Unconventional drilling
29 January 2014
Technology is a major theme in the drilling equipment market – from pipe laying to foundations construction to blast hole drilling in quarries, manufacturers are concentrating on improving the versatility, efficiency and accuracy of their products.
Remote performance management devices are becoming more and more common in the industry, for instance, while innovative water-powered drilling techniques are also making waves.
Another major trend has seen producers strive to fit more and more power into ever more compact machines for operation in tight and hard-to-reach areas.
For example, Montabert has launched new drilling attachments in North America with versatility in mind.
It argues that these drilling attachments require less initial investment than their conventional dedicated drill rigs, as well as offering the versatility of being easily transportable between sites and quickly exchanged for other attachments.
The smaller models, the Micro CPA H22/H25 and Micro CPA R25/R32 drills, are designed for use on a variety of carriers in the 5 to 10 tonne range — including compact excavators, backhoe loaders and skid-steer loaders.
The larger CPA 225E drilling attachment is designed for carriers in the 15 to 25 tonne range. All the new models boast radio remote control capabilities, and a dust collector is an option on the smaller Micro tools but comes as standard on the CPA 225E.
The larger drill has a radio remote controlled performance management system which automatically analyses drilling conditions and adjusts factors such as feed pressure, feed speed, anti-jamming controls and percussion pressure.
Panama drills
Another manufacturer with new drill attachments in its range is TEI Rock Drills, and it said that while its excavator-mounted drill was not suitable for every type of project, it was the only option capable of drilling high enough on the US$ 5.2 billion Panama Canal expansion project.
TEI’s HEM550 excavator drill supported dry excavation of the new Gatun locks for the project – specifically rock bolting and blasting operations.
“This was the only drill that could adequately reach the holes, which are located at heights up to 40 ft (12.2 m),” the manufacturer said.
The drill and steel operators worked from an aerial lift to drill the holes and add or remove the drill steels. The holes were 4 ½ in (114 mm) diameter and up to 30 ft (9.1 m) in length. An operator in the excavator cab of helped position the drill, and TEI said it took a co-ordinated effort between these three people to undertake this difficult drilling work.
After drilling each hole, the drill basket was returned to ground level to drop the drill steel out of the basket and load the bar into it, before being raised again to manoeuvre the bar into the hole. The bolts were grouted into place at the end of each day.
Little Beaver has also been developing its compact drill products and has launched a new trailer-mounted rig for water well drilling, soil sampling and geotechnical drilling. Designed for longevity and ease of ownership. It said the LS300T+ offered the capabilities of a large drill rig in a lighter, more convenient package.
Mounted to a 7,000 lbs (3.17 tonne) capacity, towable tandem-axle trailer, the drill is 19 in (482 mm) long and 82 in (2.1 m) wide, featuring a 6 ft x 3 ft (1.8 m x 914 mm) mast that folds down for transport. It can be shipped fully assembled in a standard container.
The LS300T+ can bore holes 6 in (152 mm) in diameter and 300 ft (91 m) deep in ground conditions from sand to clay to soft rock, as well as many rock formations.
DTH for emerging markets
Meanwhile, the latest drill from Atlas Copco is the DM 30 II down-the-hole (DTH) rotary blasthole model, manufactured in Nanjing, China, and targeted at all non-Tier 4 emissions countries – that is to say countries with lower diesel exhaust emissions legislation than the US, Europe and Japan.
Upgrades on the Mark II version include a robust I-beam frame, increased decking and component access, and improved rod handling and breakout. Standard features now include auto thread lube, head up tram interlock and grease manifold, plus a wider range of options created from customer special requests. The company said it aimed to develop a world class but affordable product.
And in the horizontal directional drilling (HDD) field, Vermeer has introduced a new addition to its Navigator family – the D220x300 Navigator HDD. The drill boasts 242,100 lbs (1,077 kN) of thrust/pullback and 30,200 ft-lbs (40,946 Nm) of rotational torque.
The D220x300 HDD is 37 ft (11.3 m) long and 8.5 ft (2.6 m) wide and is well-suited to urban utility work, as well as large pipeline installations. It features a sliding-arm rod stager can stage five rods at a time, allowing for increased boring efficiency.
Environmental impact
Environmental concerns are also a big issue in the drilling sector, and manufacturers are coming up with new technology to reduce a drill’s impact on the ground around it – an issue that is particularly pertinent when drilling in urban areas. New water-powered drilling technology has been developed by manufacturer Wassara, for instance, and is in use on a rail project in Stockholm, Sweden.
A 6 km commuter rail tunnel is being built beneath central Stockholm – a € 1.7 billion (US$ 2.3 billion) development dubbed the Citybanan project.
Since the project involves tunnelling under the historic heart of the capital in challenging ground conditions, authorities stipulated that environmentally sensitive construction techniques must be used.
To limit interference from vibrations and noise, no tunnel boring machines could be deployed along the route. In addition, instead of conventional air-powered drilling, which could pressurise the rock formations and put surrounding buildings and infrastructure at risk, contractors must use water powered down-the-hole drills (DTH), which were supplied by manufacturer Wassara, across the project.
However, subsidence is a big issue in central Stockholm as the foundations of many buildings sit just above the water table. The ground beneath Stockholm consists mostly of solid bedrock, but in some places the rock is deeper and covered by a layer of clay – these areas can be particularly sensitive to groundwater fluctuations.
Contractors therefore have to keep careful track of water levels and dewatering pumps from Grindex are being employed together with the Wassara drills to remove waste water.
Close to the existing Stockholm South railway station, the new commuter rail tunnel will be driven beneath an existing park and also beneath a building that is listed as a National Heritage site.
Challenges
This shallow, 331 m part of the tunnel is being built using the cut and cover method, which involves driving retaining wall foundations then excavating the tunnel and casting the base slab before the roof of the tunnel is put in place. When completed, the building will actually stand on the tunnel’s roof.
Contractor Bilfinger Spezialtiefbau is using Wassara DTH drills and jet grouting hammers to support foundations work. Dewatering pumps from Grindex are also on site to keep water levels in balance.
Wassara drills are powered by high pressure water (up to 180 bar), and use up to 300 litres per minute. No power is lost through the drill string during operation, and when leaving the hammer, the pressure is also reduced to ambient pressure as it is an open system.
Christina Salmonson, area manager at Bilfinger Spezialtiefbau, said, “With the Wassara drills, there is no sediment and dust thrown into the air compared to the air-powered drills, and instead the cuttings are flushed out in the water, which we pump away for treatment. But we are working in clay so it gets messy – it is always wet and now we are down to sea level.”
That is where the Grindex dewatering pumps come in. “We are currently handling about two million litres of water a week,”
Ms Salmonson said. “The project will require around 2,000 holes to be drilled for pile driving operations. We are always measuring the ground water level, and the Grindex dewatering pumps are working hard to remove excess water.”
When the works are complete, the new tunnel and the existing main line track will be fully covered. Construction of this section started in January 2010 and is scheduled for completion in 2014.
There is more technology on drilling equipment than ever before, targeting a variety of challenges faced by contractors. With more and more focus on protecting the environment – particularly in urban areas – from emissions, dust and noise, it will be interesting to see how manufacturers integrate new technology that tackles these issues in the coming year.
STAY CONNECTED

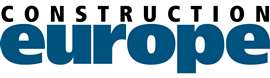
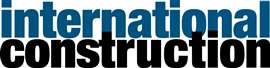
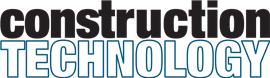
Receive the information you need when you need it through our world-leading magazines, newsletters and daily briefings.
CONNECT WITH THE TEAM
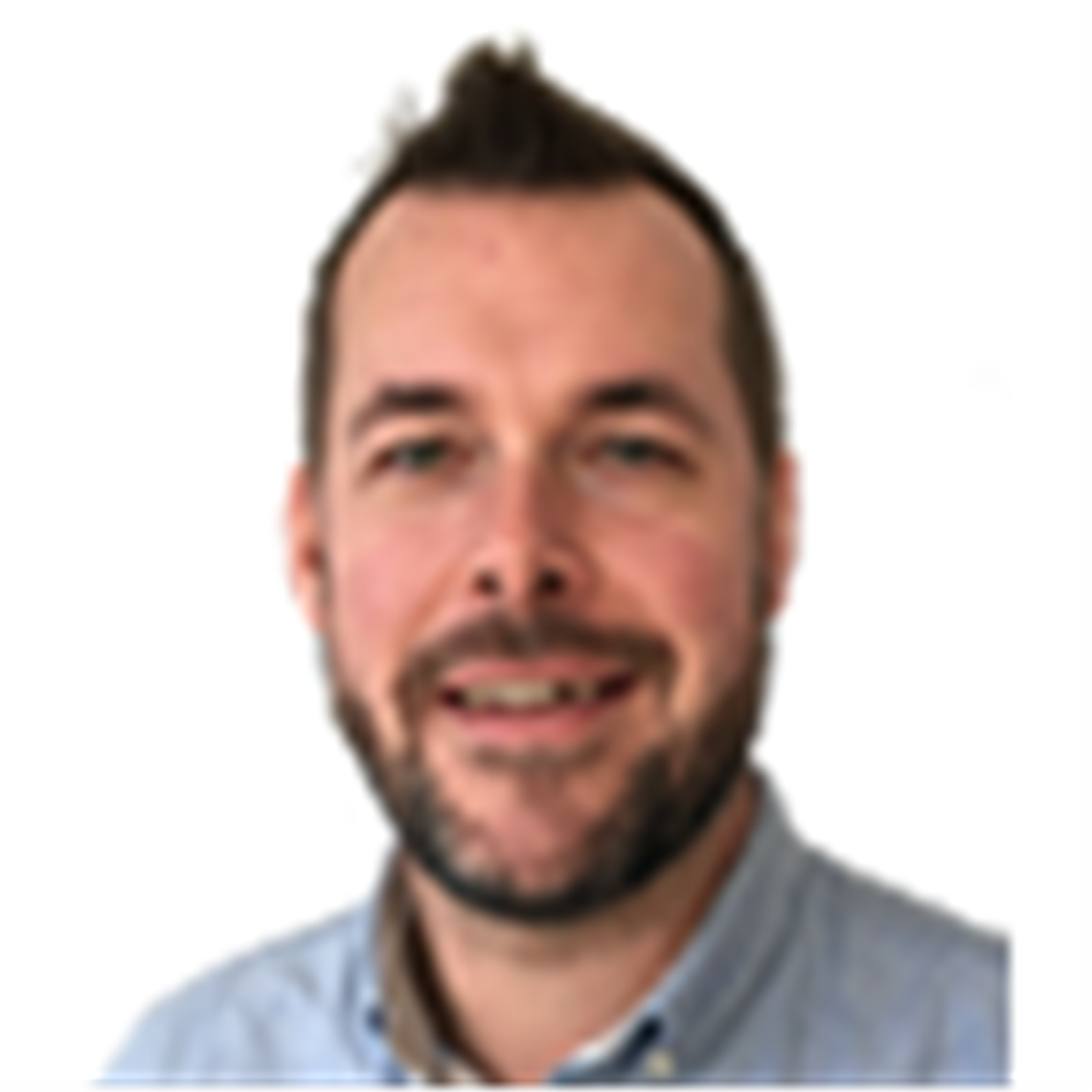
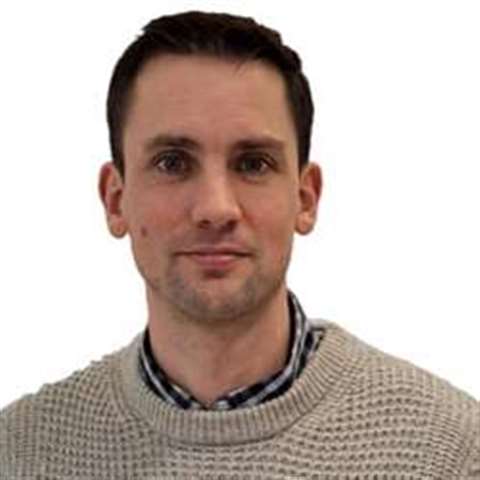
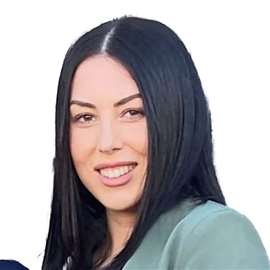
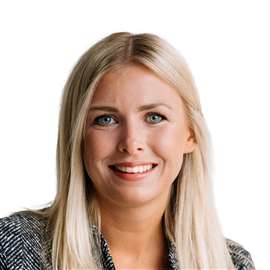