Automatisch von KI übersetzt, Original lesen
Ist Zusammenarbeit der Schlüssel zur globalen Transformation im Lehrgerüst- und Schalungsbereich?
12 Februar 2025
Will die Branche durch die Kombination von Spitzentechnologien, nachhaltigen Materialien und verbesserter Teamarbeit entlang der Wertschöpfungskette einen globalen Wandel vorantreiben? Catrin Jones findet es heraus.
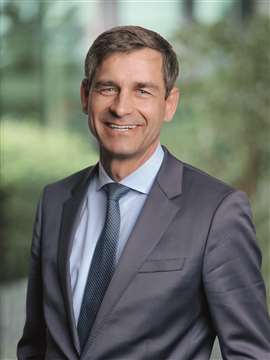
Die Schalungs- und Traggerüsttechnologie unterliegt einem tiefgreifenden Wandel. Die Fortschritte zielen darauf ab, die Sicherheit, Effizienz und Nachhaltigkeit auf Baustellen zu verbessern. Robert Hauser, CEO von Doka, beleuchtet diese Entwicklungen und gibt Einblicke, wie diese Innovationen die Branche umgestalten und einige ihrer dringendsten Herausforderungen angehen.
Viele der jüngsten Fortschritte in der Schalungs- und Traggerüsttechnik basieren auf Automatisierung. „Automatisierung verbessert Sicherheit, Geschwindigkeit und Effizienz – das sind die drei Kernparameter, die wir optimieren wollen“, erklärt Hauser. Auf der Bauma 2025 in München wird Doka seinen DokaXbot Lift vorstellen, einen halbautomatischen Roboter, der Schalungsplatten effizient auf eine Höhe von bis zu sechs Metern heben kann. Das per Fernbedienung gesteuerte System reduziert die körperliche Belastung der Arbeiter und verbessert die Sicherheit, da das Klettern auf die Schalung entfällt.
Eine weitere bemerkenswerte Entwicklung ist die Vorfertigung vor Ort, die einem Fließbandprozess ähnelt. Durch die Montage der Schalungseinheiten in einem dafür vorgesehenen Bereich wird laut Hauser ein Fließbandprozess in einer Fabrik nachgeahmt. Vorgefertigte Einheiten werden an ihren Platz gehoben, wodurch die Herausforderungen bei der Montage vor Ort minimiert und die Projektzeitpläne verbessert werden. Hauser fügt hinzu: „Die Bohrabläufe werden ebenfalls optimiert und Fehler minimiert. Wenn Sie es auf dieser angegebenen Seite tun, haben Sie eine bessere Qualitätskontrolle. Sobald die Schalungsmasse montiert ist, nehmen Sie im Grunde den Kran, heben sie an die Seite oder an die bestimmte Stelle, an der Sie den Beton gießen möchten, und dann erfolgt die Betonierung.“
Die Rolle der Digitalisierung
In der gesamten Branche verändert die Digitalisierung weiterhin die Arbeitsabläufe im Bauwesen. Die Integration von Building Information Modeling (BIM) hat die Erstellung präziser 3D-Modelle für Schalungssysteme ermöglicht, wodurch der Materialverbrauch optimiert und Abfall reduziert wurde. „Der Übergang von 2D- zu 3D-Modellen hat alles verändert. Wir minimieren Abfall, reduzieren Fehler und rationalisieren den gesamten Prozess“, erklärte Hauser.
Darüber hinaus ermöglichen IoT-fähige Systeme die Echtzeit-Datenerfassung auf Baustellen und liefern verwertbare Erkenntnisse. In die Schalung eingebettete Sensoren überwachen Parameter wie Temperatur, Druck und Ausrichtung. Hauser hob das Betonüberwachungssystem von Doka hervor, das den genauen Zeitpunkt bestimmt, wann der Beton zum Abschalen bereit ist. Dies gewährleistet eine bessere Qualität und Sicherheit und ermöglicht es den Bauunternehmern, fundierte Entscheidungen zu treffen und Vorschriften einzuhalten, sagt Hauser.
Betonsensortechnologie wird zunehmend auf dem Markt verfügbar. Das in Großbritannien ansässige Unternehmen Converge bietet sowohl eingebettete Sensoren als auch wiederverwendbare Sensoren mit großer Reichweite an. Ebenso hat Heidelberg Materials die drahtlosen Betonsensoren SmartRock entwickelt, die bis zu 60 Tage lang alle 15 Minuten Temperatur und Festigkeitszunahme überwachen.
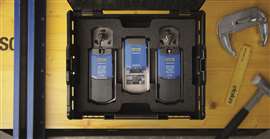
Reduzieren und Wiederverwenden
Nachhaltigkeit ist ein wichtiger Schwerpunkt für die Gerüst- und Schalungsindustrie, den Doka auf jeden Fall im Auge behält. „Indem wir die Nutzungszyklen der Schalung maximieren, reduzieren wir den CO2-Fußabdruck pro Nutzung erheblich“, erklärt Hauser. Sanierungs- und Wartungsdienstleistungen verlängern die Lebensdauer der Materialien zusätzlich und entsprechen damit nachhaltigen Praktiken.
Hauser wollte noch keine Details zu einer der nächsten Entwicklungen von Doka verraten, verriet aber, dass diese zu 100 % aus recyceltem Kunststoff bestehen wird. „Wir glauben, dass wir damit die CO₂-Emissionen auf null reduzieren können“, verrät Hauser. „Und das wird ein echter Wendepunkt sein.“
Natürlich spielt auch die Art des beim Bau verwendeten Betons eine entscheidende Rolle und Doka hat Methoden gefunden, den Prozess mit seinen Lösungen zu synchronisieren.
„Vergleicht man den CO2-Fußabdruck von Beton, der in Schalungen verwendet wird, wird deutlich, dass der Beton selbst den weitaus größeren Anteil ausmacht. Um diesem Problem zu begegnen, treiben wir Innovationen voran, die uns helfen, CO2-reduzierten Beton besser zu verarbeiten“, sagt Hauser.
Zementhersteller arbeiten aktiv an der Reduzierung des CO2-Fußabdrucks ihrer Mischungen und machen mit den mittlerweile verfügbaren umweltfreundlicheren Betonmischungen bereits Fortschritte.
„Allerdings“, sagt Hauser, „weisen diese Mischungen oft deutlich unterschiedliche physikalische Eigenschaften auf. Einige dieser Mischungen härten beispielsweise bei niedrigeren Temperaturen nicht richtig aus, weil die Anfangstemperatur, die zum Auslösen der chemischen Reaktion im Beton erforderlich ist, entweder nicht erreicht wird oder nur sehr langsam abläuft.“
„Um dieses Problem anzugehen, haben wir ein Prototypsystem mit intelligenter beheizter Schalung entwickelt. Das System erwärmt die Oberfläche der Schalung, die mit dem Beton in Kontakt kommt. Indem wir dem Beton durch Erhitzen eine kleine Menge Energie zuführen, können wir den Aushärtungsprozess einleiten oder beschleunigen, wodurch wir diese innovativen Betonmischungen effektiv einsetzen können.“
Fallstudien in Aktion
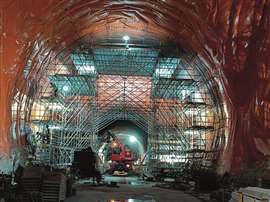
Unternehmen gehen nicht nur die Herausforderungen der Nachhaltigkeit an, sondern finden auch innovative Wege, um technische und logistische Hürden bei Bauprojekten zu überwinden.
Der Ausbau der gelben Linie der Lissaboner Metro in Portugal, einschließlich des Baus der neuen Estrela-Station, ist ein großes Infrastrukturprojekt, das eine Ringstrecke zwischen Rato und Cais do Sodré schaffen soll. Das Projekt wurde in drei Hauptbaubereiche unterteilt: das Apothekengebäude, den Stationsschacht und den Stationstunnel.
Das Projekt war mit erheblichen Herausforderungen verbunden. Dazu gehörten die Notwendigkeit, die historische Fassade des Apothekengebäudes zu erhalten, einen 60 m tiefen Schacht mit begrenztem Platz für Rolltreppen zu bauen und die technischen Komplexitäten des unterirdischen Tunnelbaus in einer dichten städtischen Umgebung zu bewältigen.
Ulma und Zagope haben diese Herausforderungen gemeinsam mit innovativen Schalungs- und Stützlösungen bewältigt. Beim Apothekengebäude ermöglichten modulare Schalungssysteme den präzisen Bau von Fassadenwänden, Aufzugsschächten und elliptischen Säulen. Beim Bahnhofsschacht erleichterten moderne Rundplatten, Stützsysteme und Schalungen den Bau von dicken Balken, variablen Platten und tiefen Schächten, während eine 60 Meter lange BRIO-Treppe den Zugang zur Baustelle ermöglichte.
Im Stationstunnel unterstützten leichte MK-Schalwagen und Gerüstsysteme den effizienten Bau von Tunneln, Gewölben und Wänden unter Tage. Da im Stadtzentrum nur begrenzt Platz zur Verfügung stand, wurden Materialien wiederverwendet und sechs Schalwagen gleichzeitig eingesetzt.
In einem weiteren wegweisenden Projekt lieferte Altrad RMD Kwikform (Altrad RMDK) eine groß angelegte, maßgeschneiderte temporäre Baulösung an das Balfour Beatty Vinci Joint Venture (BBV JV), um den Bau des neuen „Curzon No. 3 Viaduct“ als Teil des neuen HS2-Bahnhofs Curzon Street im Stadtzentrum von Birmingham, Großbritannien, zu unterstützen.
Das Lehrgerüstsystem unterstützte den Bau von vier Viaduktdecks, die zu einem einzigen Brückendeck mit drei Hochgeschwindigkeitsgleisen zusammengeführt wurden.
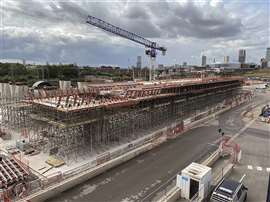
Ingenieure entwarfen eine Lehrgerüstkonfiguration, die Lasten von der Betondecke und Windkräfte sicher auf die Fundamente übertrug, ohne die Struktur zu überlasten.
Durch die Kombination von Rapidshor-Lehrgerüst, Alform-Aluminiumträgern und Superslim Soldier-Schalungsträgern ermöglichte das System eine einfache Bewegung und Wiederverwendbarkeit der Deckeinheiten.
Cliff Shepherd, leitender Projektingenieur bei Altrad RMDK, sagte: „Dies war eines der größten Projekte, an denen ich in meiner über 33-jährigen Karriere gearbeitet habe, und das gesamte Team von Altrad RMDK ist äußerst stolz, Teil dieses historischen Projekts zu sein. Dies ist ein hervorragendes Beispiel, das nicht nur die technische Exzellenz von Altrad RMD Kwikform zeigt, sondern auch, wie kompatibel und vielseitig unsere Geräte sind, wenn sie zusammenarbeiten, um sehr komplexe Formen zu formen.“
Herausforderungen und Chancen
Mit Blick auf die Zukunft steht die Schalungs- und Traggerüstbranche vor mehreren Herausforderungen, darunter Arbeitskräftemangel und stagnierende Produktivität. „Wir haben nicht nur nicht genug Arbeitskräfte, sondern auch unsere Produktivität auf der Baustelle stagniert ziemlich, sodass es keine Produktivitätsverbesserungen gibt, wie man sie in anderen Branchen, beispielsweise im Automobilsektor, sieht“, stellt Hauser fest. Automatisierung und Digitalisierung sind entscheidend, um diese Lücke zu schließen, die Abhängigkeit von Handarbeit zu verringern und gleichzeitig die Effizienz zu steigern.
Auch Nachhaltigkeit wird eine transformative Rolle spielen. Hauser prognostiziert strengere Vorschriften und eine steigende Nachfrage nach kohlenstoffarmen Lösungen. „Wir haben hier also nicht nur einen Mangel, sondern auch eine Kompetenzlücke. Außerdem werden wir zunehmend aufgefordert, unseren CO2-Fußabdruck zu reduzieren. Dies geschieht entweder durch Kunden, die uns nach Lösungen fragen, weil sie selbst ihren CO2-Fußabdruck reduzieren möchten, oder es werden die Regulierungsbehörden, die Regierungen sein, die den Bauunternehmen im Projekt Vorschriften auferlegen“, sagt er. Um diese Anforderungen zu erfüllen, sind laut Hauser gemeinsame Anstrengungen entlang der gesamten Wertschöpfungskette des Bauwesens von entscheidender Bedeutung. „Die Zusammenarbeit der Beteiligten innerhalb der Wertschöpfungskette des Bauwesens wird viel stärker erforderlich sein. Wir müssen alle wirklich zusammenstehen und dafür sorgen, dass dies funktioniert“, schließt Hauser.
Da die Branche der Traggerüste und Schalungen zunehmend auf Digitalisierung und Nachhaltigkeit setzt, werden Traggerüst- und Schalungstechnologien die Branchenpraktiken revolutionieren. Mit Fortschritten in den Bereichen Robotik, IoT-Systeme und Materialien ist die Branche gut aufgestellt, um die Effizienz zu steigern, die Umweltbelastung zu minimieren und zukünftige Herausforderungen anzugehen – vorausgesetzt, dass Vorschriften und Zusammenarbeit diese Bemühungen unterstützen. Die erfolgreiche Umsetzung dieser Innovationen hängt jedoch auch davon ab, Qualifikationslücken zu schließen und sicherzustellen, dass die Ausbildung der Belegschaft mit dem technologischen Fortschritt Schritt hält. Darüber hinaus wird die Förderung von Partnerschaften entlang der gesamten Lieferkette von entscheidender Bedeutung sein, um den Nutzen dieser Lösungen zu maximieren.
Bleiben Sie verbunden

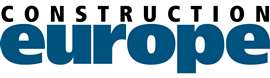
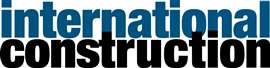
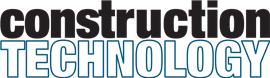
Erhalten Sie die Informationen, die Sie brauchen, genau dann, wenn Sie sie benötigen – durch unsere weltweit führenden Magazine, Newsletter und täglichen Briefings.
Mit dem Team verbinden
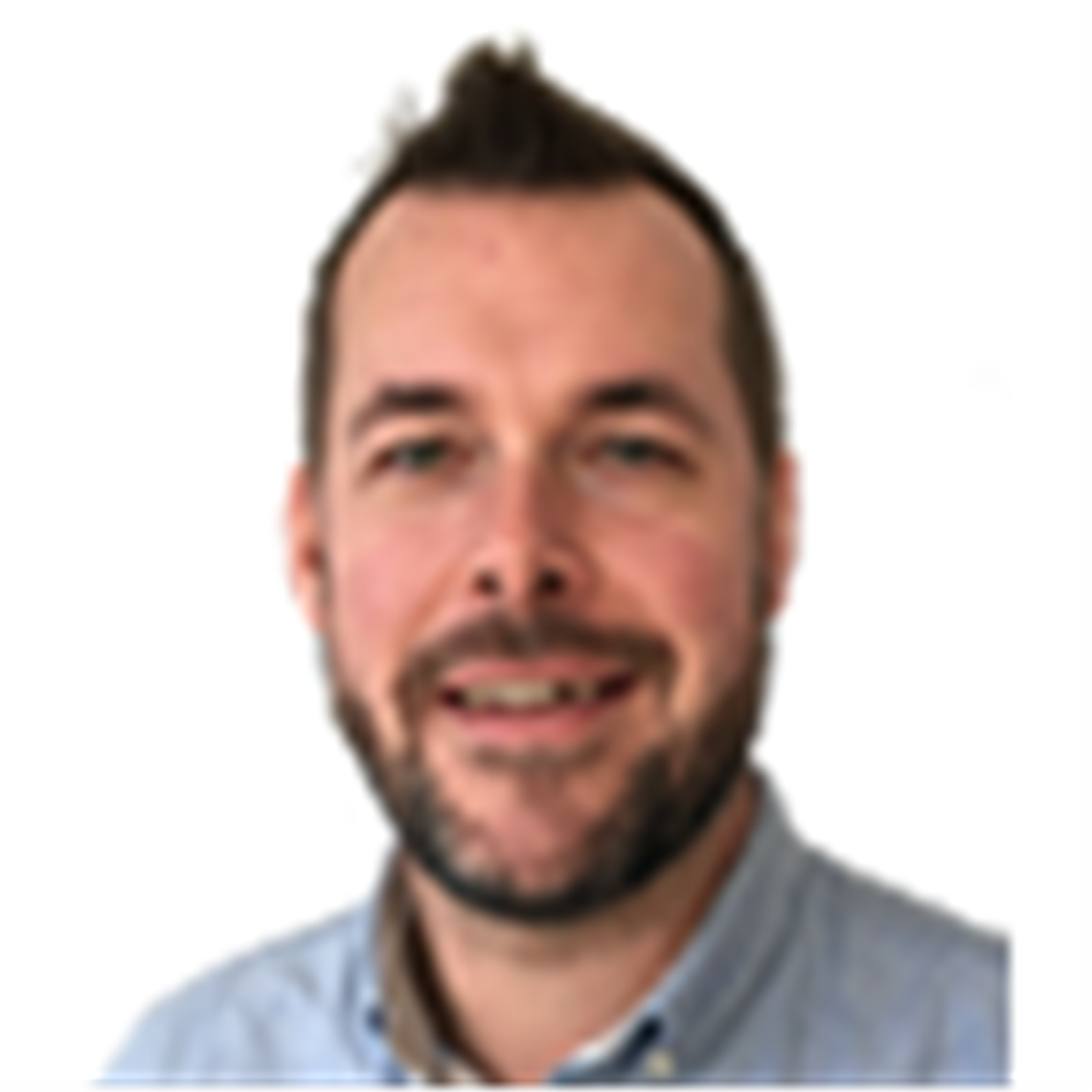
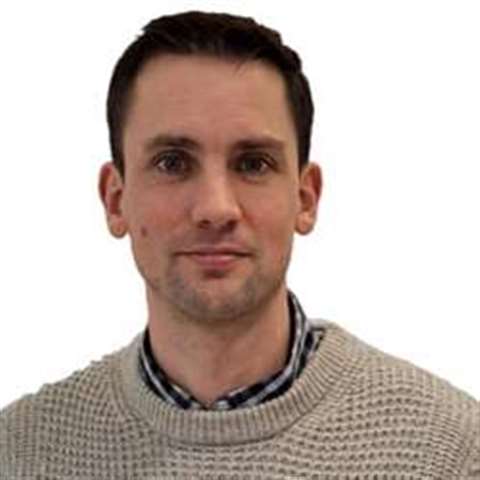
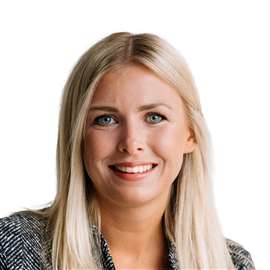