Read this article in French German Italian Portuguese Spanish
How construction is under pressure to decarbonise its cement more quickly
07 May 2025
Decarbonising the cement industry is proving to be one of the hardest challenges on construction’s journey to net zero and the sector needs to start moving even more quickly.
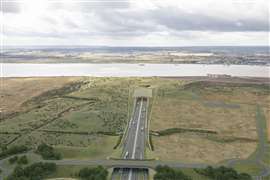
That’s the message from Andrew Kidd, director of environmental sustainability for National Highways’ £9 billion (€10.6 billion) Lower Thames Crossing Programme in the UK.
Cement relies on clinker, the output of cement kilns which forms after heating a mix of raw materials (including limestone and clay) to an intense heat of 1,450°C (2,650°F). Combined with the chemical reactions involved, the carbon emissions resulting from the process account for 90% of cement’s total carbon footprint.
Slag from blast furnaces used in steel production has long been used as a low-carbon supplement to cement in concrete mixtures. But as the steel industry also moves to decarbonise, there’s a problem.
While today’s steel production is based 70% on blast furnaces and 30% on electric arc furnaces (EAFs), steel production is becoming increasingly reliant on the latter because it is a greener method of producing steel. And that means less slag for lower-carbon cement.
Steel manufacturing will rely increasingly, possibly exclusively, on EAFs in the future.
As a result, the cement industry is being forced to radically rethink its processes, approaches and systems, and find greener replacement ‘ingredients’ to drive a low-carbon future.
Construction’ having to innovate much faster

Kidd, who leads the decarbonisation of the Lower Thames Crossing, which relieves pressure on the Dartford Crossing over the Thames near London, is looking for new ways to decarbonise cement used in the project’s construction.
“We set the Lower Thames Crossing up as an industry pathfinder for low-carbon construction. Our mission is to build the scheme for the lowest emissions we possibly can – but, with all projects now, you must demonstrate that that infrastructure is built with a carbon intensity consistent with the carbon budgets,” he says.
“Our biggest challenge is that the construction industry is currently emitting more carbon than it did in 1990 and yet we have a nationwide commitment to achieve 68% reduction by 2030. We will be mid-way through construction of the scheme in 2030 and want to play our part in delivering our national commitments on carbon reduction. The challenge is only going to grow. The government recently announced a new target of 81% reduction in emissions by 2035 - so we have a huge opportunity to do something radically different with the Lower Thames Crossing project.”
Kidd notes that the construction industry, generally conservative and used to evolving only slowly, is having to change its approach.
“It’s now having to innovate at a much faster rate than it has done for the last two centuries. There has been a real shift in the approach of the big players and their appetite to innovate and bring new products to market.”
Low-carbon start-ups offer new solutions
One start-up company that has devised a new approach to low-carbon cement is Reclinker (previously known as Cambridge Electric Cement), a spinout from the University of Cambridge.
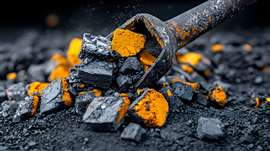
Recently named on this year’s Cleantech Group 50toWatch list, Reclinker has succeeded in making the reactive component of ordinary Portland cement while avoiding the main sources of emissions.
The method involves taking the old concrete from buildings and structures that have been demolished, crushing it to separate out the old (and, at that point, non-reactive) cement paste and the clean aggregate.
While the aggregate can go on to be used elsewhere, the old cement paste is passed through an EAF alongside the regular steelmaking process and, thanks to Reclinker’s proprietary process, out comes new cement, which the company calls Cambridge Electric Cement (CEC).
The scientific journal, Nature, recently reviewed and published Reclinker’s full spectroscopy and materials analysis, and confirmed that it meets the specifications of ordinary Portland cement – that is, more than 67% Alite and Belite compounds together in the optimum ratio, and able to deliver both ‘day-one’ and ‘ultimate’ strength.
Kidd says: “What Reclinker is producing is not a supplementary material like blast furnace slag; it’s a direct replacement for the cement content itself. And while there is inevitably a green premium to pay for such innovation, it doesn’t require the construction industry to change anything within its accustomed methods of working.”
New supplementary cementitious materials (SCMs)
Pete Winslow is director of Expedition Engineering at The Useful Simple Trust, a family of professional design practices driving change. He is focused on pushing best practice and innovation in concrete and steel decarbonisation to create a better built environment.
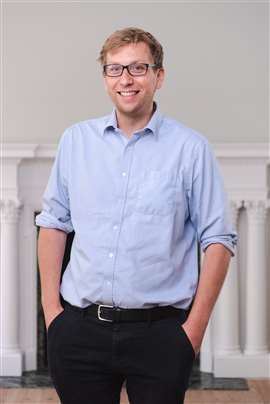
Winslow, who also chairs The Institution of Structural Engineers’ research panel and the Infrastructure Client Group’s Concrete Decarbonisation Group, says: “Overall, the cement industry is not decarbonising fast enough. It’s been difficult because it’s a hard material to tackle and there are many existing assets around the world with permits, planning permissions and processes in place to make cement and concrete. We need concrete and cement on a day-to-day basis otherwise we can’t build nuclear power stations, the foundations for wind turbines, reservoirs for our water security, our flood defences, or even low-carbon public transport.”
“The industry will transition in time – but we are going to need all the big global cement and concrete players to come on the journey. Many are now starting to, but the focus isn’t quick enough. And this is why the startups, the disruptors who can innovate and try something different, are key.”
Alongside Reclinker, he sees value in start-ups like Seratech and NeoCem which are filling the gap left by the diminishing quantities of blast furnace slag to offer an alternative halfway solution. These companies are focused on producing supplementary cementitious materials (SCMs), which reduce the carbon footprint of concrete by displacing a portion of the cement used in a mix. Aside from blast furnace slag, conventional SCMs include calcined clay, finely ground limestone and fly ash (a residue left from the combustion of coal). Provided only a percentage of the cement is displaced, the carbon footprint of the overall mix can be lowered without significantly affecting the performance of the concrete.
Winslow adds: “There are very few technologies which can claim to be complete carbon eliminators why is why it’s critical to scale up companies like Reclinker and alternative SCMs such as calcined clay, which are widely abundant and relatively cheap too. Many blast furnaces won’t be running for that long, which means we need to be using alternatives to blast furnace slag. Some heat-treated calcined clay can be used to substitute 50% of cement - enabling great concrete.
“Although there are huge amounts of steel being reprocessed in arc furnaces, the cement making capacity is not nearly as much as the total amount of cement that the world needs. Recycled cement would go twice as far if you blended it 50:50 with calcined clay rather than just using it as a ‘like for like’ product.”
Entirely new cements
Meanwhile, US-based companies like Sublime Systems, a spin-out from Massachusetts Institute of Technology (MIT), and California-based Brimstone are focused on delivering greener, altogether new cements.
Brimstone starts its unique process with a ‘new’ rock – that is, carbon-free calcium silicate rocks instead of conventional carbon-heavy limestone, which releases CO2 when processed.
Sublime’s approach uses electrochemistry instead of heat and combustion to produce a low-carbon cement. Currently still in the trial phase, they have had some success producing calcium hydroxide, which when combined with silica, can be used in place of cement. Although such materials may demonstrate ultimate strengths similar to Portland cement, curing times and early strength may be different from what the construction industry is used to.
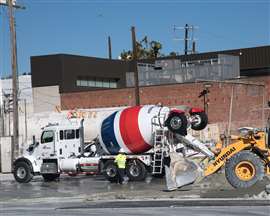
Nevertheless, Sublime has, to date, raised more than $200 million from leading climate tech investors, leading cement producers and the US Department of Energy cooperative agreements, and is looking to build a first-of-its-kind plant this year.
Kidd says: “Being based in the US, one of the advantages that Brimstone and Sublime have is access to bigger and bolder government investment. I would like to see more public and private sector investment in supporting the UK businesses in this sector. The construction industry doesn’t invest in itself nearly enough. Our big construction companies typically operate on tight margins, and it can be hard to reinvest. And, looking at the long-term statistics in the construction sector, the investment in R&D is pretty low compared to other industries. The great opportunity now is to turn the paradigm on its head, invest in the future and create an industry that is globally competitive in a net zero world.”
Carbon capture and storage (CCS) meanwhile remains a hot topic with our UK Government. This process aims to capture the CO2 that’s emitted at the time of making cement and immediately sequester it.
Kidd says: “This idea that you can take your existing cement, bolt on your carbon capture, and it’s going to be an important part of how we get to zero carbon is just not going to be applicable for everyone or everywhere. The UK is lucky to have old gas fields in place to put/ use the carbon – but that isn’t true for all cement plants around the world. Whereas there are already a lot of electric arc furnaces globally, which makes the electric cement option inherently super-scalable – with the added advantage that the construction industry won’t need to adapt their processes.”
STAY CONNECTED

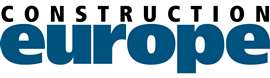
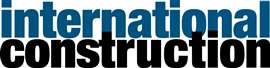
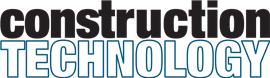
Receive the information you need when you need it through our world-leading magazines, newsletters and daily briefings.
CONNECT WITH THE TEAM
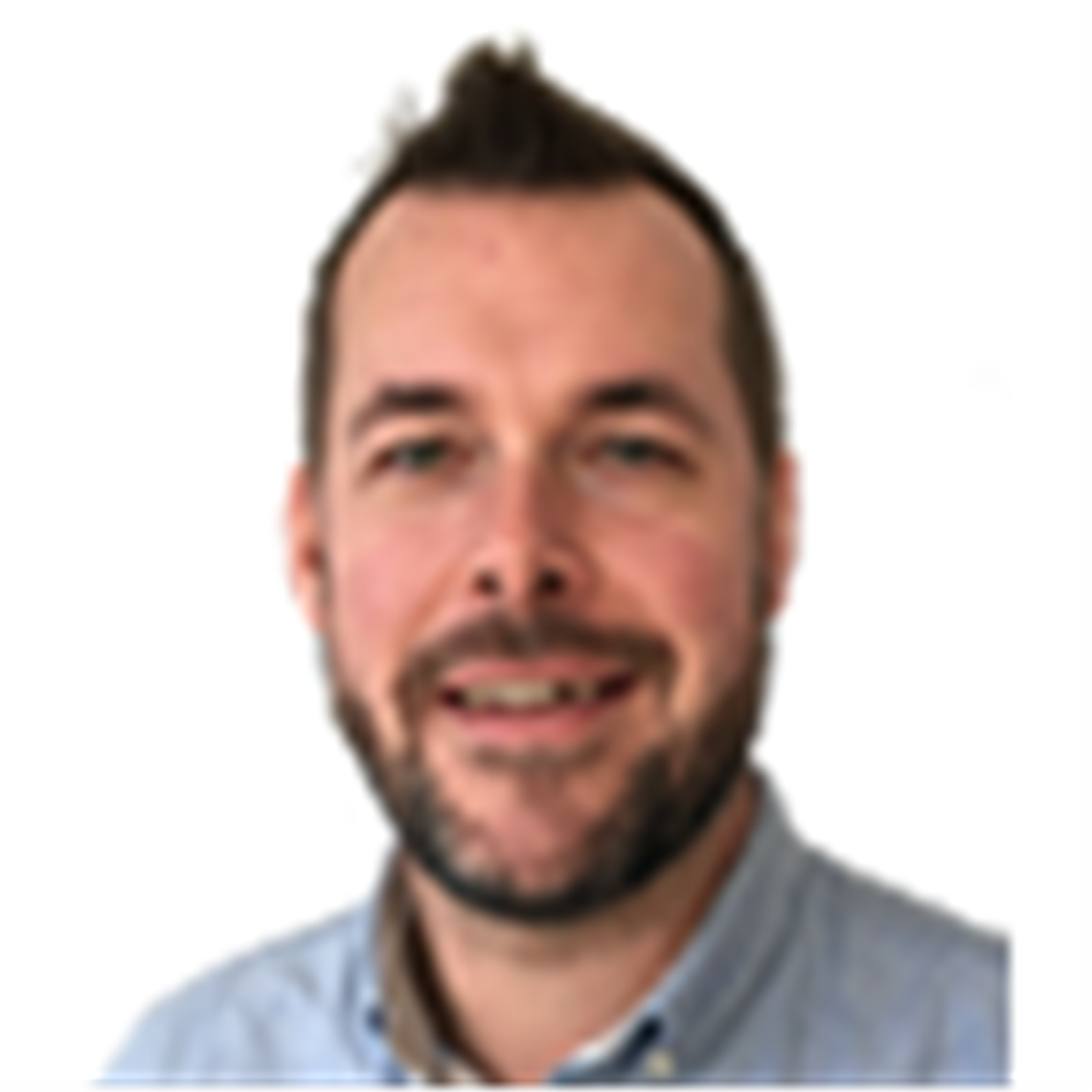
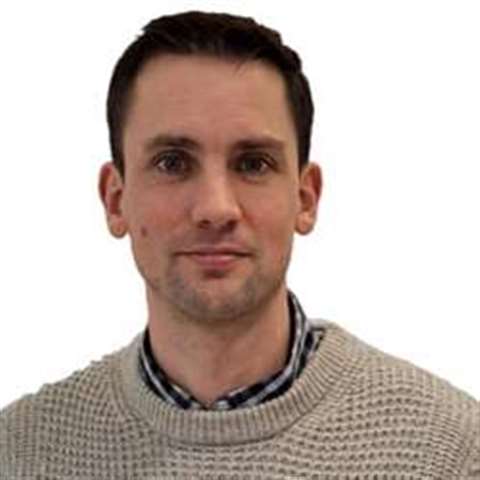
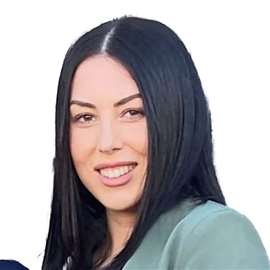
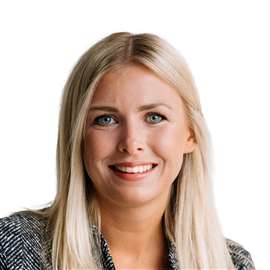