Haulers: Loaded with innovations
12 April 2017
Since its inception by Volvo CE in 1966, the articulated dump truck (ADT) has come to dominate the European market for haulers.
Its popularity is demonstrated by the fact that so much focus has been put on developing innovations for ADTs as opposed to rigid dump trucks (RDTs).
Bell Equipment introduced their new E-series ADT range globally at the end of 2016. The series, which began with the smaller B25E and B30E offering four years ago, has now been completed with the addition of five new models – the B35E, B40E, B45E, B50E and 4x4 crossover B60E.
The company said that these new additions had achieved its main design goal, to improve upon the lowest cost per tonne industry benchmark set by its D-series counterparts.
According to Gary Bell, chief executive of the Bell Equipment Group, “Our products need to perform and what we see with our E-series trucks are world class machines capable of taking on any of the competitors, anywhere in the world.”
Comparative testing carried out by the company between the B40E and B40D has indicated that the E-series model is capable of reducing cost per tonne by up to 10%. Bell said that this was representative of the entire range.
One standard feature that has been on Bell’s ADTs since 2002 is the on-board weighing function. However, after years of development and improvement, Bell is now confident to claim an accuracy of plus or minus 5% irrespective of the loading method and loading tool.
Other regular features enhance safety while operating on inclines. Tip Safe is designed to mitigate any risk of the bin being tipped when in a precarious position, namely if the rear chassis is leaning heavily while the front is level.
The improved Downhill Speed Control automatically varies retardation in order to keep the vehicle at a set speed when travelling downhill. Conversely, when going uphill, the automatic Hill Hold applies the brakes if the operator takes their foot off of the accelerator pedal, so that the vehicle does not roll backwards.
ADt highlight
One particular highlight of Bell’s E-series is the B60E, which was debuted last year.
The 55-tonne crossover truck comes with a new EU Stage IV/Tier 4 Final certified 430kW Mercedes Benz 6-cylinder engine. This, combined with the Allison 7-speed transmission connected via an economical drivetrain, is said to lower fuel consumption and make the B60E available on emissions-regulated markets for the first time.
A complete redesign of the rear chassis has resulted in a suspended 63-tonne rear axle with 24.00 R35 twin tyres. In addition, the dimensions and geometry of the flat-bottomed 35m3 bin are said to mimic those of a rigid hauler, making it compatible with existing loading equipment in mines and quarries.
The design also includes auto grease systems, wet brakes on all wheels to ensure braking in adverse conditions, and FleetM@tic telematics with full production data reporting.
Doosan’s new EU Stage IV/Tier 4 Final compliant DA40-5 is the latest addition to a three-generation fleet of Doosan machines being used in a quarry at North Cave in East Yorkshire, UK.
Purchased by Humberside Aggregates, the DA40-5 ADT will be working alongside four Doosan crawler excavators and seven Doosan wheeled loaders, all of which were supplied by Filtermech Plant Sales in Wakefield – the authorised Doosan dealer for the area.
With an articulation hinge positioned behind the turning ring on the DA40-5 – as on all Doosan ADTs – there is equal weight distribution to the front axle. The free-swinging rear tandem bogie provides equal power distribution and good performance on difficult terrain. In fact, Doosan claims best in class for rough and soft terrain capabilities due to the machine’s forward turning point, specially-designed tandem bogie and sloping rear frame, which avoid the need for electronic aids such as traction control.
Fuel efficiency
Another best in class that the company claims is for fuel consumption. The hauler’s new Scania DC13 368kW diesel engine uses Selective Catalytic Reduction (SCR) and Exhaust Gas Recirculation (EGR). Also, greater energy efficiency is claimed by the ZF EP transmission, which is said transmits power from the engine to the wheels more effectively.
The enhanced rear differential system reduces engine rpm, thereby increasing the machine’s durability, said Doosan.
Compared to the previous MT41 model, the 40-tonne payload of the DA40-5 represents a 15% increase, without the addition of a tailgate.
In Poland, the Dębówko quarry, which has recently been carrying out a large investment programme to upgrade the facility, uses a number of Doosan products, including the DA30-5 ADT.
All the machines run 20 hours per day under a three-shift scheme – with four hours of maintenance at night – extracting sand and gravel from the 200ha mineral estate.
Powering the six-wheel-drive DA30-5 through this gruelling regime is an EU Stage IV compliant 5-cylinder 9.3 litre Scania engine with an output of 266kW. On average, it consumes 16.72 litres of diesel per hour.
The dumping speed is automatically reduced to ensure that all the wheels maintain permanent contact with the ground, allowing this hauler to work on rough and soft surfaces.
Operators are able to see data for the distance travelled, the number of cycles made, the total load transported and fuel consumed, all shown on a clear colour display. This can be done from within the air-conditioned cab, which boasts good visibility and a heated air suspension seat that automatically adjusts to the weight of the operator.
As standard, the DA30-5 is fitted with scales for weighing the load.
Hydrema has announced some improvements to its F-series 922HM, a 20-tonne ADT that was introduced to the North American market for the first time at ConExpo 2017.
The Danish-based hauler manufacturer said the 922HM delivered more power with its Cummins QSB 6.7 litre engine. At 218kW and 1044Nm, it produced 8.5% more power than the previous model and 5.5% more torque. This is achieved at the same time as meeting Tier 4 Final emissions standards by using a Diesel Oxidation Catalyst (DOC) and SCR with Diesel Exhaust Fluid (DEF), without having to use a Diesel Particulate Filter (DPF).
A new exhaust brake has been integrated into the variable turbo, and a variable engine fan provides cooling as needed. These features help to make the 992HM quieter and more fuel efficient, said Hydrema.
Hydrema has given the interior of the cab a revamp to offer greater comfort and ease of operation. A backlit, multifunctional joystick and electronic keypad panels are designed to give easy fingertip control of the hauler. The operator also benefits from simple access to on-board diagnostics and service tools via a new central computer unit and instrument display. All this can be done from within a cabin that should never get too hot thanks to the upgraded heating, ventilation and air conditioning system (HVAC).
Additional features that can now be controlled from the driver’s seat include ZF transmission optimisation; calibration of the front axle suspension settings; monitoring of the differential lock; cruise control; and the Idle Stop function, which stops the engine once it has been idle for a set period – adjustable between 1 and 60 minutes.
These come in addition to pre-existing features, such as the intelligent ZF 6-gear soft-shift transmission for a smooth ride, an electrically powered bonnet that allows for easy ground-level checks, and separate pumps for steering and tipping so that the bin can be tipped while positioning the vehicle.
Caterpillar has also announced an updated cab design and advanced control features on its new Cat 745 ADT.
According to Scott Thomas, application specialist for articulated trucks, “An operator can make a huge impact on profitability just based on his comfort and skill level.”
In recognition of this fact, the engineers at Caterpillar have put a greater focus on the operator, using feedback from around the world to create a more quiet, comfortable and spacious cab.
Virtual Product Development (VPD) and simulation environments were used to develop improved ergonomics before the cab was even built.
Paul Taylor, worldwide new products introduction (NPI) manager for articulated trucks, said, “Our virtual reality technology allowed our engineers in Peterlee, England, to sit on a machine in the cab for the past three years, to make sure we've got all these distances [for the controls] right.”
Inside the cab, they have also cut down solar heating by using infrared glass, created 20% more space when compared to the previous 745C model, and reduced the sound by 7dB, from 79dB to 72bB.
Improved visibility
The new external “spinal” Rollover Protection Structure (ROPS) features bonded rear quarter glass, which eliminates the need for a structural pillar. This improves visibility, as does the repositioning of the mirrors, which were once mounted on the fenders but are now mounted on the cab where they vibrate less. Also, a convex front visibility mirror allows the operator to see directly in front of the machine from a seated position.
A better quality of air inside the cab is maintained with the aid of the door’s shut assist, which creates a tighter seal to block dust infiltration. The air temperature is regulated more efficiently by an HVAC system that now has more vents positioned above and behind the operator. For extra ventilation – and easier external communication – Caterpillar has installed left- and right-hand sliding windows.
As soon as the door is opened, machine displays are initiated and the system begins to warm up. This new wake-up feature is intended to save time by automatically running through diagnostic checks while the driver is getting settled.
The intelligent machine controls include a new combined transmission and hoist lever, which gives efficient single-lever control over the truck’s speed and body hoisting functions. Also, at the flick of a switch, the operator can choose between manual or fully automatic assisted hoist control, which automatically applies the waiting brake, sets transmission in neutral and hoists the body to its maximum angle at high rpm.
Safety is improved by the new Cat Detect with Stability Assist system, which gives the driver visual and auditory warnings when the tractor or trailer unit has reached an angle threshold at which it is at risk of toppling over. Another new safety feature is the emergency stop brake switch located next to the touchscreen display. This can be used in the event that both the main and secondary brake circuits fail.
Directional gear shifting protection brings the machine safely to a stop when transitioning between forward and reverse drive in order to save the powertrain from damage.
Advanced Automatic Traction Control monitors underfoot conditions and proactively applies the differential locks to prevent wheel spin. Also, terrain-based throttle smoothing prevents the truck from surging when, because of uneven ground, the operator cannot keep steady pressure on the accelerator pedal.
With a payload of 41 tonnes and six-wheel drive, this ADT is driven by one of Caterpillar’s 375kW C18 ACERT engines. It is EU Stage IV/Tier 4 Final compliant and comes with a new economy feature that is said to reduce fuel consumption by an average of 5% in applications where the truck is not required to operate at full capacity.
Philippi-Hagenbuch recently designed Autogate Tailgates as a solution that increases a hauler’s payload capacity by as much as 20%, according to the company.
It said that operating without a tailgate often resulted in front loading, so Autogate Tailgates help to ensure a more balanced load distribution. This, in turn, has a number of benefits.
It said spillage over the back and sides was reduced, even on inclines and when making sharp turns. This diminishes the risk of tyre punctures, with less fugitive material on the road. Tyre life is also extended by the fact that the front wheels are no longer put under excessive stress as a result of front loading.
Along with easier and safer manoeuvring, this is said to add up to less maintenance work, including maintenance of the Autogate Tailgate itself. The simple design – without locks, cylinders, grease points or controls – means that there is less potential for malfunction.
As a result of the uncomplicated, three-piece construction of the tailgate, it can be easily adapted to different bed widths.
Versatility
Philippi-Hagenbuch’s tailgate is suitable for a variety of applications, from quarries to mineral mines, and can handle just about any material, whether hard and rocky or liquid. For those rocky materials, though, it has been made using high-strength steel and exclusive steel alloy for the chain, to withstand abuse.
The company has also introduced a line of rear eject bodies that use a single ejector blade to push materials towards the rear of the bin for elimination.
Once again keeping the design straightforward, Philippi-Hagenbuch said it was curtailing the need for maintenance. A single hydraulic cylinder operates both the ejector blade and rear tailgate mechanism, and there is just one grease point that requires greasing once a year. The ejector guides are integrated into the inside of the body, allowing for smooth operation without the need for rollers, which are susceptible to damage. Also, the body is composed of high-strength steel that can withstand years of abrasion.
This solution can apparently be adapted to any make or model of ADT as well as a number of rigid frame haulers. Therefore it can be used in a range of applications, from general construction and roadbuilding to mine reclamation and underground hauling.
In fact, a hauler with an ejector can be used as an auxiliary feeder, acting as an alternative tool for delivering material to crushers and asphalt plants when there are issues with a primary feeder.
Without a need to raise the body, the hauler can dump in the presence of overhead barriers such as power lines, rooflines and bridges. Dumping on downhill slopes or in conditions with soft footing also becomes possible due to the lower centre of gravity.
The system supposedly allows more dumps to be made in less time. This enhanced productivity is supplemented by the greater capacity and ease of loading that come as a result of having no external rails or guides.
Volvo Construction Equipment (CE) has revealed the latest phase of its electric load carrier concept.
In a bid to transform the quarry and aggregates industry by eliminating up to 95% of carbon emissions at the same time as cutting the cost of ownership by up to 25%, Volvo CE has been working on an electric site research project. As part of this, the HX2 autonomous, battery-electric load carrier is a second-generation concept machine.
Uwe Müller, Volvo CE’s chief project manager for the electric site project, said that shared technologies and components from the Volvo Group were incorporated into the HX2, including electric motors, batteries and power electronics. A new drivetrain was required in order to take full advantage of “ground breaking” electromobility developments, and a new vision system enables the machine to detect obstacles, such as humans, in its vicinity.
Volvo CE’s vision is for a fleet of HX2s to be loaded by electric hybrid wheeled loaders with material from grid-connected excavators and then transport it to a secondary crushing site. This requires new machine and fleet control systems and logistic solutions for electric machines.
In the words of Jenny Elfsberg, director of emerging technologies at Volvo CE, “The electrification of construction equipment will produce cleaner, quieter and more efficient machines – this represents the future of our industry.”
STAY CONNECTED

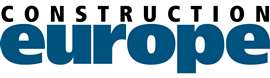
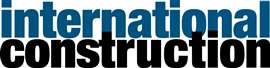
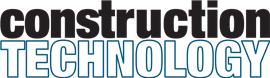
Receive the information you need when you need it through our world-leading magazines, newsletters and daily briefings.
CONNECT WITH THE TEAM
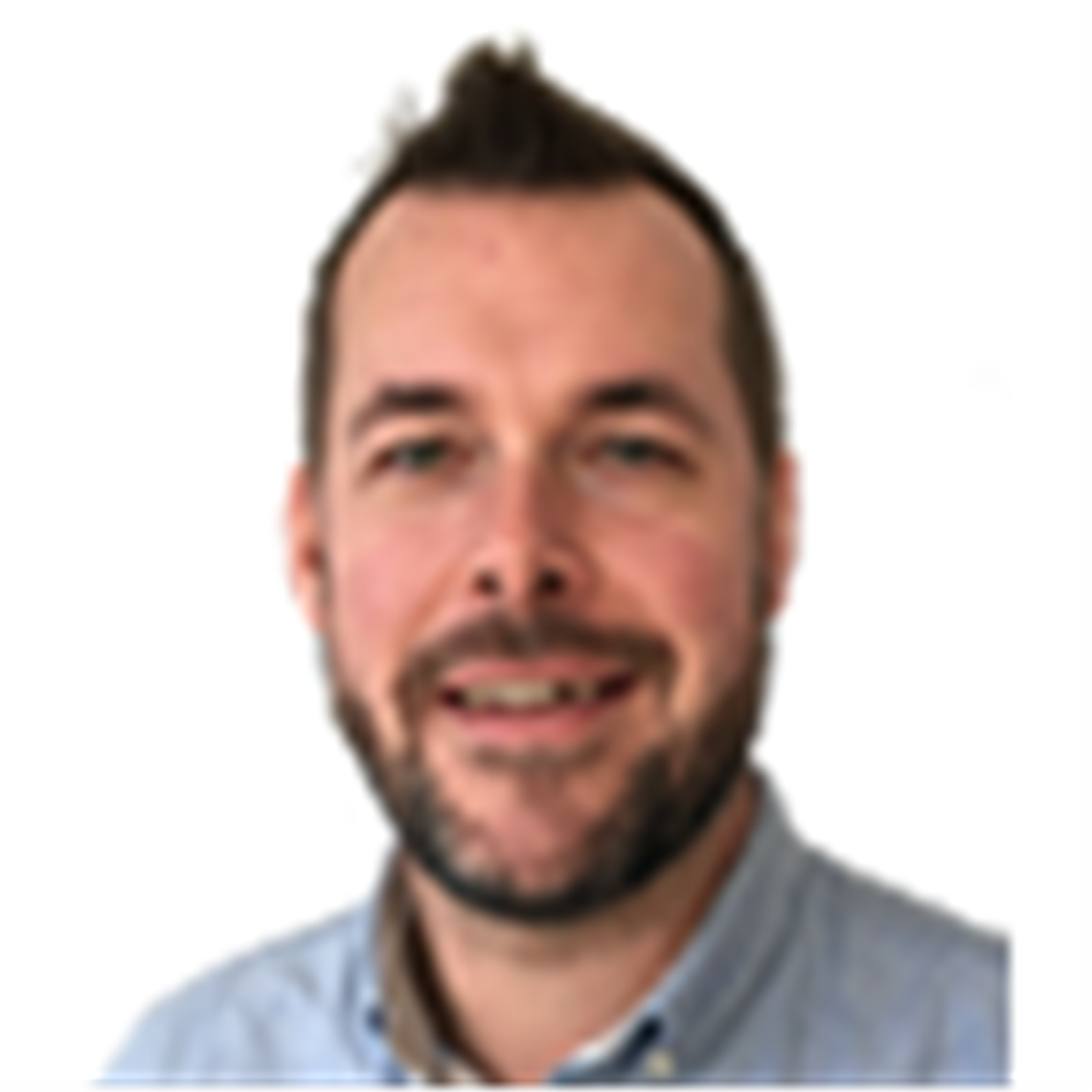
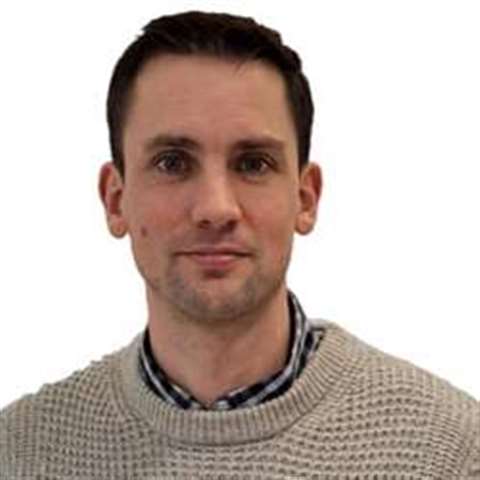
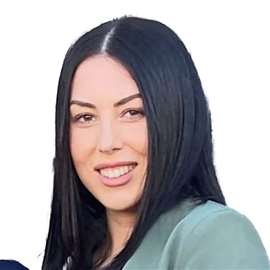
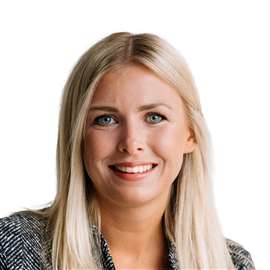