Concrete without cement developed
02 November 2018
The production of concrete without cement is being developed by scientists at Kaunas University of Technology (KTU) in Lithuania, where they are claiming to be using industrial waste such as fly ash.
The university said that the final product was as strong as traditional concrete, was more resilient to damaging effects of acid, and more stable in cases of exposure to extreme heat and cold.
Scientists at Kaunas University have said that to produce 1 tonne of Portland cement – a basic ingredient of concrete and the most commonly used type of cement around the world – up to 1 tonne of CO2 was released. They said it was estimated that the global cement industry was responsible for 7% of yearly CO2 emissions into the atmosphere.
With a view to reducing the concrete industry’s negative impact on the environment, KTU researchers have been investigating methods of substituting Portland cement with other materials.
Vytautas Bocullo, researcher at KTU Faculty of Civil Engineering and Architecture, said, “At first, the idea that concrete can be produced without using cement seemed radical. Now, after several years of intensive work we succeeded to develop alkali-activated concrete, which has compressive strength of 55MPa – the same as in usual concrete.
“Instead of Portland cement, we are using alkali-activated industrial waste products – fly ash, biofuel bottom ash, AlF3 production waste – silicagel, etc.”
Bocullo added that the biggest advantage of this type of binder was that a large amount of industrial waste, containing the active form of silicon and aluminium compounds could be used in its production. He said that theoretically, any material containing silicon and aluminium compounds could be used, such as blast furnace slag or metakaolin, material derived from modification of clay mineral kaolitine.
He said that treated with a special alkaline solution, these materials started melting and binding in a similar way to traditional cement. Depending on the composition, the final product can be either geopolymer or alkali-activated material. Alkali-activated concrete is said to be much more resilient to the effects of fire and acid. Also, as it has a higher pH, this concrete is said to protect against corrosion.
Local materials
Bocullo said that alkali-activated concrete could be used instead of traditional concrete in many fields, and was becoming a globally popular alternative to traditional concrete. To produce this type of concrete cost-efficiently, he recommended the use of local materials.
“We are trying to use waste materials from local industry, such as aluminium fluoride production waste – silica gel and biofuel ash,” he said. “The preparation of the substance depends on the material itself. For example, fly ash of coal can be used instantly, but the biofuel ash needs to be ground up to the fineness of the cement.
“In order to improve the qualities of the final product, several substances can be mixed, but before that their chemical composition and additives need to be investigated for their impact on the environment and on the compressive strength of the concrete.”
The research groups working in the KTU Faculty of Civil Engineering & Architecture are also experimenting and developing other types of concrete mixtures, such as ultra-high performance concrete – which is being used for safe production – self-renewing concrete and others.
STAY CONNECTED

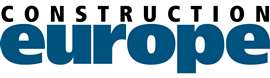
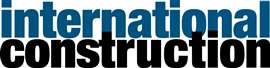
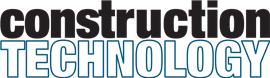
Receive the information you need when you need it through our world-leading magazines, newsletters and daily briefings.
CONNECT WITH THE TEAM
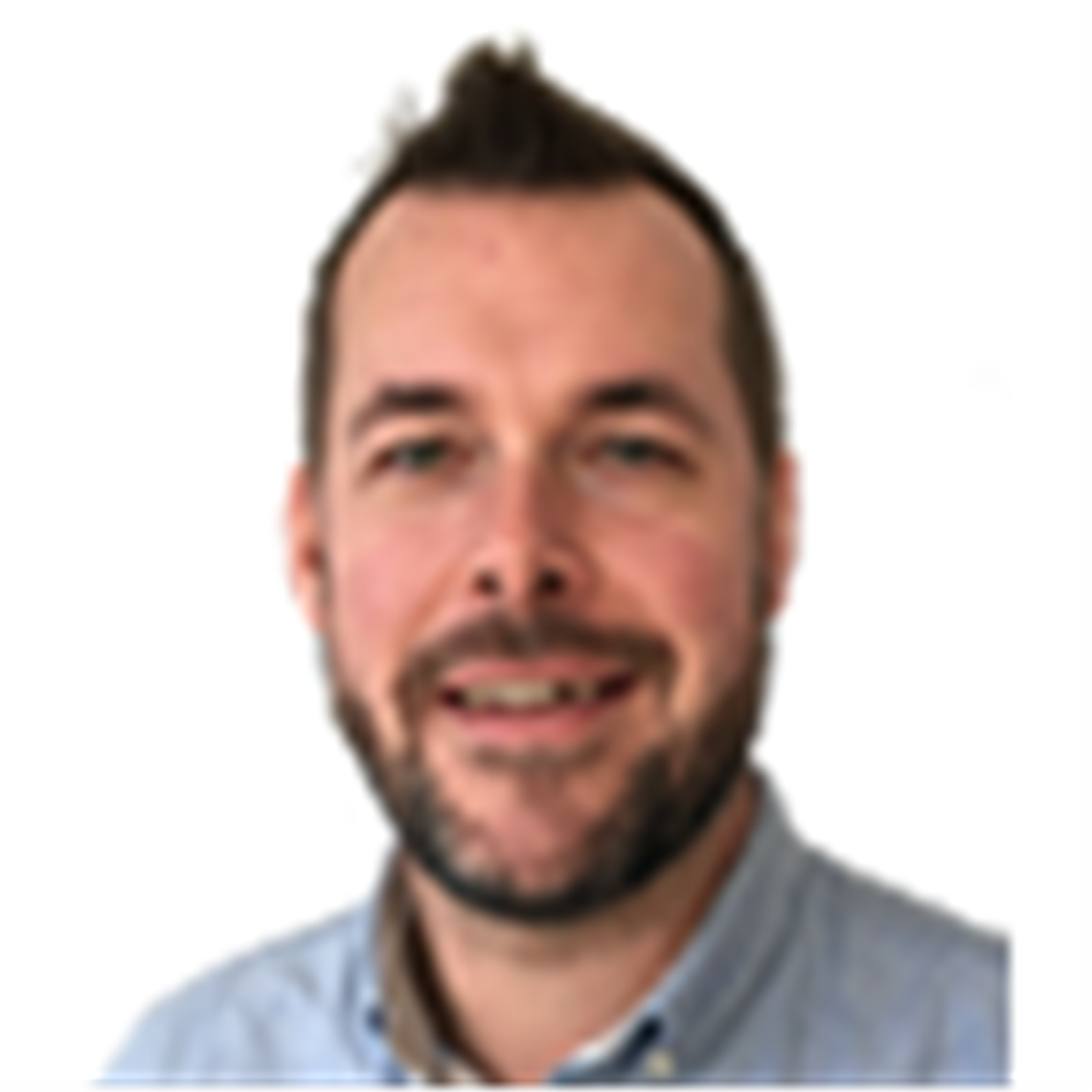
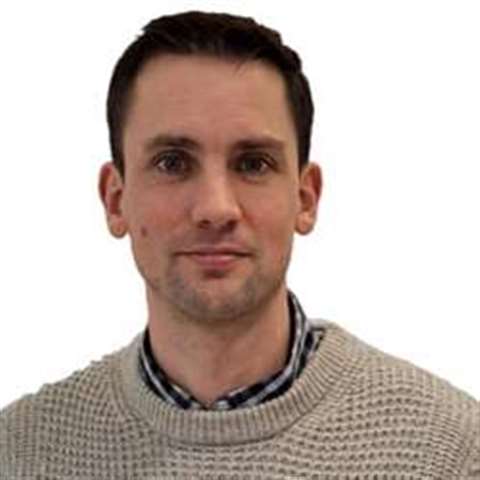
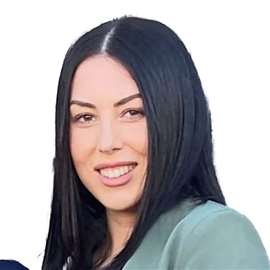
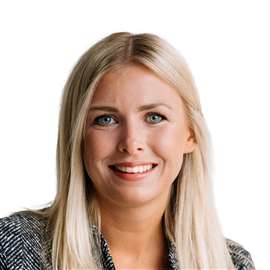