Digital twins enter construction mainstream
10 August 2021
The Covid pandemic and advances in computing are pushing the use of ‘digital twins’ into the construction mainstream. But experts say we are only beginning to see the implications for the technology. Lucy Barnard reports.
Surrounded by grey water as far as the eye can see, the Clair Ridge oil platform off the coast of Shetland is a pretty remote spot in which to be carrying out routine maintenance.
But the technicians in blue overalls and hard hats abseiling down the side of the vast structure in Scottish territorial waters in the North Sea are connected to thousands of up-to-date maintenance reports and work instructions using digital twin technology as well as to dozens of other team members back on the mainland.
Using an ipad, workers on the remote platform can access a digital replica of the entire off-shore platform to check maintenance records and engineering data for each of the components they inspect.
At the touch of a screen they can access data from sensors throughout the platform which monitor everything from flow rates to temperature to wind speed. And any work or unusual findings can quickly be logged onto the digital twin.
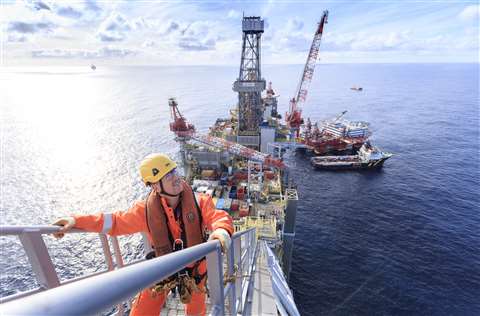
“The implications for digital twin technology are huge,” says Lee Tedstone, global VP, head of digital project execution at software developer Aveva, which worked with a team led by BP on the project. “We can use augmented reality where people use technology to see part of the digital twin. That means the guy conducting maintenance on the oil platform can look at each component and see its operational performance, scheduled maintenance etc.”
Faced with a sudden need to maintain social distancing and enable more staff to work from home during the pandemic, more and more big oil, energy, construction and engineering companies have been speeding up their plans to create digital twins.
“We had quite a few customers coming to us in March/April 2020 with requests to help them keep the workforce connected through our online software offering for unified project delivery,” says Tedstone.
“People had to work remotely, but company infrastructures were generally not geared to manage heavy remote working, in particular with their 3D design solutions. We saw a huge uptake in our offering during that time which in turn accelerated a lot of digitalisation initiatives forward. By having the software in the cloud it was easier to access therefore driving productivity.”
But this is just the beginning. As advances in technology enable companies to harness the Internet of Things to constantly measure the things that they are building and operating, digital twins provide a good way to keep track of that real-time data and use it in a meaningful way.
How big is the digital twin market?
A survey by market research company Markets and Markets predicted that the global digital twin market is set to increase to US$48.2 billion by 2026 – more than 15 times its size in 2020. Construction companies are expected to be among the biggest drivers.
“Digital twin technology is one of the fastest growing concepts in the construction industry,” says Frank Weiss, senior director for new products at Oracle Construction and Engineering, an arm of computer giant Oracle which specialises in developing software solutions for construction firms. “Digital twins can play a profound role in how owners manage built assets, and how consumers interact with these structures.”
Weiss says that, digital twins can make the construction process quicker and faster and help teams work together better using more up-to-date information, especially if teams are working on a project from different physical locations.
“Today’s organisations want to consolidate as much as possible into a single, cloud-based platform, and eliminate on-premise silos of duplicate information,” Weiss says. “A digital twin helps ensure that team members will be working off the latest data analytics for a project, including those for repeatable processes that are being built offsite. It can help act as the cornerstone for prefabrication and can play a prominent role in achieving efficient communication and construction business processes.”
And, he says, the information from the digital twin can then be used in computer simulations to predict how a project will perform over time - providing information which can then be used by the designers and engineers to optimise their designs before work has even started.
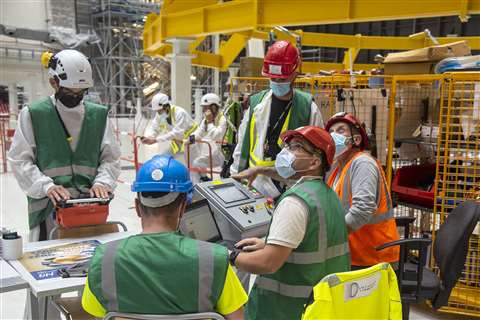
“A 4D simulation [over time] provides the context and chronology to create simulation scenarios in the digital twin,” he says. “It helps the design and engineering phase of a construction project by expediting and automating traditional design, production, and operational processes. It will identify opportunities to improve the construction of an asset as the project is evolving.”
Rich Humphrey, vice president of construction product management at another software firm, Bentley Systems, agrees. He points out that unlike Building Information Modelling software which has been used to varying degrees in construction for the past twenty years, digital twins provide real-time information about projects, making them invaluable on construction sites where designs can be altered based on the conditions in the field.
“A digital twin is a realistic digital and dynamic representation of a physical asset, process, or system in its built environment,” he says. “The keyword is dynamic and that is what distinguishes a digital twin from any other static model. It’s living. It’s changing along with the physical asset.”
Humphrey says his teams start work on digital twins before construction has even started, capturing existing conditions on site such as survey results and encapsulating design models and engineering data from the design phase. Then, on-site sensors can monitor construction conditions in real time.
“Digital twins can significantly benefit the construction industry, helping users make data-driven decisions and achieve more predictable outcomes,” he says. “They quickly allow users to perform construction sequences and simulations, so that they can detect and resolve errors before construction begins which reduces time for project teams and, therefore, costs for the owner.”
By buying materials early and plugging the data from it into a digital twin, software firms say contractors can start engineering components such as piping 3-4 months earlier than would otherwise be possible, reducing overruns and bringing construction projects closer to budget.
How are digital twins used in construction?
And, once a digital twin is built, the sky is pretty much the limit in terms of the sort of simulations you can perform. Engineers can assess how a structure would be likely to behave when faced with freak high winds or earthquakes.
They can run a test to see how a structure will perform over twenty or fifty years. They can look at what would happen if they changed a key part of the structure or designed it with cheaper materials.
Digital twins for construction design and engineering
Florent Thebault, areas sales director for Southern Europe at simulation software specialist Ansys, works with companies looking to understand how to design and engineer their products more efficiently.
Computer simulations of digital twins can give clients information about just how long each component can keep working efficiently, he says. Replacing a pipe too late could cause a costly and dangerous leek - but replacing them too early is a waste of money, time and global resources.
“You can optimize the efficiency and profitability of the company,” he says. “So, simulation can ensure that a cable is not too small so it might break and you can also ensure it is not too big. So I can use a smaller or cheaper cable perhaps and save money or I can be faster to produce it. You can play with several parameters to optimize your design.”
And, as part of a team helping to build the vast International Thermonuclear Experimental Reactor (ITER) experiment in the South of France which is hoping to produce nuclear fusion, Thebault is at the cutting edge of seeing where simulation technology could lead.
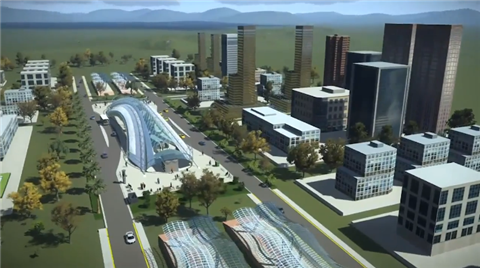
“The main value of simulation lies in being able to physically represent all the phenomena on the computer,” Thebault adds. “It opens all the doors to testing in very difficult environments like space or deep seas. All of this kind of stuff can now be possible on the computer.”
At ITER, where teams of scientists are building the world’s largest nuclear fusion reactor by heating plasma into extreme temperatures and confining it within a super-strong electromagnetic cage or tokamak, Thebault says the technology really comes into its own.
Practical use of a digital twin
“For the ITER tokomak this is where simulation is making sense,” he says. “We don’t have any real prototype of the ITER tokomak but we can take the data of the materials and virtually test it in that environment. That it means that you are sometimes going to discover more in the research mode of what might be the results that you can expect in that situation that we have never faced.”
As a result, Thebault says, Ansys has been able to help design and engineer key components of the experiment including the vacuum chamber, the cooling system and the microwave antenna which heat gas up to 150m degrees to turn it into plasma.
Aveva’s Tedstone too believes that the full potential of digital twins is only starting to become apparent. Once companies get used to the concept, he believes it could revolutionise the way in which companies look at their environmental impact.
His aim is to include data on the amount of carbon produced by each component on a project in its digital twin in the same way that cost is currently treated, enabling engineers to model a structure’s environmental impact over time and to procure and construct in the most sustainable manner.
How will digital twins develop in construction?
“When our customers are buying materials, we could include information from a government online catalogue of materials providing them with an associated carbon score,” he says. “We could then give our customers the option of buying materials from place A or place B but place A has a much better sustainability initiative. You start making those types of decisions.”
But, despite the optimism, many in the construction industry remain to be convinced. Sceptics point to the fact that many large companies in the sector are struggling to implement digital twins because they have legacy systems which are incompatible with the technology, or do not currently employ staff with the skills and training to be able to use the technology at scale.
“The use of digital twin is still in the early stages in the construction industry,” admits Bentley’s Humphreys. “Building Information Models [BIMs] aren’t even that widespread.”
“But the good news for those that have BIM, the gap isn’t that big to take them to a digital twin and we don’t suspect it will take long,” he adds. “However, for those users in construction who haven’t even embraced model technology as part of their contract, may take a little longer to transition to a fully digital world.”
What is a digital twin?A digital twin is a complex digital representation of a physical thing with a real-time connection. It is an assembled aggregation of data captured by other tools, usually including a 3D model. A digital twin in the construction industry spans the lifecycle of a project, from the beginning (planning and building), to the middle (operating and improving), to the end (decommissioning and disassembling the asset in a sustainable and cost-effective manner). For the construction industry, digital twins can play a profound role in how owners manage built assets, and how consumers interact with these structures. |
STAY CONNECTED

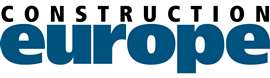
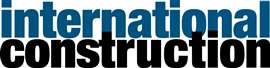
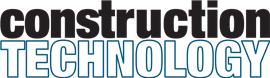
Receive the information you need when you need it through our world-leading magazines, newsletters and daily briefings.
CONNECT WITH THE TEAM
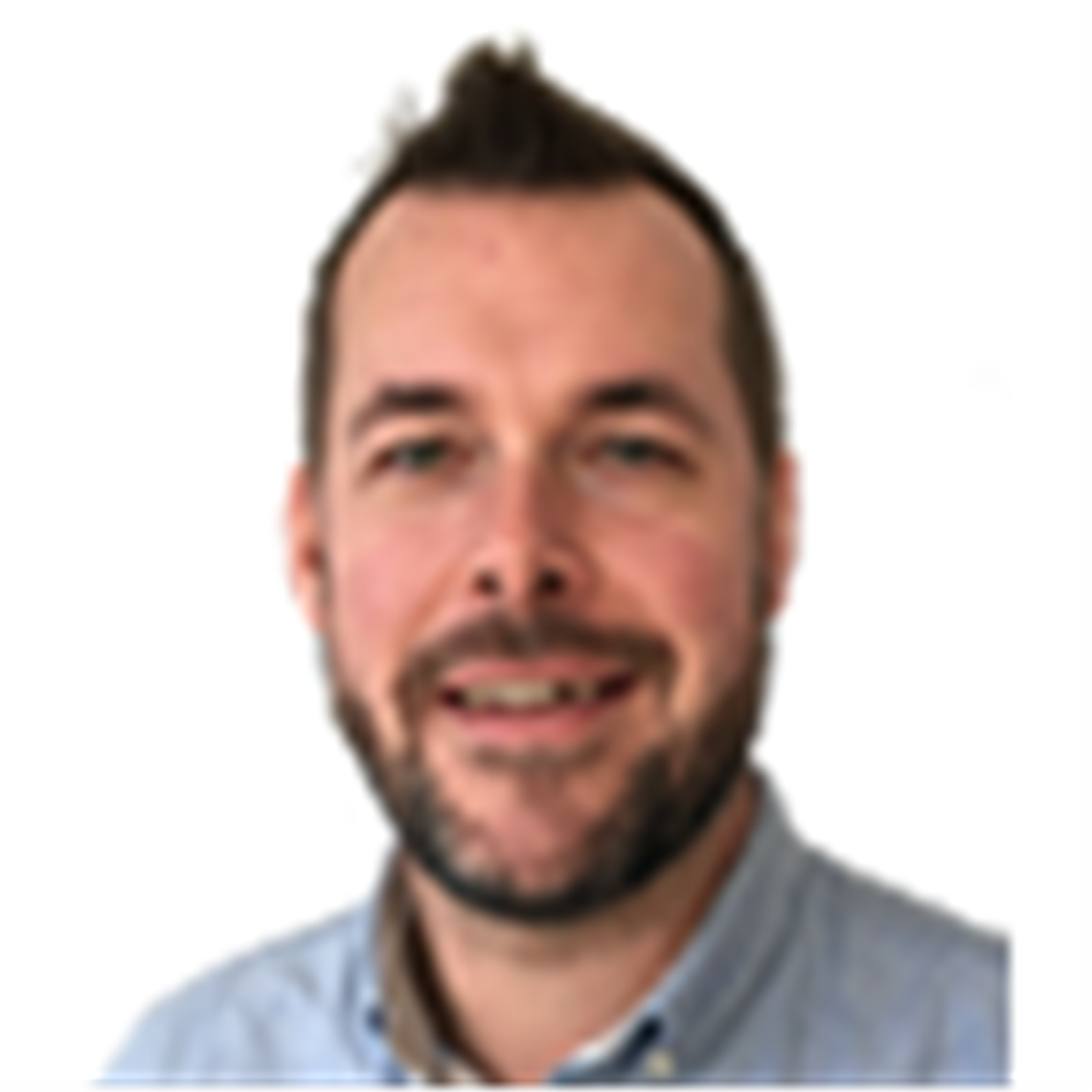
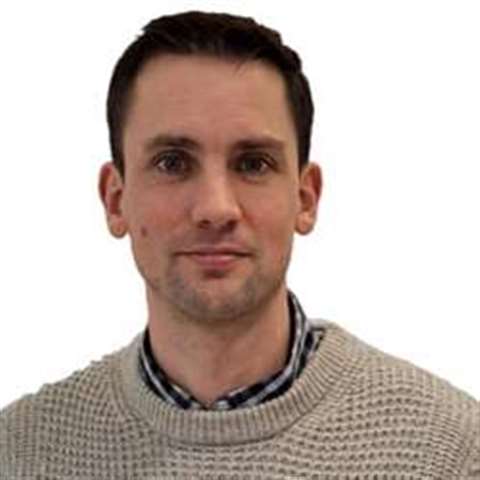
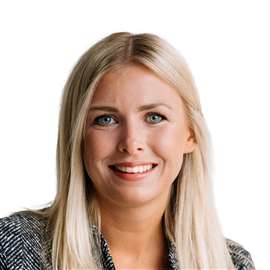