Tunnelling: Just keep digging
11 May 2016
As traffic continues to cause a problem around Acapulco Bay, with peak times resulting in a two-hour journey around the tip of the Cumbres de Llano Largo Mountain to Acapulco Bay, Mexican-based Acatunel SA has been handed the task of completing a 3.2 km tunnel through the Cumbres de Llano Largo Mountain, Mexico, using Sandvik’s DT820-SC and DT1131-SC tunnelling jumbos.
The journey faced by tourists and visitors to Acapulco Bay from the airport is a relatively short journey of 12 km. However, to travel this distance they face a scenic but winding trek on a badly congested road, said Sandvik.
In 2013, 3.5 billion pesos (US$ 213.4 million) was raised for the construction of what would be the longest highway tunnel in Mexico. When finished, this will help facilitate a much shorter and quicker journey time to and from the airport, with the investment also leading to the creation of hundreds of new jobs.
The company is using Sandvik’s DT1131-SC, which is 18 m long from its rear overhang to the front of its fully-extended booms, and its fail-safe disc brakes securely lock the machine in place.
The DT1131-SC is a large rig, weighing 44 tonnes, which carries three booms that can excavate an area of 18 m by 11 m.
The four-wheel drive boom carrier is powered by a 110 KW diesel engine.
To meet the challenge where the drilling boom meets the rock, Acatunel is using Sandvik T38-Hex35-R32 16 foot rods, T38-T38 couplings and RD525 drifter shanks with 48 mm bits.
Acatunel has also used Sandvik’s DX680 and DX700 drill rigs to open the tunnel, and create benching for water drainage within the tunnel.
Meanwhile, High Himalaya Hydro Construction, a newly established company in Nepal, has acquired a Sandvik Construction DD321-40 2 boom drilling jumbo with telescopic boom for its tunnelling projects in Asia.
The DD321 drilling jumbo is the latest addition to Sandvik’s fleet, and is ideal for small-scale tunnelling operations.
The DD321 is powered by new rock drills, robust booms and a wide selection of feeds, and offers an optimal coverage of 49 m2. The carrier layout is specifically designed for safe access to all service points, and all daily maintenance is conducted at ground level. To ensure highly accurate drilling results and enable valuable feedback information of the drilling process, the drill rig may also be equipped with TCAD+ instrumentation.
The aim of High Himalaya Hydro Construction is to provide a superior service to its clients in every aspect of hydropower construction in terms of time, cost and overall quality, said Sandvik.
The company added that the use of the DD321-40 2 boom drilling jumbo would add to the service quality of the company, and help ensure that its projects are delivered on time, within budget and to the highest possible quality levels.
In Germany, a single tube, two lane road tunnel, named Scheibengipfel Tunnel, was constructed to reduce the amount of traffic passing through the city of Reutlingen.
Before the tunnel was completed, over 65,000 cars passed through the city each day, and the aim of the tunnel was to reduce traffic by over 30%.
The project consisted of two tunnels. The main 100 m2 cross section tunnel was designed to take the traffic, with a second 40 m2 tunnel for emergency evacuation running parallel to the main tunnel. A cross-tunnel was also excavated at intervals of 250 m. the Overall tunnel length is 1,910 m.
190,000 m³ of rock was excavated from the main tunnel and 76,000 m³ from the emergency tunnel. The tunnel was driven using NATM (new Austrian tunnelling method) with the majority of the excavation using drill and blast. In sections of very soft rock, excavation was completed using a ripper bucket on an excavator.
Mounted on the Liebherr R944 tunnel excavator, the ER 2000 – the 2000th transverse drum cutter manufactured by Erkat – was used to scale the face after blasting and to achieve an accurate tunnel profile. By maintaining an accurate tunnel profile, the contractor was able to make significant savings on shotcreeting, the primary layer of tunnel lining, said Max Boegl, the contractor for the project. The average rate of tunnel advance was maintained at 4.5 m/day.
The smaller ER 1500 was used in the emergency tunnel. It was fitted with a hydraulic tilt unit and mounted on a Caterpillar 321 excavator with a special tunnelling boom. As the Caterpillar excavator didn’t have a rollover boom, the tilt unit was required to get access to all sections of the tunnel profile.
The ER 1500 was also used to lower sections of the tunnel floor where they didn’t achieve the correct level with blasting. Due to the accurate profiling achieved with the drum cutters, it was estimated that the savings in shotcreeting costs were between 10 and 20%. The total volume of shotcrete used was 110,000 m³.
The second largest project in Europe is the Stuttgart 21 underground station and rail scheme in Germany, and the associated Stuttgart-Ulm high-speed rail project, both of which involve multiple tunnels. Taken together, they are costing around €10 billion (US$ 11.23 billion). Both are now significantly into construction after years of controversy and protest.
The city project is building a new central station, underground in the heart of the city, with eight tracks running at 90º to the orientation of the 15-platform existing station. The client, Deutsche Bahn, said that despite fewer lines, the through nature of the station was quicker and faster than the existing in-out terminus, which funnels into just five exit lines.
The project involves reconfiguring local and regional lines with a series of radiating soft ground tunnels in the city, which is enclosed by hills on three sides. Complex work is needed beneath buildings and a river crossing.
There is also a new high-speed rail link running out southeast through the largest of the tunnels, the 9.5 km hard rock Filder tunnel which is currently being driven.
Austrian contractor Porr is working from the southern portal, using TBM drives and a central 1.5 km long section of drill and blast. The drill and blast is needed to pass through anhydrite Keuper gypsum which must be kept dry to avoid expansive reaction with water which could trap a machine. Special water seals have to be installed around the tunnel bores.
Work on the first bore began in autumn 2014 using a 10.82 m Herrenknecht multimodal machine, in EPB mode. Spoil goes to the surface with a Swiss Agir conveyor for immediate loading for truck disposal from a tightly constrained worksite. To save space, segments arrive on a just-in-time basis by train from precast works operated by Max Bögl near Berlin.
The first 4.5 km is just finished, and the TBM is being dismantled and moved to the portal for a parallel drive beginning next spring. Atlas Copco rigs are starting the centre sections. After its second drive the TBM will be hauled through the conventional sections for two more drives at the far end.
At this city end, meanwhile, large NATM caverns are being made for the TBM reception and turn, and for link tunnels into the station. Sophisticated compensation grouting is needed to stop the settlement of buildings above the tunnel. Specialist consultant Professor Walter Wittke is advising on the tunnel and this work.
He is also working on the high speed link to Ulm, which continues from where the Filder finishes at the airport with another 60 km of new line. Some five major tunnels are required, several in construction for the last three years.
The biggest are under the Schwabian Alps, a highland national park where two tunnels, totalling 14 km take the line upwards and another, the 5.5 km long Albabstieg, descends into Ulm.
Difficult karstic limestone and squeezing conditions are being tackled for the first ascending tunnel – the Bossler. Part of this is driven by an 11.3 m Herrenknecht TBM, while the remainder is using drill and blast methods. The same Porr-led joint venture is doing this work.
It has also completed the 4.8 km long Steinbühl tunnel, which continues the upward climb after a 485 m bridge over a narrow valley. Despite further difficult karstic limestone sections, this twin bore has gone well and breakthrough was due to be celebrated on 6 November 2015, six month ahead of schedule.
A further soft ground tunnel of 7 km is still in preparation along the line.
Even bigger high speed tunnels are underway through the Alps linking northern Europe to Italy.
The largest is the world record 57 km long Gotthard Base tunnel, up to 2,500 m deep, where track laying is complete and the opening is expected to be in June this year.
The AlpTransit scheme includes a second tunnel further south, the 15.4 km long twin-bore Ceneri where drill and blast operations with Sandvik rigs and a Rowa backup system are nearly complete. This was one of the first major projects for Agir conveyors.
Two southern drives were completed in March and more difficult 8 km northern drives will finish by the end of the year when rail and signalling work begins. The Ceneri will shave a further 10 minutes from the Zurich to Milan route when complete.
Meanwhile, attention has moved to Austria and Italy where not only the great Brenner Pass base tunnel is well underway, but two more base tunnels as well – Koralm and Semmering.
The Brenner, from Tyrolean capital Innsbruck to Fortezza in Italy, forms part of the Trans-European Network (TEN-T) route from Berlin to Palermo. It is comparable to Gotthard at 55 km long and has a maximum cover of 1,800 m. If taken together with a 9 km linked bypass tunnel at Innsbruck for trains heading onwards, it will claim a world record length of 64 km.
Between two single-track main bores of 8.1 m in diameter there is a smaller central service tunnel of just under 5m inner diameter and running 12 m lower. It serves for later maintenance and drainage but is also vital for exploration and geological investigation, according to the client, the Austro-Italian Brenner Base Tunnel company.
Preparation for the main tunnel drives has been underway for several years, with five major access adits virtually complete, including a 6 km length of the exploratory from Innsbruck. The most important work recently has been a 1.5 km long, conventionally excavated section across the Periadriatic fault on the Italian side. This tectonically crumbled rock was potentially a major obstacle, but while the fractured rock was difficult going, it has proved passable. The same contract, completed this year also excavated and lined the first two 1.5 km sections of the main bores.
The next major work is an additional 15 km of exploratory tunnel being made with a Herrenknecht gripper TBM southwards from the initial Innsbruck section. It started this October after assembly in an underground cavern.
The €380 million (US$ 426.74 million) multipart contract was let to Austrian contractor Strabag with Salini Impregilo from Italy in September last year. Work also includes completing more access points in the Innsbruck area, and a long 9km drill and blast drive parallel to the bypass tunnel as a safety tunnel.
Austria has another trans-European high speed link underway, upgrading the line from Vienna to Graz, and with an entire new line section onwards to Klagenfurt.
A key feature of the link is the 32.8 km Koralm tunnel with maximum cover of 1,200 m, and like other base tunnels it has a very flat gradient. Apart from a small 1.5 km portal section begun in 2011, it is being driven in two main contracts.
The largest is by contractor Strabag and joint venture partner Jägerbau with 20 km to do. A first section of around 3 km was in soft ground while the rest is parallel hard rock drives – one of 16 km and one 17 m, both with segmental linings.
Begun two years ago, these have proved slow going in hard and often blocky rock, though the contractor is pleased with its two “tough” CREG-Wirth TBMs now over 11km in. The client, Austria’s Federal Railways civil engineering company ÖBB Infrastruktur, has said that things are within the parameters of the contract for the eventual 2018 completion.
The remaining approximately 12 km of tunnel was let last year to Porr, and is being driven by conventional methods in one tube, where half was excavated in the investigation stage, and by a multimode Herrenknecht TBM on the full length of the other bore.
North of Graz, meanwhile, the 27 km long Semmering is just starting. Cutting under the historic but speed- and gradient-limited Semmering mountain railway, it will also provide a flat gradient for high speed trains.
Because of exceptionally complex geology and high water heads, investigated in detail over the last decade, the tunnel is divided into several sections, mostly to be built by conventional means. Contracts are currently being let.
Only one central section of 9 km can be done by TBM, starting from a cavern at the base of a 400 m deep shaft currently under construction by a joint venture of Implenia and Svedelski. Some 4.4 km of conventional drive will head in the other direction from the shaft cavern.
A 7.4 km section from Gloggnitz at the east portal has been let to Hochtief Infrastructure Austria, Implenia Austria and Thyssen Schachtbau for €457 million (US$ 513.21 million). Work will go from the portal and an access shaft.
One final trans-European base tunnel route is the 57 km Lyon to Turin cross-border project. Final go ahead was agreed in February last year between France and Italy. An EU subsidy of 40% of the €8.8 billion (US$ 9.88 billion) cost, was agreed in July 2015.
The tunnel between St Jean-de-Maurienne in French Savoy and the Susa valley in the Piedmont will have twin bores with a separation of 30 m. The inner diameter will be 8.4 m – slightly larger than Gotthard and Brenner – allowing clearance for lorry shuttle trains.
There had been work on access and exploratory tunnels completed in recent years but full commitment to the scheme has been uncertain until now.
A fourth access and exploratory adit on the Italian side is still in excavation and about half complete. It began later in 2013 because work had previously been disrupted by hostile demonstrations. This Maddalena tunnel site still has a police guard.
It is using a 6.3 m diameter Robbins main beam TBM both to test possible TBM drive conditions and gather rock data.
Volvo Construction Equipment has been helping open up the remote Portuguese regions of Douro and Trás-os-Montes for development, thanks to its role in the Túnel do Marão project, one of the largest road tunnels in the Iberian Peninsula.
A new government-funded project to extend the A4 motorway from Porto all the way to Vila Real near the Spanish border, takes a route straight through the mountain. There are two tunnels, each measuring approximately 5.7 km in length. The Túnel do Marão will be the longest road tunnel in Portugal.
EPOS (Empresa Portuguesa de Obras Subterrâneas) began work on the twin tunnels in October 2014 and plans to finish the concreting and paving stages of the project by February 2016.
It used 22 pieces of Volvo construction equipment, 13 of which were purchased shortly before the project began.
STAY CONNECTED

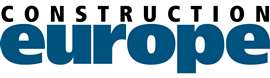
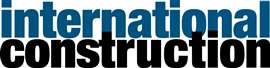
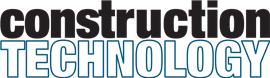
Receive the information you need when you need it through our world-leading magazines, newsletters and daily briefings.
CONNECT WITH THE TEAM
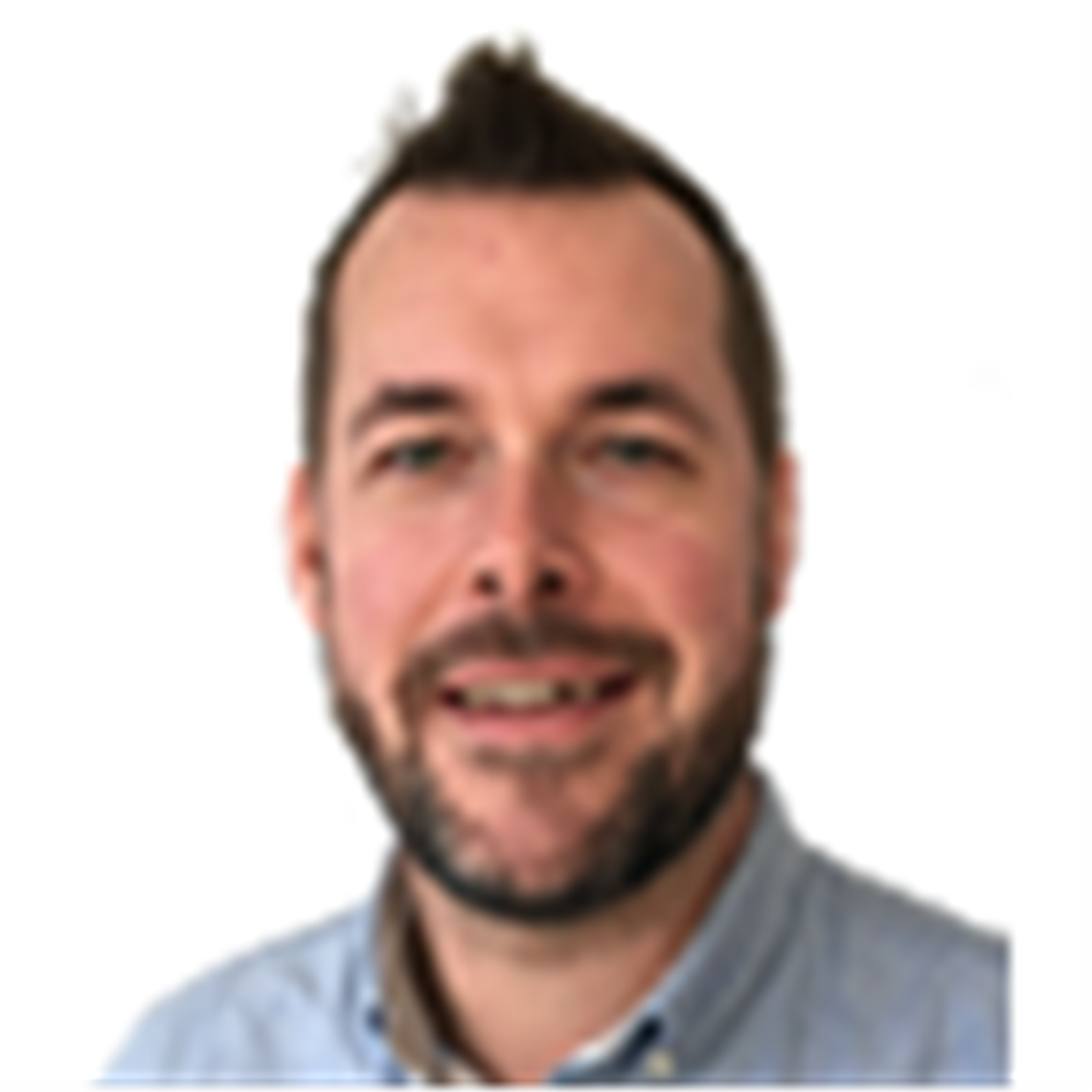
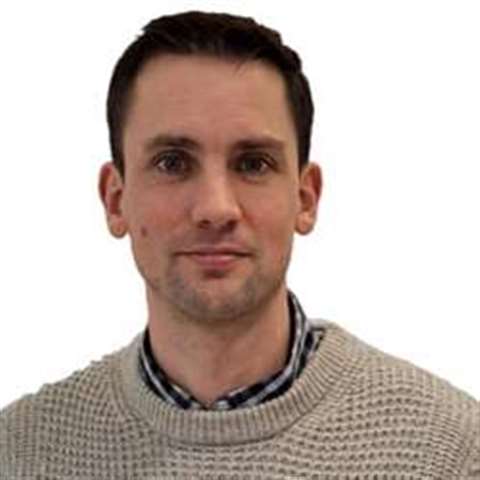
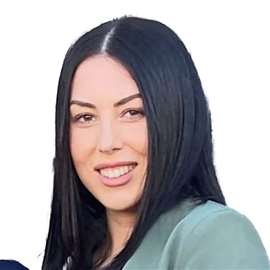
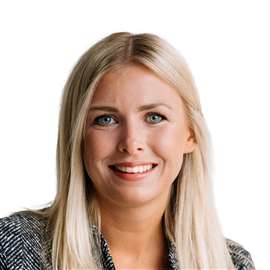