Interview: Ray O’Connor, CEO, Topcon
13 May 2021
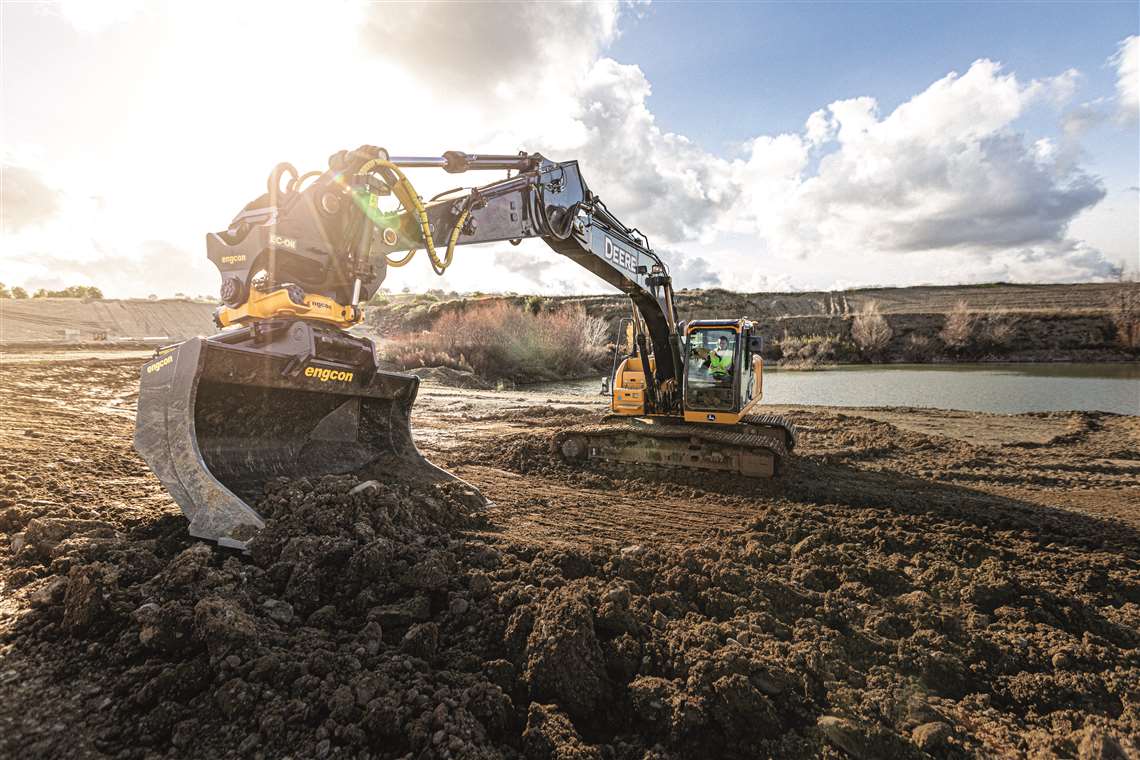
In 1984, when Ray O’Connor first started selling construction lasers, the units were powered by 12-volt car batteries. Since then, successive waves of innovation in consumer and construction electronics have transformed all of our lives. And while, in 2021, it may seem that GPS/GNSS machine automation, spatial measuring and mapping technology are mature markets, that is hardly the case, says O’Connor, now the CEO of Topcon Positioning Systems.
As a native of Ireland working in California, US, for a Japanese company, O’Connor has more than a few unique global insights to share. He says that the next big moves in the market will come from integration and smarter use of data flows, accelerated technology adoption in China and Latin America and a relentless and aggressive pursuit of devices that are better, faster, more intuitive and less expensive.
In the early 2000s GPS/GNSS machine automation took off in the US and Europe. But thus far the adoption rates in China and Latin America have not matched those elsewhere.
Construction technology adoption rates
“Money, competition and margins drive adoption rates in the West,” says O’Connor. “In North America you’re getting paid the same amount to move a cubic yard of dirt in 2021 as you were in the 1960s. So, if you can automate and double the productivity of a machine you can drive your margins up.”
In China there is a drive for money too, but they’re more focused on speed and volume – building hundreds of airports, multiple high-speed rail systems, and brand new cities. “They’re not trying to squeeze money out of a rock,” says O’Connor. As a result, it is less common to see machine control equipment running in China, compared to most sites in the US and Europe where jobs are more competitive and margins tighter.
Nonetheless, machine control adoption is growing in the developing world, thanks to the big OEMs who are starting to install the equipment at the factory and legitimising the technology, says O’Connor.
Another limiting factor is price, which for a standalone machine at the high end of the market, can run from US$60-70,000. “But it’s coming down and that will continue,” says O’Connor. “At the end of the day, every machine will be automated. The benefit is too large.”
Pushing construction technology price and performance
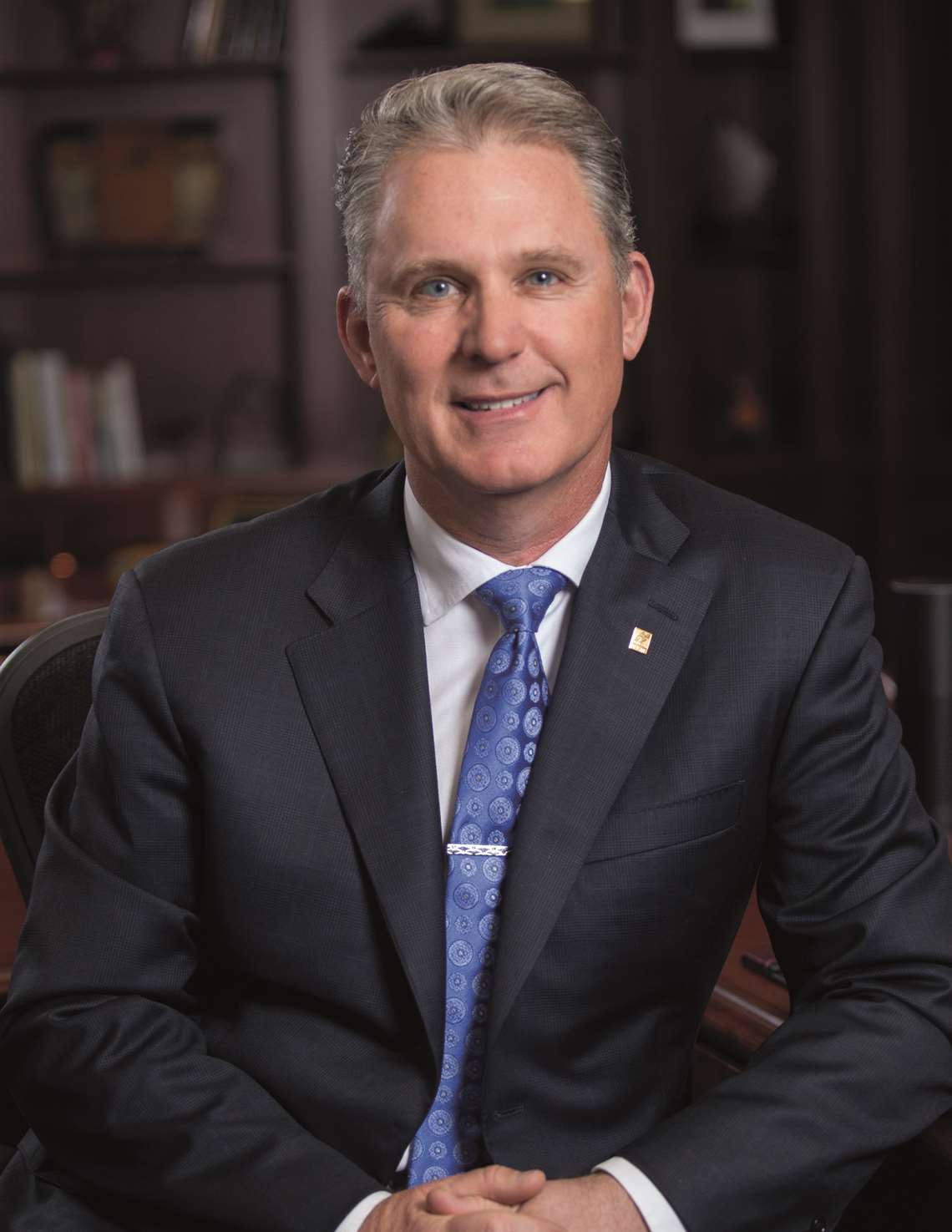
O’Connor says that the next big market for machine control in Europe and North America is going to be compact and ancillary equipment, such as skid steers, compact track loaders and mini-excavators. Success in that market will be determined by two things: price sensitivity and ease of use.
“Making automation easier to use is perhaps the greater challenge, but one that has been underway for a long time. When I joined Topcon, I told the engineers my vision is to have a box. When you open it a device crawls out, climbs up the leg of a tripod, sits on top of the tripod and starts measuring everything in the room. And it does it all by itself. And it just gives you the information that you’re looking for.”
Technology should be intuitive and self-explanatory, says O’Connor, who sees the iPhone as the gold standard in simplicity. “There’s no manual for the iPhone. You take it out of the box and just push a button or tap the screen. And if I push the wrong one, I find the right one to push again.”
Not only is the iPhone easy to use, but Apple pioneered an incredible amount of innovation in the technology field – chips, sensors, batteries and software – to make it so. This is something that all manufacturers, including Topcon, have learned from and adopted.
“The importance of simplicity in our business is critical,” says O’Connor. “We have a long way to go to get to where I would be satisfied with the simplicity of the products. It’s not easy what we do, it’s complex. And that’s a challenge for every company. But when we do that, we win.”
Education is the next big thing for construction
Contractors have long struggled with what’s sometimes described as a ‘firehose’ of data such as BIM, telematics and GPS coming from their technology devices. This makes it hard to pick out the essential information they need or to integrate data flows. Topcon’s answer was to form a joint venture company with Bentley Systems called Digital Construction Works.
The company’s consulting services for integration of automation hardware and software address this need by helping contractors manage the data they receive from a myriad of devices. Digital Construction Works was launched in 2019 and has garnered participation from some of the top companies in the industrial and infrastructure construction world.
Covid-19 concerns cut into the company’s participation, but construction activity has remained strong throughout 2020 and into 2021, giving O’Connor some optimism. “There is real business being transacted, not at the rate we had hoped at the beginning, but we’re seeing it really pick up.”
O’Connor says some of his top people signed on with the joint venture company, “They see this as a futuristic part of the business and they’re getting to revolutionise how these businesses need to be run.”
For Topcon it’s also a chance to learn what their customers’ needs are and how to address them. In addition to the programs offered with Digital Construction Works, Topcon has multiple training sites around the world, including Japan, Australia, the US and Europe. “We’re learning a lot about what matters to the contractor, the most important workflows, how we connect all the different capabilities that we have, and then how we go about solving their problems,” says O’Connor.
Construction’s long road to full automation
There’s much talk of fully autonomous construction worksites, where machines run without operators, guided by GPS and artificial intelligence. Such sites would be a boon for the technology companies, but fully automated sites for construction are still quite a way off.
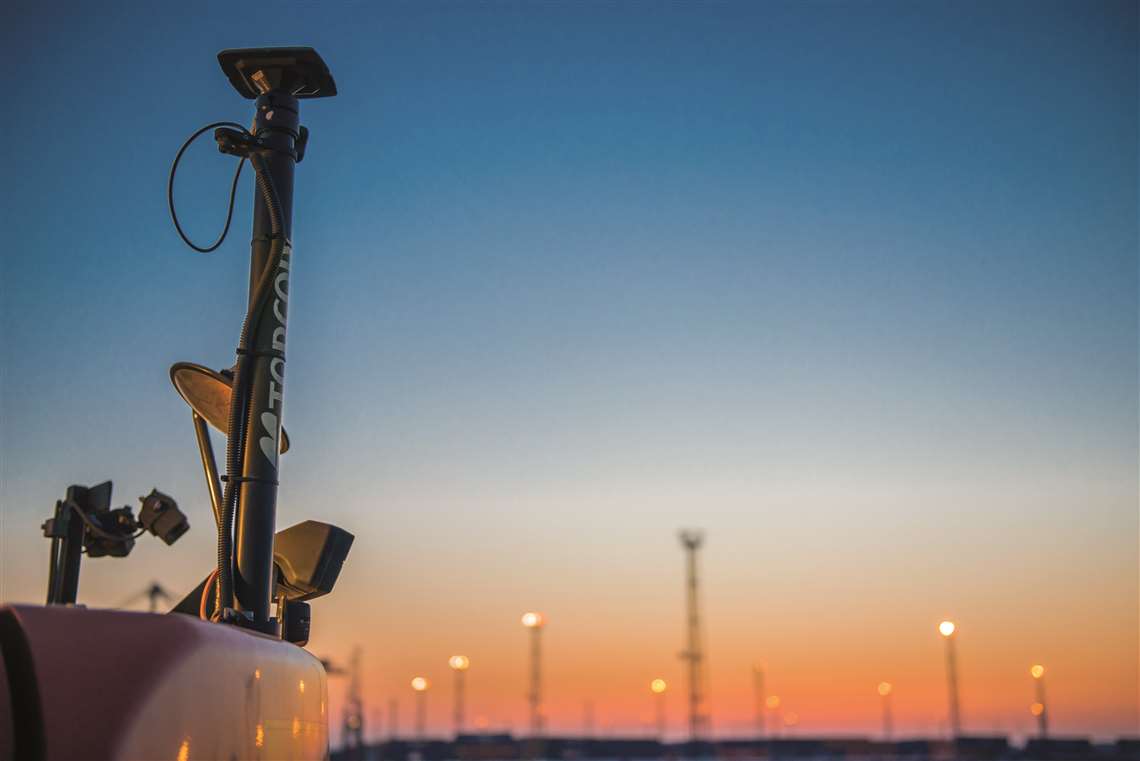
The fact that the automotive industry, Tesla in particular, has spent billions to develop full automation and still has not succeeded in producing commercial acceptance is significant, says O’Connor. Autonomy works best in controlled environments, like factories and mines and, to a certain extent, agriculture –where you have machines doing the exact same task every day. But every construction site is unique and constantly changing.
“If every nuclear power plant and every highway was identical, we could automate their construction. They’d all be made in factories, and we would ship them to the jobsite,” says O’Connor. “That’s the real, complex challenge that we have going forward. How do we make automation flexible, so we can do it on one of everything?”
When it comes to technology, it’s important to not get out in front of your skis, says O’Connor. Take drones, for example, which were the talk of the industry just a few years ago. “Now you don’t read about drones that much anymore except for certain applications,” he says. Despite the fact that Topcon has its own line of drones, including a fixed wing model, O’Connor says drones are limited in what they can do. “They can do certain things very well. But it’s not every job.”
More than 100 years ago the founder of Topcon in Japan said that the company should always be one step – but never two or three or four steps ahead – of the competition, says O’Connor. “If you’re more than one step ahead, you’re a philosopher, you’re talking about ideas. You’re not talking about what can practically impact the market. That’s very important to a tech business in particular.”
Future challenges for construction technology
With Covid-19 diminishing as a threat, Topcon fully plans to attend trade shows in the future.
“We will go back to all the major trade shows,” he says. “They are great selling events for us. They are a great place for people to kick the tyres. Bauma has a massive number of people. Even if it is cut in half, it’s a massive number of people.”
No other format gives customers that level of access to the company’s top executives and salespeople, and for those reasons, O’Connor says he doesn’t see trade shows ever going away, “Maybe budgets will be tighter, but I can guarantee you we will be at the trade shows.”
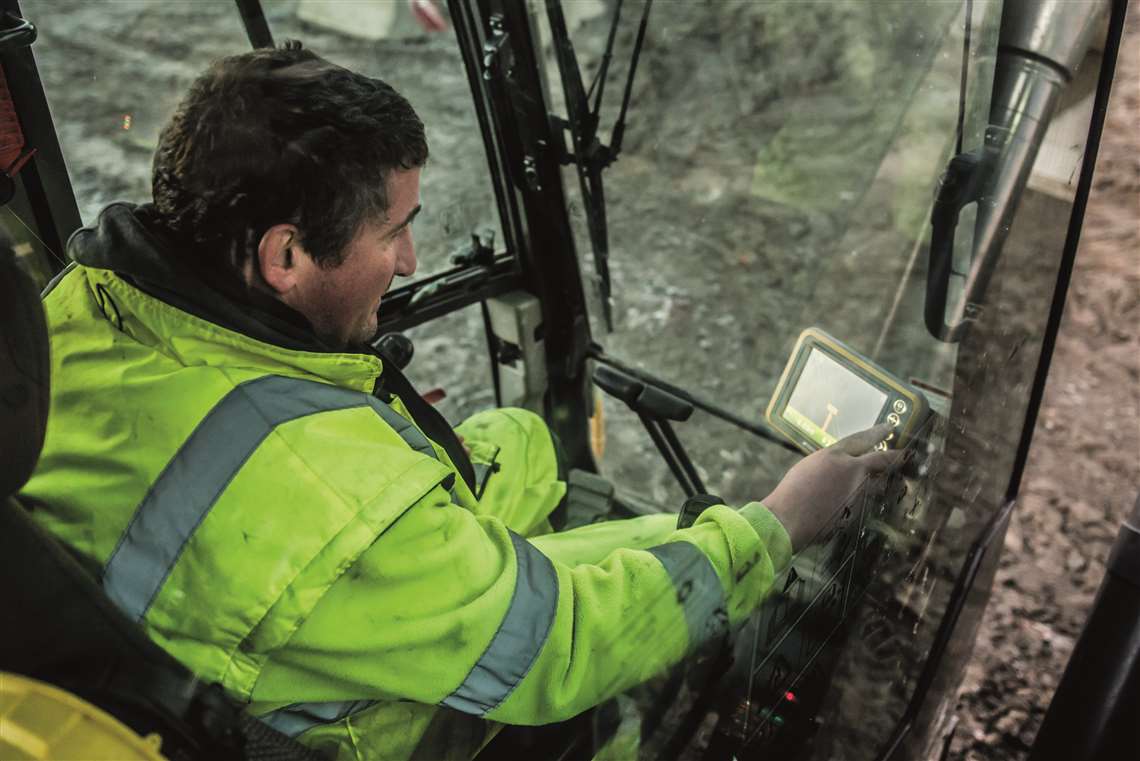
O’Connor is on the board of the Association of Equipment Manufacturers and says AEM is trying to encourage the US government to do what they’ve done in Japan, Germany, England and Australia. In those countries, legislation mandating the use of BIM, automation and machine control technology has helped to drive down costs and improve completion times on infrastructure projects.
O’Connor fully recognises that the US is less favourably disposed to regulation, but also finds an irony in that. “Isn’t it shocking, that all this machine control technology is developed in the US, and foreign countries require the use of that technology to cut their costs and improve their infrastructure. And yet we don’t mandate it here,” he says.
As with Apple products, the winners in the construction technology space will be the companies that figure out what the customer needs, even when the customer doesn’t know what they need, says O’Conner.
“Steve Jobs had a great ability to understand the problem, how to apply the technology and get the people and put them together to solve it,” he says. “Salesmanship alone isn’t enough. It requires collaborative engagement with the customer on all levels, everything from tradeshow conversations to education programs like Digital Construction Works.
“We have to know what the problem is they’re trying to solve,” says O’Connor. “And that’s a challenge for every company. We have so much education to do in the construction industry. It’s a fun place to be.”
STAY CONNECTED

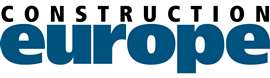
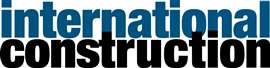
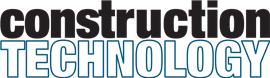
Receive the information you need when you need it through our world-leading magazines, newsletters and daily briefings.
CONNECT WITH THE TEAM
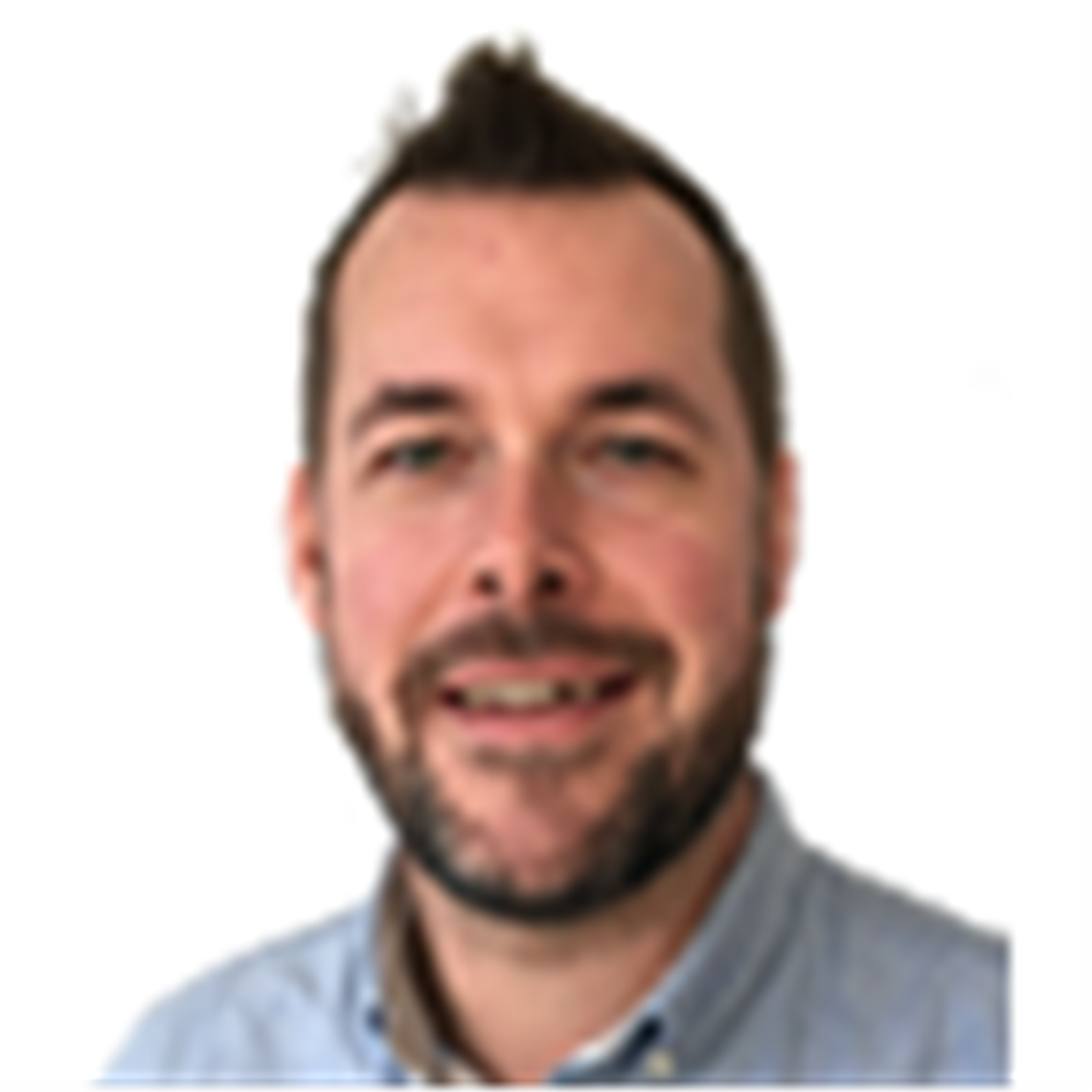
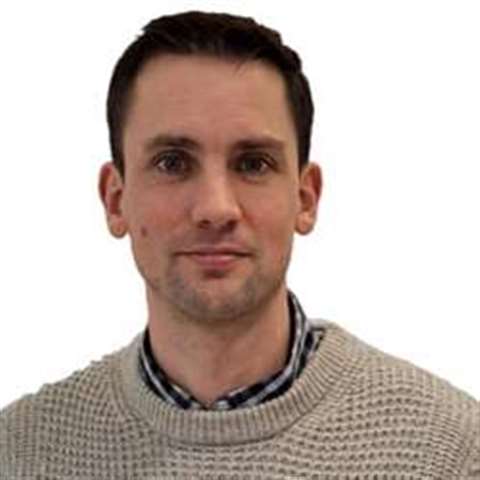
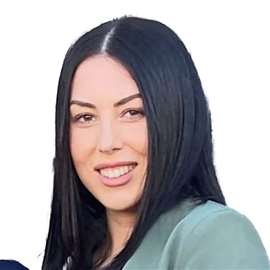
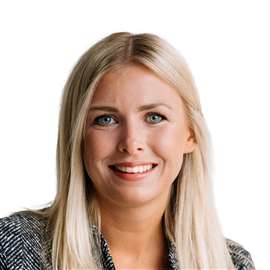