What are the stages of autonomy?
12 December 2022
Automation in construction is designed to produce higher production rates, improve project delivery times, as well as create better health and safety measures. A degree of automation – also known as machine control – has been in use in construction for decades.
Autonomous vehicles are operated by means of LiDAR sensors detecting obstacles in the surroundings, inertial measurement units (IMUs), and global positioning system (GPS) technology. This technology allows the vehicles to know their exact position on site, and a geofence is often used to prohibit the vehicles from operating off-site. A number of equipment manufacturers are including automation in the design of their vehicles, whilst construction technology companies are developing ways to enhance current fleets.
Definitions of autonomy
Level 0 Autonomy - No Automation
The human completely controls the equipment, be it a wheeled loader or an excavator. The human steers, brakes, and accelerates.
Level 1 Autonomy - Driver Assistance

Under certain conditions, the machine controls either the steering or the vehicle speed, but not both simultaneously. At the same time, the operator performs all other aspects of driving and has full responsibility for monitoring the surrounding area and taking over if the assistance system fails to act appropriately.
Liebherr says that its new assistance systems for XPower large wheeled loaders increase comfort and safety in daily operation in a range of ways. The company says that one of its advantages is that they enable machine operators to concentrate more on operating their Liebherr wheel loader by removing additional distractions.
Level 2 Autonomy - Partial Automation
At this level, the machine can steer, accelerate and brake in certain circumstances. The operator will still need to perform tactical manoeuvres such as scanning for hazards.
Level 3 Autonomy - Conditional Automation
The machine can manage most aspects of driving, including monitoring the environment. The system will request the operator to intervene when it encounters a scenario it can’t navigate, meaning the driver must still pay attention and be ready to take over at any time.
Level 4 Autonomy - High Automation
No human input or oversight is required except under select conditions defined by factors such as road type or geographic area (like poor weather or other unusual environments).
High automation allows companies to enhance safety in hazardous work environments, such as in the mining or quarrying industries, whilst also increasing productivity. Cat Command technologies by Caterpillar allow operators to use remote solutions, via onboard electronic and vision systems, to allow machines to be controlled without anyone in the cab.
Level 5 Autonomy - Full Automation
The machine can operate on any road and in any conditions a human driver could negotiate. The system is navigated via an app or online system that will tell the machine what it should be doing. This level of automation is considered to be a long way off for construction.
In an interview with International Construction magazine, Trackunit CEO, Soeren Brogaard, said, “We are very far away from autonomous systems where AI can ultimately augment a human being… clearly, AI is coming. AI is an element that we all have to be part of. I think you’ll see it on expensive machines where each little component just starts getting more and more utility, so you cannot misuse it, or it cannot be of danger. But doing it at large construction sites with multiple systems; I wish it would happen in our lifetime, but I doubt it.”

To drive the development of autonomous transport solutions across the company, at the beginning of 2020, Volvo Group established the Volvo Autonomous Solutions business unit.
“Our approach is to start in a narrowly defined environment and build on the successes achieved there over time,” says Perjohan Rosdahl, Head of Off-Road at Volvo Autonomous Solutions. Rosdahl adds, “A perfect place for this is in quarries, which have clearly defined loading and unloading locations over generally short distances.”
The company’s autonomous and electrically powered load carrier TA15 uses GPS, lidar, radar and multiple sensors. Since the innovative vehicle does not require a driver, it comes without a cabin, enabling a completely new machine profile. According to Rosdahl, the next step could be the use of autonomous Volvo construction machines in underground mining and tunnels.
STAY CONNECTED

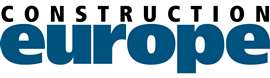
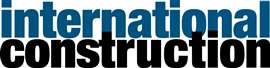
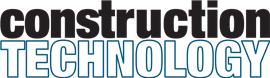
Receive the information you need when you need it through our world-leading magazines, newsletters and daily briefings.
CONNECT WITH THE TEAM
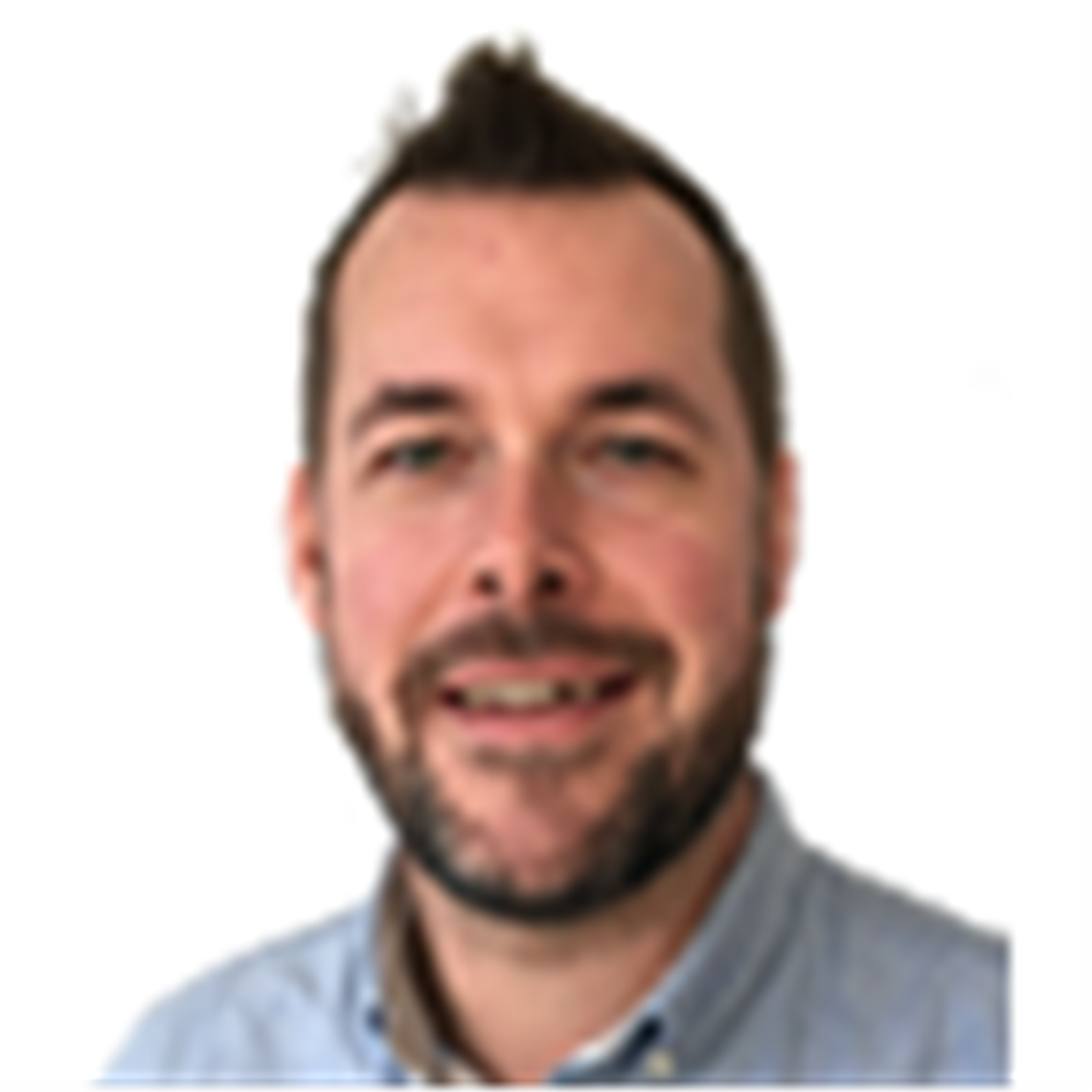
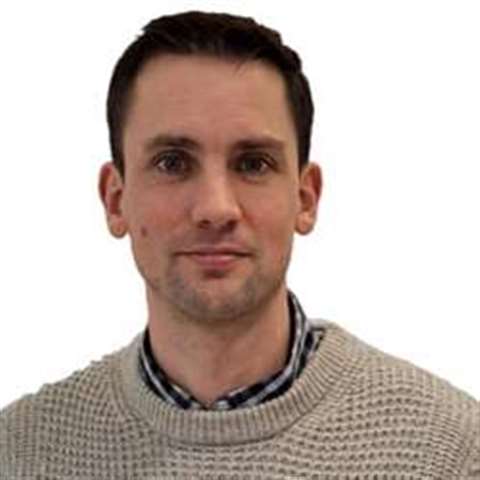
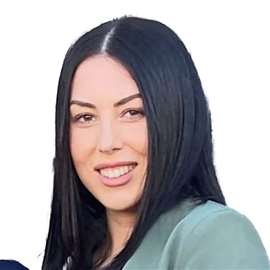
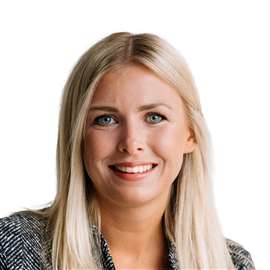