Environmental strides are being made in road building. Steve Skinner reports
02 June 2009
The road building sector is looking at ecological processes and more recycling in order to reduce environmental impact. Steve Skinner reports on the green shoots of change.
The level and flatness of a road surface combined with specified friction properties and load bearing attributes are the fundamentals behind road construction. According to Richard Owen, vice president of road machinery Europe at Volvo, "The ability to meet these specifications in a road is paramount.
"The thing with paving is it has to be absolutely right every millimetre of the way. You cannot have trial runs on a job site, so you have to get it right first time, every time," he said. "As you build through the layers towards the surface of a road the materials become more expensive and so the requirement to do a perfect job becomes vital for a contractor."
It's against these criteria that any environmental advances must fit. Andreas Biedermann of the research and development department at Ammann told iC, "The annual amount of material used for road construction is immense. As such, the industry has a responsibility to preserve our environment.
"At Ammann, we carry out our product development activities concentrating on more ecological processes, safer systems and reduced use of resources."
One of the more recent and significant environmental advances made by the industry has been the advent of warm mix asphalt (WMA), which has the ability to lower the carbon footprint of road construction and reduce the emission of fumes on construction sites. Production of WMA inherently requires less heating than traditional hot mix asphalt, which as well as reducing energy consumption also offers cost savings.
When hot's cool
"Warm mix asphalt is going to revolutionise road building," said John Irvine, vice president of sales and marketing at Roadtec in the US.
"To reduce Nitrous oxide (NOx) and Sulphur oxide (SOx) emissions it's critical to keep asphalt liquid below 1400C. WMA achieves this."
As well as environmental benefits, WMA also offers paving advantages over hot mix asphalt.
"A new stiffness test developed by the National Centre for Asphalt Technology at Auburn University found that WMA is much more fluid and it's easier and quicker to achieve the required densities than hot mix," said Mr Irvine. "The only issue is the working window as it's much narrower."
Below 1000C WMA becomes stiff very quickly. With the mix delivered at a maximum of 1320C as opposed to 1500C with hot mix, it's crucial to keep the temperature as near to the 1320 as possible to prolong its working life.
One area that could extend the working window is remixing on site. "I think remixing with material transfer equipment will become increasingly important," said Mr Irvine.
WMA has taken a foothold in the US, while integration, particularly in Europe, is somewhat slower. "Road building materials have to be tested and approved by the authorities before contractors can use them," said Volvo's Mr Owen.
"I think in Europe, the rate at which the industry gets governments and authorities to specify WMA will determine the speed of its growth. Authorities specify the exact design of the material to be used for different applications so we have to pave to their specifications," Mr Owen told iC.
Ammann's Mr Beidermann believes there are uncertainties relating to WMA that need to be addressed before it receives widespread acceptance in Europe. "There are some questions about the recyclability of WMA," Mr Beidermann told iC. "I believe these doubts need to be put to rest in order for WMA to be more broadly used."
Energy
Regarding production, the Fayat Group recently unveiled its RF400 Retroflux asphalt plant capable of producing 400 tonnes/hour of recycled materials, WMA and half-warm mix asphalts.
The RF400 can be erected on any stable ground and therefore doesn't require bespoke foundations. The unit also features an additional burner mounted on the inlet of the filter to prevent unwanted condensation. The company attributes this additional burner to a significant reduction in energy requirements over more traditional designs.
The company also launched its ‘Beluga' mobile mini-production plant for the manufacture of either WMA or a hot-mix asphalt based on an innovative new vegetable based binder developed by road building contractor Colas and made from Beta vulgaris (more commonly known at beetroot).
Capable of producing asphalt on site at 1200 C, the Beluga has a throughput of seven tonnes/hour and as a result of the cooler process the company estimates there will be a -30% reduction in energy requirements and CO2 emissions.
Making the cut
Wirtgen launched its 265 kW W150 cold milling machine with Widrive control last year and has since sold 70 units, far exceeding initial expectations.
"This is a new class of machine," said Bernd Holl, product manager for cold milling machines. "And it's very light at just 22.5 tonnes including water and fuel, which is a big advantage. Despite the current global issues we currently have a three month delivery time, so this shows the popularity of this new generation machine."
Widrive ‘networks' all the main functions of the machine such as the engine and milling drum drive to improve performance and reduce fuel consumption. The system also automatically activates the water flow when milling.
The operator platform features a seat that can be moved in all directions to enhance visibility of the milling edge. "The W150 is a tool for the operator to achieve the quality that he needs to," said Mr Holl. "We know the operator is the most important part of any milling process, so it's important that we give him the most practical and comfortable tool to do his job."
Wirtgen estimates that operator input is reduced by -50% through the use of Widrive, so that operators can concentrate more on milling and less on machine control.
At Intermat Bomag launched its BM2000/60 milling machine, the first model in the 447 kW class with a working width of 2 m. A fully automatic hydraulic folding conveyor belt and folding roof means the BM2000/60 is easy to move between sites without the need for specialist transport.
The machine also features a wide roof that can be moved sideways together with the windscreen to provide cover, even when watching the milled edge.
A 3500 litre water tank, up +10% on its predecessor, mounted at the rear improves ballast, which in turn means the rear tracks suffer less slippage. There are also new hydraulic side plates on the milling box to disperse material before it accumulates, thus eliminating any ‘float' effect.
Alongside the BM2000/60, Bomag also unveiled three models in the 224 kW Class of cold planers. With working widths of 1 m, 1.2 m and 1.3 m, the series has been designed with speed and manoeuvrability at its heart.
Earlier this year Volvo launched its MT2000 milling machine for the US market. With a maximum cutting width of 2.18 m and 356 mm cutting depth, the MT2000 is ideally suited to milling large car parks, city streets and highways.
Powered by a 455 kW Cummins engine, the machine features a 914 mm conveyor system to quickly move material out of the drum box.
Sonic sensors fitted at the front and rear of the tracks identify objects of greater than 102 mm in size and stop the machine to prevent damage to the drum or cutting tools.
"The control system is more advanced than anything we've seen before on a milling machine," Mr Owen told iC. Although only currently available in the US, he confirmed, "Volvo will be launching this machine in Europe in 2010."
A vibration damping deck mat manufactured from closed-cell foam increases operator comfort, while a ‘walk-in' service compartment to the rear of the machine lends itself to safe and easy maintenance.
In the utility class, Volvo also launched its MW500 milling machine this year offering the highest travel and working speed in its class.
Meanwhile, Dynapac's new 92 kW PL500T and 97 kW PL500TD compact cold planers feature 500 mm cutting widths and are available in three and four wheel configurations. With maximum cutting depths of 160 mm and 200 mm respectively both models are powered by a Stage IIIA compliant Cummins QSB4.5 engine.
Roadtec launched its RX-400 1.2 m cold planer with a rear mounted drum last year. The RX-400 features milling widths of between 660 mm and 1.2 m and a maximum cutting depth of 320mm. Maximum operating speed is 52 m/min. A conveyer swing of 600 to either side increases the flexibility of material discharge.
Smooth operators
When it comes to compaction, Hamm this year debuted its new concept HD+ articulated 120 and 140 tandem rollers from its heavy duty range as well as a new HD14TT rubber-wheeled roller from its compact line.
The HD+ 120 has an operating weight of 12.9 tonnes, while the HD+ 140 increases that to 13.8 tonnes. Both are fitted with a vibration and oscillation roller and there's also a high-frequency version for the US market.
The ergonomic operator's seat can be moved across the machine to view the drums and water sprinkling system. A new articulated joint ensures improved driving stability and improved quality when compacting on bends while the ‘offset' during crab steering has been almost doubled over that found in earlier HD models.
At Intermat Hamm also launched its new 7 tonne DV65 all-wheel drive roller, which is an addition to the DV range and is available with a vibration roller, oscillation roller or combination.
Bomag has also released its BW216D-40/PD-40 for outside Europe. The BW216D-40/PD-40 has an operating weight of 15.7 tonnes and is powered by a 114 kW stage II Deutz engine.
JCB Vibromax has replaced its VMT850 with the VMT860 tandem roller. With a drum width of 1.68 m, the VMT860 weighs 8.7 tonnes and can operate with high amplitude on low frequency for large asphalt or standard soil applications. A 240 litre fuel tank and 1070 litre water tank extend the operating window.
As well as launching its 8 tonne AV80X4 split drum articulated tandem roller earlier this year, Ammann is also now fitting its ACE compaction expert system to all its single drum and tandem rollers as well as its heavy plate compactors and Rammax trench rollers.
"ACE provides a real-time indication of the achieved compaction," said Mr Biedermann. "In combination with GPS, our ACEplus system can gain savings of up to +55% in time and resources, by avoiding overcompaction."
Sakai unveiled its new 10.6 tonne SW770HF vibratory tandem roller earlier this year featuring three stage vibration frequency and a 1.7 m roller. The machine represents the company's entry into the larger roller market in the US.
"In developing the SW770HF we wanted to produce a low profile roller with a high profile appearance," said Shane Sirmons, marketing manager. "The new model features a totally new frame that we intend to use in the future for a new range of combination rollers."
Dynapac launched four new tandem and split drum rollers in April. At 7.7 tonnes, the CC224HF features 1.5 m drum widths while the split drum version, the CC234HF, weighs 8.1 tonnes, again with 1.5 m drum widths. At 8.1 tonnes and 8.6 tonnes respectively the tandem CC324HF and split drum CC334HF both feature drum widths of 1.7 m.
All the new models are powered by a 60 kW Cummins QSB 3.3 engine with an option to upgrade this to a 74 kW version.
Caterpillar debuted its 11.9 tonne CB54XW vibratory drum roller with a compaction width of 2 m for the US market in March. The model features a new frame design, which enables the operator to easily see the 18 nozzle spray bars mounted over each drum.
In Europe, the company launched its 74 kW CD54 drum steer vibratory roller last month. The 9.5 tonne machine has a maximum working width of 3 m and features a drum width of 1.7 m with a maximum offset of 1.3 m.
Surface
Bomag replaced its BF331 finisher this year with a new BF300 range of seven to eight tonne pavers. The new BF300 range is available in tracked or wheeled versions with 2-wheel, 4 wheel and 6-wheel variants and either gas or electric powered screeds.
The range offers built-in widths of 1,7 m to 3,4 m and is also extendable by up to 400 mm with two side plates. The hopper has a capacity of 4,8m3 while Ecomode machine management in conjunction with a low-consumption Kubota engine provide excellent fuel economy.
Time machine
While the physical attributes of materials will continue to reduce the environmental impact of road building, it will be further advances in electronics that will make the difference in the future.
"I believe in the future we will see greater recording for quality control and performance measurement," said Mr Owen. "This will make the whole process even more efficient and eventually eliminate any excesses in road building."
Mr Holl agrees that electronics are the future but also believes that recycling will have an increasingly important role. "Recycling of asphalt can have a major environmental impact and at Wirtgen we are committed to pursuing this avenue to reduce emissions and the demand on natural resources."STAY CONNECTED

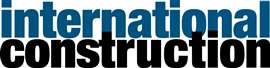
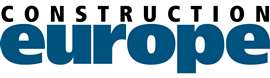
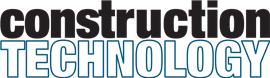
Receive the information you need when you need it through our world-leading magazines, newsletters and daily briefings.
CONNECT WITH THE TEAM
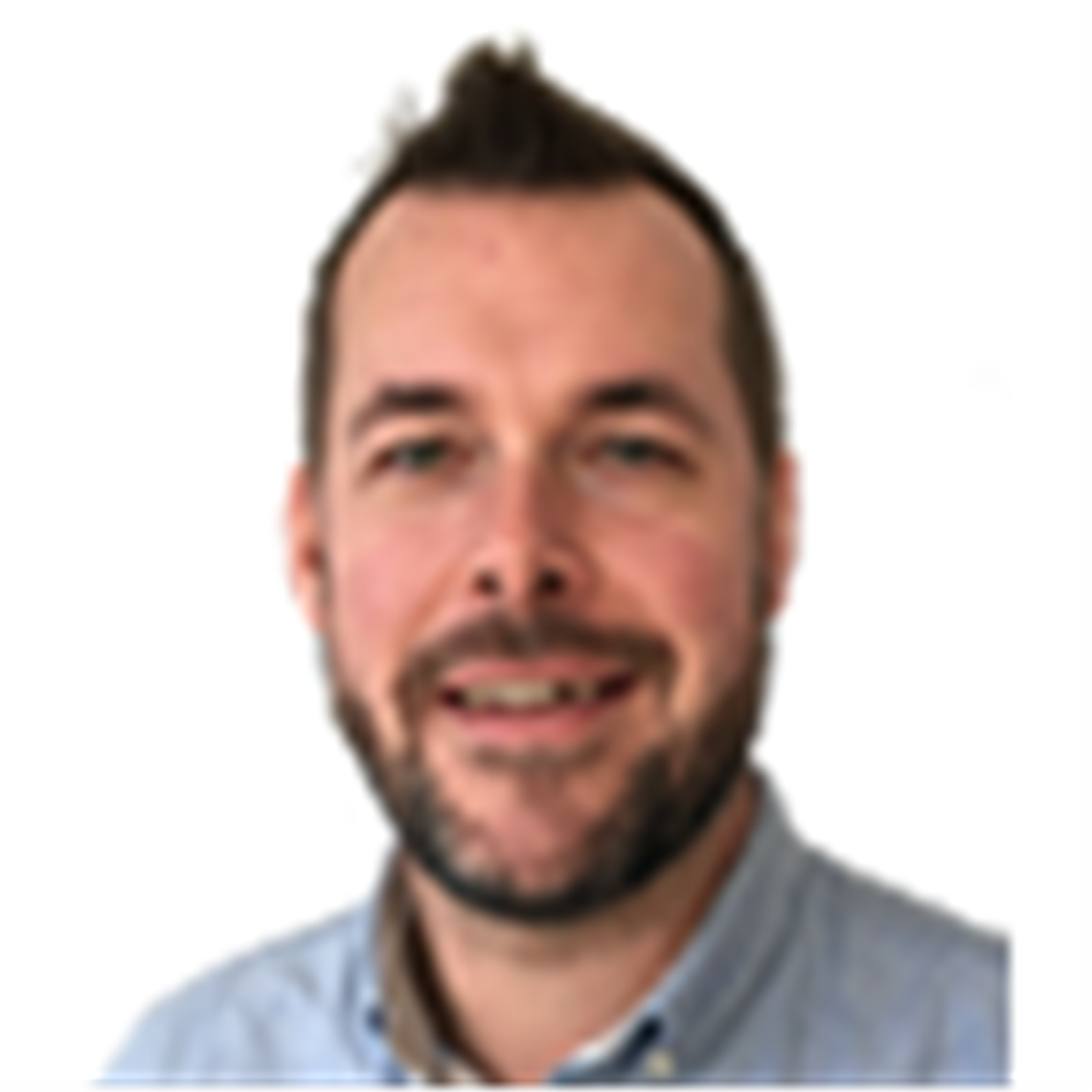
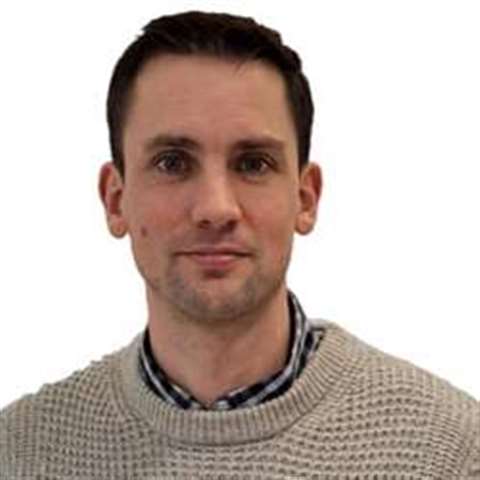
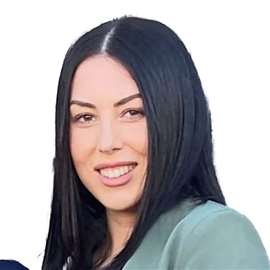
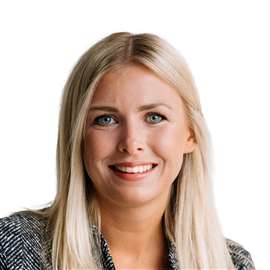