Read this article in French German Italian Portuguese Spanish
Is battery-electric still the best zero-emissions machinery option for contractors?
11 July 2025
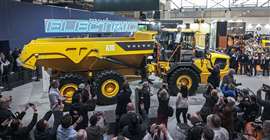
OEMs have been investing significant sums in construction heavy construction machinery running on batteries, hydrogen, alternative- and low-carbon fuels. So does battery-electric remain the best option for contractors if they want a zero-emissions machine today, asks Tom Jackson?
In the last decade, most construction equipment Original Equipment Manufacturers (OEMs) have invested significant sums of money in developing machines that run on batteries, hydrogen, alternative and low carbon fuels.
For now, battery electric technology leads, primarily because grid power is available in most locations. And – even when grid power is unavailable – many OEMs offer mobile charging solutions.
By contrast, the infrastructure for hydrogen is still in its infancy, and creating solar or wind power to generate hydrogen is necessary to ensure hydrogen is genuinely zero carbon. Other alternative fuels are still niche and offer only marginal improvements in CO2 reduction.
Electric power, in addition to being widely available, is much less expensive than diesel for an equivalent amount of work and produces much less CO2.
Application advantages
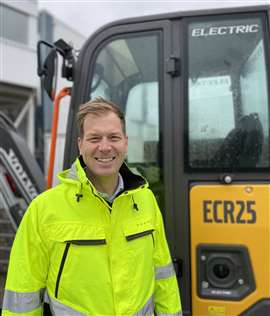
Addressing climate change is the biggest reason for choosing battery electric over diesel, says Fredrik Tjernström, electromobility solutions sales manager at Volvo Construction Equipment (Volvo CE). Climate change aside, battery electric machines also prove essential in a variety of scenarios where an internal combustion/fossil fuel powered machine might be problematic.
“You get rid of the NOx and the particulate emissions, which immediately affects the people around you whether it’s the citizens in a city or the workers on a construction site,” says Tjernström. “Another benefit we see is the improvement in the operator environment. Having so much less noise and vibration really helps.”
UK-based JCB is another OEM promoting the benefits of electric equipment. “We can put these machines into inner city environments, suburban neighbourhoods on weekends or indoor applications where noise makes diesel operations disruptive,” says Lee Tice, product manager at JCB. “And it’s all done with zero loss in performance from its diesel counterpart.”
Return on investment
The initial cost of electric equipment is higher – often substantially – compared to its diesel equivalents, and the question of return on investment (ROI) for electric machines is a complicated one, says Alistair Hayfield, vice president, commercial vehicles at Interact Analysis.
In most cases, the ROI does not justify an immediate switch to battery electric machines. But there are some cases – high duty cycles or other environments – where there can be a justification. This will change quickly, however, as battery prices decrease and the volume of machines produced increases.
And ROI does not matter if the application or the client require a noise and/or emissions free work zone. In that case, electric is currently the only choice.
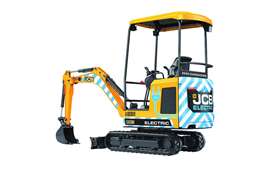
When calculating ROI, it’s important to do thorough analysis of all the costs. This would include purchase price (factoring in any government subsidies or credits), fuel costs (diesel vs. electricity) and maintenance costs.
“Because of the simplicity of electric drive trains you don’t have to spend the money or time on things like oil changes and the typical diesel engine maintenance,” says Tice.
He adds that JCB’s 19C-1E battery electric excavator was introduced commercially in 2019 with a five-year warranty on the battery. “Hitting that five-year mark was a good deal for us,” says Tice. “We wanted to see what that battery would do past that. And we’re proud to say they’ve surpassed the mark without dropping off in performance. They’re holding up very well in the field.”
Tjernström says Volvo CE is confident that they can make it more financially attractive to go to zero emissions in the future. “We need more cost-effective batteries and volume in the factories to get the product costs down a bit more. But we are advancing model by model and year by year. And we have customer cases where it’s actually easier, neutral or even a bit beneficial to go to zero emissions now. But unfortunately, that’s not always the case yet.
“A customer of ours, Skanska, built a $10 million school project, and they did it 97% emissions free using two excavators, one truck, one wheel loader, one compactor and hand tools that were all electric,” says Tjernström.
Reaching a favourable ROI in electric equipment is easier when the contractor takes a total project view, Tjernström says. “For a one-person company owning a single excavator, it’s a much bigger challenge to step into zero-emissions solutions.”
Electric equipment statistics
Off-Highway Research initiated coverage of electric construction equipment in 2024, looking at six types of equipment – compact tracked loaders, crawler excavators, mini excavators, telescopic handlers, wheeled excavators and wheeled loaders – which are in series production with multiple OEMs worldwide. Electric wide bodied trucks have since been added to the coverage.
In 2024, nearly 19,000 electric machines were sold worldwide, representing 1.6% of the global market in unit terms. This was a sharp increase on the 8,861 electric machines sold in 2023, but the growth was by no means widespread.
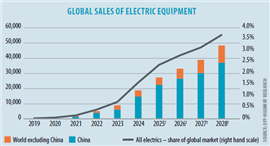
Almost 80% of global demand for electric equipment is in China, where the main products are medium to large wheeled loaders and wide bodied trucks. A further 9.5% of the global electric equipment market is represented by various emerging economies where Chinese OEMs – the major producers of electric equipment – have been promoting the concept with the aim of securing first mover advantage.
In contrast, uptake of electric equipment in Europe and North America stalled last year with the downturn in those markets. Off-Highway Research believes that a further issue in these territories is that the focus on low powered compact equipment by most OEMs is not the best avenue to pursue for electrification.
These machines are not utilised enough to make back their high purchase prices through lower running costs, and are generally used in areas and applications where there is no access to grid power for charging. This is in contrast to the Chinese model, where electric machines are used for long hours in quarries and mines, sites where grid power tends to be available for charging at the end of a shift.
Market news
Over the last five years, multiple OEMs have debuted a variety of electric machines, some prototypes and some commercially available. And while the market for electric equipment hasn’t diminished, it isn’t booming either.
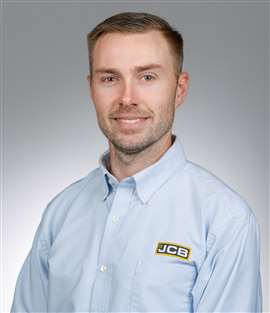
Growth is flat across the industry, says Tice. “We still have customers who are interested in electric products and see the benefits. There is some uncertainty as to the incentives offered for the purchase of electric machines, especially in light of a new administration in Washington DC. But right now, we’re pretty stable.”
“The market is doing OK in Sweden and Northern Europe,” says Tjernström. “In the US, adoption of electric equipment is progressing along the coasts, and you could say that interest is picking up. But we are a bit frustrated. It is improving, absolutely, but we want it to go faster. China, on the other hand, is transforming quickly – especially the wheel loader market.”
Regarding the US, the change in the White House has negatively impacted the push to electric, at least on a federal level. “I suspect interest has plateaued in the US on the basis that there are relatively few trials/demos taking place and there is little pressure to move to new solutions,” says Hayfield. “This is likely to change as cities increasingly drive investment in battery-electric machinery, but right now I would say interest probably hasn’t increased that much.
“Outside of California (where the funds have come from the California Air Resources Board), there have essentially been zero federal funds for battery electric construction machines in the US,” he adds. “That said, as with Europe, it is the cities that are driving adoption.”
The North American Electric Construction Coalition covers six cities – New York City, Austin, Boulder, Los Angeles, Montreal (in Canada) and Philadelphia – that are committed to purchasing zero emission machinery.
Net zero has no single solution
“We are still working with all the alternative power sources, battery electric, grid-connected excavators, hydrogen combustion and hydrogen fuel cell, because we are a global company,” says Tjernström from Volvo CE.
“We don’t believe there is one silver bullet. A lot of this depends on how the energy infrastructure will be developed in different parts of the world. This is not in our hands, and we need to be able to adapt.”
It’s still too early to go into the other technologies – of which there are many – today, says Tjernström.
“There is basically no availability for green hydrogen yet. So, the energy efficiency of that complete chain is very favourable for electric and battery electric.”
The next big thing?
Diesel-electric hybrid engines are likely to be an up-and-coming engine technology going forward, especially when applications call for higher horsepower than most battery electric machines provide. Not only do they eliminate the need for power from the electric grid, but there is reduced worry about battery life, and previously wasted energy from braking action and/or boom swing can be recycled back into the batteries.
Caterpillar displayed a number of reduced emissions iterations of its diesel engine platforms at Bauma, including a new series hybrid power expansion powertrain. Luke Bennett, technical sales and advanced power systems machine integration specialist for Caterpillar shares the capabilities and plans for this hybrid platform.
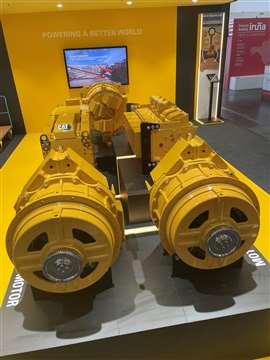
Is this designed for a specific range of horsepower?
We have a variety of components used in today’s Cat machines that allow us to offer a range of different powers. For example, the 2x 250kW motors shown at Bauma can also be used as generators, so we could offer a smaller system with a 250kW generator and a Cat C9.3B engine instead of the C18 and 500kW generator. The system is also flexible in the size of battery we can use to add more energy storage if needed.
Does Caterpillar have in mind any specific machine types for the hybrid engine?
Hybrid systems are especially suited to machines that can recover what would be wasted energy on a non-hybrid system. Wheeled machines are one type of application that would be suitable. The hybrid system is also suitable for cyclic machines where the battery can be used to temporarily store energy to reduce the peaks in demand, allowing engines to be downsized and system efficiency increased.
Does Cat have a timeline for introducing this to the market?
A version of this system is being developed with a number of OEMs, with the aim to test it in 2026 and production following sometime after.
STAY CONNECTED

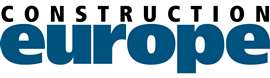
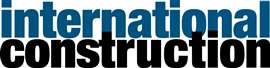
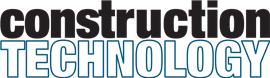
Receive the information you need when you need it through our world-leading magazines, newsletters and daily briefings.
CONNECT WITH THE TEAM
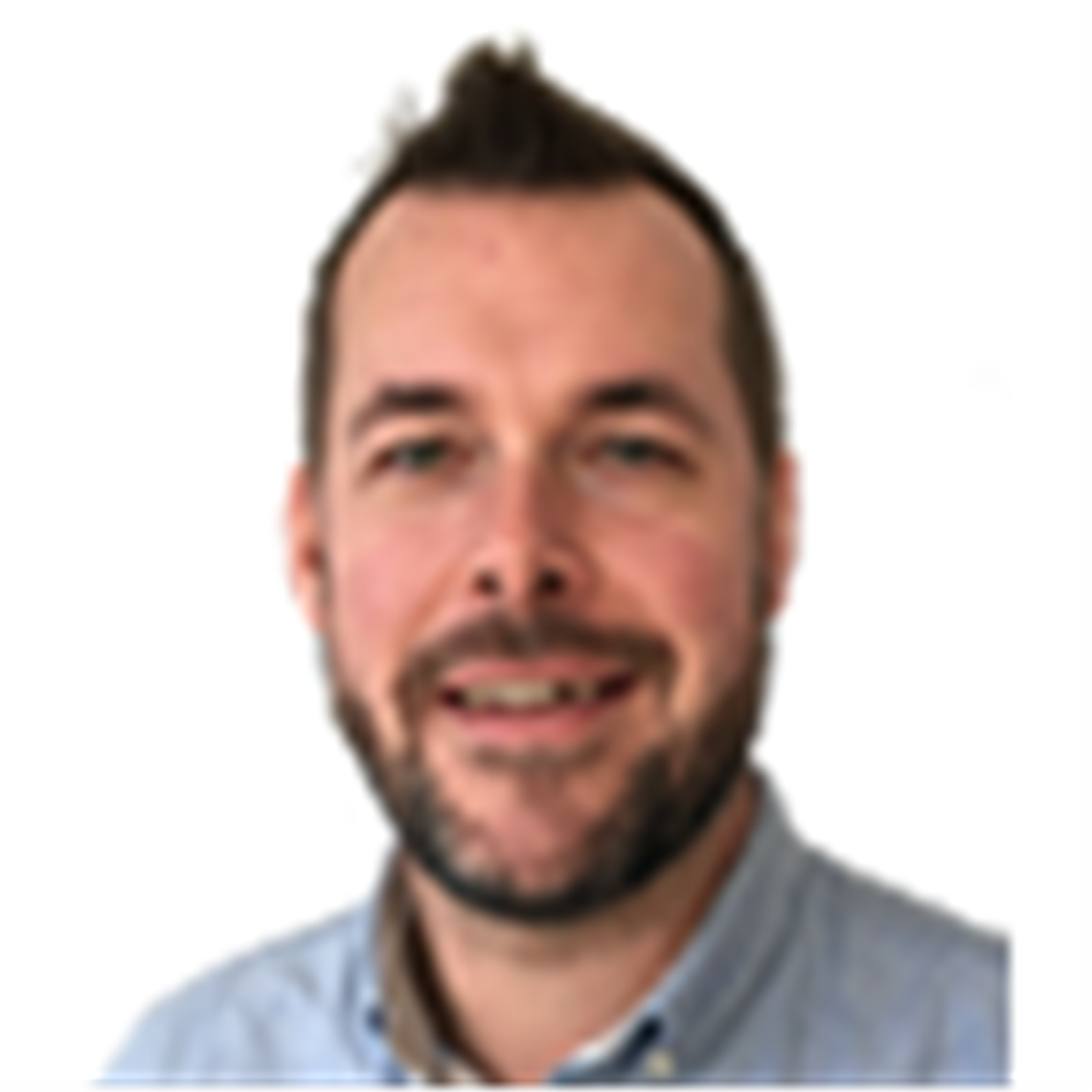
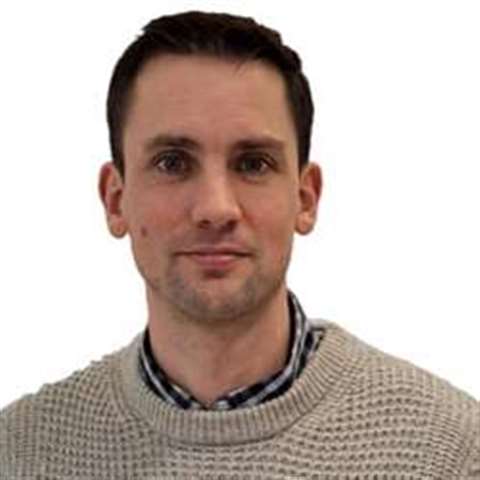
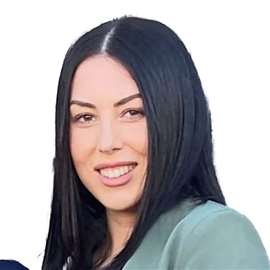
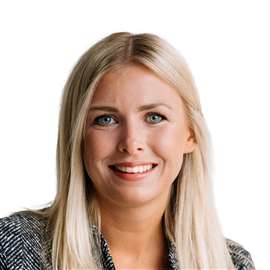