Read this article in French German Italian Portuguese Spanish
The tech a former Caterpillar exec claims can improve even the best excavator operators
18 July 2025
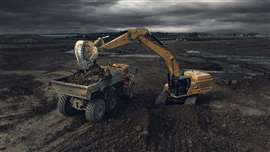
For decades, excavator productivity has depended largely on the skill of the operator behind the controls.
But even among seasoned professionals, performance varies far more than many in the industry realise. A Volvo Construction Equipment study found that, for experienced operators, productivity can differ by as much as 300%, while fuel efficiency may fluctuate by 150%. For less experienced operators or rental customers, the productivity gaps are even wider, reaching 700% in some cases.
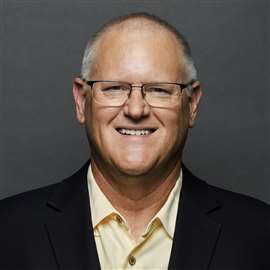
It is this problem - the vast spread in operator performance - that Ken Gray, former global director of innovation at Caterpillar, is now trying to solve. As co-founder and chief performance officer of Israeli start-up Dig Robotics, Gray believes his company’s LiDAR-powered technology can help even the most capable excavator operators achieve levels of consistency, efficiency and productivity that have previously been out of reach.
“The problem that we want to solve is around the variability of operator performance,” says Gray. “All the money manufacturers spend developing new product - those improvements can be lost in the noise if operator variability isn’t addressed.”
Founded in October 2023, Dig Robotics has moved quickly from concept to prototype. Just 90 days after formation, the company had its system running in a quarry. Its solution combines LiDAR-based computer vision, machine learning and real-time operator feedback to fine-tune excavator performance during every bucket cycle.
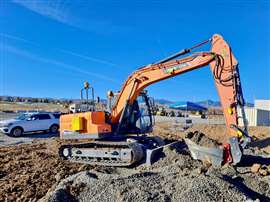
‘We don’t want to take control from the operator - they hate it’
A LiDAR sensor mounted on the roof of the excavator captures live data as the machine works, while algorithms calculate the ideal digging path at any moment, based on the site topography, machine geometry, bucket size and material characteristics. The system then compares the operator’s actual movements to the optimal path, providing immediate visual feedback in the cab.
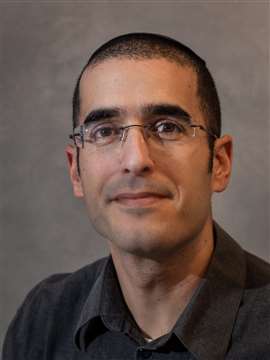
Operators are guided on four critical parameters: the depth of the cut, the angle of the bucket throughout the cut, the speed of movement, and the timing of bucket withdrawal. These metrics are displayed with simple colour-coded indicators - green when operating in the optimal zone - allowing both novice and experienced operators to see exactly where adjustments are needed.
Gray is clear that the aim is not to replace operator skill but to enhance it. “We don’t want to take control from the operator because they hate it. We want to advise them on how to be the best they can be,” he says. “For someone that’s highly experienced, they can toggle to trending information because you really want to know what your habits are. Do I tend to stay in the cut too long? Do I tend to run too deep? Those are the kinds of things they want to know.”
The system learns and adapts as it works. Its machine learning component allows it to automatically assess material conditions - including cohesiveness, granularity, and presence of boulders - without any manual input. Each bucket informs the next, while machines working on the same site share information to build a collective understanding of the material being excavated.
The commercial implications could be significant, particularly for asset owners looking to boost productivity and cut fuel consumption without investing in new machines. The system can be retrofitted to almost any excavator, regardless of brand or age, often within a single working day.
In one early case, Dig Robotics installed the system on a 20-year-old Liebherr R 984 C, operated by a veteran who had run the machine since it was new. The results surprised even the operator. “He’s performing 10% better than he did when we installed it and he’s using about 20% less fuel,” says Gray.
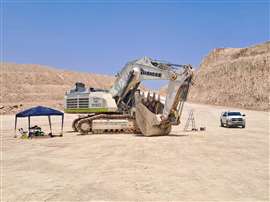
Respect for multiple OEMs
At present, the company’s initial pilots are focused on sectors where incremental productivity gains can deliver substantial financial returns - large civil infrastructure projects, quarrying and mining.
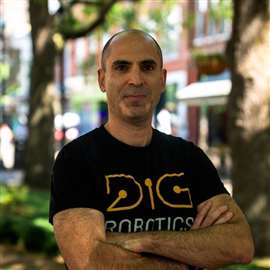
Dig Robotics’ commercial strategy centres on partnering with dealers across multiple OEMs. Discussions and pilots are ongoing with dealers representing Caterpillar, John Deere, Liebherr, Doosan and Hitachi. “I really want to respect customers’ need for multiple OEMs in fleet,” Gray explains. “I think it’s rare these days to see only one OEM out there.”
Dealers are already helping to evaluate not only the technical performance of the system but also its commercial viability, installation process, and long-term support requirements. “They are experimenting with us too. Does it really add value to their customers? How can we help? What does it cost to support it?” says Gray.
The technology itself is backed by proprietary patents, and the engineering team includes expertise in robotics and motion planning, led by chief scientist Dr Oded Medina. However, Dig Robotics must now secure sufficient funding to transition from its current pilot phase into full commercial release.
“We clearly have a problem that customers want to solve,” says Gray. “We have that technology, we found it to solve it. The question is, do we have the financial runway to take it from where we are now, which is a pilot, to delivering the commercial? I think we will.”
The target is to launch the first commercial systems in early 2026.
If successful, Dig Robotics could offer an incremental but important advance in earthmoving operations - one that allows even the best operators to do better.
STAY CONNECTED

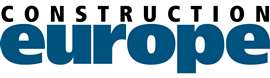
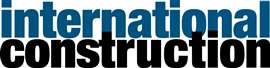
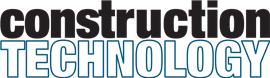
Receive the information you need when you need it through our world-leading magazines, newsletters and daily briefings.
CONNECT WITH THE TEAM
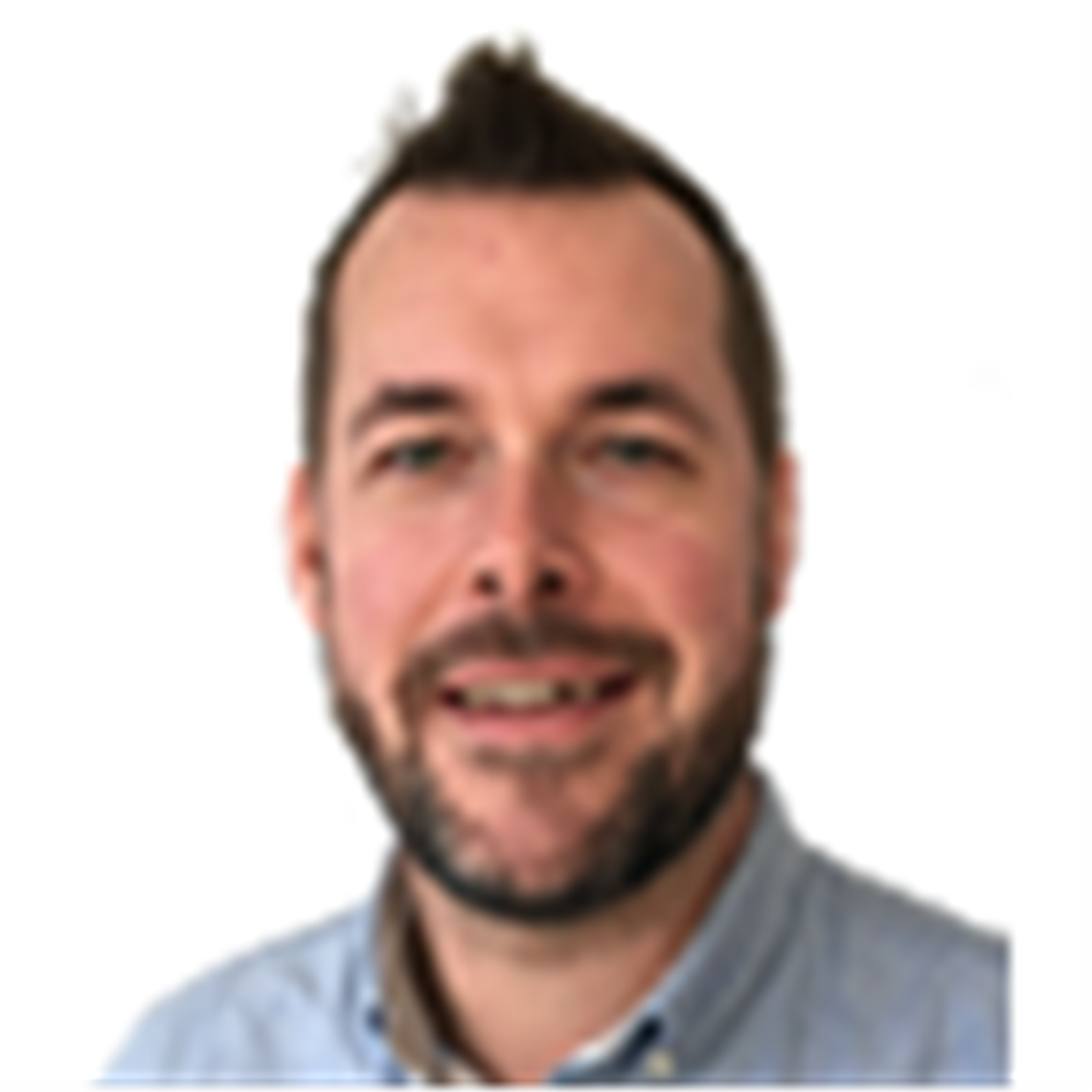
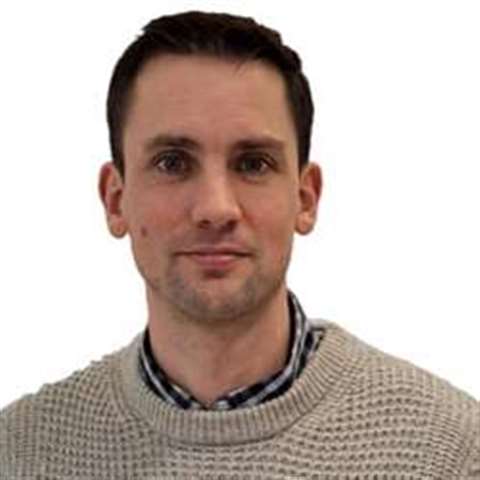
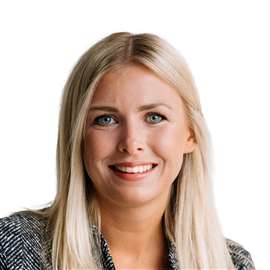