How is AI being used in construction?
01 September 2023
From helmet cams to robot printers, AI-enabled software solutions are increasingly being marketed by tech companies as quick fixes for the contractors. Lucy Barnard looks at some of the apps promising to make construction quicker, cheaper and safer.
To the casual observer, there is little to show that Rhinstrasse 143, a complex of five apartment buildings in east Berlin, Germany, has been built using artificial intelligence (AI) construction technology.
The E-shaped apartment complex of 330 flats, completed in March 2022 by German contractor MBN, became one of the first European buildings to be built using AI-enabled 360-degree footage from video cameras mounted on construction workers’ helmets.
The technology, developed by Israeli software startup Buildots enables project managers to compare the helmet cam footage with a BIM model of the site and then flags any discrepancies.
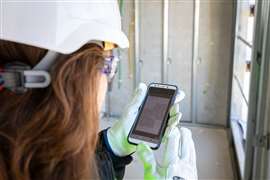
With this information, Buildots chief product officer and co-founder, Aviv Leibovici says project managers can accurately track real-time progress compared to the project’s plans and make scheduling adjustments as required.
“The cameras are mounted on a hardhat of a team member on site,” says Aviv Leibovici, Buildots co-founder. “As they walk around a video will be captured and what our tech will do is it will use the images from the video and the model and join the two together to understand what is going on so to know at what status every element of the construction is in right now.
“So, this socket could be a hole in the wall, that wall could be painted – that’s the sort of information that it captures.”
According to Buildots, by using artificial intelligence to compare the information from the video cameras with a detailed virtual model of the project, the MBN team was able to identify a total of 38 errors earlier than would otherwise have been possible, saving the company both time and money.
And Buildots is just one small example of a dizzying array of new AI-enabled, cloud-based tech applications that are starting to be used by contractors. AI – the tech behind Google Assistant, Siri and Alexa – is already a mainstay in the financial services, e-commerce and healthcare industries and is starting to gain acceptance in the construction industry.
Paul Wilson, digital director for Aecom Europe and India, says that artificial intelligence (AI), which works when systems ingest large amounts of data, analyse it for correlations and patterns and use those patterns to make predictions about future states, is already having a profound effect on the way infrastructure projects are planned, executed and managed.
“We continue to have a lot of manual processes in the construction industry,” says Wilson. “Our clients are starting to see that by using technologies like AI, machine learning and data science they can start to automate those manual processes, streamline workflows, and free staff up for other tasks whcih are a more valuable use of their time. It’s still very new within the construction industry but we’re starting to see them come to the fore much more.”
Using AI to keep projects on schedule and on budget
As one of Aecom’s 2,000 digital practitioners who make up Digital Aecom – a part of the multinational infrastructure specialist which specialises in offering digital consulting services as well as providing its own hosted services and digital adoption best practice, Wilson is in a prime position to witness a new wave of tech solutions that promise to use AI to solve some of construction’s most intractable problems.
Like Buildots, many of these are ultimately aimed at solving the age-old problem of projects running over budget and over schedule.
“The issues of budget and schedule overruns are so prevalent that it’s almost easier to give examples of projects where this is not the case,” says Brad Barth, chief product officer at US-based construction software specialist InEight.
According to a survey of 300 global construction professionals published by his company in June, just 50% of respondents said that their organisations completed construction related projects on time in 2023 while 49% said that they completed projects on budget.
In the US and Canada, the situation was even worse with just 42% of respondents reporting that their organisations completed projects on time and only 38% meeting approved budgets.
He says better data can help planners make better predictions about how long construction projects are likely to take in the first place and how much they will really cost. For contractors this means that they can set realistic expectations from the get-go. For owners, it means that they have the means of validating and assessing the bids received during contractor selection.
“Overall, what we see is that people are generally more optimistic than reality,” he says. “Historically there has also been a low bid mentality where the award of the contract is based primarily on price. That encourages the contractor to not surface some of those risks that should be covered with contingencies. Teams submit a low bid knowing that if and when the risks surface, they will be covered through a change order. That all leads to an unpredictable model between owners and contractors.”
Barth says that InEight, which provides project management software designed for the construction industry, is one of a number of project management software companies that enable a knowledge library of data from previous projects, which can be then used to optimise plans for new projects. The system’s augmented intelligence approach uses machine learning to supplement human input for more predictive results.
The company also enables planners to run schedules through a Monte Carlo risk analysis tool, a standards-based simulation approach that can identify cost and schedule contingencies for complex projects in a matter of seconds.
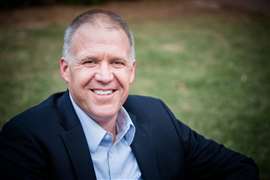
US software company Bluebeam, now part of the German-based Nemetschek Group software empire, provides digital workflow software for the architecture, engineering and construction industries.
Matt Wheelis, senior vice president of strategy at the company’s build and construct division, says that another thing AI can do is to look at the complicated schedule documents used by project managers, analyse the many interrelated large and small tasks involved and then map out the best order to complete those tasks in real time, taking into account the constantly changing circumstances of a project.
He says that AI-enabled tools like SmartPM can highlight to managers the chance to undertake a seemingly small and unrelated task early in a construction schedule that would often be overlooked by a human attempting to prioritise the same list, sometimes shaving days, or even weeks off a tight schedule.
“One of the challenges with construction schedules on these larger projects is that they can become unwieldy,” Wheelis says. “There are often tens of thousands of activities to coordinate, and the logic behind how they are all sequenced can get very complicated and difficult for managers to understand.
“Software can make this information more accessible and visible throughout the supply chain, making understanding complex schedules simple and graphical in nature for non-experts, opening up insights into logical problems and delays that would only be detectable through expert analysis before,” he adds.
How can AI make it easier for teams to communicate?
AI-enabled software is being used to solve the problem of communication difficulties between teams.
One of the most well-know of these is US software firm Nvidia, which runs a platform called Omniverse, designed to create virtual worlds and digital twins. It has teamed up with construction tech giant Bentley Systems to produce AI-assisted rendering, creating engineering-grade millimetre-accurate virtual models with realistic lighting that can be viewed on multiple devices, including virtual reality and augmented reality headsets.
The technology is already being used by engineering and consulting services contractor Brigantium at the ITER project in southern France where teams from countries all around the world are collaborating to build the world’s largest tokamak.
Lynton Sutton, managing director of Brigantium Engineering, says that although the official language of the ITER project is English, often teams from a variety of countries find it difficult to find the right words to exchange technical information and so, an intuitive photo-realistic virtual model helps to communicate critical information to these teams much more effectively.
“These kinds of visualisations are critical to project communications,” says. “In the past we relied on specialists devoting valuable time and effort toward creating these essential project deliverables. It was inefficient, but necessary. Now everyone on the project can create compelling visualisations in less time and of higher quality than previously possible.”
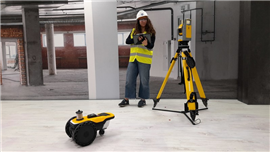
Trimble is another technology company attempting to do something similar. In November, it unveiled SitePrint, a collaboration with printing giant HP which uses AI-enabled robots to print detailed site layouts on the floor of indoor projects with pinpoint accuracy.
And yet, with so many software solutions to choose from, how can the average small or medium sized construction companies even begin to make sense of what’s on offer and start to use it?
Aecom’s Wilson says that a first step for any organisation is to come up with a coherent strategy to define what outcomes they want to achieve from a programme or project. Then, a digital implementation plan can be prepared, establishing exactly what data needs to be surfaced, what is already available, how reliable it is, and how this data can then be best presented and securely managed.
“It’s about being data driven in everything we do because everything we do is about the data,” Wilson says. “It can be data including GIS information, topographical, drone information but the more information you capture and the more you build these data sets in layers. So, you’re layering the information to help you to build up that full picture. You’re increasing the quality of the information to help make better and more informed decisions.”
More AI apps for construction
Wilson says that a growth in the number of “low code” solutions and platforms that enable anyone to apply AI automation without writing a line of code, combined with an increasing popularity of data-driven design and construction, is likely to spell a proliferation in AI-enabled and AI-driven apps for the construction industry in future.
“What we’re starting to see in the industry is more citizen developers – people who are building applications easier,” he says.
“To build an app in the past you would have had to know scripting and Java and all sorts of fancy IT code. But now many elements are pre-programmed and you can create an app that automates processes for you. This has been in the banking sector for a long time but we are seeing this coming into our industry.”
STAY CONNECTED

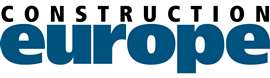
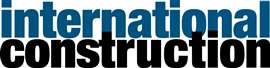
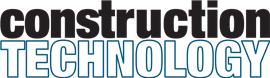
Receive the information you need when you need it through our world-leading magazines, newsletters and daily briefings.
CONNECT WITH THE TEAM
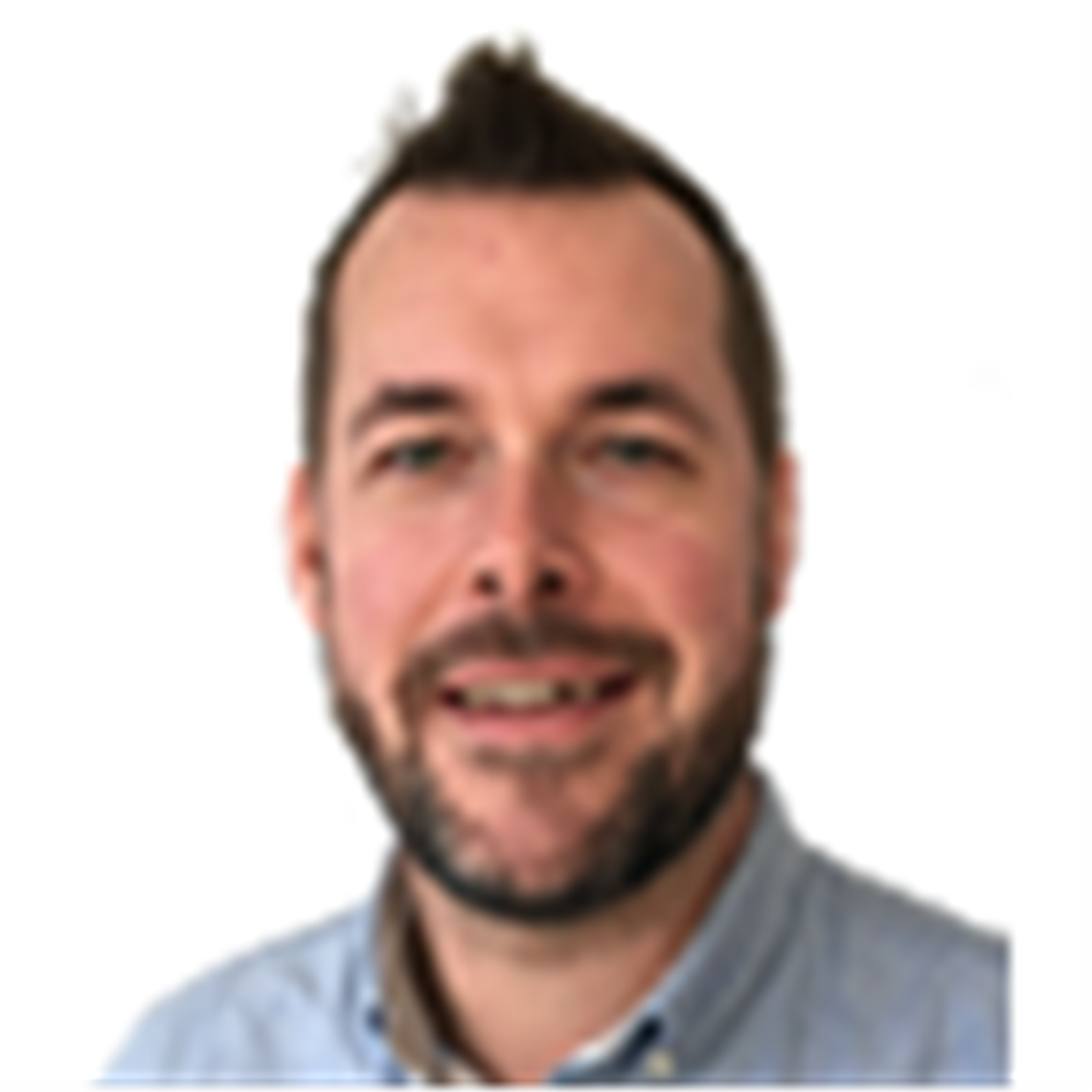
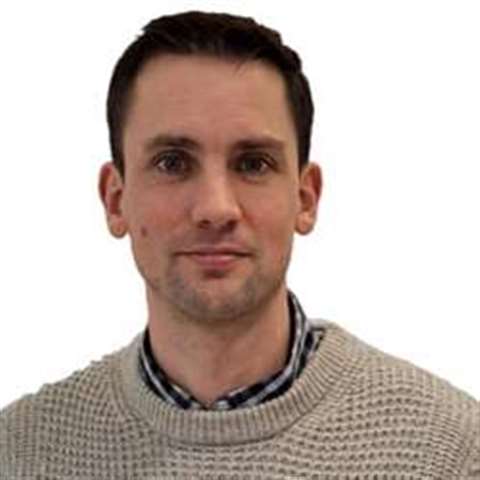
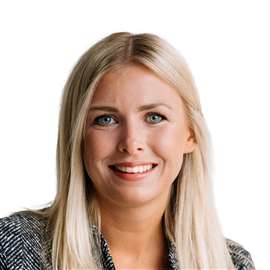