Automatisch von KI übersetzt, Original lesen
Die Technologie, von der ein ehemaliger Caterpillar-Manager behauptet, sie könne selbst die besten Baggerfahrer verbessern
18 Juli 2025
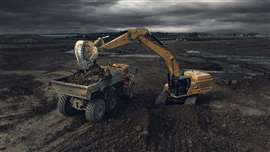
Jahrzehntelang hing die Produktivität eines Baggers weitgehend von der Geschicklichkeit des Bedieners hinter den Bedienelementen ab.
Doch selbst unter erfahrenen Profis schwankt die Leistung deutlich stärker, als vielen Branchenkennern bewusst ist. Eine Studie von Volvo Construction Equipment ergab, dass die Produktivität erfahrener Fahrer um bis zu 300 % und die Kraftstoffeffizienz um bis zu 150 % schwanken kann. Bei weniger erfahrenen Fahrern oder Mietkunden sind die Produktivitätsunterschiede sogar noch größer und erreichen in manchen Fällen bis zu 700 %.
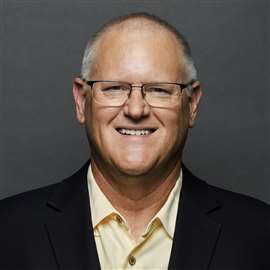
Genau dieses Problem – die enorme Streuung der Fahrerleistung – versucht Ken Gray, ehemaliger Global Director of Innovation bei Caterpillar, nun zu lösen. Als Mitgründer und Chief Performance Officer des israelischen Start-ups Dig Robotics ist Gray überzeugt, dass die LiDAR-Technologie seines Unternehmens selbst den fähigsten Baggerfahrern zu bisher unerreichbarer Konstanz, Effizienz und Produktivität verhelfen kann.
„Das Problem, das wir lösen wollen, betrifft die Variabilität der Bedienerleistung“, sagt Gray. „Hersteller investieren viel Geld in die Entwicklung neuer Produkte – diese Verbesserungen können im Lärm untergehen, wenn die Variabilität der Bedienerleistung nicht berücksichtigt wird.“
Dig Robotics wurde im Oktober 2023 gegründet und hat sich schnell vom Konzept zum Prototyp entwickelt. Nur 90 Tage nach der Gründung hatte das Unternehmen sein System in einem Steinbruch im Einsatz. Die Lösung kombiniert LiDAR-basierte Computervision, maschinelles Lernen und Echtzeit-Bedienungsfeedback, um die Baggerleistung bei jedem Schaufelzyklus zu optimieren.
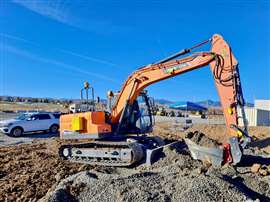
„Wir wollen dem Betreiber nicht die Kontrolle entziehen – das hassen sie.“
Ein auf dem Baggerdach montierter LiDAR-Sensor erfasst Live-Daten während der Arbeit der Maschine. Algorithmen berechnen jederzeit die optimale Grabroute basierend auf Geländetopografie, Maschinengeometrie, Schaufelgröße und Materialeigenschaften. Das System vergleicht anschließend die tatsächlichen Bewegungen des Bedieners mit der optimalen Route und liefert sofortiges visuelles Feedback in der Kabine.
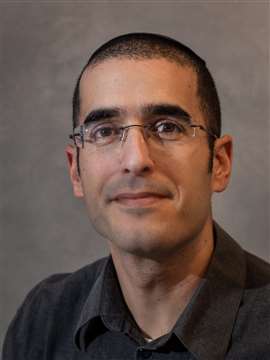
Der Bediener wird anhand von vier kritischen Parametern geführt: Schnitttiefe, Schaufelwinkel während des Schnitts, Bewegungsgeschwindigkeit und Zeitpunkt des Schaufelrückzugs. Diese Werte werden durch einfache Farbmarkierungen angezeigt – grün im optimalen Bereich. So erkennen sowohl unerfahrene als auch erfahrene Bediener genau, wo Anpassungen erforderlich sind.
Gray ist sich darüber im Klaren, dass es nicht darum geht, die Fähigkeiten der Bediener zu ersetzen, sondern sie zu verbessern. „Wir wollen den Bedienern nicht die Kontrolle entziehen, nur weil sie es hassen. Wir wollen ihnen Tipps geben, wie sie ihr Bestes geben können“, sagt er. „Erfahrene können auf aktuelle Informationen zugreifen, weil sie ihre Gewohnheiten kennen müssen. Bleibe ich zu lange im Schnitt? Neige ich dazu, zu tief zu tauchen? Genau das wollen sie wissen.“
Das System lernt und passt sich während der Arbeit an. Dank der Machine-Learning-Komponente kann es den Materialzustand – einschließlich Kohäsion, Körnigkeit und Vorhandensein von Felsbrocken – automatisch und ohne manuelle Eingabe beurteilen. Jeder Löffel informiert den nächsten, während Maschinen, die auf derselben Baustelle arbeiten, Informationen austauschen, um ein gemeinsames Verständnis des ausgegrabenen Materials zu entwickeln.
Die wirtschaftlichen Auswirkungen könnten erheblich sein, insbesondere für Anlagenbesitzer, die ihre Produktivität steigern und den Kraftstoffverbrauch senken möchten, ohne in neue Maschinen investieren zu müssen. Das System lässt sich in nahezu jeden Bagger, unabhängig von Marke und Alter, oft innerhalb eines Arbeitstages nachrüsten.
In einem ersten Fall installierte Dig Robotics das System auf einem 20 Jahre alten Liebherr R 984 C, der von einem erfahrenen Fahrer bedient wurde, der die Maschine seit dem Kauf bediente. Die Ergebnisse überraschten sogar den Fahrer. „Er arbeitet 10 % besser als zum Zeitpunkt der Installation und verbraucht rund 20 % weniger Kraftstoff“, sagt Gray.
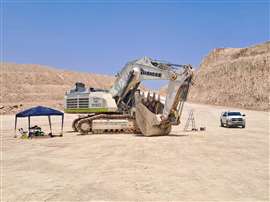
Respekt für mehrere OEMs
Derzeit konzentrieren sich die ersten Pilotprojekte des Unternehmens auf Sektoren, in denen schrittweise Produktivitätssteigerungen erhebliche finanzielle Erträge bringen können – große zivile Infrastrukturprojekte sowie Steinbruch- und Bergbau.
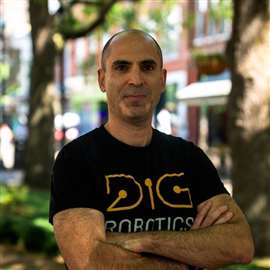
Die Geschäftsstrategie von Dig Robotics konzentriert sich auf die Zusammenarbeit mit Händlern verschiedener OEMs. Derzeit laufen Gespräche und Pilotprojekte mit Händlern von Caterpillar, John Deere, Liebherr, Doosan und Hitachi. „Ich möchte dem Kundenwunsch nach mehreren OEMs in der Flotte gerecht werden“, erklärt Gray. „Ich glaube, es ist heutzutage selten, nur einen OEM zu sehen.“
Händler helfen bereits dabei, nicht nur die technische Leistung des Systems zu bewerten, sondern auch dessen Wirtschaftlichkeit, Installationsprozess und langfristigen Supportbedarf. „Sie experimentieren auch mit uns. Bietet es ihren Kunden wirklich einen Mehrwert? Wie können wir helfen? Was kostet der Support?“, sagt Gray.
Die Technologie selbst ist durch eigene Patente abgesichert, und das Ingenieurteam unter der Leitung von Chefwissenschaftler Dr. Oded Medina verfügt über Expertise in Robotik und Bewegungsplanung. Dig Robotics muss nun jedoch ausreichende Mittel sichern, um von der aktuellen Pilotphase zur vollständigen kommerziellen Veröffentlichung überzugehen.
„Wir haben eindeutig ein Problem, das unsere Kunden lösen möchten“, sagt Gray. „Wir haben die Technologie, wir haben sie gefunden, um es zu lösen. Die Frage ist: Haben wir die finanziellen Mittel, um es vom jetzigen Pilotprojekt bis zur kommerziellen Umsetzung zu bringen? Ich denke, das wird uns gelingen.“
Ziel ist es, Anfang 2026 die ersten kommerziellen Systeme auf den Markt zu bringen.
Bei Erfolg könnte Dig Robotics einen schrittweisen, aber wichtigen Fortschritt bei Erdbewegungsarbeiten ermöglichen, der selbst den besten Bedienern bessere Ergebnisse ermöglicht.
Bleiben Sie verbunden

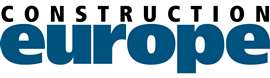
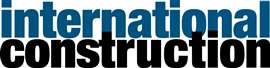
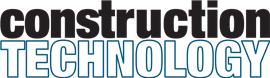
Erhalten Sie die Informationen, die Sie brauchen, genau dann, wenn Sie sie benötigen – durch unsere weltweit führenden Magazine, Newsletter und täglichen Briefings.
Mit dem Team verbinden
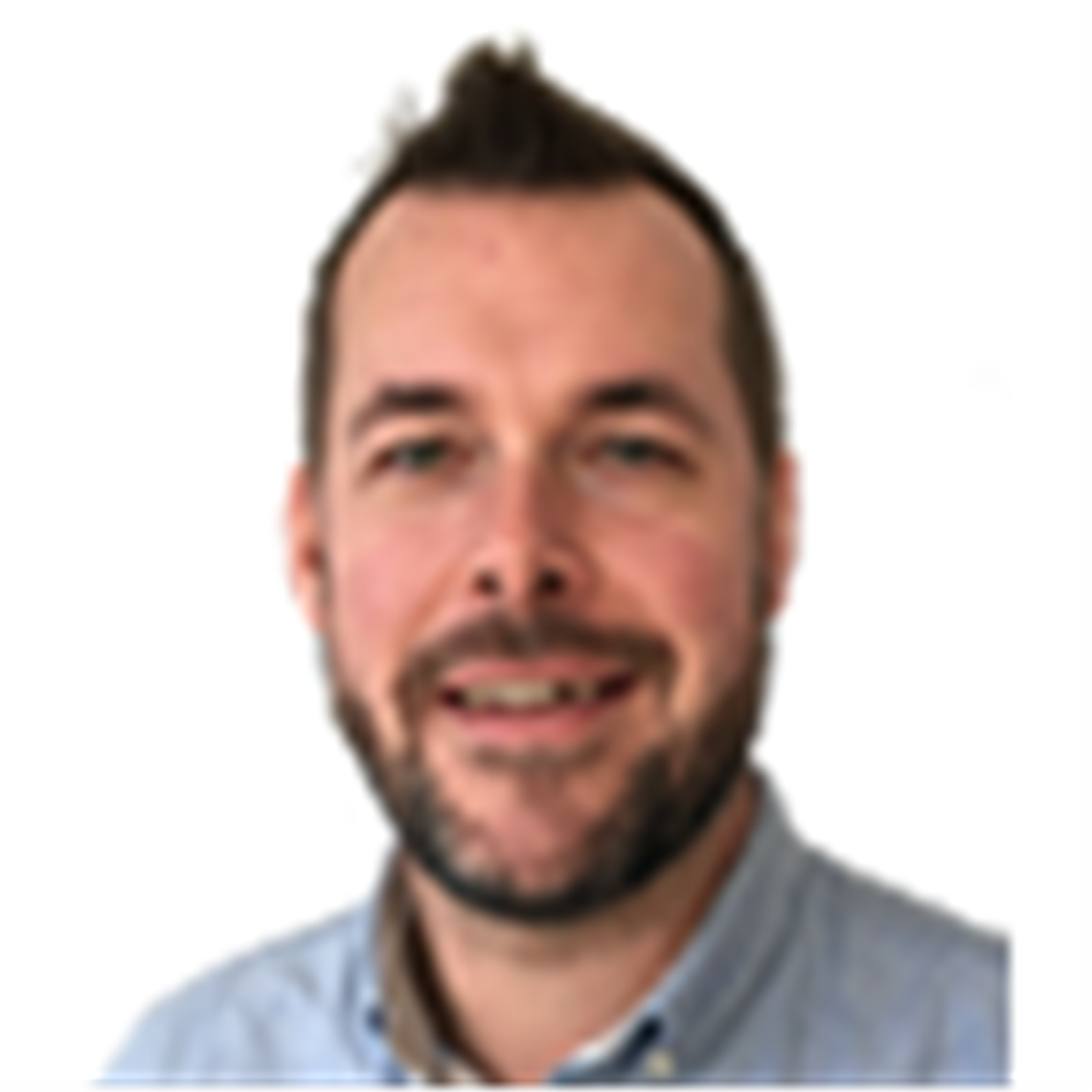
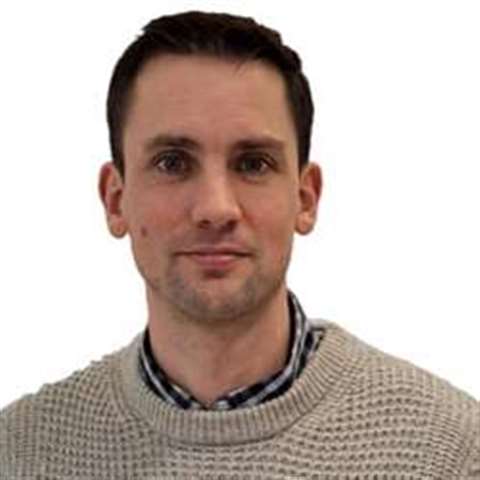
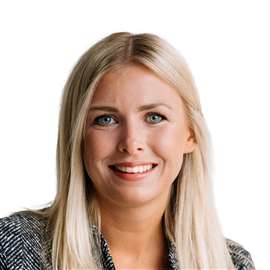