Roadbuilding: Project spotlight
09 November 2010
The road building sector is continuing its drive towards greater efficiency, more accurate monitoring and the increased use of recycled materials. Steve Skinner reports.
Current economic conditions may not be particularly favourable for the road building sector, but they are also driving innovation, with contractors forced to look at more cost effective ways of working and more efficient methods. The industry has also seen some help in the shape of government stimulus spending programmes.
One of the projects funded by the US stimulus programme is the rehabilitation of Tulsa, US's Inner Dispersal Loop (IDL) around downtown - the largest single project in the history of the Oklahoma Department of Transportation (ODOT) and largest stimulus-funded project in the US at the time of its letting.
Initiated in June of 2009, the US$ 75 million project encompasses reconstruction of all lanes of the west and north loop segments of Interstate 244 around downtown Tulsa and some surface repair to the other loop segments.
The job was won by a 60:40 joint venture between Manhattan Road and Bridge and Sherwood Construction. Manhattan Road and Bridge is responsible for nearly 80% of the project's bridge work, while Sherwood is handling the surveying, grading and removal and repaving of the IDL's roadways as well as the remainder of the bridgework.
The most critical work for the IDL centred on bridge reconstruction and paving. The north and west segments include 44 bridges that require significant repair. "A majority of the bridges are rated as structurally deficient," commented Travis Smith, resident manager - Tulsa Residency for the ODOT Reed Wood, general superintendent for Manhattan Road & Bridge, added, "Every bridge required removal of the deck to the top of the beams, and we fixed some of the substructure on those in worse condition."
The designs presented multiple challenges for the crews and bridge pavers. Several of the decks transitioned from a left slope to a crown to a right slope. Others had a continuous span that had to be poured by skipping segments so as to not overload the deck beams.
"Fifteen of the decks flared out from one end to the other more than 4.5 m. "One deck measured 4.9 m wider from one end to the other, and the total bridge length was only 45.7 m," recalled Mr Wood.
The main workhorse chosen for the project was a Terex Bid-Well 4800 paver. With its 1.2-m truss depth, the paver is capable of paving widths from 11 to 52.4 m without deflection. The 5.5-m end segments of the 4800 offer up to 4.5-m of leg travel to each side to handle bridge width flares.
The summer months in Tulsa see peak daytime temperatures exceed 40° C, and this meant most of the concrete pours had to be carried out at night. "We must keep the concrete below 32.2° C, so we poured in the early morning hours and ended by 9 a.m.," recalled Mr Wood.
To aid this, Manhattan Road and Bridge equipped the 4800 with an optional fogging system. Attaching to the finish pans, this system produces a true light fog of water o aid in finishing the concrete.
Micromilling
Meanwhile in Nebraska, US, the state is looking at more cost-effective ways of repairing minor damage to roads. Nebraska's Department of Roads (NDOR) is using a process called micromilling, or profiling, to remove shallow ruts in its Interstate highways, and it has found the method to be a cost effective solution.
"If we're starting to get a rutting problem, we don't have to do a really deep milling job," said Tom Anderson, a project manager for the NDOR. "We get a smooth surface. Profiling takes the ruts out and doesn't tear up the surface. We get a lot smoother ride than with conventional milling."
To achieve this smooth finish, a milling drum with a huge number of teeth is required. According to Roadtec, which has supplied one of its RX 900 models to such a scheme, the 12'6'' (4.58 m) wide drum it has supplied has 840 teeth, compared to 271 on a normal drum.
Werner Construction of Hastings, Nebraska used such a machine for a two-part project to repair two 6-mile (9.6 km) stretches of the I-80 highway. "We just milled enough to take the ruts out, no more than a half-inch [13 mm]. The milling teeth just barely touched the bottom of the ruts on the highway," said project superintendent Ken Kalvoda.
Jerrid Fuehrer was an Inspector for the NDOR on the project. "The asphalt itself wasn't bad. All that it needed was to put it back to the original profile," he said.
According to Mr Fuehrer, the process cost US$ 25000 per lane mile. This compared to US$ 165000 per lane mile to mill to a depth of 1.5 inches (38 mm) and lay 2 inches (51 mm) of hot asphalt afterwards.
However, John Irvine, Roadtec's vice president of sales and marketing cautions agencies against thinking that micro-milling can replace conventional milling for all purposes.
"The labour costs of changing drums and the additional horsepower and fuel must also be taken into account. We just don't want agency people to specify this process thinking it doesn't cost them anything - or without evaluating the cost versus benefit of micro-milling."
Pilot project
Meanwhile in Germany, civil engineering contractor Bunte spent the summer hard at work on upgrades to the A1 motorway between Bramsche and Osnabrück/North, working round the clock to meet tight schedules.
The project was a pilot scheme in Germany, with the new asphalt being produced entirely from recycled material removed from the existing road - a total of about 200000 tonnes over an 8.4 km stretch.
Quality and quality assurance was crucial so project supervisor Jürgen Schimang turned to Bomag and its Asphalt Manager II system to monitor the laying of all three layers - surface, binder and base layer. In addition, some stretches saw the top two layers placed simultaneously using the 'hot on hot' process.
Asphalt Manager measures parameters like surface temperature and the effective amplitude of the roller via a graphic display, so the operator can select the right roller mode for the layer being compacted.
It is an automatic system, but at the same time the roller operator can follow changes in surface temperatures to make sure he is always working in a hot zone.
On this scheme, density measurements were also made using a probe from Troxler, and these were used to calibrate the results from the Asphalt Manager software.
These supported the fact that the rollers were achieving the correct degree of compaction, although in some cases poor weather conditions meant the mix cooled quicker than expected, and there was only a narrow window in which to compact the asphalt.
New build
Western Australia asphalt specialist BGC Asphalt, is using a Dynapac F6-4W paver to lay roads on the last few remaining sub-divisions of Ridge Wood residential development in Brighton, the latest northern suburb of Perth, Australia.
BGC's latest contract, sub-contracted by earthmoving specialist R J Vincent, features laying 6000 m2 of asphalt over three days. A 40 mm base coarse with 14 mm aggregate will be topped by a 25 mm wearing course - both sitting on a 200 mm limestone sub-base.
Backing up the Dynapac paver is CP142 pneumatic tyred roller and a CC142 twin drum compaction roller. Across the sub-division, roads are generally 5.5 m wide often with 2.2 m wide parking bays. Outside the sub-division main roads can be 6 m or 7.4 m.
According to gang supervisor, Mick Sheahan, the Dynapac paver is simply "beaut". He elaborated, "By fitting the extensions, the paver can offer a 3.8 m width making it highly versatile for any road work in the suburbs."
On the sub-division contract the paver is followed by two vibratory passes by the CC142 and multi-passes with the CP142 until the surface is "firm". The CC142 then makes two final vibratory passes to remove the possibility of any tyre marks made by the CP unit.
According to Mr Sheahan, depending on the paving speed, pass lengths of around 20 m are made, although, "this can be increased to 80 m subject to the ambient temperature and weather conditions."
"The slide plates are the best ever, just perfect for laying up to the flush kerbs and so easy to set."
"Although only delivered last year, the paver has clocked more than 410 hours, testament to how highly we rate it. The paver is just a fantastic machine," he concluded.
Service oriented
In a different type of new build project all together, Caterpillar has supplied two RM500 rotary mixers to Portuguese contractor Mota-Engil, which is using them to upgrade a 70 km section of Mozambique's national road between Maputo and Beira.
The work involves stabilising the soil with a mixture of cement and water, and the machines are progressing at a rate of about 6 m to 7 m per minute, working to a depth of 180 mm. They are then followed in the train by soil compactors and graders, and finally by pneumatic tyred rollers to finish the surface.
As part of the support package, Caterpillar commissioning engineer Davide Della travelled to Mozambique to commission the units. This involved three days of training with operators and technicians, as well as taking the machines to a practice site where crews could learn to use the machines and set key parameters like setting the right amount of flow through the water pump.
Once the crew was trained, Mr Della went with the machines to site to get them started on the project. "When I left the job-site after my commissioning, the Rotary mixers were perfectly running, set in working mode and the crew perfectly comfortable with the use of the machines," he said.
Work to renovate the 70 km stretch of road is expected to take two years, with the project requiring two layers of overlapping stabilised soil to be created, which will be suitable to receive the final chipping spread.
Trans-Siberia
A project facing a very different set of environmental challenges is section M58 of the trans-Siberian highway, the eastern most 2000 km of the road between Khabarovsk and Chita in Russia.
Although it was officially opened in 2004, many stretches were little more than dirt tracks, and some 1000 km remained unpaved.
The challenges involved in completing this project are immense. Besides the 200 bridges along the route, construction is hampered by the fact that temperatures can fluctuate up to 100° C from high to low throughout the year.
The coldest point on the route is the village of Mogocha, where January temperatures average -30° and can be as low as -62°.
However, it is three hours south from here that an Ammann JustBlack asphalt plant has been set up to produce several million tonnes of material over the next two years.
Despite being in the middle of nowhere with no running water, electricity or mobile phone signal, Ammann's engineers had the plant up and running just four weeks after the first components arrived.
Paving the final sections of M58 is expected to be completed in 2011, providing an unbroken 10000 km road all the way from Moscow to Vladivostok.
Efficiency drive
These different projects may illustrate the different requirements around the world, depending on the state of existing roads, the climate and so on, but they all have a common thread of contractors looking to their equipment to make the road building process as quick and efficient as possible.
STAY CONNECTED

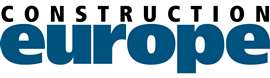
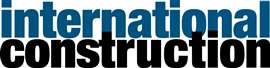
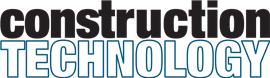
Receive the information you need when you need it through our world-leading magazines, newsletters and daily briefings.
CONNECT WITH THE TEAM
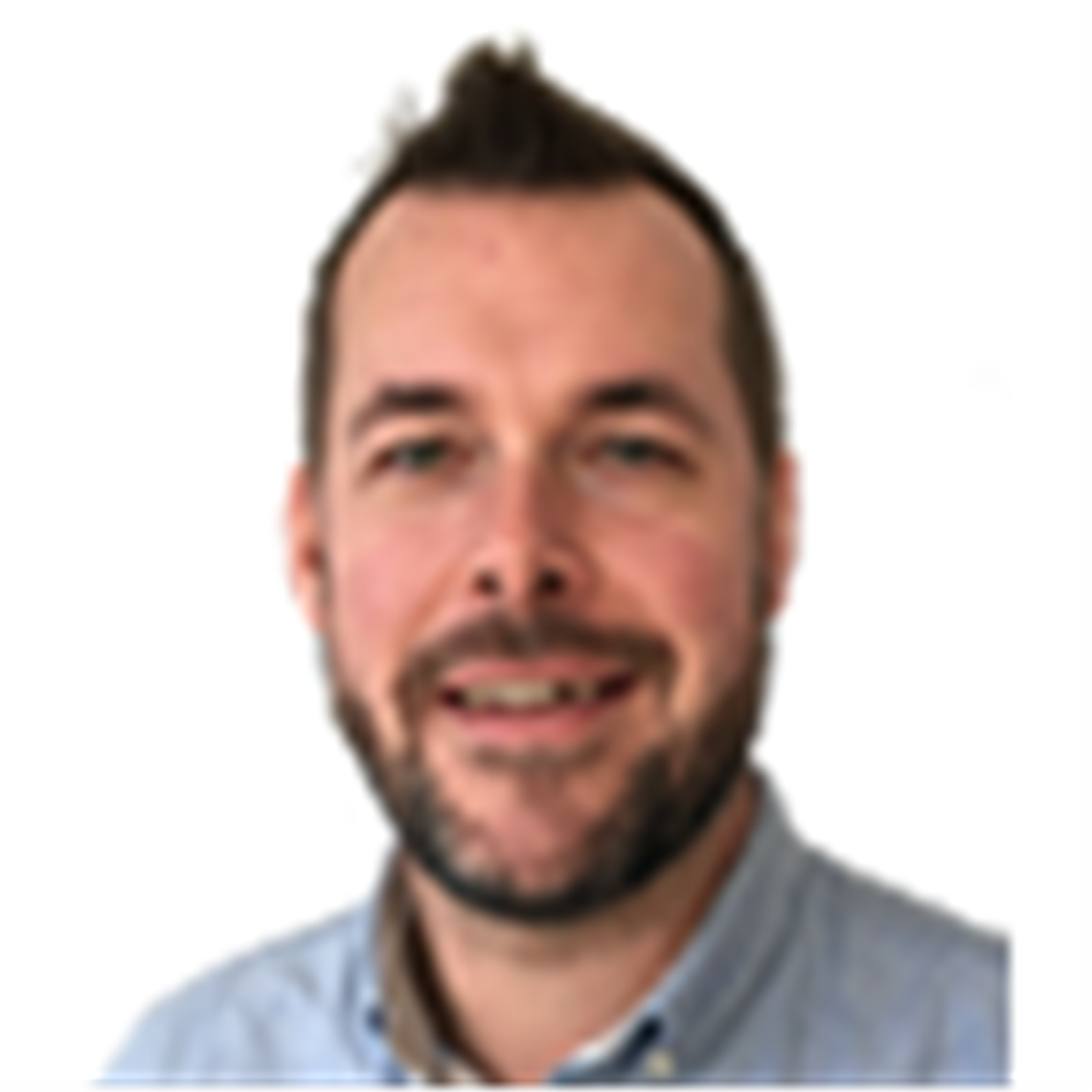
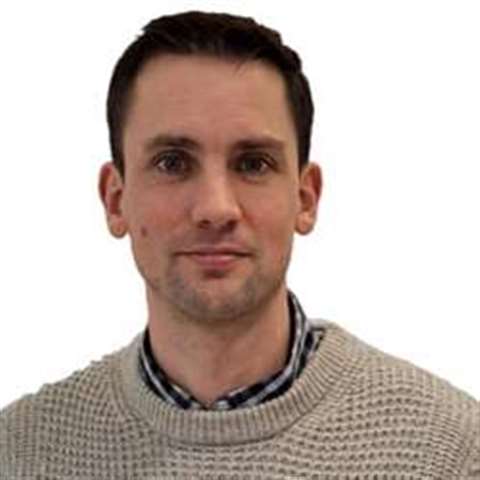
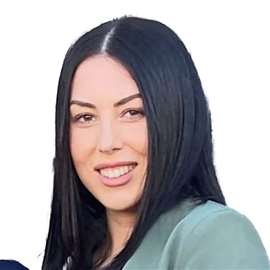
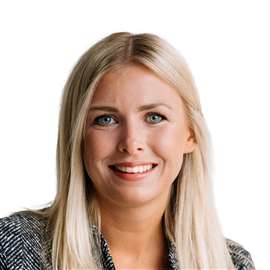