Bringing them down: The latest from the demolition and recycling sector.
10 March 2009
Is it time that contractors rethink the way they make use of specialist demolition contractors? Lindsay Gale, editor of sister publication Demolition & Recycling International (D&Ri) reports, and also highlights some of the latest equipment available to speed the demolition process.
Traditionally, demolition contractors only become involved with specific buildings and structures at the very end of their lives - when they have to be cleared to make way for new builds or for other redevelopment work on the site they occupy. This means that there is normally no formal input from a demolition perspective as to how a building is to be demolished during the initial planning phase of a new construction.
As a result, demolition contractors are increasingly faced with having to work with a building or structure that creates a challenge - a challenge that can arise from the materials used in its construction, the way it was constructed or the physical configuration of the building itself. And once the actual demolition is carried out, there then comes the challenge of disposing of the resultant demolition waste.
In these days of ‘sustainable' construction - a buzzword increasingly being heard - perhaps it is time that general architects and general contractors make better advance use of the expertise of the demolition industry by gaining some degree of ‘expert advice' from the demolition specialist who will be eventually tasked with removing the fruits of their labours.
Increased capability
One feature affecting many of today's demolition contracts is the change in the nature of the structures that have to be removed. Increasingly, they date from the 1960s onwards, and they reflect the changes in the nature of construction techniques and materials, and the quality of the build itself, with better concrete and reinforcement, and thicker foundations.
This is fuelling the need for more capable, powerful attachments for hydraulic excavators that can handle the more modern, robust structures that demolition contractors are increasingly being called on to bring down.
Intermat is sure to see a considerable number of new tools on show, but the specialists who cater for this market have been adding products to their ranges that meet this need in addition to those that will be on show in Paris.
Last year, Italian attachment specialist Mantovanibenne launched its monster CR100 crusher. This new attachment was developed in part due to the success the company has gained with its MS130 multiprocessor (to iC's knowledge, the demolition attachment with the widest jaw opening currently available worldwide, designed specifically to deal with large reinforced concrete foundations). The CR100 is the largest crusher ever produced by the company and is designed for by 80 to 130 tonne excavators. It weighs in at 11 tonnes, is more than 4 m long and has a jaw opening of 2 m.
Arden Equipment is another who has not completely held back, and has introduced two new products recently. Marketing director Eric Daubail said that the company is continuing the development of its universal processor range by adding a third model in the shape of the 360° rotatable CU1300. This weighs in at 1.27 tonnes or 1.35 tonnes, depending on the jaw set fitted, and is intended for carriers in the 14 to 19 tonne class.
A fifth hydraulic pulveriser has also joined Arden's range alongside the existing BBH800B, BBH880R (rotating), BBH1000 and BBH1000R (rotating) in the form of the BBH1300B. This is a 5.12 tonne unit designed for carriers in the 45 to 55 tonne class. The BBH1300B has a maximum jaw opening of 1.3 m and an operating pressure of 350 bar.
Another Italian attachment manufacturer, Promove, has recently introduced the CP1510P 360° rotation multiprocessor. Yet to be officially launched (it will almost certainly be on show in Paris), the new attachment is currently undergoing full field-testing with companies in Italy and other European countries. It weighs 16 tonnes and is designed for use on carriers weighing 15 to 27 tonnes. Promove has used a closed body design for the CP1510P to prevent damage to the crusher's hoses and internal components.
Many of the major OEMs offer a range of attachments for their machines that they either manufacture themselves or are branded versions from other specialist attachment manufacturers. JCB is just one OEM that does this, and the company has announced new additions to its attachment offering. It has added three new multiprocessors, the 1.68 tonne MP200, the 2.58 tonne MP300 and the 3.48 tonne MP400, designed to cover the 15 to 50 tonne carrier class, which matches its range of tracked excavators. These tools feature easily changed interchangeable jaw sets. A universal jaw set allows for primary and secondary demolition masonry applications while a steel shear set allows the demolition and processing of steel structural elements.
Fast cycle times are achieved through the inclusion of speed valves, with twin rams ensuring that high crushing forces are achieved throughout the entire cycle for maximum productivity. The twin ram also eliminates displacement forces, reducing stress on the carrier and ensuring that the unit is always central to the material being demolished.
The company has also added a seven-model line of selector grabs, suitable for use on carriers weighing from 10 to 46 tonnes.
The grabs offer volumes from 300 litres in the case of the smallest, the SG 300, to 1000 litres in the case of the largest, the SG1000. The SG line features 360°rotation, with a speed control valve to adjust rotational speed for optimum cycle time. Large jaw openings allow the grab to handle even the largest material, while a good clearance between the shell and head enables maximum material fill. The shell's central cylinder, rib and end-stop configuration allows force to be evenly applied by the grab.
The SG series of grabs has been designed for heavy-duty applications - casing protects all major components, with the hydraulic cylinders and motors being full covered to maximise protection from damage. Large diameter tempered pins and brushes, including dust seals, provide maximum service life, with hoses featuring wire guarding and a braided sleeve. A cross-line relief valve on the motor protects the hydraulic system from potential damage form pressure spikes originating from the carrier.
As many of these new attachments indicate, demolition equipment is getting bigger. These more powerful tools mean contractors can be more productive, and demolish buildings in shorter timescales.
STAY CONNECTED

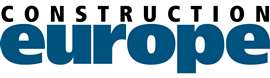
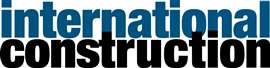
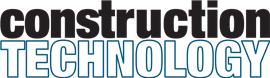
Receive the information you need when you need it through our world-leading magazines, newsletters and daily briefings.
CONNECT WITH THE TEAM
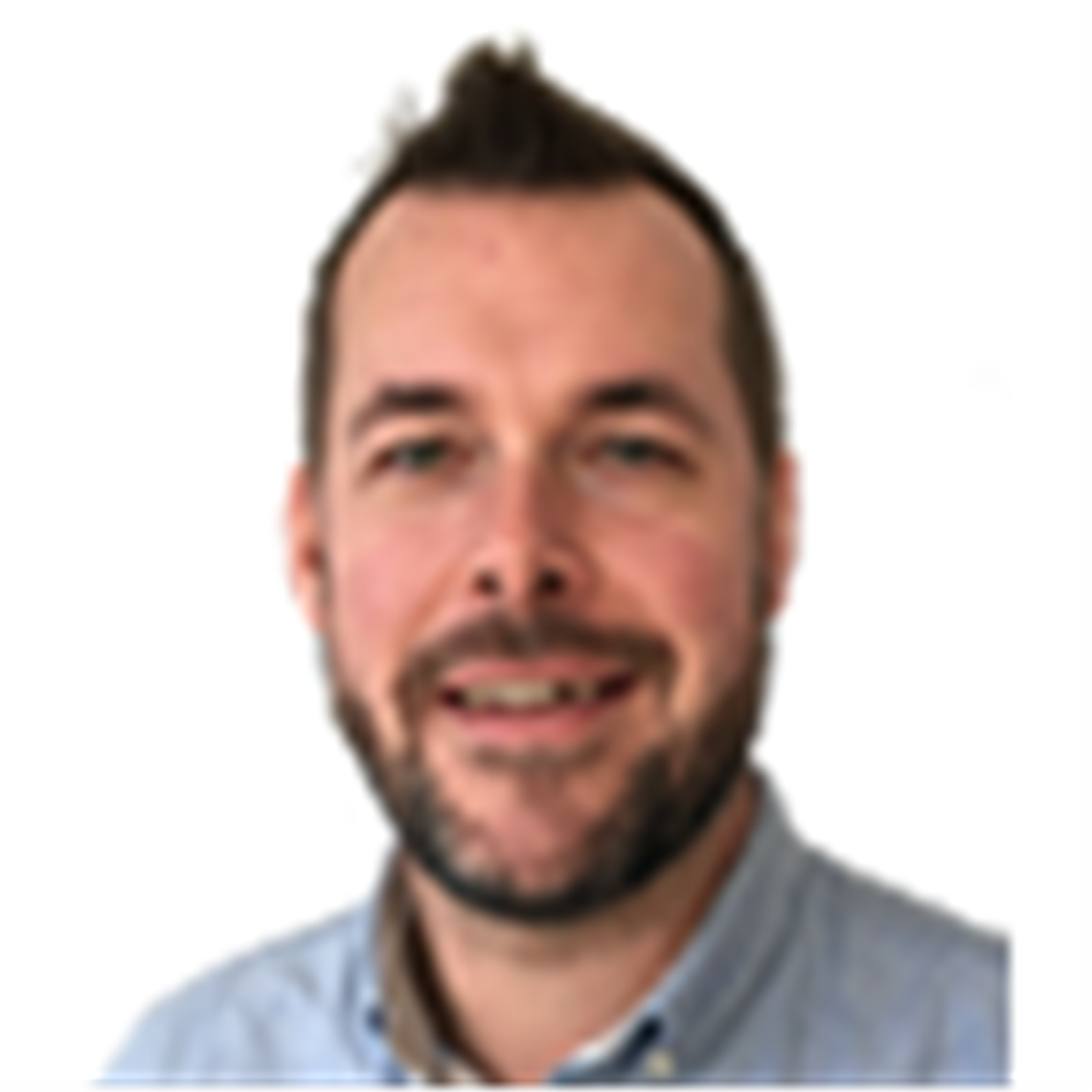
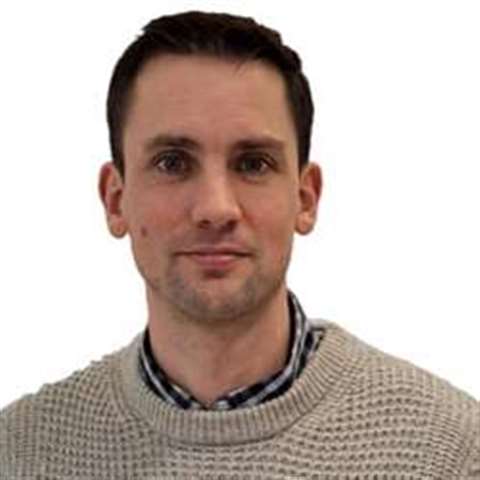
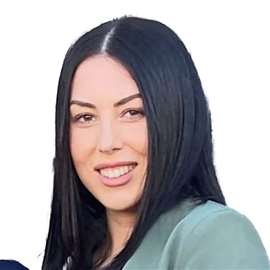
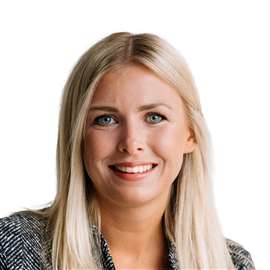