How to increase the sustainability of tall infrastructure
23 February 2023
To accommodate the world’s growing population cities are building taller infrastructure, but how does this fit with the global target of increasing the sustainability of infrastructure? Catrin Jones reports.
Tall buildings pose a unique challenge to sustainability because they offer both positive and negative environmental impacts. Positive impacts include reducing urban sprawl, promoting alternative transportation, and allowing efficient energy use on a district scale. But these benefits come at the cost of emitting more carbon dioxide to produce the required materials and to construct the building.
A tall building’s embodied carbon footprint is significantly higher than low-rise buildings on a per-square-foot basis. This is because the structure is usually responsible for the majority of a building’s embodied carbon footprint, and tall buildings require more structure to support their height.
Tall buildings have typically been constructed using steel or concrete, but what if there was an alternative that used more sustainable materials?
Sustainable alternative to traditional construction methods
Architecture and engineering firm Skidmore, Owings & Merrill and researchers from Oregon State University recently launched a research project investigating the performance characteristics of a hybrid wood and concrete structural floor system that may offer the industry a traditional flat plate construction alternative.
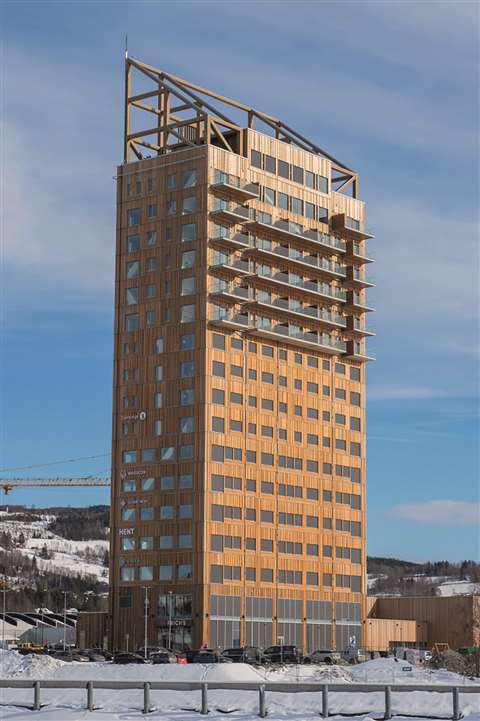
The research project’s purpose was to study and develop a conceptual structural system for tall buildings that are as sustainable as possible while remaining cost competitive with contemporary building techniques.
Sustainability is a challenge for high rise construction – another is a lack of space. Constructing a 50-storey building on the corner of two of the most well-known streets in central London took this to extremes with the development of 8 Bishopsgate.
“After many changes to both the client’s requirements and our own recommendations, we agreed that four tower cranes would be required on site at any one time, with two cranes moving onto the building’s two cores when they reached full height,” said Adrian Hawkins, Wolffkran sales director.
However, one of these cranes – TC1a – would require some clever thinking and a unique design if it was to work at all. Crane TC1a was to be a WOLFF 275 B, with a 45m jib that would be parked at a 13m radius out of service.
This crane would need to climb up the inside of a lift shaft that was only 2.9m wide. Additionally, its sway had to be kept to a minimum to ensure it did not clash with the jump-form rig being used to construct the shaft.
The use of 2m wide mast sections was considered but eventually discounted. “The tower would not have been stiff enough to limit the sway sufficiently if we’d used 2m sections,” commented Bernard Holman, Wolffkran engineering manager. “And the dimensions of the climbing collars was still too big to fit within the confines of the 2.9m lift shaft.”
Therefore, a sway-limiting 2.3m internal climber was used, but without the climbing collars.
What is the tallest building in the world?
As speculation continues around whether or not the 1km-tall Jeddah Tower in Saudi Arabia will ever be finished, plans are already afoot to build a 2km-tall skyscraper in the kingdom.
A 2km-tall building would exceed the world’s current tallest building, the 828-metre-high Burj Khalifa, by nearly 1.2km. And the Burj Khalifa is itself more than 300m higher than the 508m-tall Taipei 101, which was previously the world’s tallest building.
Such huge increases in height beg the question: are there limits to building supertall buildings and what governs those limits?
Peter Weismantle, director of supertall building technology at architecture firm at Adrian Smith + Gordon Gill Architecture based in Chicago, US, has decades of experience working on tall buildings.
He was part of the team that designed the 88-storey Jin Mao tower in Shanghai, China. In 2003, he took on the role of senior technical architect for the Burj Khalifa and helped to design the Jeddah Tower.
“I don’t think the limits are technological. First is money and the economics of these tall buildings,” he tells KHL.
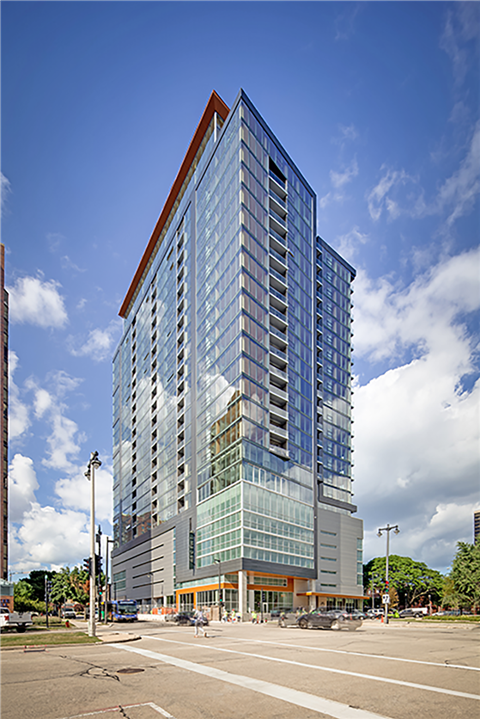
“In order to build tall, you have to build a big building in the sense that it has a lot of area – a lot of surface area and a lot of floor area. That is money. And the taller you go, the more the cost per square metre goes up.”
Tied to the cost of building structures at such a huge scale is the amount of time it takes – and time also means money. “In order to build these things anywhere near efficiently, you have got to build them quickly. And quick for a supertall means about five years. That is a long time, especially now with inflation the way it is,” he adds.
Tallest timber towers
High-rise buildings built with timber have been appearing more frequently on horizons as companies develop new products, techniques and materials to increase the sustainability of tall infrastructure. Norway has been spearheading this trend, finalising the wooden 85.4m Mjøstårnet in Brumunddal, but there is an even taller timber tower in the US.
Ascent, an 86.6-metre-tall mass-timber tower in Wisconsin designed by Korb + Associates Architects, was certified as the world’s tallest timber building in August 2022. It appears that the race has only just begun though. The Indian Ocean Island of Zanzibar is planning what is reported to be the next highest ‘green’ building in the world – a 28-storey apartment tower designed in hybrid timber technology.
Named Burj Zanzibar – burj meaning tower in Arabic – the high-rise is designed to reach 96 metres in height. It has been called a ‘vertical green village’ and would be the first timber structure in the world of such proportions.
The design of the mixed-use apartment and commercial building, in a beehive style, was unveiled to the public in October 2022. Dutch-born architect Leander Moons, responsible for the concept, said, “Burj Zanzibar is not just an outstanding building but a new ecosystem for the future of living.”
The tower, which will have 266 residences, is to be located in Fumba Town, East Africa’s eco-town developed by German-led engineering firm CPS. It is planned as a hybrid timber tower with a steel-reinforced concrete core designed to meet all required fire and life safety standards. The project is to be executed by a consortium of leading specialists from Switzerland, Austria, Germany, South Africa, Tanzania and the US. When completed, it would be the highest timber building in the world.
Mass timber building movement
In 2017, the Council on Tall Buildings and Urban Habitat published ‘Tall Timber: A Global Audit’. The study accounted for all 48 known mass-timber projects of seven stories or higher that had either been proposed, was under construction, or was completed.
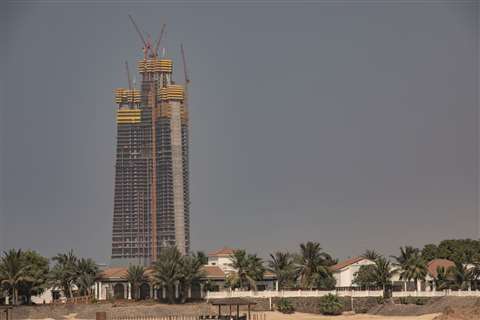
The mass timber movement has gained significant momentum since then with more than 200 mass timber buildings around the world that are seven stories or higher. Wood has undergone remarkable advances in its technological capabilities.
Recently, Ramboll and architecture studio Haptic Architects partnered to explore sustainable development through a regenerative modular tower. Doug Baldock, Director and Head of High Rise UK at Ramboll, says that to reduce carbon, the main structural frame centres around a timber structure comprising three-storey high-structural hard decks, with each hard or permanent deck supporting three intermediate soft or temporary decks.
“The regenerative high-rise uses hard floors, which are plated with cross-laminated timber (CLT). The load-carrying structures are made using a combination of glue-laminated timber sections and recycled steel,” said Baldock.
By adopting this approach to high-rise construction, it was possible to consider the modules in terms of volume, not floor area, boosting the flexibility and adaptability of the whole structure.
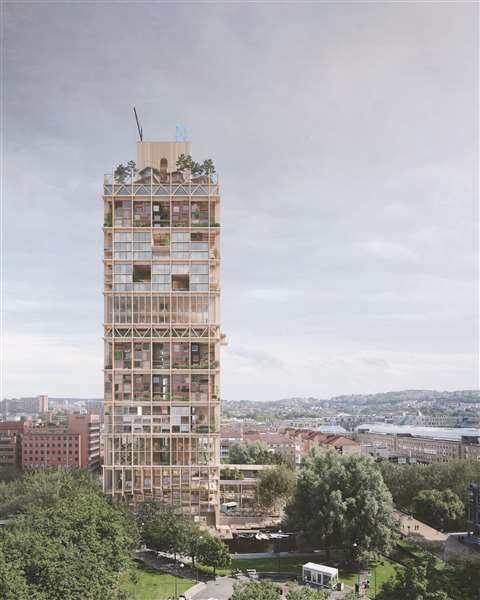
“Instead of demolishing the entire building,” adds Baldock, “obsolete modules can simply be replaced with new ones, without horizontal or vertical constraints, to fulfil new spatial requirements. Embedding flexibility and adaptability into construction philosophy provides an opportunity to make real progress towards sustainable high-rise buildings.”
As the structures are designed to last for a long time, the choice of building material for modular high-rise construction was based on keeping the carbon footprint to a minimum.
Those behind the sustainable structure hope to create a new precedence in the building industry. “In theory, adopting these construction philosophies could lead to buildings that could potentially last forever,” adds Baldock.
Falsework and formwork specialist Meva highlights that, whilst timber is a greener choice for some applications, this needs to be balanced against the environmental impact of deforestation to harvest the material and the waste created from plywood formwork.
Plywood formwork stores harmful carbon within the material, protecting the environment. Additionally, it can also be harvested and produced locally, so that the material does not have to travel so far to the site – which saves emissions from transportation vehicles.
With increased popularity for its sustainable properties comes increased demand, which is fuelling deforestation and creating an ecological balance, says Meva. According to the World Wildlife Foundation (WWF), trade in forest products has increased significantly in the last five decades, with illegal logging representing 40–50% of all logging in some cases.
The WWF adds that as forests store large amounts of carbon, destroying these areas contributes to global warming by releasing carbon into the atmosphere – around 15% of global greenhouse gas emissions are caused by deforestation.
Smart technology in construction
As projects are becoming increasingly ambitious, construction technology is developing at a pace that demonstrates its ability to support new and bold ideas.
Baldock of Ramboll believes that a powerful tool to create sustainable solutions for high-rises is integration with the digital environment.
“Tall buildings can be designed as platforms to take full advantage of the latest and future smart technology. Thousands of smart sensors feed data to the integrated Building Management Systems to allow the building to adapt and optimise for improved energy efficiency, safety and security.”
Despite sustainability traditionally being about the implementation of energy-efficient and renewable technologies to enhance the ‘green’ credentials of the building Baldock says that it is also about delivering a liveable environment to maximise the health, well-being and comfort of occupants.
“Using these strategies in an integrated way creates value for both our clients and society as a whole – and provides a blueprint for a sustainable high-rise.”
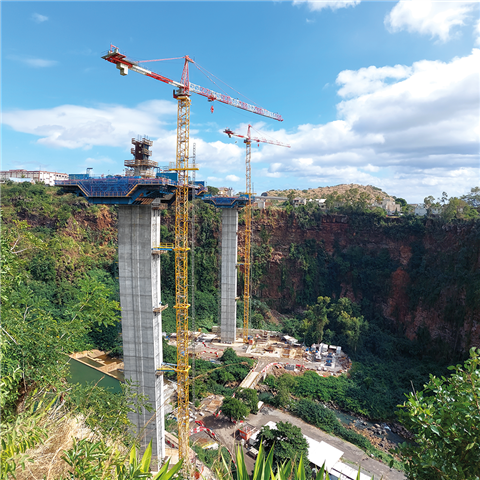
Providing the island nation of Mauritius with alternative access to its capital, Port-Louis, Doka worked with TGBV JV Transinvest-GCC-Bouygues TP-VLSi to deliver a solution for the country’s Road Development Authority, which centred around providing a formwork solution for the A1-M1 Link Road Grand River North-West Valley Bridge BR5.
Upon completion, the bridge will link two of the country’s most important highways, while helping commuters to avoid the long and often steep roads that traverse the nearby valleys and canyons.
Designed around a two-pier structure, with the highway suspended from pylons at a height of 90m, Doka’s engineers had to factor in seasonal weather conditions such as cyclones, which have already tested the project’s design with winds reaching in excess of 190km/h.
Both piers were built with a step height of 4.50 metres, poured in weekly cycles during typical lifts, with the centre wall thickness of each pier increasing with height. A formwork system was implemented to avoid changing out panels during transitions, while considering changes to platform design, soffit formwork and safe direct climbing platform access from stair towers and access hoists.
The project is estimated to be delivered in 2023.
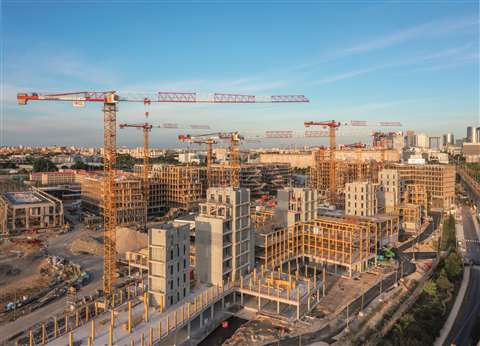
Ten Liebherr EC-B series tower cranes are involved in a €650 million (US$705 million) project in France to build the largest timber campus in Europe.
The campus is designed to create a new connection between nature and the workplace using solid wood construction.
The ‘Arboretum’ project on the banks of the Seine will provide 125,000 square metres of office and service space and will be mostly built of solid wood.
Measures designed to reduce the site’s carbon footprint include the reuse of materials, bioclimatic architecture and a geothermal system that will cover up to 80% of heating and cooling requirements.
Liebherr says that their top-slewing cranes are being used for positioning timber and concrete elements such as posts, beams, columns, staircases and lifts. This work is supported by the Micromove fine positioning mode.
The assistance system is said to make use of Liebherr’s drives so that loads are moved with precision over the course of several minutes and positioned with accuracy, which is said to protect precast filigree concrete parts as well as existing constructions.
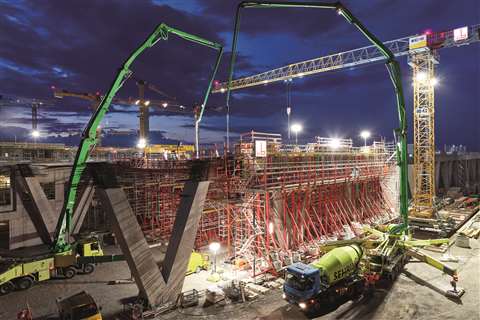
Frankfurt Airport, Terminal 3, is currently one of Europe’s largest infrastructure projects, due to be completed in 2024. Peri assisted Max Bögl with the construction of the drive-by platform, which will provide passengers with direct access to the departure level of Terminal 3.
The 550m long and 27m wide drive-by platform with its total bridge area of 15,300m² is supported by 70 V-shaped columns at a height of over 10m and connects the two access and departure ramps to the terminal. Engineers from Peri designed a customised formwork carriage using the VARIOKIT Engineering Construction Kit and the PERI UP Scaffolding Kit as a basis. It was 40m long, 25m wide and up to 12m high – and weighed just under 500 tonnes. The construction process was carried out entirely in 3D.
With an integrated hydraulics system, the entire formwork carriage could be lowered by 2.20m for striking and repositioning. Between the V-shaped columns, the Peri solution was made up of six individual carriages that could be separated for relocation and striking.
STAY CONNECTED

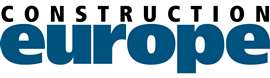
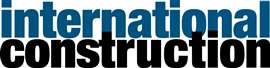
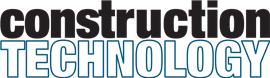
Receive the information you need when you need it through our world-leading magazines, newsletters and daily briefings.
CONNECT WITH THE TEAM
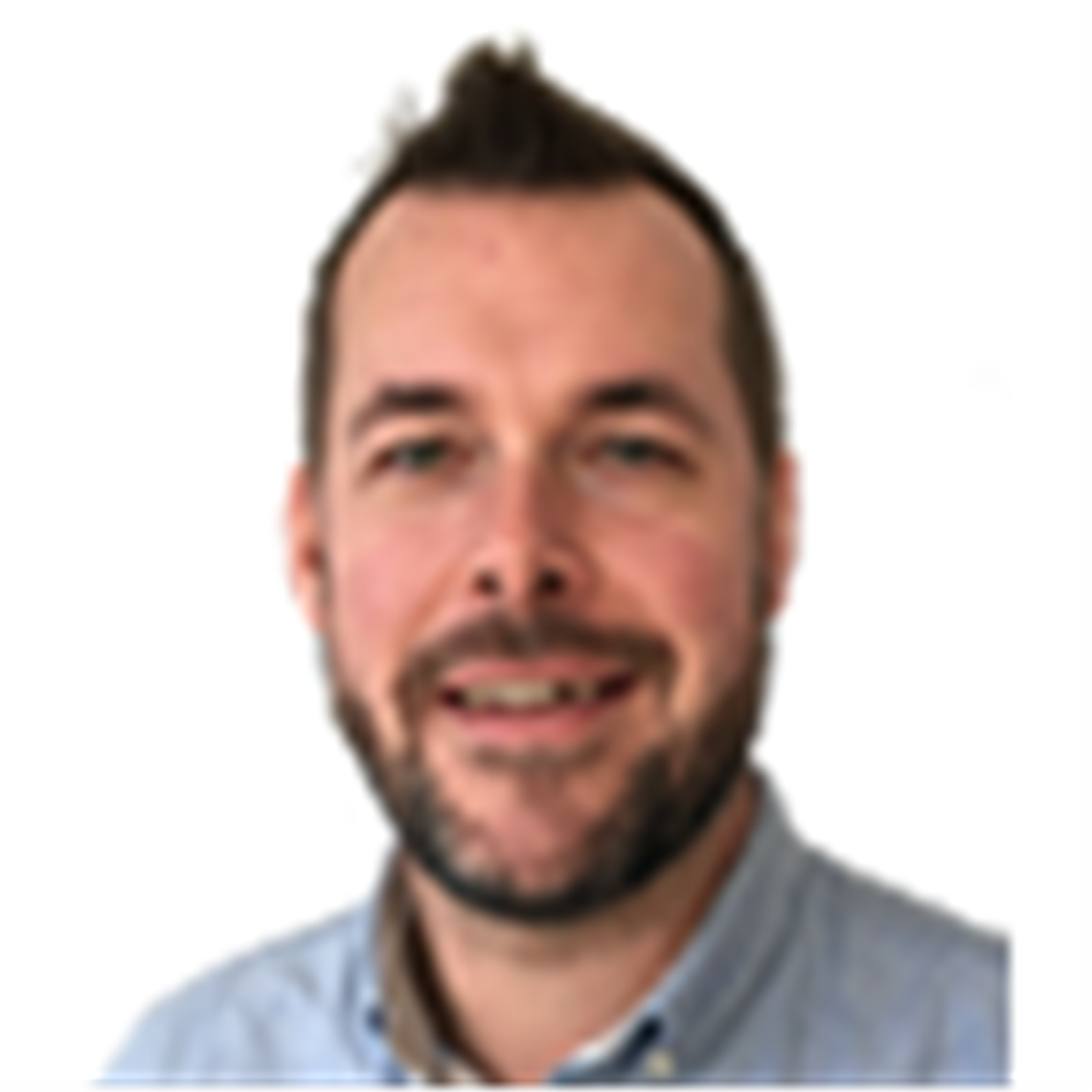
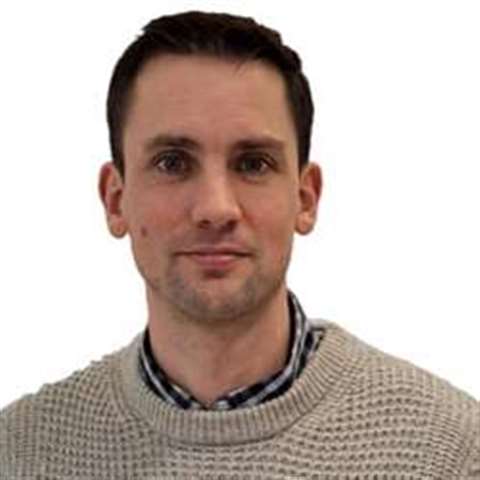
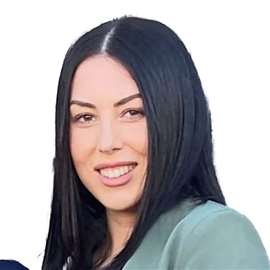
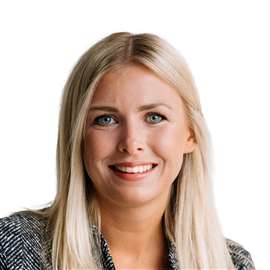