Streamlined surveying: An in-depth look at the surveying equipment sector.
12 October 2009
Surveying equipment manufacturers are developing easier-to-use, more productive instruments using the latest technologies. Becca Wilkins reports on the improvements being made in this specialised sector.
Contractors can carry out surveying tasks more easily with the advent of new and refined technologies such as wireless and remote computing, handheld GPS devices and remote data access.
Such technologies not only simplify surveying processes, but data flow is streamlined between surveying instruments and construction machines as well as the field and the office. Ultimately this makes for a more productive jobsite.
User friendly
A key area of focus for surveying equipment manufacturers is to ensure complex technology in surveying devices is hidden away from the user - thereby making them simple and easy to use.
Simplifying surveying tasks is also vital given the fact that contractors are increasingly carrying out these tasks themselves due to reduced budgets and a lack of qualified surveyors working in the construction industry.
According to Karl Soar from Hexagon, the parent company of Leica, making software as user-friendly as possible is a common theme with all the major surveying equipment manufacturers.
He said with the increase in mobile computing power and communications technology converging in portable devices, the company has an opportunity to design ever more intuitive, "operator-centric" or "task-centric" software applications to make construction surveying tasks much simpler.
"The demographic in the business is changing, we can't always rely on having traditionally educated survey professionals on construction jobsites these days.
The advent of this new breed of survey technology means we can make what was traditionally rather complex equipment much easier for non-survey people to use - therefore, keeping machines moving and construction crews on the go," he added.
Mobile management
Portable instruments are undoubtedly increasing in popularity on the construction site. Like many GPS handheld devices, Leica's allow contractors rather than surveyors to carry out the staking out process.
Mr Soar explained, "The software will walk the user through the task of selecting which points he wants to set out and then provides an on-screen map or an arrow to tell him which way to go until he arrives within centimetre accuracy of the point he wants to stake out.
"Anyone who can work a mobile phone these days can switch on one of these devices and locate a point on a jobsite. By making it easy for the contractor you not only keep your crew moving but you also remove that delay in waiting for a survey crew to come from one side of a big jobsite to another," he added.
Topcon's Ian Stilgoe agrees handheld GPS and the development of mobile communication and data management is beneficial to contractors.
He added the company's GRS-1 is the world's first fully integrated dual-frequency handheld GNSS receiver and field controller with internal modem, high speed processor, built-in camera, compass and bar code reader. It also features wireless connectivity, Bluetooth or optional UHF radio pack as well as a SD memory card slot.
Mr Stilgoe said the GRS-1 "packs all the power of a full GPS plus Glonass dual-frequency receiver, celluar modem and Windows PC into a very small and versatile device for all applications."
He added forward-thinking contractors will invest in the device because it "meets all positioning needs."
Johan Smet, director of marketing for Trimble's Heavy and Highway division, told iC contractors have increasingly wanted to take control of their own stakeout and measurement needs, which saves both time and money as external sub-contractors can be expensive and not always immediately available.
According to Mr Smet, the Trimble Site Positioning Systems give contractors the flexibility to complete any task and the ability to reduce downtime by quickly resolving problems on site. This he added is achieved without office assistance or the need to rely on a surveyor for site measurement and stakeout requirements.
Central to the Trimble Site Positioning Systems is the Trimble SCS900 Site Controller Software. The software is available to run on all the company's handheld devices like the Trimble TSC2 and Trimble TCU as well as the new Trimble Tablet PC.
"This easy-to-use software helps you efficiently control and quantify site operations. It is easy to learn and can be used with Trimble GPS or total station positioning. You can use SCS900 software at every stage of construction," Mr Smet explained.
Worksite flow
The importance of exchanging data seamlessly between the field and the office and between construction equipment is increasing and this is reflected in new product development.
Trimble's Tablet, a "rugged, easy-to-use" handheld computer has built-in connectivity allowing jobsite supervisors, foremen, site engineers, grade checkers, construction site and project managers to compute in the field and connect to the office online.
The Tablet runs Microsoft Windows Vista Business as well as offering the contractor a choice of office software. It allows for large amounts of data to be processed with ease and performs office functions in the field, making overall workflow vastly more efficient, Mr Smet said.
Meanwhile, Trimble's Connected Community (TCC) is described by the company as the "information management backbone" of its Trimble Connected Site.
"It allows contractors to build information portals, share information and collaborate between head office management, site office teams, field crews, subcontractors, suppliers, engineers, clients and partners on a project," Mr Smet explained.
In addition, using web communication technologies, contractors can integrate head office, site office and field crew operations into a communication portal that allows information to be accessed by other project stakeholders, such as the finance team, the HR team, or senior management.
Remote revolution
Mr Soar told iC remote data exchange is one of the company's three main areas of focus in surveying and machine control.
"We are on the cusp of something very exciting there," he said.
"It has only been possible within the last 24 to 36 months to get fairly reliable, high-speed wireless data exchange - depending on which market you're in and where you are geographically. The ability to send reasonable sized files over wireless connections is really going to be the change enabler for this business."
He explained currently, when design changes need to be made they can be e-mailed to the contractor - but the final step of transferring the information onto the machine is carried out via a data card.
"You then get multiple copies of that data strewn across various devices and keeping all the data synchronised is a task in itself, for example if something gets revised in the field how can everyone involved be sure they are working on the latest revision of the design?"
He added nobody has the complete solution to this problem, but there is a move in the industry towards having more intelligent CAD models.
"The first step towards that for us is to have something like a web-based interface where the designer can post a file to a repository somewhere on the internet which then takes care of delivering it to the assigned machines or pieces of survey equipment on the jobsite. Remote data exchange is ultimately about quality and improving the speed by which you can move data around between the jobsite and the office," Mr Soar explained.
He added having the ability to remotely log-in and guide the user through tasks without having to drive 500 miles to physically be there has huge time and cost saving benefits for everyone involved.
Meanwhile, Topcon, in collaboration with RIB, has introduced a new system which directly links data to construction site equipment - including heavy machinery and surveying instruments.
Speaking for Topcon, Achiel Sturm said the company's central server - SiteLink - updates the status of construction work and supplies it in a transparent form to design and construction companies alike.
"To this server we link RIB's STRATIS software. The server transfers the incoming design data directly to the construction machines that are currently being used. So there's no need for e-mails, USB memory sticks and other interface-related exchange formats," he added.
According to Mr Soar, wireless and remote data exchange will remain important product drivers for Leica and its competitors. All the major players will be rolling out new developments within this area in the next 18 to 24 months, he added.
Outlook
Manufacturers of surveying equipment are confident that products which enhance communication and data flow on the construction site will continue to increase in popularity. The current weak state of the construction market is not deterring the surveying equipment sector from further advancing technologies that aid the contractor's work.
Mr Soar said, "The forward looking contractors are saying to themselves that this is the time to be investing in our equipment so they're ready for when the upswing comes and they can be more competitive against others when they come out the of this rather unfortunate period."
STAY CONNECTED

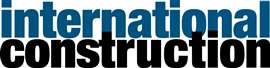
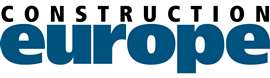
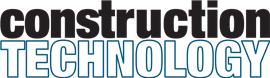
Receive the information you need when you need it through our world-leading magazines, newsletters and daily briefings.
CONNECT WITH THE TEAM
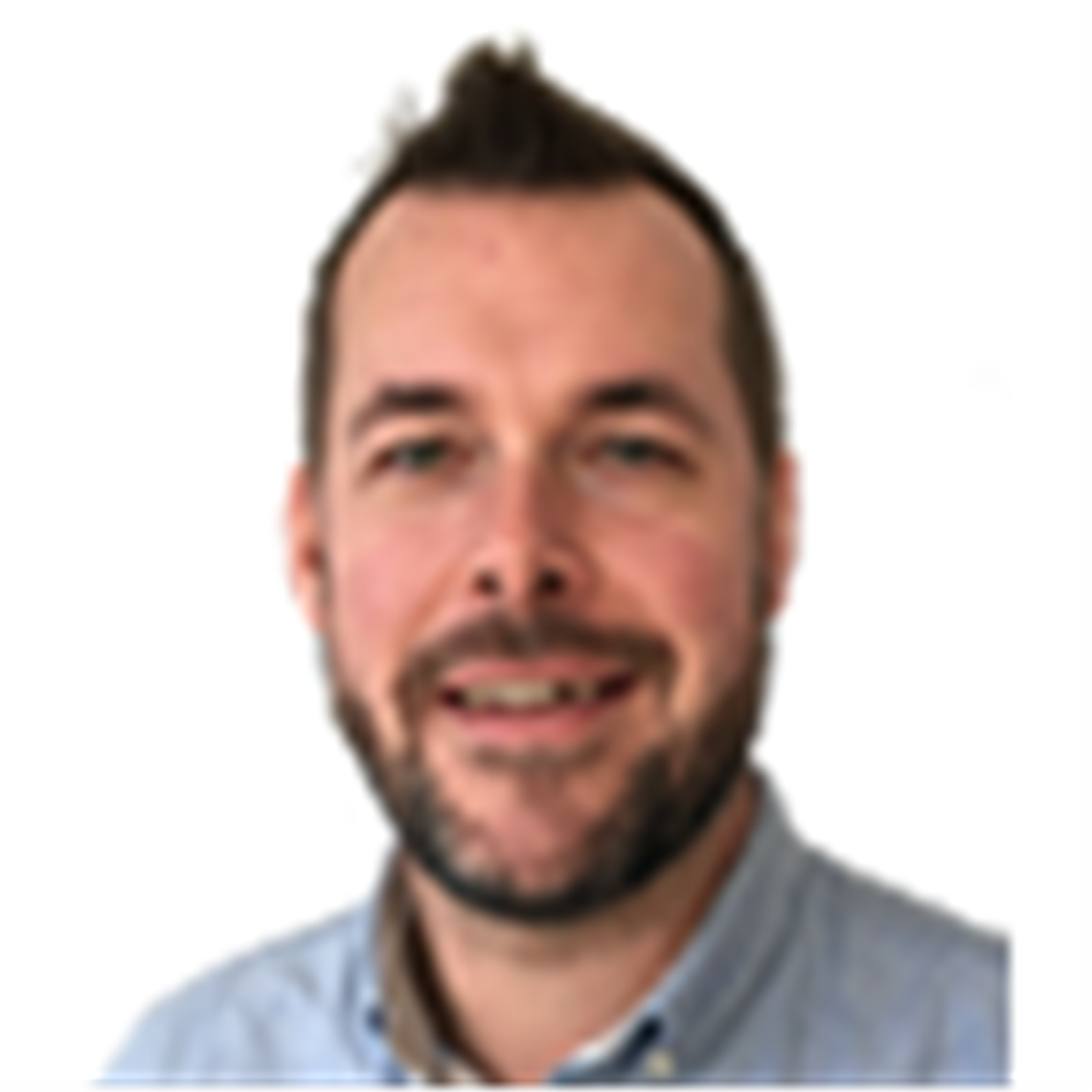
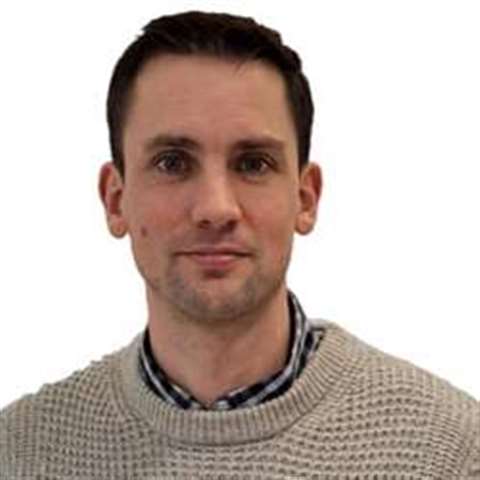
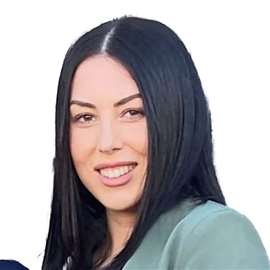
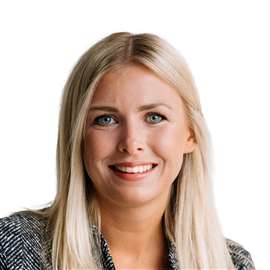