Investing in workforce wearables on construction sites
13 January 2022
Matthew Marino, director of Ergonomics and Human Factors at HeroWear, a provider of exosuit technology, on how the technology can best help construction
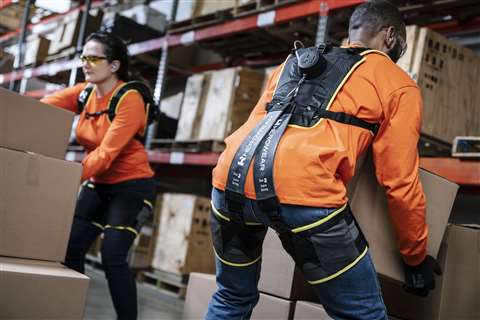
Businesses across the world are trying to navigate a worker shortage so widespread that it’s been dubbed the Great Resignation. Some construction companies are feeling the pinch of not being able to fill out a jobsite.
This makes winning over potential workers critical in the effort to get back to normal, but how can construction companies improve recruiting and retention? Of course, more money always helps. But making jobsites less painful and showing potential workers the company values their quality of life can also provide a competitive advantage.
For example, exoskeletons, exosuits and other workforce wearables are investments that can result in healthier, happier workers. Considering the punishment their backs go through on a jobsite, the much-needed assistance from workforce wearables is a great way to keep workers coming back each day.
However, there is a very important factor to consider when researching workforce wearables: Is it comfortable and does it allow a full range of motion?
While assistance helps workers throughout the day, a rigid workforce wearable could get in the way. That’s when a worker might make ‘adjustments’ so it’s more comfortable, but that makes it less effective – or worse, counterproductive. What started with good intentions ends up worsening the problem and the workforce wearable is discarded.
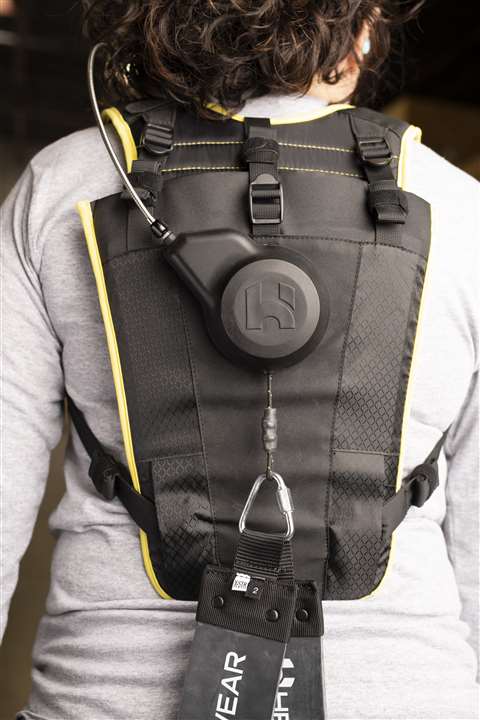
Why is wearable technology important to the construction industry?
The truth is adoption of wearables will be an uphill battle if workers are annoyed by it.
That’s why comfortable workforce wearables that don’t restrict freedom of movement are more practical for many industries, especially construction sites. Workers need to be able to quickly adapt to any challenges they face to get their job done, which means they need full mobility and no distractions.
As an example, lightweight, soft exosuits that are built to comfortably fit any body type and be worn all day have incredible potential to help workers who frequently bend and lift. That’s especially true because construction workers who frequently make those motions or hold awkward postures need the most protection.
The wear and tear from those frequent forces and postures on their spine adds up physically – not only over the course of a single day, but over the course of a career.
How an exoskeleton works
The rise of workforce wearables is exciting because they could help fight a major problem: work-related musculoskeletal disorders (WMSDs).
Government agency OSHA (Occupational Safety and Health Administration) said WMSDs are frequently the cause of lost or restricted work time. The annual cost from back pain in the US alone is US$253 billion, according to the Bone and Joint Initiative.
“Musculoskeletal disorders (MSDs) continue to be a leading workers compensation injury,” said Woody Dwyer, Director of Loss Control at insurance company AmTrust Financial.
“Exoskeletons and exosuits have the potential to reduce ergonomics risk in the workplace where traditional engineering solutions were not technology feasible. Exoskeletons could also support injured workers in their transition back into the workplace and be one component of a robust return to work strategy.”
According to AmTrust Financial, exoskeleton devices could have a positive impact on workers’ compensation insurance by lowering the number of long-term workplace injury rates by protecting against repetitive motions or awkward postures that lead to WMSDs.
However, AmTrust Financial highlights that not properly wearing workforce wearables could potentially increase insurance claims.
That means a major hurdle in the ‘War on WMSDs’ is enthusiastic buy-in from the workers to properly use the wearables. When they feel comfortable using a wearable and quickly see the difference it makes by improving their quality of life, the way physical work is done can change forever.
The good news is new wearables are available for construction companies that want to protect workers without sacrificing production.
Companies have started using workforce wearables, including rigid exoskeletons or ‘soft-shell’ exosuits, to lower the forces that increase the risk of chronic pain. Toyota, Ford and Boeing have been using workforce wearables for years. Toyota has reported reductions in injury rates for workers using shoulder exoskeletons for overhead work.
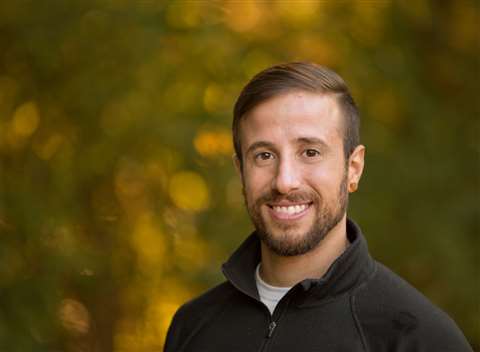
Construction productivity
The importance of productivity and hitting timelines, paired with the tiring motions and postures needed to do their job, open construction workers to the risk of a back injury that could sideline them for an extended time.
Reported back pain for construction workers is 20% higher than all other industries, according to a study by the Center for Construction Research and Training.
However, workforce wearables give construction companies options to help protect workers and potentially reduce medical costs and, most importantly, provide hard-working construction workers better quality of life. That’s if they are used correctly – which means comfort and freedom of movement are just as important as assistance.
STAY CONNECTED

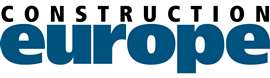
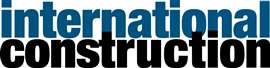
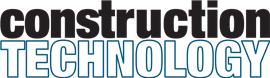
Receive the information you need when you need it through our world-leading magazines, newsletters and daily briefings.
CONNECT WITH THE TEAM
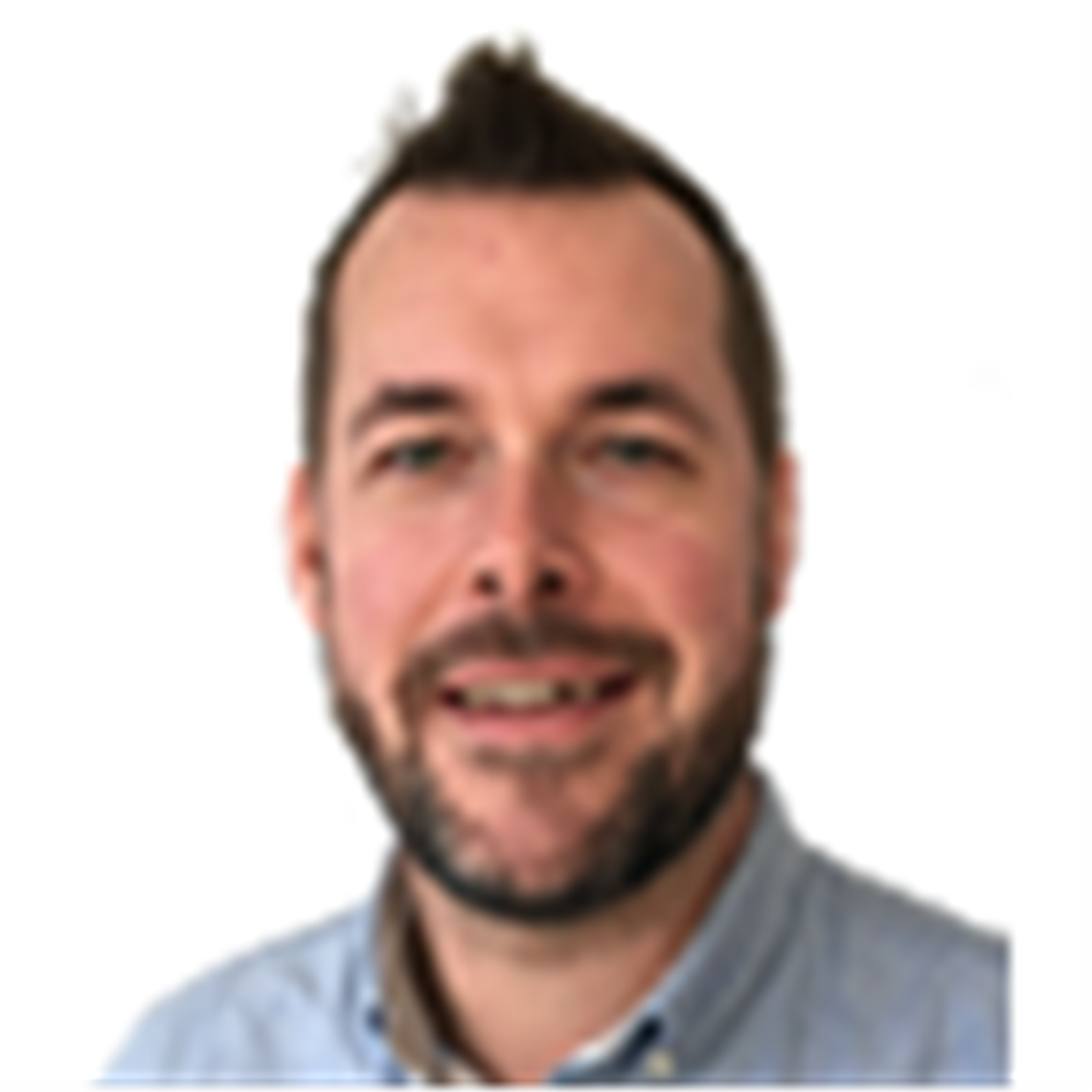
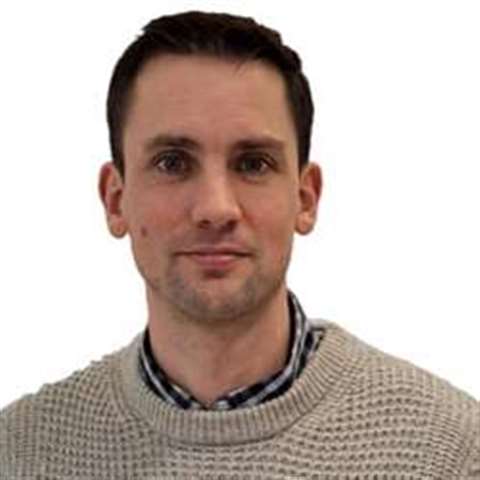
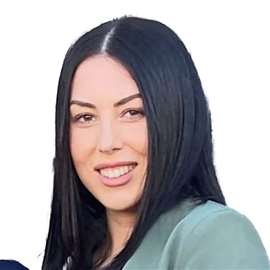
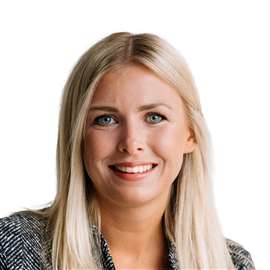