Latest low emission wheeled loaders
07 September 2011
As with other types of construction equipment , the new Interim Tier 4 engine emission laws in the US, and the European Stage IIIB equivalent are driving a run of new product launches in the US and Europe. The start of this year saw the first step of the anti-pollution measures applied to 130 kW to 560 kW engines, which translates to machines with about a 2.5 m3 bucket or larger.
The next two years will see the new requirements extended in two steps down to 37 kW engines, which will cover the smaller classes down to about 1 m3 capacity machines.
The main focus of the new laws has been to reduce particulate matter (PM) from engine exhausts. This is the black soot that many people would associate with diesel engines, and as a pollutant it has an impact on air quality and human health.
Most manufacturers have gone for a solution based around a diesel particulate filter (DPF) in the exhaust system along with existing pollution control systems around the engine, most notably exhaust gas recirculation (EGR). The large DPF 'cans' contain a ceramic honeycomb that physically traps the soot particles. As the soot builds up, it is either burnt off as part of the machine's normal operating cycle (passive regeneration) or fuel is added and ignited to dispose of them (active regeneration).
This has of course added price and complexity to equipment and it has also made the global market more complicated. In order to run correctly, loaders with Interim Tier 4/Stage IIIB engines must be fuelled by ultra low sulphur diesel (ULSD), which means less than 50 parts per million (ppm) of sulphur and often less than 15 ppm. Using high sulphur fuels will clog the DPFs, increasing the back pressure on the engine and causing overheating, perhaps damaging them permanently.
In the market for new machines, this shouldn't be a problem. Interim Tier 4/Stage IIIB loaders will only be sold by manufacturers and their dealers in markets like Europe, Japan and the US, where regulations demand them and where the correct fuel is available.
However, things may become more complicated in a few years, when these machines start to be sold as used equipment in other parts of the world. Buyers will have to be very careful that they do not buy Interim Tier 4/Stage IIIB machines if the equipment is going to be used in an area where low sulphur diesel is not available. It would be a very expensive mistake!
Loader manufacturers are aware of this problem, and they say it should not be too technically challenging to 'de-tier' exhaust systems to allow engines to run on poorer grades of fuel in less regulated countries. However, there are several legal questions over this - would the modified engine need to be re-tested and approved before it was legal to use it in a new country with different emissions regulations, for example? It is a question that remains unanswered at the moment.
But in terms of new machines, the latest wave of regulations in Europe and the US have produced a decisive split in the wheeled loader market, between these highly regulated markets (including Japan) and other parts of the world. In fact, some manufacturers say they now have to produce three versions of the same model - one for highly regulated markets, one for less regulated markets (Brazil and China for example) and one for un-regulated markets.
The reason is that some of the less regulated markets now have quite high standards - equivalent to Tier 2 or Tier 3 - which require systems like electronic control and EGR to keep emissions down. These systems add cost that is not required and not necessarily appropriate for other parts of the world.
New this year
In terms of new equipment launches, many of the latest models were unveiled at the various construction equipment shows at the start of the year. The most significant was ConExpo in Las Vegas, US, in March, but there were also exhibitions in Europe in the shape of Samoter in Verona, Italy, and Smopyc in Zaragoza, Spain
These of course focussed on the latest Interim Tier 4/Stage IIIB models for the European and US markets. But some manufacturers did not wait for the deadline at the start of this year to bring out their new models.
In the US John Deere's first K-series Interim Tier 4 loaders were available some six months ahead of the deadline. The company said there was an advantage in being early to the market with low pollution machines, particularly in states like California where contractors are required to have the lowest emission machines available on the market to win work.
Earlier this year the company surprised everyone at ConExpo with the unveiling of a prototype 9 cubic yard (6.9 m3) bucket wheeled loader featuring a diesel-electric drive system. This uses the diesel engine as a generator to drive four separate electric motors in the loader's wheels - a similar principle to Caterpillar's D7E diesel-electric dozer, launched three years ago.
Deere product manager for four wheel drive loaders John Chesterman said, "In addition to fewer emissions, customers asked for durability, fuel efficiency and reduced tyre wear. We've responded with a loader that incorporates four modular, independent wheel drives with electronic traction control."
The company hopes to make the machine commercially available in 2013.
Caterpillar's ConExpo launches included five new K-series wheeled loaders, which all meet the Interim Tier 4/Stage IIIB emissions requirements. The 950K, 962K, 966K, 972K and 980K cover the 157 kW to 275 kW power bands and bucket capacities from 3.3 m3 to 5.3 m3. The K series machines replace the H-series models in the US and Europe, while in less regulated markets, the H series will be retained.
As well as the low emission engines, Caterpillar has made a range of improvements all round the machines. Common across all five loaders is a new cab with a wider doorway and an inclined ladder up from the ground to make it more like a staircase. The cab itself has been streamlined and the driving position moved forwards for better visibility, while new viscous mountings reduce noise and vibration.
Options include a low-effort hydraulically assisted steering wheel, or Cat's Command Control system for short cycle applications. The in-cab switches are large enough to be used when wearing gloves, and an LED light and audible click tell the operator when they have been activated.
In terms of performance, Cat has redesigned the Z-bar linkage at the front end, and this can be used with its Performance Series buckets and Fusion quick coupler for better performance, fuel efficiency and visibility.
All five machines have new torque converters in their drive trains, which have been matched to the new Interim Tier 4/Stage IIIB engines to reduce fuel consumption while delivering more power. Software changes mean that the transmission now shifts down based on torque requirements rather than speed, which Cat says also says saves fuel, and in general the gear shifts have been improved to increase efficiency and the smoothness of the ride.
Volvo has had a similarly busy start to the year with wheeled loader launches. New in the first quarter of the year were the L110G, L120G, L150G, L180G (including a high lift version) and the L220G, covering the 191 kW to 273 kW engine classes and 2.7 m3 to 5 m3 standard bucket sizes.
These machines replace existing models, but Volvo has also added the L250G to its range with a 5.1 m3 standard bucket and 290 kW engine, designed specifically to load on-highway trucks.
New Interim Tier 4/Stage IIB engines, along with other improvements mean the latest machines are more powerful and fuel-efficient than the models they replace. The L120G for example offers +20% more lifting force and +5% more breakout force than its predecessor, but with lower fuel consumption - up to a -5% saving in load & carry or truck loading work. The improvements in lifting and breakout force are thanks to up-graded hydraulic pumps that allow for higher working pressures.
Other features include Volvo's Automatic Power Shift (APS) system that keeps the loader in the ideal gear by sensing the travel speed, load on the engine, braking and other factors. Some models are also available with Volvo's Optishift system, which includes other enhancements to the driveline that can cut fuel consumption by up to -15%.
At the front of the new loaders is Volvo's Torque Parallel linkage, which the company says combines the breakout force of a traditional Z-bar linkage with the flexibility to parallel lift.
Komatsu meanwhile unveiled its first Interim Tier 4/ Stage IIIB loader at ConExpo, in the shape of the WA380-7. Fitted with Komatsu's own 142 kW SAA6D107-2 engine, the company says the new machine has lower fuel consumption than its predecessor, and the advanced electronic control used to help achieve this has also led to a system called 'SmartLoader'. This matches the engine torque to the load being placed on it, which helps keep fuel consumption down.
Inside the new cab, the front glass has been lowered and the dashboard has been redesigned to improve visibility. A new high resolution 7 in (17.8 cm) LCD monitor features enhanced capabilities and displays information in 25 languages for global support. The operator can use this monitor to modify settings, check operational records, or check how long until the next service is required. A separate high-resolution reversing camera is mounted on the right hand side of the console for operator convenience.
Case started the year with the introduction of three new F-series wheeled loaders, again featuring Interim Tier 4/Stage IIIB engines. Unlike most of the other new machines on the market however, these use a technology called selective catalytic reduction (SCR) to achieve the required emissions levels.
Rather than running the engine at a low combustion temperature and then capturing the PM in a DPF, the idea behind SCR is to have high combustion temperatures, so particulates don't form at all.
The down side to this is that this creates more nitrous oxide (NOx) - another legislated pollutant, which does not form to the same extent at the lower combustion temperatures of other systems. This is where SCR comes in. This after-treatment technology removes NOx from the exhaust stream by injecting a urea into the exhaust gasses as they pass through a catalyst - again this is contained in a ceramic honeycomb.
The downside to SCR is that it means there is another fluid on the machine to keep topped-up - the urea. On the plus side, there is no DPF to regenerate (although in many cases this happens automatically), and many manufacturers say that SCR will have to be used to meet the Final Tier 4/Stage IV regulations in a few years time anyway.
Commenting on the use of SCR Case Construction Equipment marketing manager Tim O'Brien said, "With the SCR technology in our Case F Series wheeled loaders, Case has made what was already the industry's most fuel-efficient line of wheeled loaders even more fuel efficient. At the same time, the Case F Series engines are more powerful and respond faster."
Case's new models are the 721F, 821F and 921F, with engines rated at 133, 158 and 180 kW and 2.5 m3 to 3.6 m3 buckets. With the optional five-speed transmission, Case says it can deliver an 8% saving in fuel costs, against a comparably sized four-speed machine. The F-series machines also have a fuel saving mode and idle systems to cut consumption further.
Sister company New Holland also launched new wheeled loaders at the start of the year, again meeting emissions requirements with SCR technology. The company says this delivers more power and lower fuel consumption for the W170C, W190C and W230C, which operate in the 133 kW to 168 kW brackets and
2.5 m3 to 3.6 m3 bucket classes.
The loaders have four power modes to allow the operator to match engine power to the job at hand. Like the Case machines, there is an option for a five-speed transmission and lock-up torque converter that provides faster acceleration, quicker cycles and higher travel speeds.
There is also a 'PowerInch' feature common to the Case and New Holland machines that allows the operator to approach objects on steep slopes with precision and control. New Holland offers PowerInch and the five-speed transmission along with heavy duty axles in a single options bundle that it calls its Efficiency Package.
Like the 921F for Case, New Holland's W230C is a new class of machine for the company, operating in the 20 tonne class.
And it is not just the traditional suppliers that are tackling the challenge of Interim Tier 4 and Stage IIIB to supply the US and Europe. This year's ConExpo also saw China's Liugong unveil a machine that meets the new emissions requirements in the shape of the 842IV, a 144 kW machine with a 2.7 m3 bucket.
The drivetrain features a Cummins QSB6.7-C200 six-cylinder engine and the transmission is an automatic torque converter model from ZF which can deliver a forward speed of 42 km/h. Features include an automatic return-to-dig function on the Z-bar linkage bucket, which speeds up cycle times, while a quick hitch is available as an option.
In the heated air/conditioned cab there is a suspension seat, rear view camera and sound system that can accommodate an MP3 player. Liugong's ride control system is standard and maintenance is simplified thanks to an electrically raised engine hood.
Technological progress
Although the new generation of Interim Tier 4/Stage IIIB wheeled loaders will be more costly to buy because of the expensive emissions reduction technology, most manufacturers have managed to make their new machines more fuel efficient and more powerful.
However, the industry and legislators still have to make sure the trade in used wheeled loaders does not result in expensive mistakes such as these engines being fuelled with poor quality diesel in countries they were never designed to work in.
STAY CONNECTED

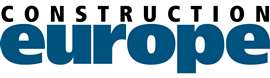
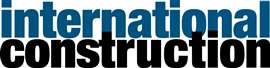
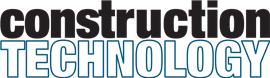
Receive the information you need when you need it through our world-leading magazines, newsletters and daily briefings.
CONNECT WITH THE TEAM
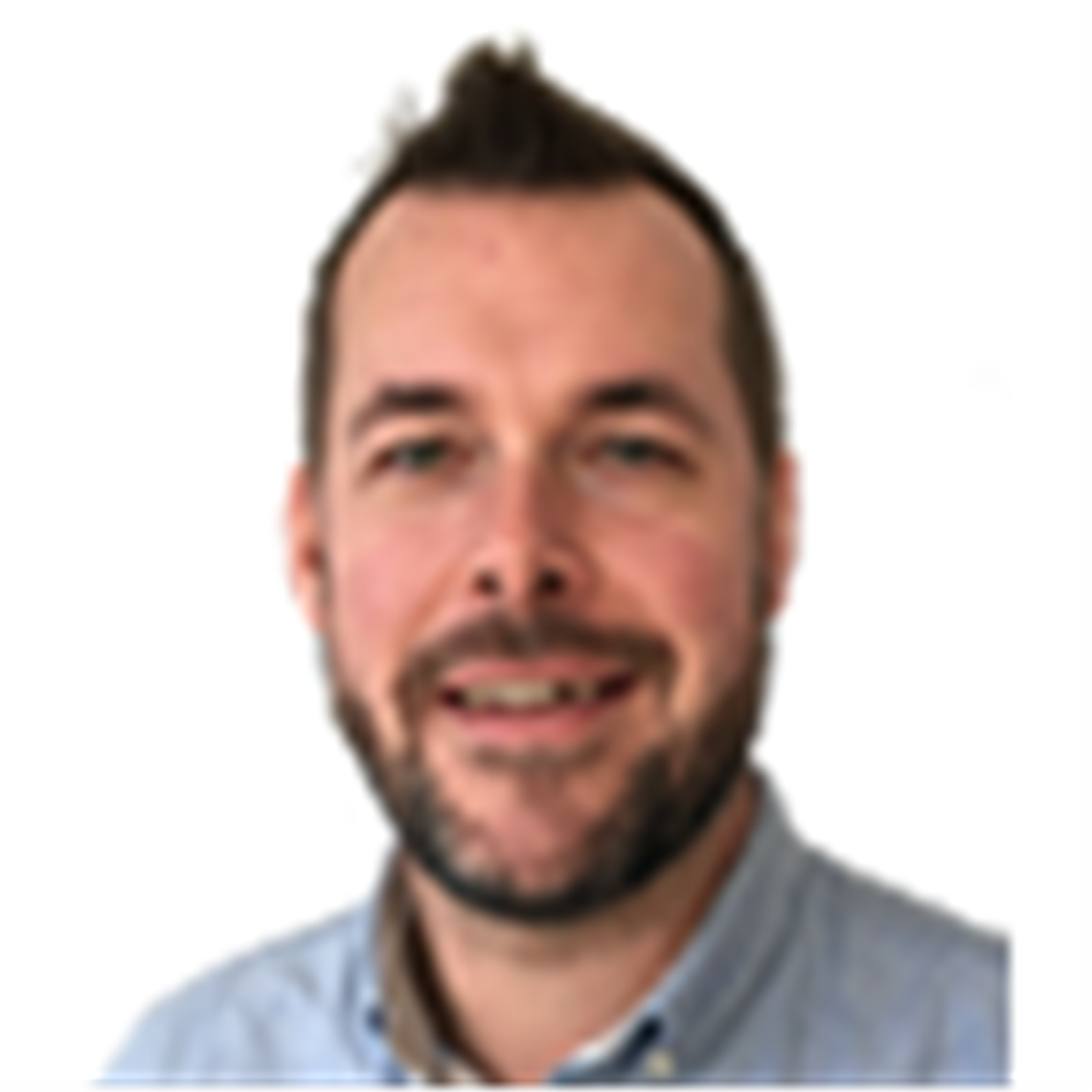
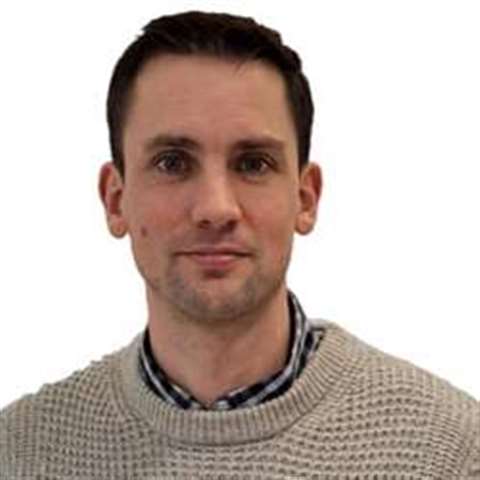
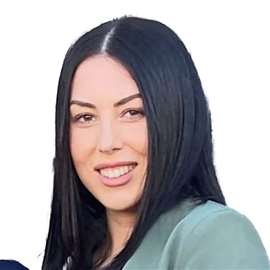
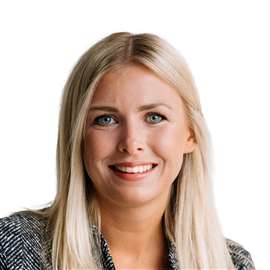