Trump's triumphant tower
09 April 2010
Construction of Chicago's Trump International Hotel & Tower, crowned the tallest building completed in 2009 by the Council on Tall Buildings and Urban Habitat, is all about the concrete; from the huge amount - over 180000 yd3 (140000 m3) - to the large pours, special mixes, pumps and formwork. Richard High reports.
The mixed use 1389 ft (423 m) high Trump International Hotel & Tower has dominated the Chicago skyline since topping out in late 2008. And when construction of the 92-storey tower, by Bovis Lend Lease, finished in 2009 it became the second-tallest building in the US after Chicago's Willis Tower.
Situated on the banks of the Chicago River, with commanding views of Lake Michigan, it is, of course, named after real estate developer Donald "The Donald" Trump. Designed by architect Adrian Smith of Skidmore, Owings & Merrill (SOM) it sits on a site previously occupied by the Chicago Sun-Times building.
The tower's design incorporates three setback features to "provide visual continuity" with the surrounding skyline; each one reflects the height of a nearby building. The first setback, on the tower's east side, aligns with the cornice of the Wrigley Building.
The second, on the west side, aligns with River Plaza to the north and with the Marina City Towers to the west. The third setback, on the east side, relates to 330 North Wabash building.
The tower's setbacks and rounded edges also help combat vortex formation, a feature of the "Windy City". The body of the tower is raised 30 ft (9.1 m) above the main Wabash entrance and 70 ft (21 m) above the Chicago River.
It uses clear, low-emissivity coated glass and a curved wing-shaped polished stainless steel mullion system that projects 9" (230 mm) from the glass line, and incorporates brushed stainless steel spandrel panels and clear anodized aluminium.
The "Big Pour"
The Trump Tower is a reinforced concrete structure. Reinforced concrete was selected over steel because of the economics of the design and because the structure must maintain as little movement as possible because of its height.
"We decided on the concrete design for a handful of reasons," said Andrew Weiss, executive vice president with 401 N. Wabash Venture, the Tower's owner and developer.
"Given Chicago's extreme wind gusts, we wanted to minimize movement as much as possible, to make the future occupants of the building feel comfortable. The natural properties and heavier mass of concrete make that possible while providing a more efficient use of the space by utilizing concrete flat slabs for higher ceiling heights."
More than US$ 130 million of its construction budget was earmarked for the concrete elements, which were undertaken by Chicago-based contractor James McHugh Construction.
But before the main construction work could get under way the former headquarters of the The Sun-Tribune had to be cleared from the site. A disused freight tunnel, which passes below part of the site, also had to be sealed and, due to the riverfront location, old dock piles also had to be removed.
The tower's foundations are formed by a steel reinforced concrete raft supported by over 240 caissons sunk up to 110 ft (33.5 m) through the underlying clay and into the limestone bedrock below. McHugh senior vice president Dale Hendrix said, "We built the foundation raft, which measures 200 ft (61 m) in length, 66 ft (20 m) in width and 10 ft (3 m) in depth, using more than 5000 yd3 (3800 m3) of self consolidating concrete. The raft effectively anchors the building to the foundations below."
Orchestrating what Mr Hendrix calls 'The Big Pour' was a monumental task. Thirty concrete trucks worked for almost 24 hours to complete the work in a single pour.
Prairie Material Sales provided the concrete and the trucks, making 600 trips between the construction site and its concrete distribution site. Chemists were on hand during the continuous pour to ensure the special formula of concrete was to exact standards. Designed specifically for the job, the concrete needed to be able to support the 327000 tonne load of the building.
According to Prairie's vice president of operations Paul Blatner, the compressive strength of conventional concrete is 48 N/mm2, but the mix used for the Trump Tower foundation raft was designed to reach 69 N/mm2.
Special additives were used in the mix to ensure the concrete met the strict design, which included keeping the concrete's temperature during the placement below 26.7 °C and the temperature during curing below 76.7 °C.
Construction of the foundation raft, basement levels and mechanical facilities were completed in December 2005, clearing the way for McHugh to start bringing the structure "out of the hole," according to Mr Hendrix.
Core construction
The core uses five I-beam-shaped walls and exterior columns, narrowing to two as the tower rises. Each floor is a concrete slab, with stainless steel, glass, and aluminum panels attached. McHugh implemented a comprehensive formwork solution using over 16900 of Peri's Multiprop aluminium post shores and 2600 of its PEP steel props for the shoring alone on the lower levels.
Peri's Skydeck aluminium panel slab formwork with drophead system was also used, allowing the slabs to be struck after only two days.
The massive reinforced concrete columns on the north and south sides were constructed with Peri's ACS climbing system and its Vario girder wall formwork, which freed up valuable crane time. At the same time, its ACS platforms also functioned as protection against falling on slab edges.
Peri's engineers also developed customized climbing units for the column and climbing rail spacings of 9.10 m. While from the 16th floor onwards, the east and west sides were clad with its RCS rail climbing system protection panel.
Reinforced concrete was selected over steel because of the economics of the design and the fact that the structure must maintain as little movement as possible because of its soaring height, according to Andrew Weiss, executive vice president with developers 401 N. Wabash Venture
"We decided on the concrete design for a handful of reasons," said Mr Weiss. "Given Chicago's extreme wind gusts, we wanted to minimize movement as much as possible, to make the future occupants of the building feel comfortable. The natural properties and heavier mass of concrete make that possible while providing a more efficient use of the space by utilizing concrete flat slabs for higher ceiling heights."
"Trump Tower Chicago is a great challenge because it's massive in every way possible," said Mr Hendrix "Everything you can think of in this structure is maximized; the soaring height, thickness of the columns and walls, the amount of concrete, amount of rebar and even the amount of people working together to build this structure. It's almost like we're building two buildings."
To place the massive amount of concrete - 180000 yd3 (140000 m3) in total - McHugh relied on a placing system combining Putzmeister's BSA 14000 trailer-mounted concrete pump and a Putzmeister 34/38Z-Meter Series II Detach boom.
The BSA 14000 was located in the basement of the structure where the ready mix concrete trucks drove up and delivered the concrete. The 22.4 ton (20.4 tonne) Putzmeister BSA 14000 pumped about 1100 yd3 (841 m3) per day.
Taller and taller
"There were two towers at the top of the Trump structure where the 34/38Z placing boom could be positioned, one on each end of the building," said Mr Hendrix. "The two tower locations helped us pour the concrete wherever it was needed with ease. The pedestal is mounted to the structure's own core-form by a clamped-down base.
"Flying the pin-connect boom and pedestal with the crane from one location the other is a relatively simple process. It only takes 30 minutes and we're back in business," added Mr Hendrix. By the 27th floor the BSA 14000 and 34/38Z had placed about 65000 yd3 (49700 m3).
"As the building gets taller and taller, the square footage for the upper floors gets smaller, which makes a pour go quicker as a smaller amount of concrete and formwork is required for each floor," said Mr Weiss.
"Up to floor 16, it took four concrete pours in a seven-day schedule and for floors 18 through 29, it took three pours in a five-day schedule," explained Mr Hendrix. "Our goal for floors 30 to 48 was two pours in a four-day schedule and for floors 52 and above in one pour, within a three-day schedule.
"We don't place a floor all at once because of the great yardage. First we pour the horizontal floor, and then the vertical columns that support the next floor. The four floor Peri Skydeck was used to support each floor once a pour was complete."
Mixes
"There are at least 30 different concrete mixes used on the Trump Tower Chicago," said Bob Sinn, senior structural engineer, SOM. "Most needed to be very specific and were tested ahead of time."
The structure ranged in compressive strength depending on use. The mechanical floors and the middle of the structure were specified at a high-strength self-consolidating concrete (SCC) 16000 psi (110.3 N/mm2) concrete mix due to the amount of steel reinforcement in the building.
Some of the structural and all of the mat foundation used 10000 psi (68.9 N/mm2) concrete. The columns and walls ranged from 8000 to 12000 psi (55.2 to 82.7 N/mm2), although some horizontal and vertical elements used 16000 psi (110.3 N/mm2) mix as well. The lowest strength concrete mix was used for the floors - 5000 to 6000 psi (34.5 to 41.4 N/mm2).
"The core walls, especially, are just massive at 4 ft (1.22 m) thick. That's why we are pumping such a high volume of concrete," said Mr Hendrix.
According to Mike Pistilli, technical director, ready mix concrete supplier Prairie Material Company, "All of the mixes contain different percentages of a high-range water reducer, Portland cement, fly ash, slag and silica fume.
"The outrigger walls are very impressive at up to 7.5 ft (2.3 m) deep. We used SCC in a variety of locations throughout the project, including the foundation and the outrigger horizontal walls. Very few people use this type of concrete," he added.
Testing
"In addition to ensuring the right strength was specified for each mix, there was a learning curve for all of us in making sure a different characteristic was up to industry standards for each of the four zones of the structure," said Mr Sinn.
"The structure is made out of concrete, which provides significant inherent damping, a characteristic that takes motion away from a building, much more than steel does, so we had to ensure we found the right combination of materials for the mixes."
Mr Sinn said this included the challenge of judging stiffness vs. motion for the concrete reinforced structure. "This challenge was just as important as specifying the strength of the mixes. Together with Prairie, we had to specify a stiffness characteristic, 'modulus of elasticity,' to determine the stiffness vs. motion for the structure's concrete mixes. Our joint efforts are truly pioneering."
Before ground even broke for the Trump Tower Chicago project, SOM commissioned a 1-500 scale model of the proposed structure and its neighbouring buildings. This model was placed in a commercial wind tunnel laboratory.
"The model moves on a 360° pivot that tested winds out of the east and west," explained Mr Sinn. "We tested the modulus of elasticity very thoroughly because we had constructional obligations and industry standards to meet due to the building's height."
"With our technology and teamwork together with SOM, we were able to find the right ingredients for the right modulus of elasticity specification," said Mr Pistilli.
Facts and figures
Groundbreaking: March 17, 2005
Constructed: 2005-2009
Type: Mixed-use
Height (antenna/spire): 1389 ft (423.4 m)
Height (roof): 1170 ft (356.6 m)
No. Storeys:92
Floor area: 2.6 million ft2 (242000 m2)
Cost: US$ 847 million
Developer: Trump Organization
Architects: Skidmore, Owings and Merrill
Structural engineer: William F. Baker
Construction manager: Bovis Lend Lease
Concrete contractor: James McHugh Construction
Concrete: 180000 yd3 (140000 m3)
STAY CONNECTED

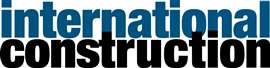
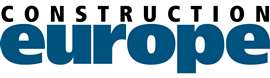
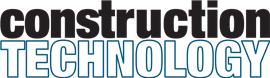
Receive the information you need when you need it through our world-leading magazines, newsletters and daily briefings.
CONNECT WITH THE TEAM
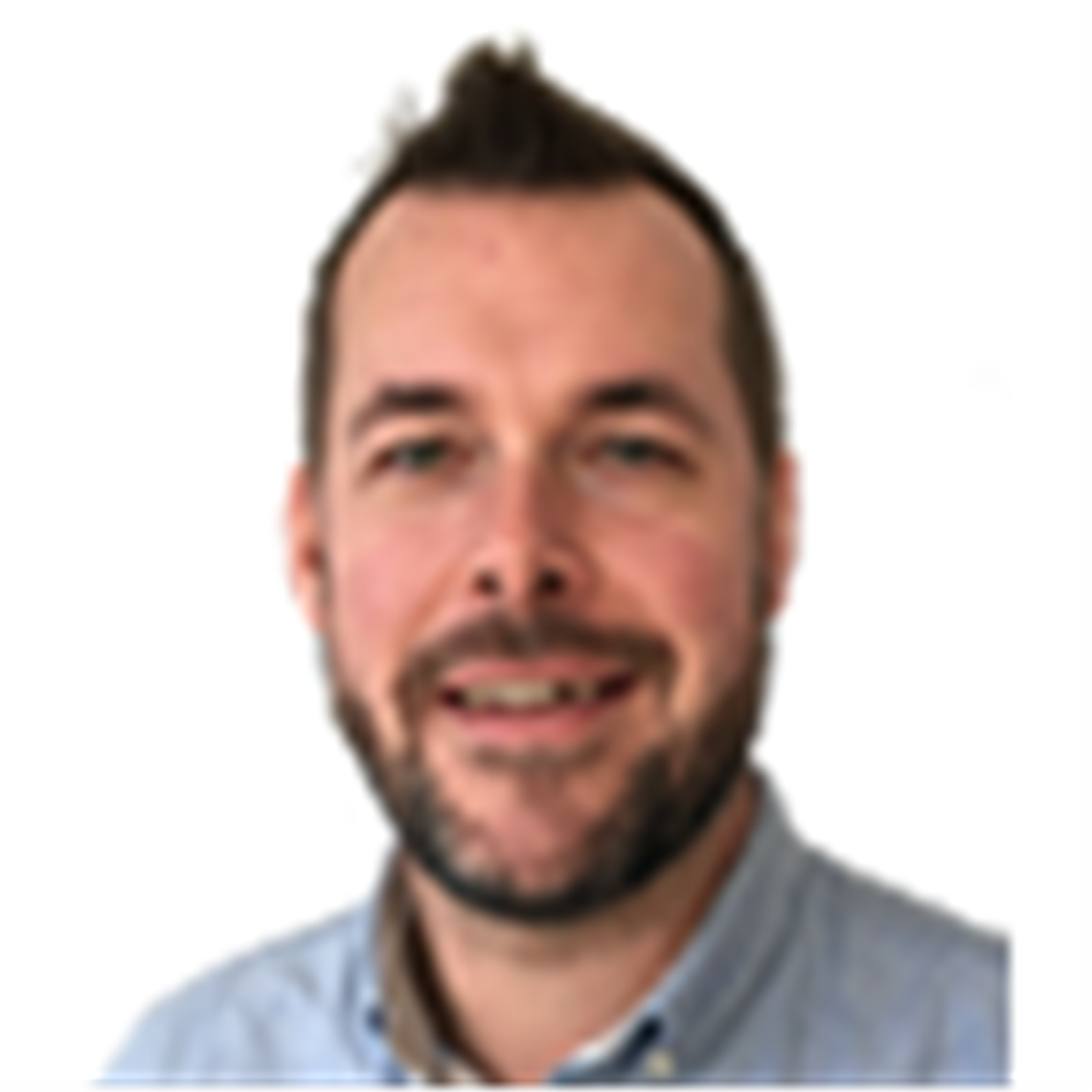
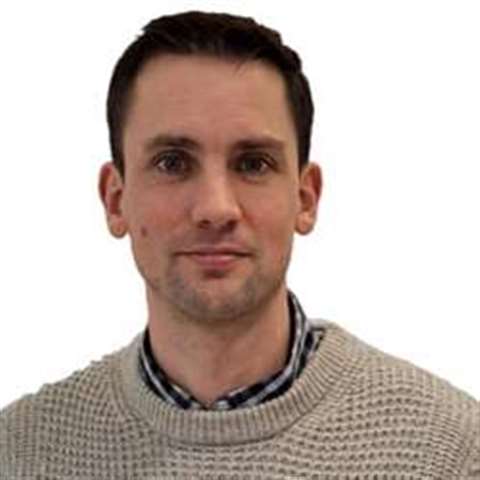
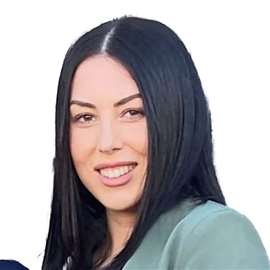
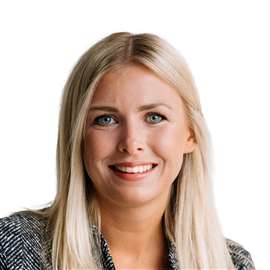