Doka forwork solution helps save on costs at Orix Tower
18 February 2010
The 133 m-high Orix Tower in Osaka, Japan is rising on an extremely cramped downtown site in the heart of the bustling megacity and. Doka was chosen as the just-in-time supplier of the self-climbing formwork solution for the three-cell structure core. Richard High reports.
Contractor Takenaka Corporation has only 10 months to finish the structure shell for this 31-storey high-rise. This is the first time in Japan that a cast-in-place (CIP) concrete core has been combined with a steel construction.
In Japan, CIP concreting is generally performed with traditional formwork. For the CIP concrete core of the Orix Tower, however, Takenaka opted for Doka's formwork system as forming operations can be carried out by only a third of the workforce needed for traditional formwork, leading to dramatic savings in labour costs, according to Doka.
Smooth climbing
For the walls of the CIP concrete cores, 26 SKE50-plus automatic climbers are in action on the outside, and 28 on the inside. The advantage with this is that groups of 20 cylinders can be served from just one hydraulic unit. This means the entire 720 m² of formwork takes less than four hours to move to the next storey.
Another advantage, according to Doka, is the synchronised motion of all the cylinders ensures smooth, jerk-free climbing operation. At the Orix Tower the individual platforms are all linked together, for safety reasons, and are only opened at two points for the climbing operation. Thanks to this synchronisation only a few millimetres' level-difference occurs between the platforms while the 30 m long platform gang is being climbed.
Safety at all levels
Japan's strict safety regulations mean the formwork solution is completely enclosed on the outside with trapezoidal metal sheeting, from the working platform upwards. An intermediate platform, which can be tilted inward to facilitate formwork removal, provides safe access to the waling level of the 4.10 m high timber-beam formwork elements.
The follow-up platforms are also completely enclosed, in this case with scaffolding tubes and safety netting. The large area top platform level is used for setting down reinforcing steel and for installing the site infrastructure.
Takenaka's deputy project superintendent, Katsuyuki Hirao, has been particularly impressed by the technically support given by Doka during forming.
"We're really pleased with the SKE50-plus. Using traditional timber formwork, we would have to set up and remove this separately in every single storey, and vertically stack the working platforms. We could never achieve a weekly cycle working like that. Quite apart from the time savings, now we only need around a third as much labour."
STAY CONNECTED

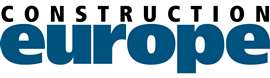
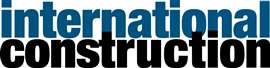
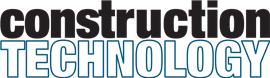
Receive the information you need when you need it through our world-leading magazines, newsletters and daily briefings.
CONNECT WITH THE TEAM
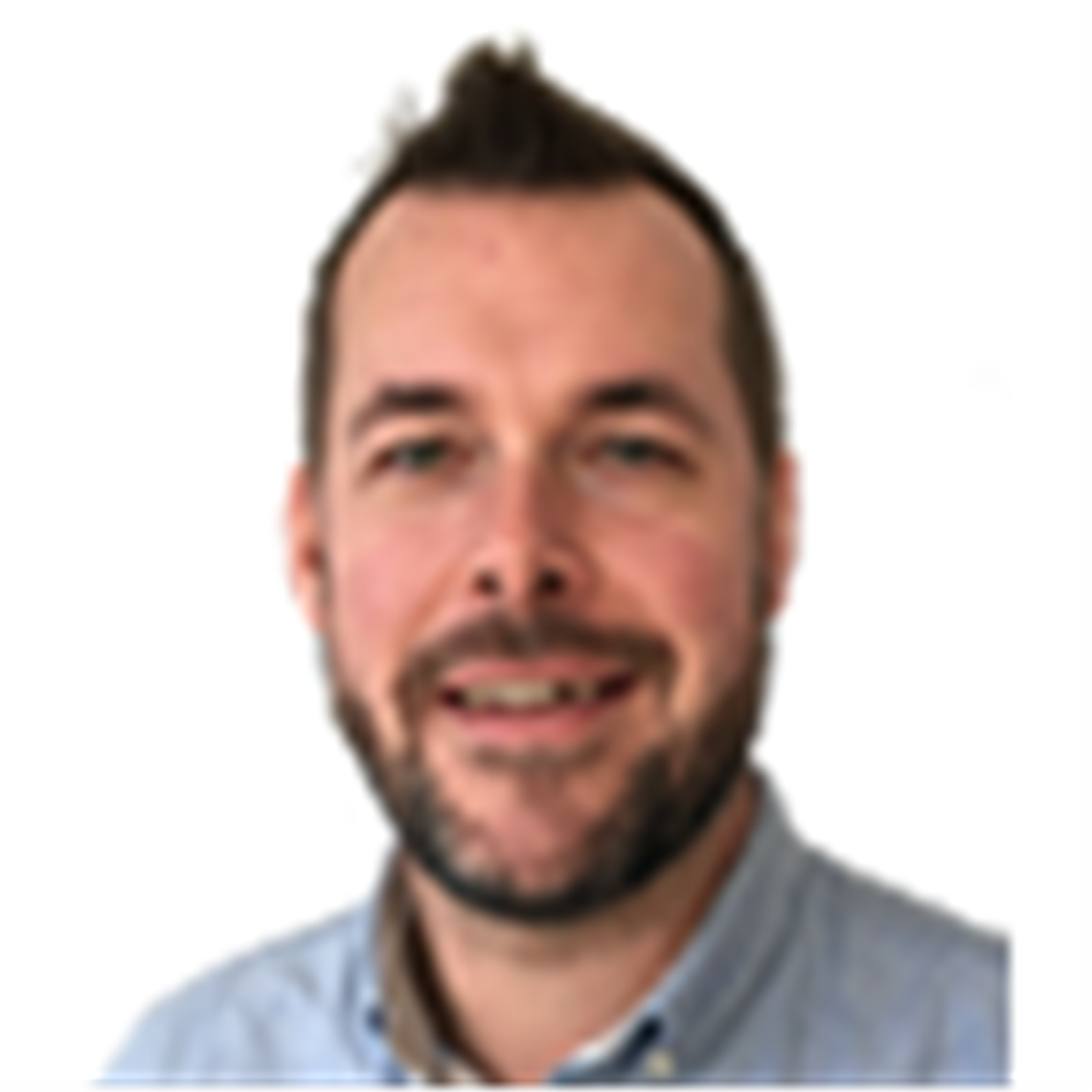
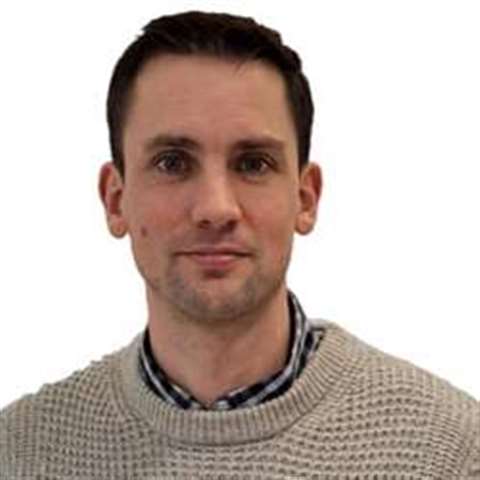
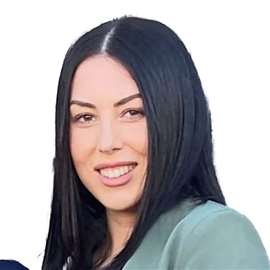
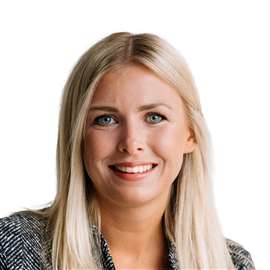