Milestones in high-rise construction
11 September 2012
Iconic high-rise buildings continue to appear in cities around the world and figures from construction data company Emporis show the world's top ten tallest buildings currently under construction have an average height of 566 m - that is 77 m more than the average for theten highest skyscrapers completed in the last decade.
With a height of 828 m, only the Burj Khalifa in Dubai, UAE, would keep its Number 1 position in the existing top ten once the current generation of skyscrapers are completed, and even then it looks likely to be surpassed by a new neighbour designed by the same architect, Adrian Smith + Gordon Gill Architecture, in the coming years.
Indeed, February saw the Saudi Arabian government grant the final permits to allow construction of the Kingdom Tower in Jeddah to go ahead. At 1 km tall, the SAR 4.6 billion (US$ 1.23 billion) sky scraper will take over as the tallest building in the world on its projected compeltion in 2018.
The brainchild of Prince Alwaleed Bin Talal Bin Abdulaziz Alsaud, chairman of investment company Kingdom Holding Company (KHC), contractor Saudi Bin Laden Group has been named as the main contractor on the Kingdom Tower project.
While Saudi Arabia appears to be the most ambitious in terms of planning the giants of the future, current data shows that nine out of ten of the tallest planned skyscrapers currently under development are located in Asia, with six of those in China and two in South Korea.
The only 500 m+ skyscraper currently under construction in the western hemisphere is One World Trade Center in Lower Manhattan, New York, US. Even though the building has not yet reached its full height, it is already the tallest structure in New York, and when complete in 2013, the 541 m tall structure will rank 6th in Emporis' list.
But rising overall construction height is just one of many factors to deal with on high rise construction projects these days.
In addition there are tight schedules, restricted site conditions, hybrid construction methods of heavy steel structures combined with reinforced concrete and the extraordinary architectural ambition of some of the latest buildings. All of these factors demand ever more sophisticated and tailor-made approaches in terms of the construction equipment used.
Formwork
For instance, the World Trade Center development, which will feature four new skyscrapers in total, is a prime example of how the falsework and formwork equipment used to construct modern skyscrapers must be adaptable enough to meet the challenges presented by the latest designs and the available space to build in.
Falsework and formwork manufacturer Doka is supporting the final stages of construction of Tower 4, for example, which will stand 72-storey, 297 m tall alongside the iconic One World Trade Center Tower and three other high-rise buildings that form part of the redevelopment of Ground Zero.
Doka Senior Account Manager for Tower 4 Mike Schermerhorn described Tower 4 as one of the more difficult skyscrapers being built at Ground Zero.
"The differing storey heights, varying layouts and wall thicknesses, and the logistics, all present us with some really big challenges," he said.
Architecturally, this office tower resembles a parallelogram up to the 47th floor, above which the storeys have a trapezoidal layout up to the 63rd floor, before tapering to its full height. Once completed in late 2012, Tower 4 will be the fourth-tallest skyscraper at the Ground Zero site.
Like most skyscrapers in New York, Tower 4 has a steel frame supported by an internal concrete core and stabilised by mega-columns on the outside. Installation of the steel frame takes place between six and eight stories above the core. This makes co-ordination of the structural-steel and concreting works a key challenge.
To increase productivity, the 27 m by 27 m structure of the core of the tower, which will house the stairwell and elevator-shafts, has been divided up into four casting sections. Doka's SKE100 automatic climbing formwork is being used to help construct the core, repositioning the large working platforms and the formwork units assembled from Doka's Top 50 large-area formwork.
SKE100 has a load capacity of 10 tonnes per climber, and is also being used for the 'mega-columns' on the outside of the structure.
In Nigeria, too, self-climbing technology is being used to construct the 100 m tall Nigerian Central Bank in the capital, Lagos. The 21-storey structure is being built next to neighbouring buildings, presenting contractor Julius Berger Nigeria (JBN) with extremely cramped site conditions.
With only three cranes were available for the shell and finishing work, JBN opted to use Peri's RCS self-climbing system and VARIO GT 24 girder wall formwork to create bespoke, climbing formwork units to construct the main core of the building.
Peri specialists dimensioned the climbing formwork units so that they could be used almost unchanged over the complete height of the building in spite of the geometrical variations in the structure. The falsework for building shell facade was Peri UP Rosett Flex modular scaffold, which was also adapted to the complex geometry of the building.
Cranes
Flexibility is also a core demand of tower cranes, which must also keep up with the challenges of modern architecture. Easy maneuverability and quick assembly are also key areas of
focus here.
In India, for example, a joint venture between Arabian Construction Company and Simplex Infrastructures is building the World One Tower in Mumbai for Indian real estate developer Lodha. At 443 m, the INR 2200 crore (US$ 440 million) project will be the tallest residential tower in the world it reaches its final height of 117 stories in 2014.
The contractors opted to use three Potain MR 160 C cranes to support construction. The luffing jib cranes must lift the 250000 m3 of concrete, 35000 tonnes of steel rebar and
40000 m2 of glass that will make up the World One Tower. To meet the demanding workload of the three-year project, the cranes are working at their maximum capacity of 10 tonnes.
Positioned within the building's superstructure as internal climbing cranes, they are configured with 40 m jibs and will eventually reach heights of more than 460 m to the summit of the building. As the cranes climb, they will be supported by beams and clamps to ensure maximum stability and safety.
Working at such heights in close proximity to one another requires precise load control. The Mumbai climate, with temperatures of up to 38˚C and a lengthy rainy season, adds to challenge. So the cranes are fitted with Potain's Ultra View cab, which ensures operators are comfortable and have an uninterrupted view of the site.
Satya Narayan Bhattacharya, deputy general manager of Simplex Infrastructures, said, "We are using another brand of crane at a neighboring site, and our contractor can clearly
see how much quicker the Potains are to erect. The pin
connection system makes mast assembly quick and efficient. In addition, the Potain self-climbing function and impressive capacity have made these cranes the perfect tools to complete this landmark project."
Trends in terms of high-rise design can vary widely from country to country, and this in turn influences the design of the tower cranes used in their construction. In India, for instance, the trend is for tower cranes with internal climbing configurations and maximum working loads to 5 tonnes, with maximum radii of about 50 m, according to Liebherr.
David Griffin, director of sales and service for tower cranes at Liebherr India, said, "In India, especially Mumbai, there is a huge amount of high-rise construction. The footprint is often quite compact, which means that by placing an internal climbing frame with a 50 m radius you can get a good coverage of the building and material yard."
The Liebherr LC tower internal climbing kits were developed with the Indian market in mind. "Our towers are so compact and fit in openings of 1.95 m by 1.95 m. We find common residential buildings have small footprints with two to four lift shafts. The cranes that we are developing have major advantages. They are equipped with hoisting gear for achieving very high hook heights, for example, our 71 EC-B 5 can achieve a maximum hook height of 278 m."
Liebherr said lean construction methodology was another key trend in the high-rise sector. For instance, just one Liebherr 110 EC-B flat-top crane is being used to erect six tower blocks for a residential project in Bogota, Colombia.
Contractor Constructora Triada's project manager Luis Guilermo Velez said that, in the current phase of construction, the blocks were 15 storeys high and stood directly adjacent to each other, allowing the crane to reach all areas of two blocks simultaneously.
The 110 EC-B has an under-hook height of 47 m, a boom length of 55 m, and a maximum lift of 6 tonnes. At La Alameda the crane is free-standing, with a single tie, placed in front of two adjacent towers.
"We are able to build one floor per tower during the course
of two days," Mr Guilermo said. "We are on the final two
towers now."
"One of the aspects lean construction has taught us is that with the correct specification of tower crane, and with the crane utilised correctly, we can save on time and costs without sacrificing quality," he added.
Customised models
Five customised tower cranes from Terex have also been working for nearly two years on a high-rise project in Milan, Italy. Four Terex CTT181B-8 TS 21 models and one Terex CTT331-16 TS23 model are helping construct two residential towers as part of a large restructuring and re-design of the city's Porta Nuova - Isola district.
Italian contractor ZH GCC is building the two residential towers, which are 16 and 23 storeys (80 m and 106 m) high, and worked with Terex to plan the positioning and layout of the tower cranes from an early stage. The goal was to provide maximum jobsite coverage while maintaining operational efficiency.
Two of the CTT181B-8 tower cranes were custom fitted with a shorter jib of 30 m, but Terex said the CTT331-16 represented the biggest challenge. Due to the height difference between buildings, when the two towers were almost completed, the CTT331 had to be climbed to a final height of 140 m to serve both. As there was no possibility to tie the crane at this height, ZH GCC and Terex application engineering team came up with a bespoke solution - a guyed collar section tied to both buildings.
ZH GCC CEO Werner Zimmerhofer said, "The CTT 331 stands out for the operating speed and has an 8 tonne capacity; whereas the CT 181s are easy to operate and in my opinion are the most reliable in their category. Terex proved to be the right choice also for their support even before the work began, understanding the project and taking care of assembly, thanks to a team of expert fitters who provided all necessary logistical support."
It is clear that construction equipment manufacturers are prepared to work very closely with contractors and structural engineers to develop a bespoke approach to constructing high-rise buildings. And as the world's cities get fuller, demand for high rise buildings looks set to continue both as residential responses to the pressures of space, but also as potent commercial symbols of the economic successes of an area.
STAY CONNECTED

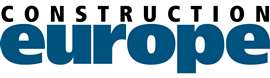
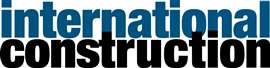
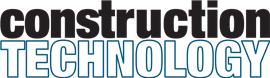
Receive the information you need when you need it through our world-leading magazines, newsletters and daily briefings.
CONNECT WITH THE TEAM
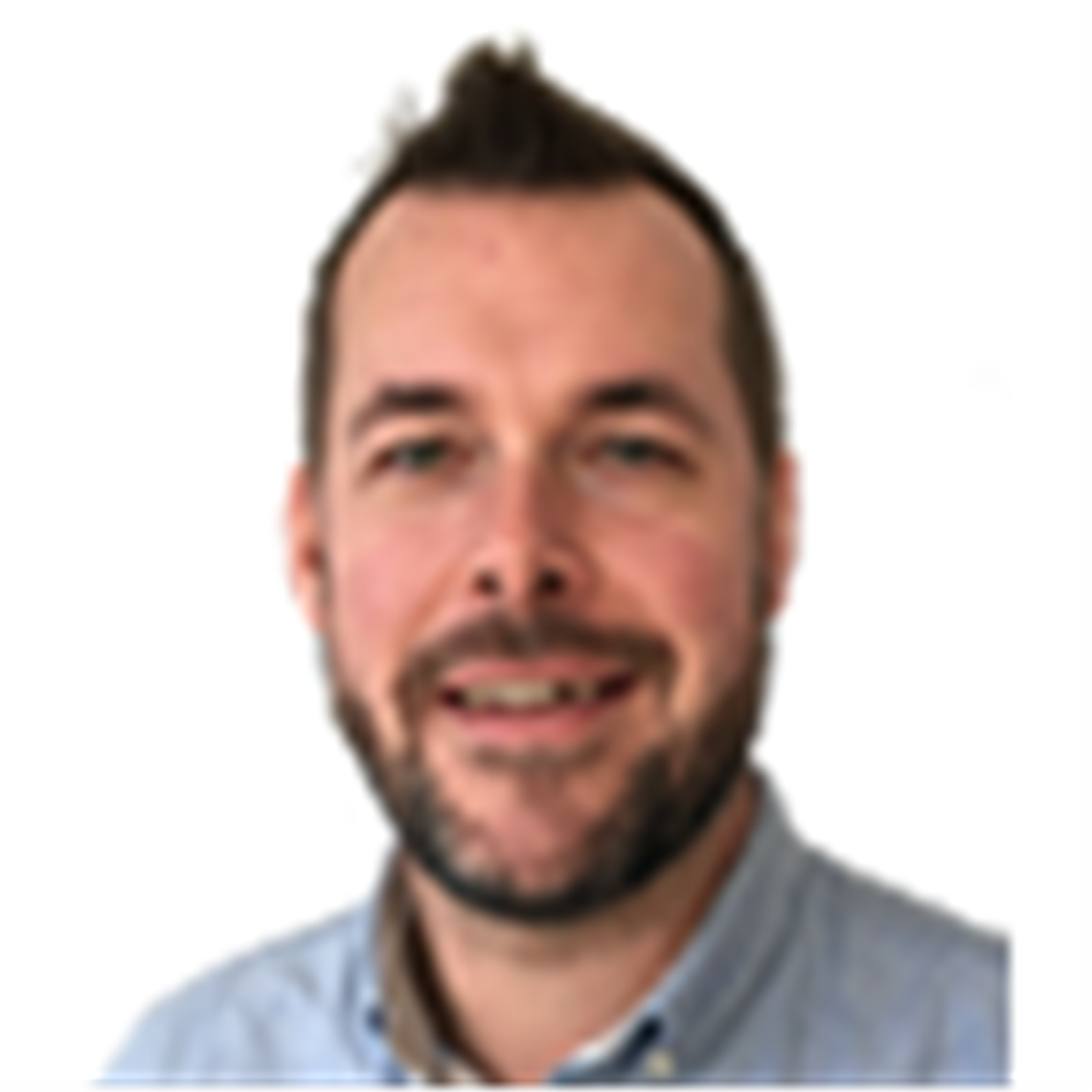
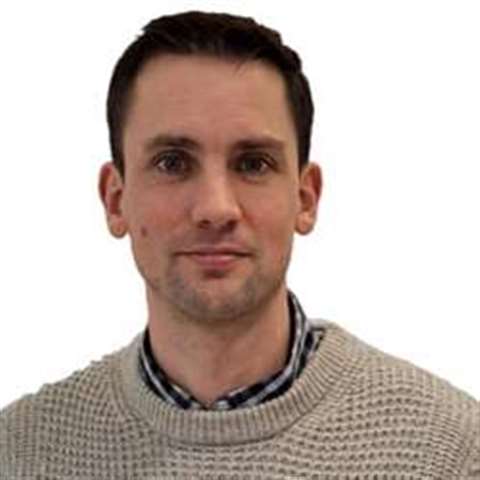
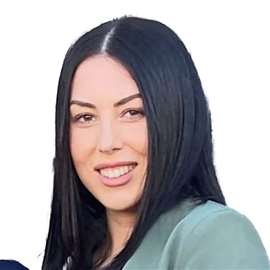
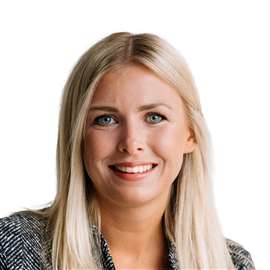