one of the world’s top carbon producers.
That has meant increased involvement from the science community, which globally has found lower-carbon solutions for cement mixtures, including researchers at Empa, the Swiss Federal Laboratories for Materials Science and Technology.
“The major innovations in cement and concrete products in the recent years have been driven by the need to improve the sustainability and reduce the emissions,” confirmed Dr Mateusz Wyrzykowski, Group Leader of Concrete Technology at the Concrete & Asphalt Laboratory at Empa.
Everything from graphene, hemp, coffee, and a host of new specialised synthetics and admixtures have been making their way into concrete and cement. The results and intent vary, but the experimentation is paramount to discovering breakthrough products that can help reduce emissions.
“Significant progress has been made thanks to reduction of waste and responsible use of resources,” adds Wyrzykowski.
One of the most intriguing materials for cement Empa has studied is ‘biochar.’ It’s a carbon-rich material created from pyrolysis of biomass; in other words, it’s the bioproduct of heating organic materials absent oxygen.
In theory, deriving from organic materials, concrete made with biochar cement could remove carbon from the atmosphere. At present, biochar has been used successfully as a form of insulation.
Some products are already on the market, but Empa suggests a stronger, safer version of a biochar additive will be forthcoming with additional research.
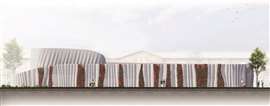
“Biochar is very porous. It absorbs a lot of water but also expensive admixtures used in concrete production,” explained Wyrzykowski. “It is difficult to handle and not completely harmless, either.”
According to Empa, the fine biochar dust is problematic for human respiratory tracts and carries a risk of explosion.
As such, investigation continues into seeing if the material can be processed into pellets.
“Such lightweight aggregates already exist from other materials such as expanded clay or fly ash,” said Wyrzykowski, noting some precedence. “The know how in handling these materials is available in industry, and this increases the chances that the concept will be put into practice.”
Reanalysing cement production
Back with Cemex, Galassini said his company has made products with less clinker than traditional cement and products with fly ash, both of which aid carbon emissions reduction.
But reanalysing the entire production of cement, he said, is as important to adjusting the chemical makeup of it.
“We burn different things in our kilns instead of coal,” he says. “We can burn recycled waste products. We can burn tyres, we can burn waste fuel, we can burn industrial and residential waste… We have some that we can take livestock, cow carcasses, and dispose of all of those in a responsible manner and use it to fuel the kilns.”
The system, he notes, is not entirely void of emissions, but they are highly reduced and help facilitate larger gains, including cost savings for the recycled fuel sources.
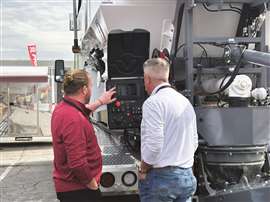
“Our cement plant in Berlin consumes 98% recycled product,” says Gassalini, noting the country moved away from landfill disposal in the mid-2000s. “We take all of that waste, pelletise it, and burn it in the kiln. So instead of putting it in a landfill and creating methane, which I believe is 30 times more potent than CO2, we can burn that waste, create cement, and create a product.”
This way-of-thinking is not isolated; most major global players have adopted aggressive approaches to reducing carbon output and increasing circularity.
Germany’s Heidelberg Materials Group launched a suite of lower-carbon products in 2023, and they plan to open a carbon-capture storage (CSS) facility at a cement plant in Norway by the end of 2024.
“Our CSS project at the Norwegian Brevik plant first started out as an ambitious idea during the mid-2000s,” said a spokesperson from Heidelberg.
“The initial thoughts matured into a desktop study. In December 2020, the Norwegian government gave final approval and support for the construction of the world’s first industrial-scale carbon capture facility at a cement plant.”
This project would remove carbon from the site to an undersea locker.
“Once operational, 400,000 tonnes of CO₂ per year are to be captured and transported by ship to an onshore terminal on the Norwegian west coast,” explained Heidelberg. “From there, the liquefied CO₂ will be transported by pipeline to the storage site under the North Sea, where it will be permanently stored.”
While capture and sequester methods for carbon are still imperfect, Heidelberg noted it’s only one lever of sustainable innovation.
“We continue to decarbonise our product portfolio through conventional carbon reduction measures,” stated the company. “For years, our teams have been working towards reducing the clinker content in our products, shifting the product portfolio, and increasing the share of alternative fuels.”
Machines aid innovation
While concrete and cement go through physical changes, the machinery mixing and pouring the substance must also keep up with the times.
Volumetric or mobile mixing trucks are not new, but advances in computer technology, material storage and data cataloguing have made the already valuable tools immensely so in the modern era.
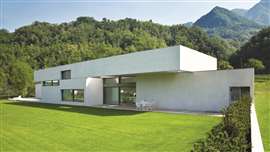
Cemen Tech calls itself the world’s largest manufacturer of volumetric proportioning and continuous concrete mixing solutions and has been in the volumetric mixing game since the beginning.
With all needed concrete materials stored and mixed on the truck and at the site, project managers tout savings on transportation, but the unit’s sophisticated technology also ensures waste is limited and the concrete outputting is meeting expectations for the job and climate.
Zach McQuay, who runs McQuay Construction in Oklahoma, US, uses a Cemen Tech C-Series, and notes the order a machine can bring to a job.
“You have complete control of it,” he says. “It’s a mobile batch plant, so we don’t have a drive time. We’re able to load all the material on site, and we’re running 440 yards (402m) a day with only three trucks.”
Compared to using a ready-mix batch plant off-site, McQuay estimated a similar job would require 20 or more trucks, plus the travel time and loading and unloading.
With a volumetric mixer, McQuay says, “We’re not making concrete until we hit ‘Start.’ We’re getting fresh concrete on demand.”
Air testing can happen on site, and the mixer can create small batches at a time, which McQuay says reduces waste.
“In the ready-mix world, if they fail that air test, that whole load is rejected,” he explained, noting volumetric mixers can simply make a new batch (and make adjustments to the mix in-between). “In the volumetric world, if we mess that air test up, we’re going to have less than a half a wheelbarrow to recycle.”
With sand, rock, water, chemicals, and synthetics needed to produce concrete on the truck, a computer interface allows users to manage the exact makeup of their mix and adjust it as needed.
“We have a live water/cement ratio. We have a live dosage rate of our chemicals. We have a live rating of our sand, rock and water, so we’re able to dial in any of those aspects anytime during the project,” added McQuay.
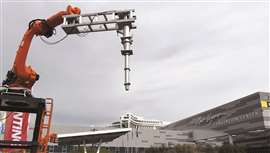
Logging data creates a network of reliable information that pavers or layers could recall for similar jobs or in comparable environments.
Elsewhere, advancements in AI, 3D scanning and printing, and sensor technology have greatly aided pavers and other concrete-focused machines. A slipform paver from the German-based Wirtgen Group offers an example.
“When paving concrete with Wirtgen slipform pavers, various automatic functions can be used, such as the AutoPilot 2.0 system or the automated dowel bar inserter,” said the company. “The AutoPilot 3D control system developed by Wirtgen is used for precise, stringless control of slipform pavers when creating all kinds of offset and inset profiles.
“The creation of a geodetic data model by a surveyor is no longer necessary. The installation and removal of a stringline, as is usual with a conventional machine control system, is obsolete.
“The machine moves along a virtual stringline with satellite positioning guidance. Both the height adjustment and the steering of the machine are automatically controlled.”
3D printing and concrete
One of the most tantalizing and visually stimulating automation advances in concrete is 3D printing.
Layered extrusion 3D printing machines, which use a controlled nozzle that accurately squeezes out a cementitious paste layer by layer, were some of the most popular demonstrations at World of Concrete.
The ‘toothpaste-like’ piles of concrete can be built as high as the printer or environment allows, with some printers large enough to print entire buildings.
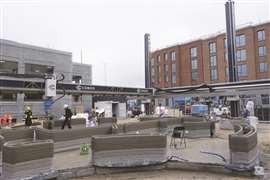
A COBOD International 3D printer, a Denmark-based product, completed what is said to be Europe’s largest 3D-printed building last year in Heidelberg, Germany. The building is 54m long, 11m wide and 9m high.
The COBOD BOD2 3D printer can create non-square geometric forms in addition to boxed structures. Construction started mid 2023 and it took approximately 172 hours.
“We expect the printers to last up to five years or ten years,” says Philip Lund-Nielsen, co-founder of COBOD, noting longevity with the machines are increasing. “It’s 90% galvanized steel. Most of the issues our customers have on-site is getting materials right; once they master that, they become really efficient.”
Putting it all together
Much like concrete is a product made of particular elements working in tandem, the industry’s leaders will need to continue to work collaboratively to move the product forward.
“It’s really working with owners, architects, engineers, to ensure that we’re designing a piece of building or sidewalk or pavement properly and not over designing it,” says Galassini. “You look at concrete that’s poured in most sidewalks in a city; it is a recipe that is specified by the city.
“That recipe will create a sidewalk that has, let’s say, 6,000 to 8,000 PSI of strength, which would be similar to an airport runway. So I can land a 747 on a sidewalk that only needs 2,500 PSI of strength.”
With all this information and available technology to tackle this example of over-engineering, Galassini thinks it’s time to find long-term solutions.
And those who don’t modernise and help solve the problem may get left behind.
“I have a belief,” says Galassini, “that the people who are continuing to innovate and push will most likely be winners. At some point, the people who resist change, they’re going to be at a tipping point where all of a sudden, they don’t have any other choices, or maybe they’re too late.”
|
STAY CONNECTED

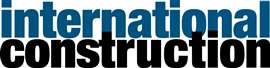
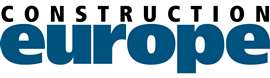
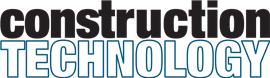
Receive the information you need when you need it through our world-leading magazines, newsletters and daily briefings.
CONNECT WITH THE TEAM
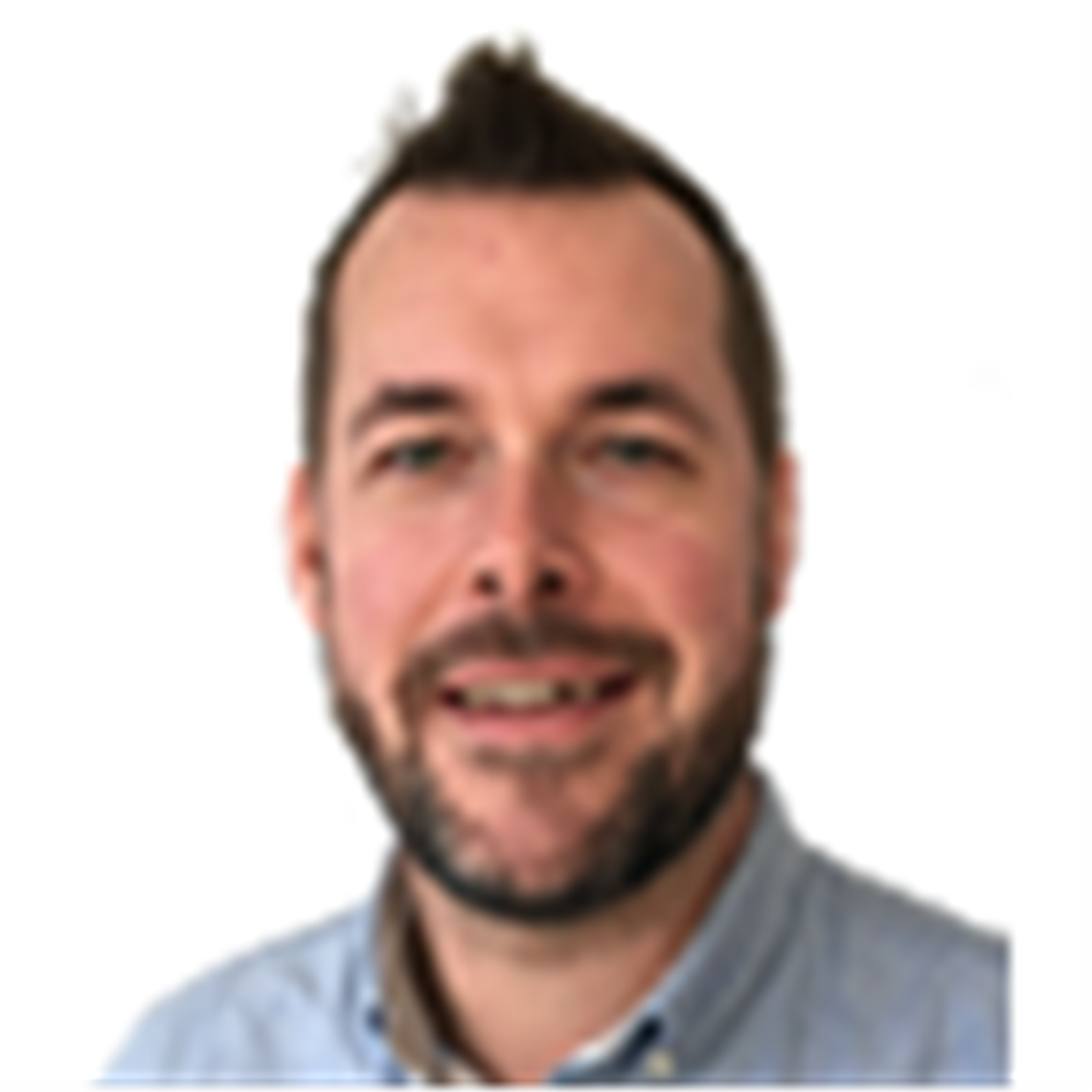
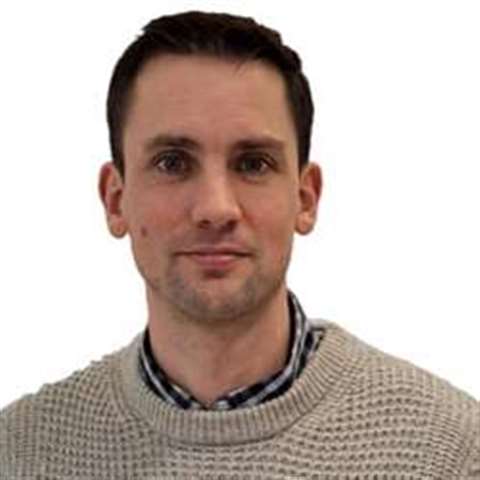
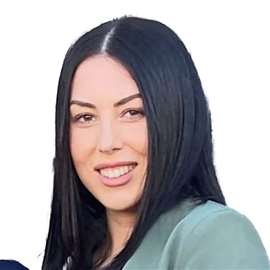
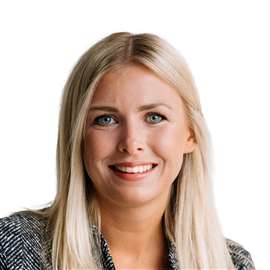