Supporting concrete: from kerb stones to high rise towers
11 December 2008
One of the most frequently used and established materials in construction; concrete continues to shape everything from kerb stones through to high rise towers. Steve Skinner looks at some of the support industries that keep concrete flowing.
While manufacture, transportation and placement lie at the core of the concrete industry, falsework and formwork clearly occupies the front line.
With a 2012 overall completion date, the Dubai Metro is said to be one of the most strategically important infrastructure projects in the Middle Eastern region. It is hoped it will go some way to relieving the traffic congestion that currently blights Dubai rush hour as well as providing a high-speed link to the new Jebel Ali airport.
The first section of the 52 km Red Line is scheduled to open in September 2009, and as the deadline looms, RMD Kwikform is confident that its Megashore support-work will assist the joint venture contractors in hitting timetable.
“Members of the project team came to Dubai from a similar scheme in Hong Kong, where they had already experienced the benefits of Megashore,” said RMD Kwikform’s project manager, David Barrington.
“Essentially, we’ve had to complete a drawing and component list for every different height of the track units above the existing ground level to ensure the installation goes ahead smoothly and safely,” said Mr Barrington. “And we’ve had to do so on a two day turn-around to keep the project on schedule.”
One of the strengths of the Megashore support system is its load carrying capacity of 100 tonnes per leg. “Employed to carry the heavy U-shaped pre-cast concrete sections in situations where there’s restricted headroom or where contractors are unable to use standard launching systems, the Megashore units are being purchased by contractors in preparation for two further Metro lines,” said Mr Barrington.
Also in Dubai, RMD Kwikform has been responsible for the formwork planning and supply for the new Mirdif City shopping centre. The 25000 m2 retail centre on two levels is almost complete, while the adjoining three-storey car park for 5000 vehicles is still under construction.
“Al Jaber Gremekar, the main contractor, chose Alshor Plus because of its speed of assembly,” said Arul Raja, RMD Kwikform’s contract manager. “The extent of the in-situ construction work is enormous and so taking the table form approach was the only way to meet the programme.”
Football World Cup
In South Africa, Doka continues to supply formwork for the Green Point stadium, the new football arena at the foot of Table Mountain in Cape Town that will host the opening and final matches of the 2010 Football World Cup.
“The thorough support that the site crew have been given by the Doka formwork experts is a crucial factor in helping work on the project to run smoothly,” said Mark Brooks, site agent for contractors Wilson Bayly Holmes-Ovcon.
The giant oval football arena is made-up of three spectator terraces with 216, 25 m long stepped beams and 72 inclined pylons. More than 1300 m2 of Top 50 large area formwork and 72 MF240 climbing brackets are in continuous use on the site to enable the joint venture contractors, WBHO and Murray and Roberts, to meet their deadline.
“As many as 36 pylons are being climbed at the same time, with each standing 50 m tall and inclined by 17°,” said Mr Brooks. “The MF240 climbing formwork is easy to adjust to the changed geometry of the structure and thanks to Doka’s planning and formwork solutions the project is on schedule for its 2009 completion date.”
In Singapore, Shimizu Corporation selected Doka to construct 30000 m2 of slab for the new Mapletree Anson office building in the heart of the central business district. Due to the location, fast, safe construction progress was paramount for the 100 m tall, 19-storey office complex.
“The independent Dokamatic table lifting system gave us big gains in efficiency,” said project manager Hirofumi Watanabe. “This speeded up our forming operations and meant our tableforms were in use much more of the time, as the repositioning times were so short,” continued Mr Watanabe.
“The Dokamatic tables let us shore large areas of slab quickly, safely and economically and we saved time and money as well as enjoying a really fast construction process,” said Mr Watanabe.
In conjunction with the forming solution, Shimizu also elected to employ Doka’s hydraulic Xclimb 60, self-climbing protection screen for the site, safeguarding two and half storeys at a time.
Spiralling springs
Peri has risen to an equally significant challenge in the shape of the Seewinkle hot springs resort in the Austrian Alps. The € 80 million project centres on a spiral shaped building featuring multiple circular structures, the shell of which has a nine month deadline for completion.
With slab thicknesses of up to 550 mm, 5 m ceiling heights and circular layouts, Habau Group, the main contractors, selected Peri’s Skydeck panel slab formwork for the construction of the concrete frame.
“The Skydeck drophead system has accelerated materials handling and reduced on-site material requirements,” said a Habau spokesman. “We’ve been able to strike formwork after just one day, leaving just slab props with dropheads and cover strips for temporary support, which has freed panels and main beams for the next section.”
The circular 400 mm thick reinforced concrete core walls are being polygonally formed using Trio panel formwork elements and trapezoidal-shaped filler timbers. “This system has offered a time-saving solution for respective radii specifications,” said the spokesman.
“Furthermore, connecting the Trio elements is a simple process with the BFD alignment coupler, the only connecting part required for the panel joints,” he continued.
Abrasive answers
Earlier this year, Caterpillar launched its 928Hz ready mix wheeled loader, specifically equipped for high production and reliable and comfortable operation in ready mix concrete plants and concrete products plants.
Fitted with a 2.7 m3 sand and gravel bucket and balanced by a ready mix counterweight package, the 6.6 litre 928Hz has a short wheelbase, automatic ride control, heavy-duty hydraulic oil cooler and a dustbowl intake air pre-cleaner.
“The sand and gravel bucket is designed for long life, and side and bottom wear plates extend its life for use in abrasive materials,” said a Caterpillar spokesperson.
Abrasion is a matter that Esser-Werke has also addressed in its new range of Twin Pipes for use on truck-mounted concrete pumps.
“Our Twin Pipes are manufactured using an ultra wear resistant inner pipe and a pressure resistant outer pipe that can be welded,” said a company spokesman. “Both pipes are produced separately, with the inner pipe then inserted into the outer and hardened. The simultaneous hardening of the Twin Pipes results in excellent resistance to wear,” continued the spokesman.
“Furthermore, when abrasive media such as concrete is being pumped, numerous field tests and examination of worn pipes showed us that there was extreme wear in the inlet area.”
Esser looked at the design of the inlet flanges and developed its Big Mouth XL flange. “Consisting of an improved twin cast inlet ring in conjunction with a 160 mm inlet flange extension, tests have shown a +50% life improvement through the Big Mouth XL,” said the spokesman.
To counter the abrasive qualities of concrete Yangzhou Liugong has employed B520JJ steel produced by Shanghai Boashan Iron and Steel for the mixing barrel and stirring blades on its range of truck mixers.
“The mixing barrel adopts a pre-shot technique after it is welded to prevent rust,” said a company spokesman. “Paint technology also helps to contribute to durability,” he continued.
Yangzhou Liugong mixer trucks range from capacities of 8 to 12 m3 and are built on chassis from China Jinan Truck or Shanxi Automobile Group.
Global market
While in October both Strabag and Russia’s Eurocement put on hold any plans for increased production in the Russian Federation following drops in both price and demand, Lafarge, last month, reported increased sales and profits for the third quarter. The mixed picture shows that certain regional markets are clearly suffering in the current economic climate, while companies whose activities serve global markets have, thus far, been able to minimise the impact.
“A strong contribution from emerging markets, up +40% in the third quarter, enabled us to deliver strong earnings and improved operating margins,” said Bruno Lafont, chairman and CEO of Lafarge. “In particular, the Asian and African markets performed strongly while many of the more developed nations saw a downturn.”
In the formwork sector, since Meva crossed the Atlantic in 2000, introducing its imperial formwork system for the US market and replacing plywood with its all-plastic facings, demand for the company’s formwork has grown at such a rate that the company’s US operations outgrew themselves last year.
In October, Meva moved into its expanded 3716 m2 headquarters with improved engineering facilities, client support and warehouse as well as a new cleaning and regeneration facility.
“The construction industry has responded favourably to our formwork solutions. With the new facilities we look forward to better serving concrete contractors all over the US with an even better and faster service,” said general manager Scott Fisk.
Concrete boundries
Despite the long history of concrete construction, equipment manufacturers continue to research and develop machines and solutions that are more durable and efficient than their forerunners. Likewise, concrete producers, such as California’s iCrete, keep moving forwards in their quest to perfect concrete and take the next step in strength and efficiency.
It would be easy to think that we’ve reached the boundaries of concrete construction, but all the time concrete continues to evolve, the industry supporting it is sure to maintain its position at the leading edge.
STAY CONNECTED

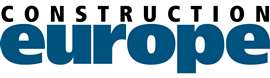
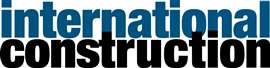
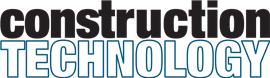
Receive the information you need when you need it through our world-leading magazines, newsletters and daily briefings.
CONNECT WITH THE TEAM
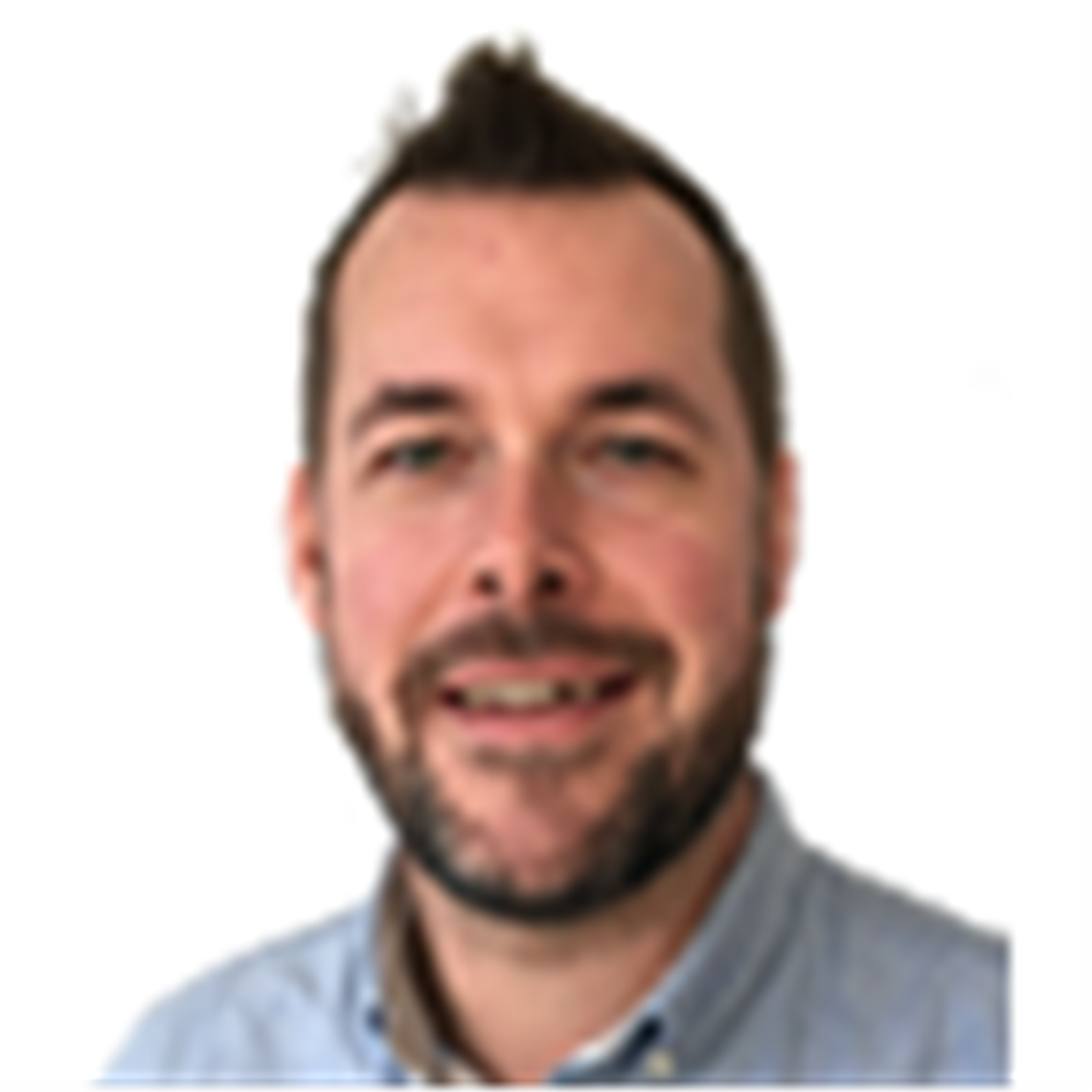
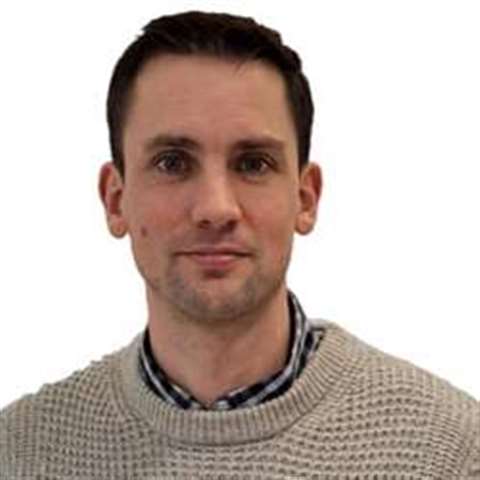
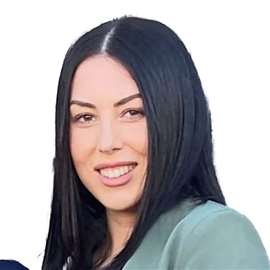
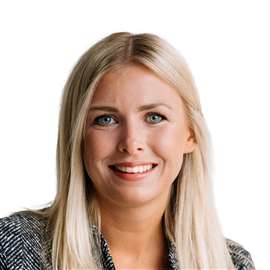