CE reports on developments to aid speed and efficiency in surveying
02 September 2009
Surveying is a high-tech area, but in recognition of how complex it has become, manufacturers are working on making their instruments easier to use. This should mean more speed and efficiency. CE reports.
Simplifying surveying tasks is not a new aim for equipment manufacturers but it remains a focus and one that's developing rapidly.
With a lack of skilled and qualified surveyors the goal has been to make work for the construction site contractor as simple as possible. The impetus for this is further strengthened by the global recession and consequently the need for contractors to increase productivity through using the latest in surveying technologies.
Speaking to CE, Topcon's Ian Stilgoe said, "Certainly, simplification is a major factor - it's always a driving force to simplify how people use things and make them more efficient."
He added that for Topcon to be at the forefront of the industry, in what is a difficult construction market, the company had to remain focused on product innovation.
"The bigger sales for us are in newer technology rather than standard technology," he said. "Companies are investing to stay ahead because that's pretty much the only way they can set themselves apart."
Contractors can reduce costs only so far in terms of overheads and staff but can more easily save money by reducing the time it takes to carry out a job explained Mr Stilgoe.
"If you can increase the speed of a job you can make a lot more money than if you just reduce the man power and keep to the same timeframe. And that's the trend at the moment, certainly in the machine control and site positioning side - people are going for products that make things quicker."
User-friendly
One of the most difficult tasks for surveying equipment manufacturers is to make products more user-friendly for workers on site.Mr Stilgoe explained, "It's probably the hardest part and probably what a lot of effort goes into - not only the technology per se, but actually how can the product be used by somebody who may not be in that position or in that profession and that's the bit that takes the most effort."
One of the ways to simplify equipment is to disguise the fact that the technology is complicated.
"It's all about taking what's inside the box and making that invisible for the user - let's say he's setting a peg in the ground - all he needs to know is where he's got to move to put the peg in the ground - everything else that's going on he doesn't need to know about. Our job would be to make it simple so he turns on the device, gets the position that he needs, navigates using menus to that point and then guide him very much like a Satellite navigation unit would. Our goal with our handheld devices is to make them very simple, that you can just pick it up, you don't need to read a manual - you just find your way around," Mr Stilgoe said.
Simplicity is also an area Hexagon, the owner of the Leica is working on. Mark Concannon, president of Hexagon Machine Control said, "In our every days lives ‘plug and play' technology is getting more and more advanced. This is something we are constantly reviewing, developing and including in all our solutions. The need is for increased functionality with less or simpler configuration required by the user."
Meanwhile, the Trimble SCS900 Site Controller Software is central to Trimble Site Positioning Systems and is available to run on the Trimble TSC2, Trimble TCU handheld controller or the new Trimble Tablet PC.
Johan Smet, director of marketing for Trimble's Heavy and Highway division said, "Trimble SCS900 Site Controller Software was designed from the ground up for contractors carrying out measurement and stakeout for earthworks, highways, landfill cells, waste disposal, and mining.
"This easy-to-use software helps you efficiently control and quantify site operations so you don't need to rely on a contract surveyor for site measurement and stakeout requirements. It is easy to learn and can be used with Trimble GPS or total station positioning equipment to maximise investment in both hardware and software systems."
He added the SCS900 software can be used at every stage of construction, including initial site measurement and verification of original ground levels, measuring site features, checking finished grade and laid material thickness and measuring stockpile sizes (including calculating their volumes). It can also be used for staking the out site features like power lines, utilities, manholes and existing structures as well as carrying out as-built site measurements.
Interface
Developing interfaces that look the same across Topcon's range of products is something the company has been working on for increased ease of use. Another focus has been to develop transferable software between products."We're very keen that if you pick up a GPS, total station or even machine control - that they're very similar. Certainly all the non-machine devices, the GPS and the levels use the same software so anybody who is starting off on a £3000 or £4000 total station can step up to use GPS with almost no further learning needed as they are already familiar with it.
"All our instruments run on the same software and therefore on the menu you just say whether you are using a total station, a robot or GPS - so we have achieved that - we are always evolving with simplification. Some users still want complex functionality, such as high-end engineers, so we are now looking at the software where you change the menu structure for different users. A guy that only sets out doesn't need to see surveying menus."
Work-flow
Mr Stilgoe added, "It can be fairly painful for a company to take on new technology and roll it out. We package it if necessary with training to make sure they are getting the best out of that technology."He said although not a new concept, taking the finished design and putting it directly into the field crew's hands, is "quite a big step" and is still not widely adopted.
"If you have a piece of construction equipment in the field and you can get the design directly into that piece of equipment, by-passing lots of CAD engines and things like that, it makes life easier and quicker.
"But if you can make the field equipment suitable for not only positioning experts , also foremen, site managers and site operatives then it's actually much more useful on site," said Mr Stilgoe.
The device spearheading this initiative for Trimble is its ‘Tablet' computer. Mr Smet said, "The rugged, easy-to-use handheld computer with built-in connectivity, allows site supervisors, foremen, site engineers, grade checkers, construction surveyors and project managers the ability to compute in the field, connect to the office, and make decisions faster."
One key point about the Tablet is that it is suitable for a range of users - there is no need to spend money on lots of different dedicated devices for specific tasks. Another point the company is keen to stress is its rugged design.
The Tablet uses Microsoft Windows Vista Business software as the basic starting point, allowing users to run whatever additional software they choose. Data is accessed and transferred the Trimble Connected Community system, and the key to this is its fast synchronisation, which means everyone is always looking at the latest information available.
The idea of a common look and feel and inter-operability is also something Hexagon sees as important. Mr Concannon said, "We have developed interfaces (CB16 and XC16) that can be transferred between different machine types allowing the user to retain the project design within the transferable hardware and connect to a different machine on the same project to continue with the construction tasks. For example, moving from an excavator to a grader. The excavator could be doing large earthworks removal and then the grader can be used to complete the final finish using one interface transferred between both machines," he said.
Downturn opportunity
Mr Concannon said, "Value for money by our clients is critical and even more so at this difficult time of a worldwide recession. Construction projects that are delayed and over budget are extremely costly to both the construction company and the end client."So the pressure in these economic times to complete projects on time and under budget is high.
"By using machine control it allows the contractor to save on material costs, to increase productivity by removing repetition in the workflow and reduces the risk of positional errors which may occur due to the complexity involved in construction projects."
Mr Smet said the recession is exactly the time contractors need to focus on costs and efficiency. "Making sure they get the most productivity out of their assets is one way to do that. A relatively small investment in Trimble technologies can help contractors dramatically improve the cash flow generated by the people and assets on the site, as well as make sure they win that next bid and keep everybody productive."
Mr Stilgoe said, "Demand in sales numbers is high but what we see is the general sales of all products - you come into a recession and rather than people cutting corners and buying cheap equipment they are actually buying things that maybe they wouldn't have done because it can save them a significant amount rather than just doing their normal job.
So we think we are seeing the lifting of technology. You are seeing a higher level purchasing. Contractors are more interested in what's new and different that can make their job quicker instead of just ordering what they ordered all the time. People didn't have the time, possibly, to look for what else was on offer before.
STAY CONNECTED

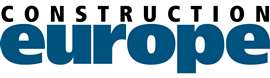
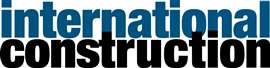
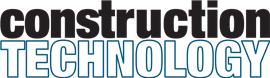
Receive the information you need when you need it through our world-leading magazines, newsletters and daily briefings.
CONNECT WITH THE TEAM
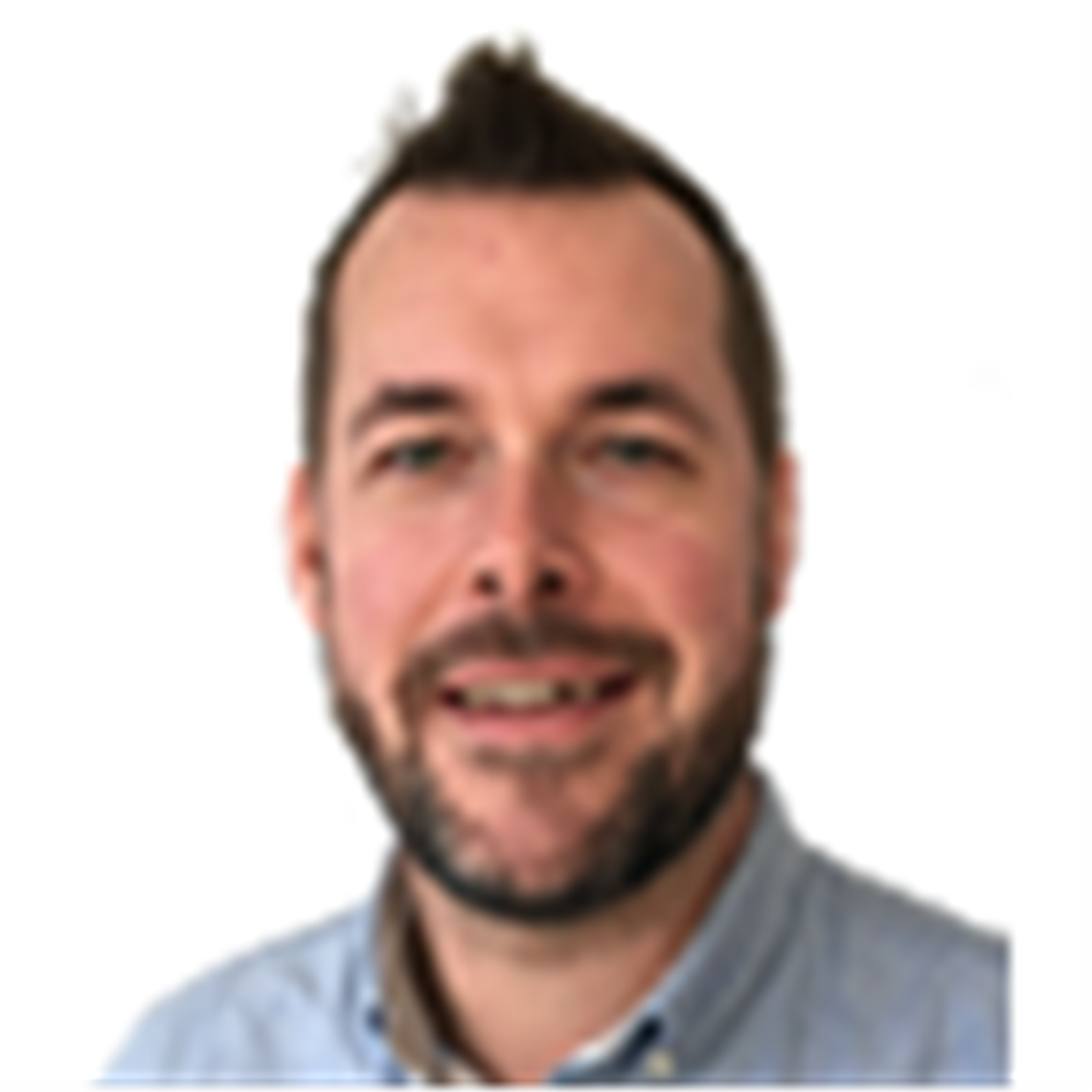
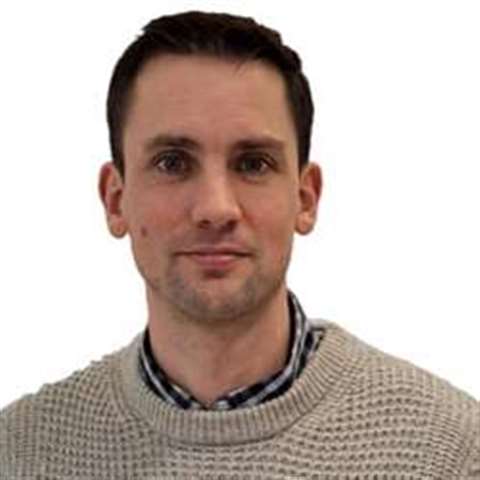
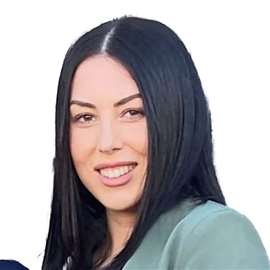
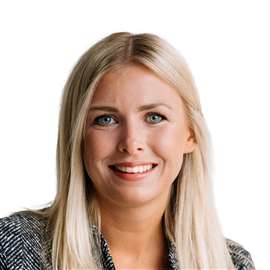