High-rise construction: Reach for the stars
31 August 2016
High-rise construction presents itself with tremendous challenges and opportunities. It’s a chance for crane, formwork and concrete pump manufacturers to bring new ideas to the table, among many others, to ensure buildings are constructed in the safest, and equally most impressive way possible.
Once completed, such buildings stand above others around them, which provides manufacturers and architects with an even bigger incentive to innovate impressive new machines and materials.
Beginning down under, Jaso Tower Cranes says it’s working on one of Sydney’s most important projects on the city’s waterfront, on what it describes as Australia’s gateway to the world.
The company has designed a unique lift shaft climbing system and a 2 m square mono block tower leg to reduce climbing stages, as the project required shorter break-out times to maximise time-efficiency on the job. Jaso Tower Cranes says the need for cranes with a high-load capacity, which are corrosion resistant, will make this possible, hence the company’s new design.
The project is using up to 14 cranes, some with capacities of 24 and 36 tonnes.
The company notes that due to site constraints, as well as accelerated time schedules, it had to come up with solutions to ensure expectations were met. For example, grillages cantilevered from basement slabs were used to locate the external cranes, which allowed intricate basement works to proceed without problems by tower crane bases.
Another solution the company used was the need for electric tower cranes to work to the highest environmental standards on such a high-profile project. Jaso says that its cranes met and exceeded such requirements.
A final solution was to use a single line pull of 9 to 12 tonnes to ensure the required components could be raised to their full height in the fastest time possible. Jaso says this involved designing a bespoke winch system.
Meanwhile in Europe, wind energy company Enercon used a Liebherr 1000 EC-B 125 Litronic tower crane to erect a wind turbine with a hub height of 149 m in Germany - the largest turbine erection ever for this crane, the company says.
The turbine - with a rotor diameter of 115 m - was erected at an altitude of around 800 m in the Prechtaler Schanze Wind Farm in the Black Forest, Germany, on the hills between the towns of Gutach and Mühlenbach. The 1000 EC-B, with its small footprint, had never before been assembled to such a height for Enercon.
With its 31.5 m jib and a hook height of 164 m, the crane was still able to hoist 100 tonnes reeved with four falls of rope. The capacity of this crane is 125 tonnes on six falls of rope and 100 tonnes on four.
The area required for erecting a complete flat top tower crane is approximately half of the normal standing area of other crane systems, Enercon said. The jib used in this case was very short, which is why no additional site clearance work was required for its assembly.
In addition, the logistics required to transport the 1000 EC-B 125 is much less than for comparable crane systems since the various components of the tower crane are supplied in small packages. The jib components of the large crane can be inserted into the tower elements, transported on a truck and assembled on site.
A 200 tonne capacity Liebherr LR 1200 crawler crane was used to assemble the tower crane to its initial hook height of 39 m. From there the tower crane erected the wind turbine and climbed the turbine tower as it rose using its own climbing equipment.
It was climbed to a hook height of 110 m and guyed to the wind turbine at a height of 100 m. Using this single guying, the crane climbed to a final hook height of 164 m. Both free standing and also fully climbed and guyed, these represented hook heights that Enercon had never achieved before.
Staying in Germany, Schwing Stetter says its stationary concrete pumps and separate placing booms have once again proved their reliability under extreme conditions, during the construction of the Upper West in Berlin.
The tower will measure 188 m and will be distributed across 33 storeys, resulting in being one of Berlin’s tallest buildings.
Schwing Stetter says the last storey has now been completed.
Motel One, which will dominate most of the building, will comprise of 18 floors with 580 rooms. The building will also offer several floors of office space in addition to a sky bar.
The company says that Ed. Züblin AG relies on the equipment and specialists from Godel-Beton when it comes to its concrete-pumping needs, which in turn uses one of Schwing’s stationary concrete pumps and separate placing booms. Cemex Deutschland AG was responsible for producing and transporting the concrete used for this project, delivering types of concrete with various strength classes.
Schwing says that C 30/37 concrete was used to concrete the ceilings and core walls. The columns of the skyscraper are made of C 80/95 concrete up to the 15th floor, and C 50/60 concrete was used beyond that.
Over to Sweden, construction company JM Sverige is about to finish the Kista Tower – a residential building located in the district of Kista, in Stockholm, Sweden. The complex is formed by the 120 m-high Kista tower – which is 35 storeys – and the smaller K2 building –which is 15 storeys – which, together, will comprise of 362 apartments.
For the construction of the Kista tower, Edins Byggkranar provided JM Sverige two brand new Linden Comansa tower cranes in September 2013. The first crane to arrive to the jobsite was a Linden Comansa 21LC750 48t, erected with 50 m of both radius and height. JM Sverige says the flat-top tower crane helped to assemble the second Linden Comansa tower crane, a 16LC185 8t, with a 35 m radius and height of 32 m.
The cranes were first used to help construct thick concrete walls in the basement of the building. From there, the 21LC750 48t started with the rising and positioning of the prefab walls that shape the building.
From floor 8, both walls and floors were prefabricated, allowing the crane to build each floor very fast, says the company. JM Sveridge also say that the 21LC750 worked three floors ahead of a team of workmen, who set the electrical and pipe installations, and used a concrete pump to fill the floors, leaving two empty levels between the tower crane and the workforce for safety reasons.
Reviewing other major high-rise projects around the world, Cemex LatAm Holdings (CLH) has begun work on a tower project that it says is bringing new construction methods to Colombia.
Atrio, in the capital, Bogota, is a multi-purpose development comprising two towers: one will stand at 201 m, with 42 storeys; the other will reach 268 m and have 58 storeys.
When the US$ 415 million project is completed, the larger of the two towers will be the tallest building in Colombia.
The volume of concrete and equipment and the size of the team in place to install the first tower’s foundation plate is on a scale not seen before in the country, according to CLH.
To deliver the required amount of material for the plate – made from a single 24,000 m2 slab with a height of 3m – an immense 7,380 m3 of concrete had to be delivered to the site before being pumped uninterruptedly for 38 hours.
To ensure the continuous flow of concrete, some 1,000 ready-mix concrete truck trips were made, with six ready-mix concrete plants in continuous use.
A team of more than 300 people worked around the clock, to complete the construction of the huge slab, which now sits 22 m below street level.
Carlos Jacks, CEO of CLH, said, “We are proud to participate in a project that will reshape Bogota’s landscape and that delivers new construction methods to Colombia. This type of project demonstrates the company’s human, logistical, and technical capabilities.”
Meanwhile, in New York, a new supertall tower is to be built by a joint venture consisting of Chinese and US developers.
The 472 m-high Central Park Tower is being developed by Extell Development and the US subsidiary of Shanghai Municipal Investment (SMI) and is set to become the tallest residential building in the western hemisphere.
The cost of the project is reported to be around US$ 3 billion, with Adrian Smith + Gordon Gill Architecture – architects of both the Burj Khalifa in Dubai and the even taller under-construction Jeddah Kingdom Tower in Saudi Arabia – responsible for the design.
Slated for completion in 2019, the tower will provide a combination of high-rise residencies and retails units.
Extell CEO Gary Barnett said, “We believe the superb location, views, design and quality of Central Park Tower will make it the most important residential building ever to be built in New York City.”
As mentioned, Jeddah Kingdom Tower, in Saudi Arabia, will become the world’s tallest building after a funding deal was secured to finance the last phase of construction late last year.
Work had already begun up to the 26th storey of the tower, north of Jeddah, and the new funding will allow the building to rise to its proposed 200 floors by 2020.
An EC Harris and Mace joint venture is project managing the £ 800 million (US$ 1.2 billion) job. Once completed, the 1 km skytower will be taller than the 830 m Dubai’s Burj Khalifa building in Dubai and four times the size of The Shard in London.
The Kingdom Tower will have enough room to include a five-star Four Seasons hotel, Four Seasons serviced apartments, office space, condominiums and an observatory that will be higher than the world’s current highest observation deck.
Heading east once more, this time to Hong Kong, Gammon Construction – Balfour Beatty and Jardine Matheson’s Hong Kong joint venture – has been awarded has been awarded two contracts worth £ 599 million (US$ 847.91million) in total, to build a new office tower and a residential block.
The bigger of the two contracts – the redevelopment of Somerset House, in Taikoo Place, Hong Kong, China – is worth some HK$ 4 billion (US$ 513.61 million), and will see a redevelopment of the site in to a 48-storey office building on top of a two-storey basement.
The project will comprise a number of office buildings and is home to companies including AXA and JP Morgan. Swire Properties, which owns the site, also plans to redevelop two other buildings on the site – Cornwall House and Warwick House.
The project is expected to be completed in 2018.
The company added that a workforce of 1,400 will be in force during the peak construction period.
Thomas Ho, CEO of Gammon Construction, said, “We are delighted to have been selected by Swire Properties and to be involved with this landmark project in Taikoo Place.
“Gammon’s advanced technological standards and expertise in building construction are key factors in the contract award.”
STAY CONNECTED

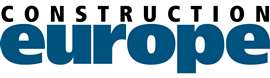
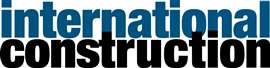
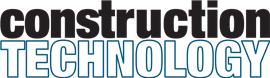
Receive the information you need when you need it through our world-leading magazines, newsletters and daily briefings.
CONNECT WITH THE TEAM
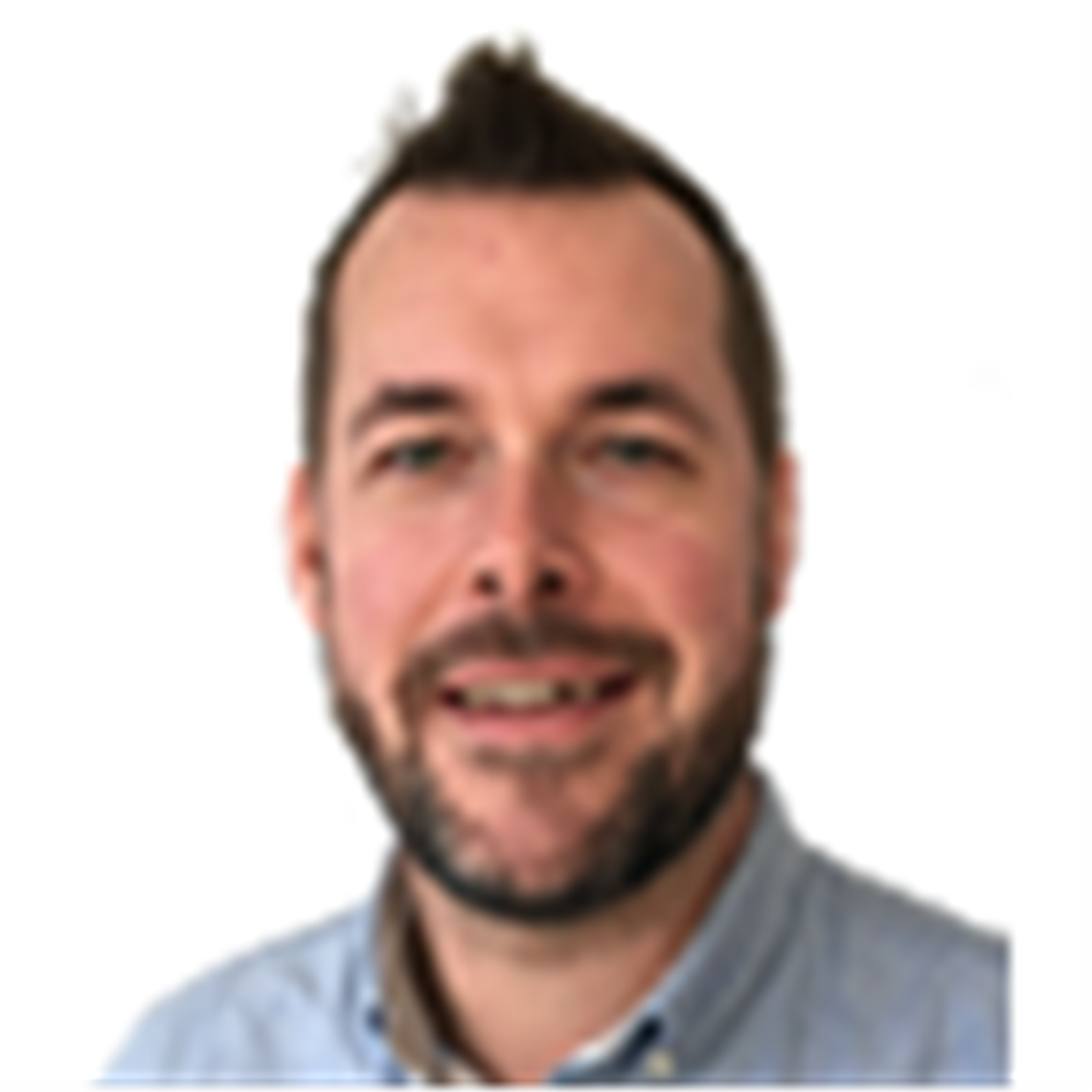
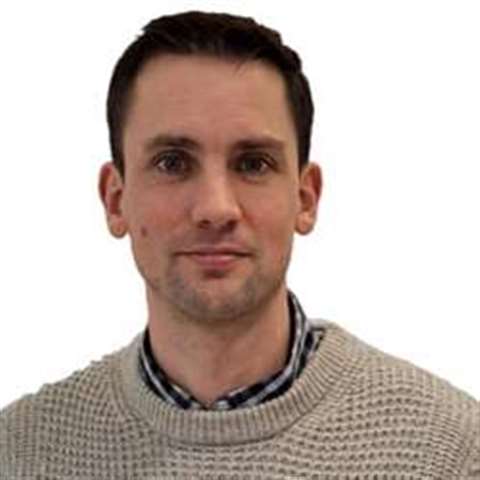
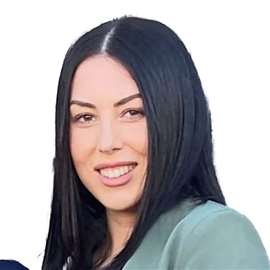
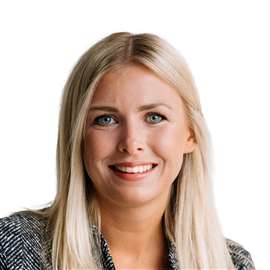