Pumps: Flooded with choice
08 August 2018
When it comes to selecting the right de-watering pump for a construction job, it is becoming increasingly relevant to question whether diesel or electric is the appropriate power source to use.
However, according to Atlas Copco, it is not a contest of technical supremacy to establish an outright winner, rather it is a common-sense selection process based on matching equipment performance and capability to all aspects of the particular job. Within this process, critical factors to be taken into account include the required volume, flow and head specifications, and the constitution of the water and materials to be pumped.
Also, when evaluating the pump capability required, variables to be considered range from the operational conditions and site access, to the project’s duration and environmental concerns.
Looking first at the advantages and disadvantages of diesel-powered centrifugal pumps, Atlas Copco said they were sturdily built for endurance and reliability. They are designed for handling large volumes of water discharge, so the operating flow range is typically between 50 and 830m3/h, with a head of up to 51m.
They are versatile, able to cope with a wide range of materials, and fully-automatic self-priming centrifugal pumps were said by Atlas Copco to be the ideal solution for transporting or raising water with abrasive solids in suspension. Their solids-handling capacity can reach up to 76mm is size due to features such as semi-open impellers and abrasion-resistant pump casings.
They are the obvious de-watering solution in scenarios where alternative power sources, such as mains power or generators, are not available. In addition, these pumps are able to operate in a high variable speed range, allowing them to cover different applications and flow/head combinations.
Together with an average fuel autonomy of up to 47 hours, Atlas Copco said that an oil-free diaphragm vacuum pump’s automatic priming makes continuous drainage possible even with significant volumes of air. Some pumps can also be equipped with an extra-large fuel tank so that they can run for longer periods without refuelling.
Maintenance was also said to be easy, with just the replacing of wear parts and engine filters, and part of the appeal to rental organisations was the inclusion of advanced controllers with the capacity to monitor data.
Portability
Turning to electric submersible de-watering pumps, they can offer portability and ease of handling, and they are generally available in a power rating and capacity range that make them well suited to mining, construction and ground water control, according to Atlas Copco.
Also, they can be useful in applications where diesel pumps simply cannot be used, such as in underground mining or jobs where emissions are prohibited. They also offer a quieter alternative that can be run in populated areas or during night-time operations.
Providing hours, and even days, of unattended de-watering pump operation, submersible pumps were said to be able to meet the demanding requirements of raising water from great depths or lowering water tables in tough environments. Atlas Copco said that some models were capable of running for up to 2,000 hours without attendance.
Since they are sub-surface units, electric submersible pumps can continue to work beneath ice, so long as the pump is completely submerged.
Durable
Electric pumps are also durable, offering high wear resistance, and their modular design simplifies maintenance procedures. Atlas Copco said that some models could be equipped with on-site servicing and parts replacement kits, including seals and impellers.
At present, manufacturers offer medium- to large-capacity ranges that deliver maximum power ratings of around 54kW and that can typically manage flows of between 225 and 16,500 litres/m with a maximum head of 85m, according to Atlas Copco. However, some higher-head pumps are available.
Electric submersible de-watering pumps used in particularly demanding applications should be equipped with hardened impellers to handle suspended solids.
Water technology company Xylem was recently called in to help construction company Sade choose the right pump for a project at a wastewater treatment plant in the town of Mainvilliers, France, which was built to replace an old watertreatment plant in the neighbouring French commune of Lèves, which was no longer fit for purpose.
As construction work on the new plant drew to a close, Sade – the company supporting the construction project on the sewer – had to connect the existing sewer inlet at the old plant to the new one. For the work to take place without disrupting operations at the pumping station, a temporary bypass pumping solution had to be set up to divert incoming wastewater.
Xylem deployed a team of engineers to work alongside Sade, delivering a customised solution.
Two Godwin CD225M diesel pumps and a Godwin Dri-Prime CD400M pump were used on the site to maximise efficiency and flexibility for the fluctuating wastewater flow levels.
The three pumps offered a combined flow capacity of 2,700m3/h, exceeding the maximum flow level of 2,680m3/h usually dealt with by the plant.
The Godwin pumps were fitted with variable frequency drives so that operators could control the motor speed and reach the required duty point to optimise operating efficiency.
To support the bypass, Xylem supplied 12 400mm pipes measuring 3m in length to safely channel the discharge away from a nearby river and thereby avoid environmental damage.
At another wastewater treatment plant, this time in Stuttgart-Mühlhausen, Germany, an old sludge pump system is due to be replaced by one of Schwing Stetter’s solutions.
The plant services about 1.2 million residents in the area and is showing significant signs of wear.
In the solution from Schwing Stetter, the sludge delivered by trucks to the 40m3-volume receiving bunker will be transported by a KSP 65 HDR pump with an SD 350 HD double-screw feeder and course material separator. With its Rock valve, it can pump sewage sludge with a high proportion of coarse material.
The conveyed material will then be pumped over a distance of 20m into a silo before being fed by another KSP 65 HDR pump with an SD 350 HD double-screw feeder over a distance of about 100m for drying and combustion.
Fish-friendly
Over the border, in the Netherlands, new environmentally-friendly – and fish-friendly – pumps are being installed as part of a €550 million project to refurbish flood defences along the 32km-long Afsluitdijk, which has been protecting large parts of the Netherlands from flooding since 1932.
Rijkswaterstaat – the part of the Dutch Ministry of Infrastructure and the Environment that holds responsibility for the design, construction, management and maintenance of the main infrastructure facilities in the Netherlands – selected the Levvel consortium, which comprises Van Oord Aberdeen Infrastructure Partners, with a 46% stake, Bam PPP PGGM Infrastructure Coöperatie, also with a 46% stake, and RebelValley, with an 8% stake, to carry out the work.
The contract is for the design, construction and financing of the project, as well as 25 years of maintenance work.
The works will include the strengthening of the dyke with innovative concrete elements and the installation of new pumps to expand drainage capacity – at present, the area drains solely through natural flow. Levvel’s discharge solution has been designed to consume as little energy as possible, using pumps only when necessary. The existing monumental Spuisluizen (drainage locks) in Den Oever will remain intact but will be renovated.
Once reinforced, it has been said that the Afsluitdijk will be able to withstand a storm that occurs once in every 10,000 years.
The pumps were said to be fish-friendly, and a floodgate of fibre-reinforced plastic will be installed in the river along which fish are known to migrate.
Construction work is expected to start in autumn of 2018 and finish in 2023.
Pumps often have to handle large solids found in flooded exactions on jobsite or on flooded roads and in tunnels, which is why UK-based Hycon supplies a range of hydraulic submersible trash pumps available in 5, 7.5 and 10cm discharge sizes and that use the company’s vortex system.
The 5 and 7.5cm pumps were said to be particularly well-suited to construction job sites and for any mobile general pumping purpose where it is easy to submerge the pump into the water or slurry. Requiring only between 30 and 40 litres/m of hydraulic flow, the pumps can be operated by petrol, diesel or electric power packs, including compact portable powerpacks that are used for breakers, cut-off saws or core drills.
Hycon’s hydraulic submersible trash pumps can run dry because they are cooled and lubricated from the hydraulic power supply, and they were said to be used by various utility contractors for pumping jobs that include services on water systems, de-centralised heating, wastewater plants and drainage lines.
A new heavy-duty trash pump was recently introduced by Australian Pumps. The 15.2cm MQ62TD was said by the company to have the potential to change the way de-watering is done on construction sites.
According to research conducted by Australian Pumps, 80% of the de-watering jobs on construction sites can be carried out using pumps that are self-priming and do not need either compressors or vacuum-primed systems.
Yet, dry primed pumps are traditionally used, and John Hales, the company’s chief engineer, said, “Those priming systems can be troublesome.”
The MQ62TD was said to deliver a flow rate of 4,100 litres/min and can achieve a 30m head when driven by a 22kW diesel engine.
Cast iron
Made with heavy-duty high-SG cast iron, the body incorporates a large priming tank that was said to enable the pump to prime quickly, even at depths of over 7.5m.
Another important feature is the large front cleanout port, which can be opened quickly to clear blockages without disturbing the pipework.
The pump was said to be able to handle a wide range of duties on construction sites, and with its non-clog impeller it can handle solids measuring up to 5cm in diameter. It was also said to be ideal for handling sandy slurry liquids.
Hales said, “Dry prime pumps depend on compressor or vacuum pumps to work. By contrast, simple self-priming is more reliable, less costly and easier to maintain.”
Another environment that poses challenges of its own is in mines, where specialist pumps are used for de-watering.
Germany-based Netzsch Pumps produces mine de-watering pumps and pump skids that come with small and compact movable units.
Included in their offering for mining applications are the Nemo progressive cavity pumps and the self-priming, valve-less Tornado T2 positive displacement pump.
The company’s base mine de-watering pump skid unit has a tank, a progressing cavity pump with right-angle gearmotor, an inspection ladder, valves and piping – all mounted on a common galvanised steel skid. It also has the option of being fitted with a control panel and instrumentation that includes high/low level switches for the tank and dry-run protection for the pump. Individual pumps are available for retrofitting on existing skids.
The tank features baffle/divider screens to filter out any solids that are too large to fit through the pump, and the pump itself is located to the side of the tank, enabling easier access and maintenance.
The right-angle gear motor on the standard unit was said to save space and eliminate the need for a belt drive – though, belt and pulley designs are also available.
For improved operator safety, the removable inspection ladder on the pump has handrails and the tank comes with a removable safety screen.
Depending on the specific needs of the contractor, the units are available with a wide range of flow and pressure capabilities, and the pump and tank can be constructed from a number of different materials, such as carbon steel, stainless steel, galvanised steel and Halar/rubber-lined steel.
STAY CONNECTED

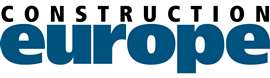
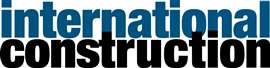
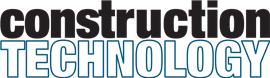
Receive the information you need when you need it through our world-leading magazines, newsletters and daily briefings.
CONNECT WITH THE TEAM
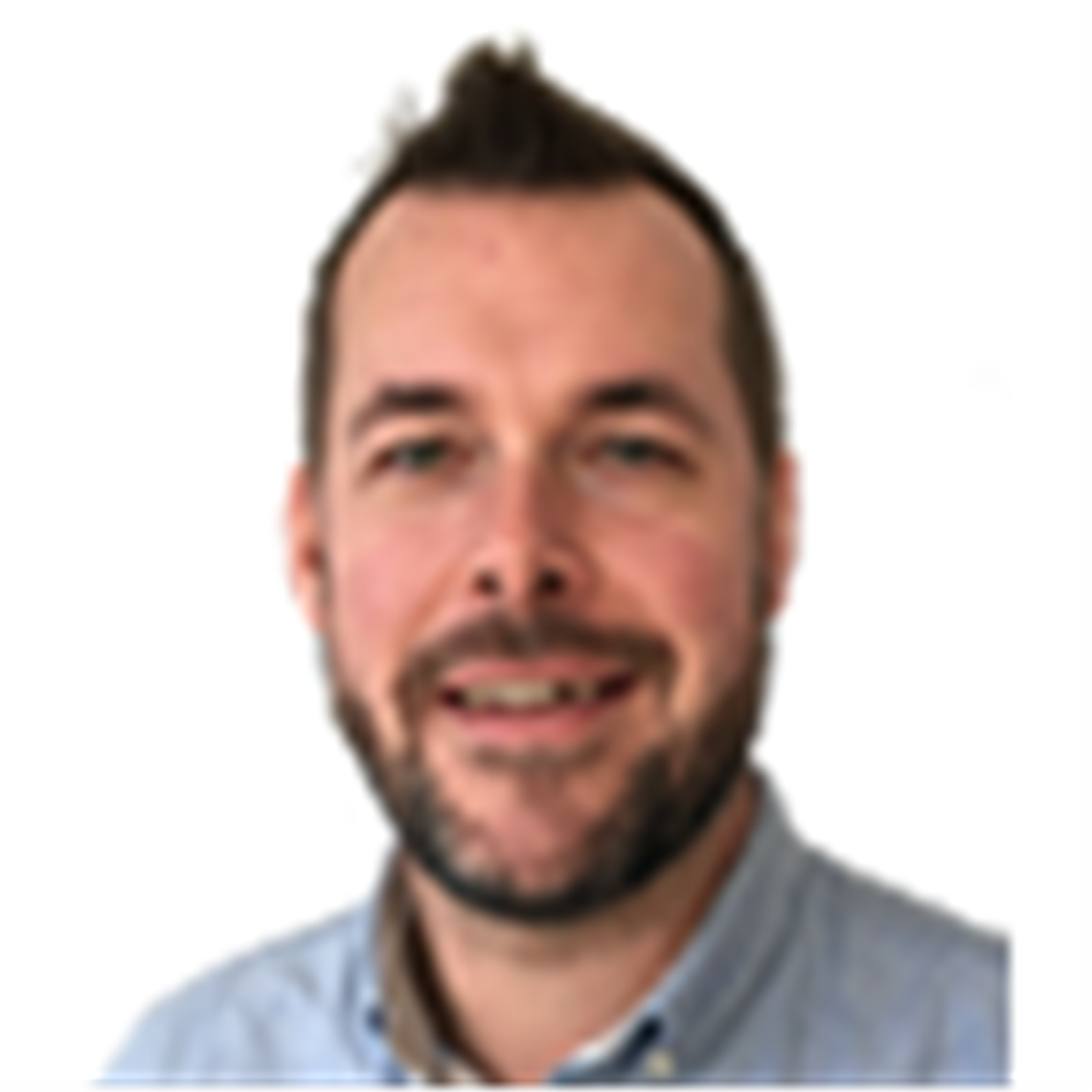
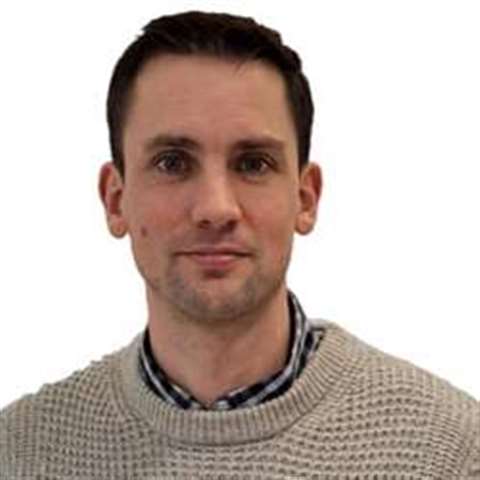
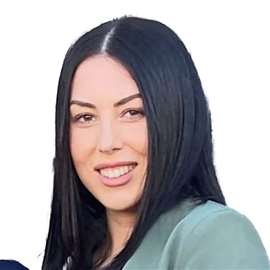
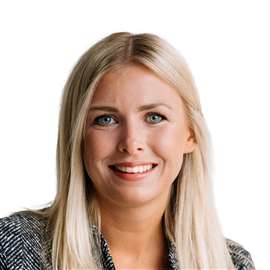