What can construction learn from Japan?
11 April 2023
Robin Vos, Director of Solutions Architects, Trackunit, on how construction industries around the world can improve their safety records by looking at Japan
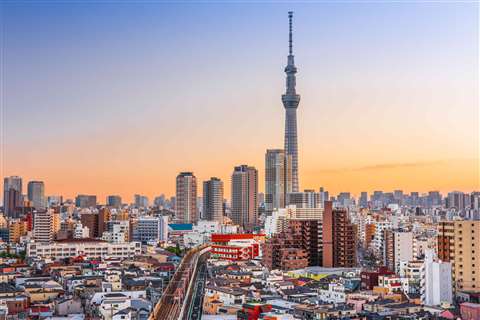
Japan’s approach to safety and quality in construction goes to lengths that Europe and North America do not come close to. There is much most of us can learn from this, but there are drawbacks too.
Japan has a near obsession with safety. We might like to think in Scandinavia, Western Europe, and North America that we are similarly vexed but the truth is that we come nowhere near.
Visit any construction site in Japan and it is a remarkable experience even for the most seasoned construction professional. Sites are full of health-and-safety professionals, some holding flags, others directing traffic and still others checking this and that ensuring no literal or figurative red lines are crossed, all in the interests of minimising the risk of injury to workers.
In real terms, that translates. In 2012, 2013 and 2014 respectively, fatalities in the Japanese construction industry numbered 367, 342, and 377 respectively. In the three years 2019-21, those numbers were 269, 258 and 288 respectively. While Japanese trends have clearly improved, they have flatlined in US construction where 1,008 fatalities occurred in 2020, according to the Occupational Safety and Health Administration. Deaths in construction in the US have remained at around 10 in every 10,000 for the decade 2011-20.
Construction health and safety
Nobody is doubting the efforts to ensure safety in the US or indeed other parts of the world, but the mindset in Japan is different. As an outsider, it seems they are personally affronted by bad numbers, disorder, and anomaly, and will do everything in their power to rectify it. It means generally going above and beyond regulation. It also means a lot of checking and ticking off, much of it manual.
While these checks and processes can be frustrating to outsiders, it’s difficult to knock it, given the numbers. But it’s also where an opportunity for telemetry exists and which can plug a gap that takes some of the manual work out of the process and allow human resource to be freed up elsewhere.
That in itself presents problems though. The typical testing process in Japan can be anything up to 12 months; for businesses that aspire to be fast and agile, this is a hurdle. But there’s no getting around it. The way of working and the culture is so embedded in Japanese business that any attempt to accelerate the process will most likely be met with a flat ‘no’ and a reversion to the way of doing things that has served them so well.
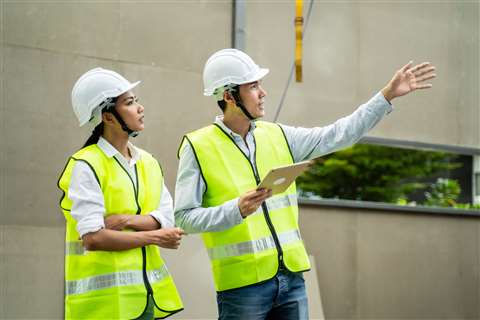
Exactly the same arguments apply to quality standards too. And it’s here that many of the big Japanese manufacturers like Hitachi, Sumitomo and Komatsu are very focused on finding telematics solutions that fit with their strategy and big-budget R&D teams. It is here that the chance to get in on a market that numbers 137 million people and still ranks as the third biggest economy in the world continues to be a big draw to foreign companies despite the difficulties in penetrating the local market.
Part of the reason for that is Japan’s ageing population crisis which will place an ever increasing strain on the economy to make sure their needs are catered for. Japan’s over 75s already account for more than 15% of the population and, on current trajectories, that could more than double by 2040.
That places an enormous premium on technology that can make a difference in all areas of the economy. It is why data-rich telematics providers are all-in on the Japanese market because they meet the quality bar to help manage the age issue.
Japan has stringent 2050 carbon reduction targets with one eye on the health benefits that would spin out from such a development and the increasing reliability of telematics data on CO2 emissions and, more importantly, how to mitigate emissions is just one area where that could help. Fuel management systems, more effective usage of machines, better resource allocation and better all-round efficiency with an emphasis on eliminating downtime in the construction industry would obviously fall into line with Japan’s goals too.
It should never be forgotten that Japan sits in a natural disaster zone that make it vulnerable to earthquakes, tsunamis and other natural phenomena that, as one example shows, led to the Fukushima disaster in 2011 that cost an estimated 18,500 lives.
Construction disaster management
Indeed, disaster management and crisis management really are a thing in Japan. And it partly explains the extreme levels they go to.
We will all have watched with some horror events unfold in Turkey and North Syria where the death toll on the back of a 7.8 Richter Scale earthquake stood at over 57,000 at the time of writing. In November 2014, Japan suffered a lesser but by no means insignificant quake near the city of Nagano measuring 6.7.
There were no deaths and, it has been reported anecdotally, locals continued with their daily business largely unruffled; almost certainly down to stringent quality standards in local construction. By way of direct comparison, a similar scale earthquake in south Italy in 1980 measuring 6.9 cost 3,000 lives.
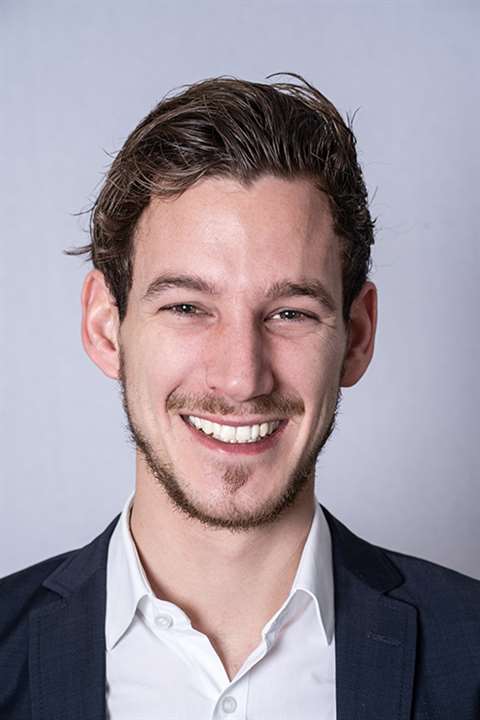
Japanese OEMs, in fact, have special protocols in place stipulating the immediate release of their machines in the event of a catastrophe as part of systematic disaster management programs. This is not to make light of the efforts or preparedness of other countries in the face of such tragedy, but it merely illustrates just how ready Japan is on every level to handle crisis both in terms of prevention and aftermath.
In a world where we’re still trying to understand what climate change, rising sea levels and natural disasters will do to the way we live – witness the floods in Germany, the forest fires in Australia and California and other natural disasters – this might in time be where we have most to learn from Japan.
Author: Robin Vos, Director of Solutions Architects at Trackunit.
STAY CONNECTED

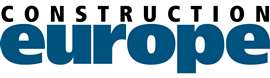
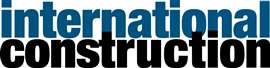
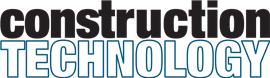
Receive the information you need when you need it through our world-leading magazines, newsletters and daily briefings.
CONNECT WITH THE TEAM
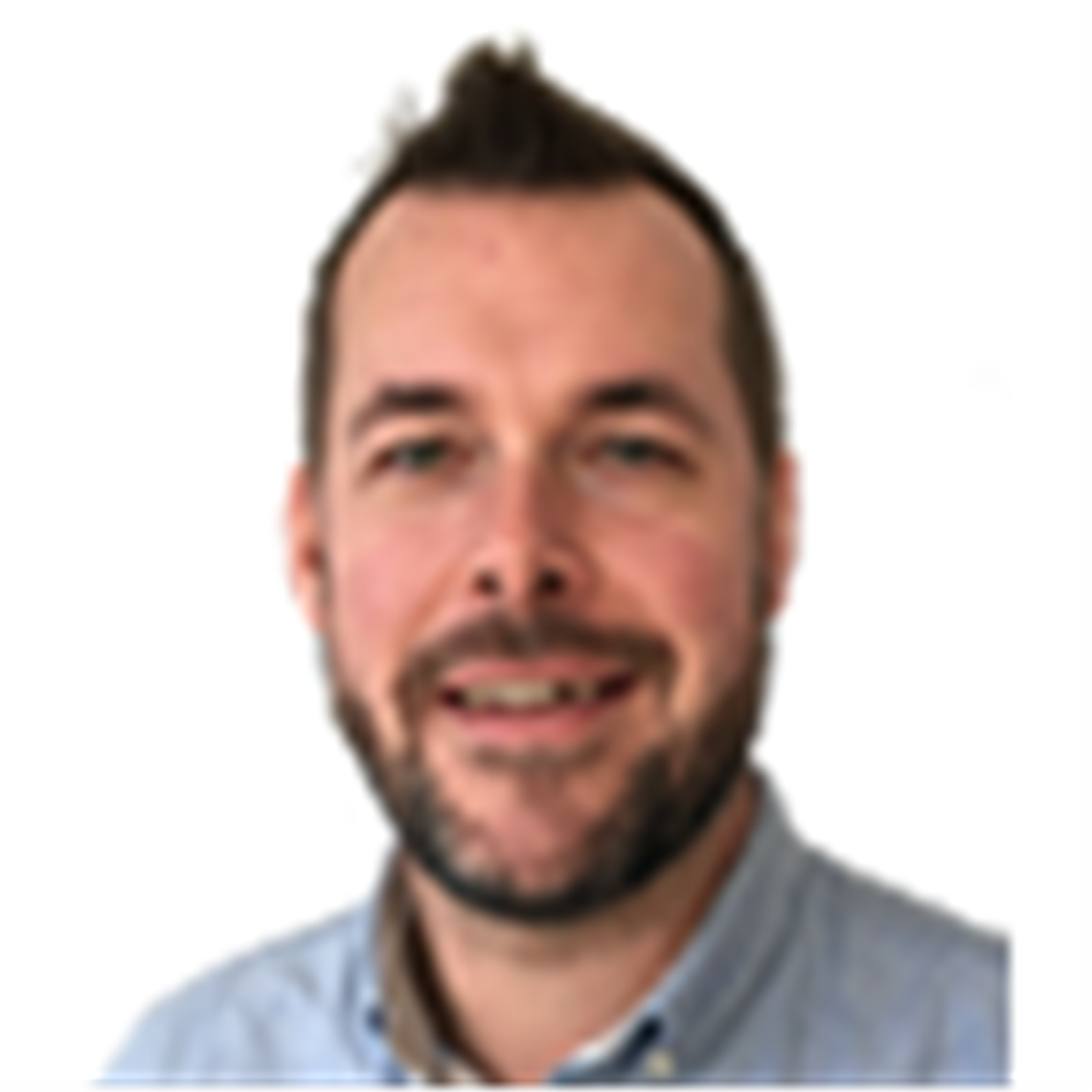
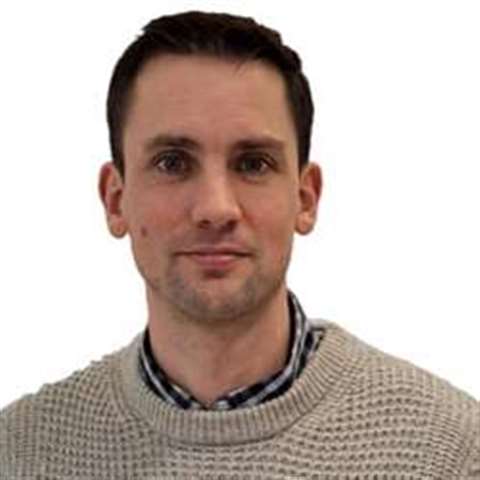
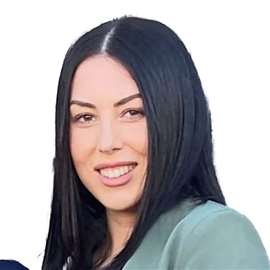
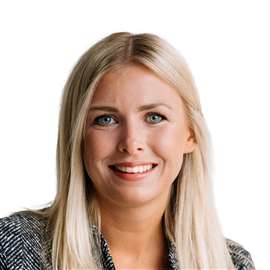