How construction equipment manufacturers are overcoming their supply chain headache
09 June 2023
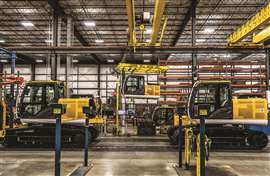
Few people give much thought to how impressively smooth modern supply chains are. Until they start to go wrong, that is.
For years it was taken for granted that manufacturers could collect together and assemble a disparate collection of parts and components from all over the globe just in time.
But recent events have conspired to stretch supply chains to their limits.
A global shortage of semiconductor chips in the wake of the Covid-19 pandemic, labour shortages, an energy supply crisis and transport disruptions have disrupted the flow of goods of all kinds. And the construction machinery industry has been no exception to that.
As Terex CEO and president John Garrison noted in a call to investors earlier this year, “It just takes one part for us not to be able to ship to a customer.”
Concern around not being able to deliver a machine to a customer on time or in the volume required has been pushing OEMs around the world to rethink their supply chain strategies.
So how are they approaching it and what strategies are they developing to avoid future problems?
Supply chain woes easing
First off, it appears that supply chain problems are starting to ease.
Following its Q1 2023 trading update, Caterpillar’s CEO Jim Umpleby told investors that improvements in the supply chain meant it was able to make stronger shipments, particularly in the construction segment.
“We have a diverse group of suppliers and a diverse product line. We did see some improvement in the quarter. There are still some areas of strength and it’s very different product by product. Even though you’ll see a number of suppliers in better shape, all it takes is one component to prevent you from shipping an engine or machine.”
Despite the improving situation, Umpleby noted that certain areas, such as larger engines, were still “more of a struggle”. Semiconductors were also still a challenge.
“Certainly we did still experience inefficiencies associated with supply chain challenges, and that had the impact on us because we’re still doing things like workarounds and it’s not anywhere as smooth as it needs to be,” he added.
Shifting production locations
Meanwhile, Bobcat confirmed that it has been developing several initiatives to diversify it supplier base, as well as running regular supplier capacity audits to secure its supply needs.
“The geopolitical and economic landscape of trade restrictions, shipping costs, and supply chain bottlenecks is constantly evolving,” Tomas Pribyl, supply planning senior manager at Bobcat told International Construction.
“We are adjusting manufacturing of our portfolio in individual plants around the globe accordingly.”
In recent years, Bobcat has moved production models for its Asian, Latin American and Oceania markets to Asia, where it has opened a new production facility. Bobcat said the move put production closer to its customers.
“This helps to kill several pain points at once: Reduce shipping costs, carbon emissions, customer order lead time, and improve resiliency,” said Pribyl.
At the same time, it has freed up production capacity in Bobcat’s European and North American plants for production models for European and North American markets.
In a similar vein, Terex will move production lines for its access equipment brand Genie to a factory in Monterrey, Mexico later this year.
It is moving a range of its scissor lifts produced in China, as well as some of its vertical mast lifts from its Redmond, WA facility to the new plant. Eventually, it also plans to manufacture all of its telehandlers there too.
Terex CEO and president John Garrison said, “The Monterrey facility was to improve our global competitiveness and diversify our global footprint.
“Yes, it will provide some incremental capacity, but that’s not why we made the investment. We made the investment to improve our global cost competitiveness, and then to utilize our Mexico supply chain as well.
“We think that will put us in a strong position…for supplying our U.S-based manufacturing.”
And Ken McDougall, president of Skyjack, which manufactures access and materials handling equipment told Access Lift & Handlers and Access International how the company has revisited its supply chain and logistics with a view to more localisation.
The company has invested $85 million in a new plant, also in Mexico, as well as investing $40 million in a plant in China.
Smoothing existing supply chains
But beyond shifting the geographical location of production facilities, OEMs are examining what else they can do to make supply chains run more smoothly and efficiently.
That can be a challenge, as Volvo Construction Equipment’s outgoing president in the Americas sales area Stephen Roy told International Construction.
“Supply chain issues have eased a touch, but you still have popups of events. We’ll place orders for subparts and then you’ll find they’re two weeks delayed. It’s just erratic,” Roy said.
“We’re having more conversation about regional supply chains and what that would look like going forward. But it’s hard to replace tier two, tier three suppliers in a short time. We’ve created this structure that’s very international.
“It’s not something you can untangle very easily, but I think the purchasing group works very closely to our supply base. We give them the technical support they need to help find a solution and continue to work with our suppliers.”
Technological solutions
Bobcat is currently reviewing and optimizing its product portfolio from a supply chain perspective, in order to reduce the overall complexity of the planning, procurement, manufacturing and shipping process.
It hopes that the simplification will bring more end-to-end stability and predictability, lower operational costs and ultimately a more reliable supply to customers.
To achieve that, it has also been working to develop new software solutions to drive efficiency.

The company is currently considering major investment into its enterprise resource planning (ERP) infrastructure and to make the supply chain more robust.
And Pribyl thinks that technology will have a major role to play in this respect.
“We have successfully integrated tools such as robotic process automation (RPA), predictive analysis and others,” he explains.
“We see that to stay ahead of the crowd, the traditional approach of keeping business and IT in separate organisations no longer serves its purpose.”
Pribyl says that Bobcat has changed its approach to hire and integrate people with strong IT skills directly into the business organisations and empower them to collaborate directly with IT experts.
“Together, they can then quickly adopt new technologies as they come, be it artificial intelligence or a major enterprise resource planning (ERP) upgrade.
“From our perspective, adoption of new technologies is not so much about implementation of one or other specific tool, but rather the right culture and people, who embrace all the new technology innovations and are keen to adopt them as soon as they emerge.”
Diversifying suppliers
And Terex has been working on diversifying its suppliers and increasing the number of options it has when availability is tight.
That’s important because the entire industry is still suffering from excessive lead times, Garrison said.
He added, “There is a tremendous amount of work going on in our supply chain teams around the world to really increase the number of suppliers that we are working with, dual sourcing, modifying design.
“We are in the business where you need a 100% of the parts to ship a product.”
STAY CONNECTED

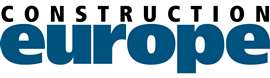
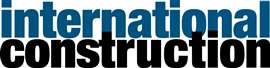
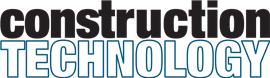
Receive the information you need when you need it through our world-leading magazines, newsletters and daily briefings.
CONNECT WITH THE TEAM
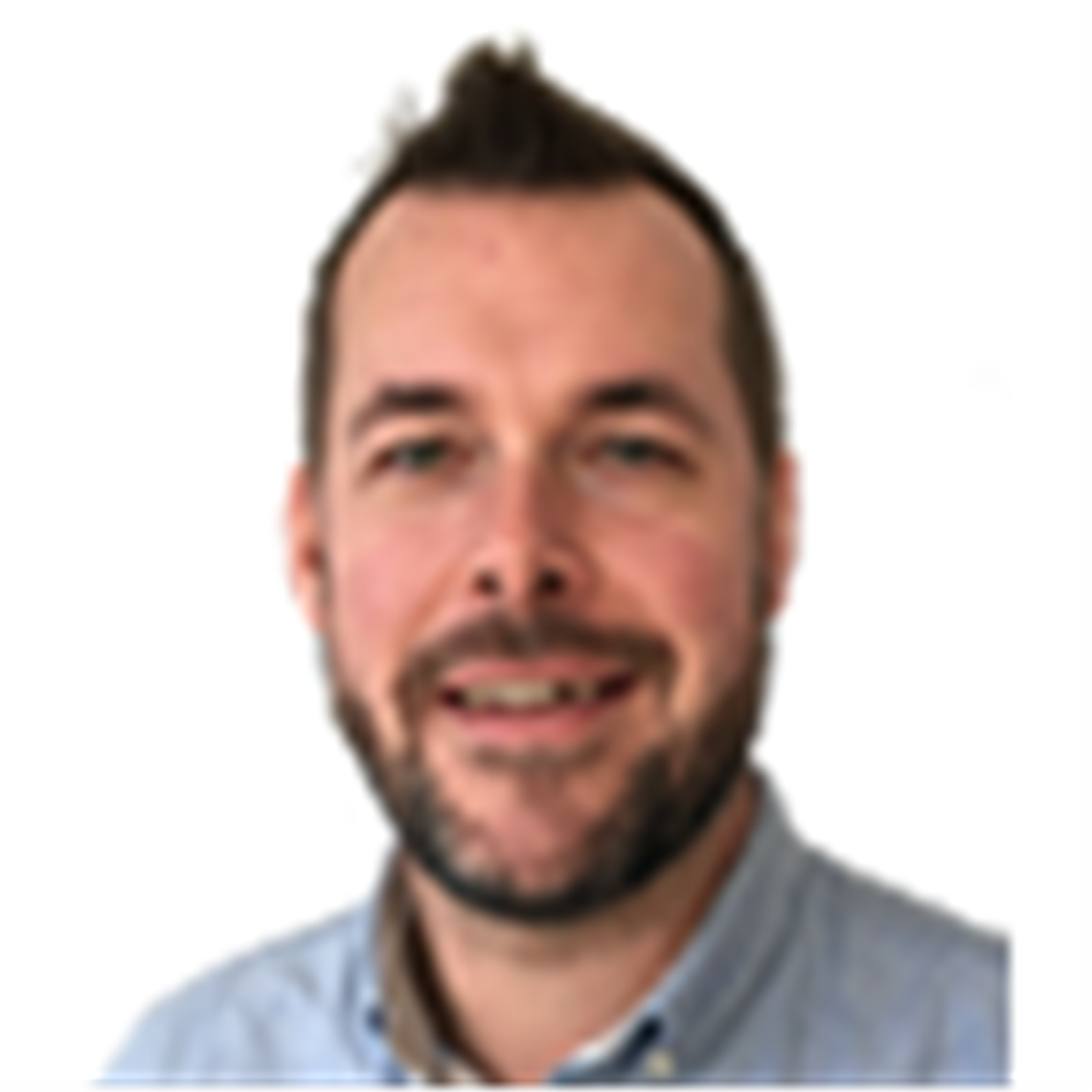
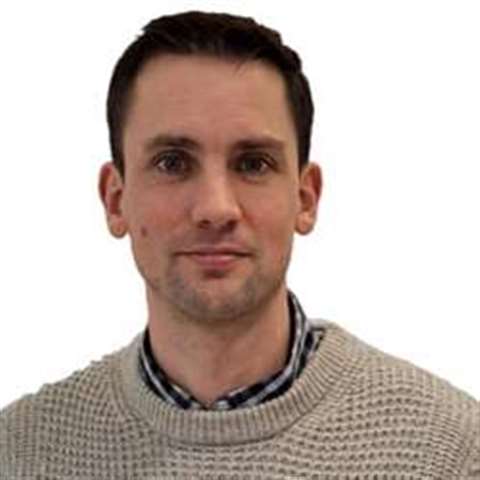
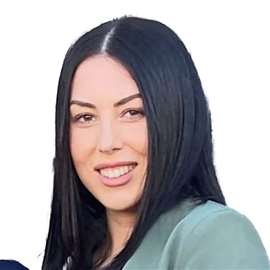
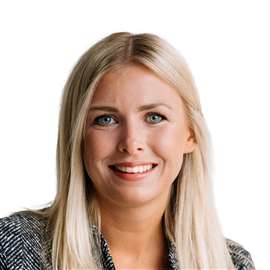